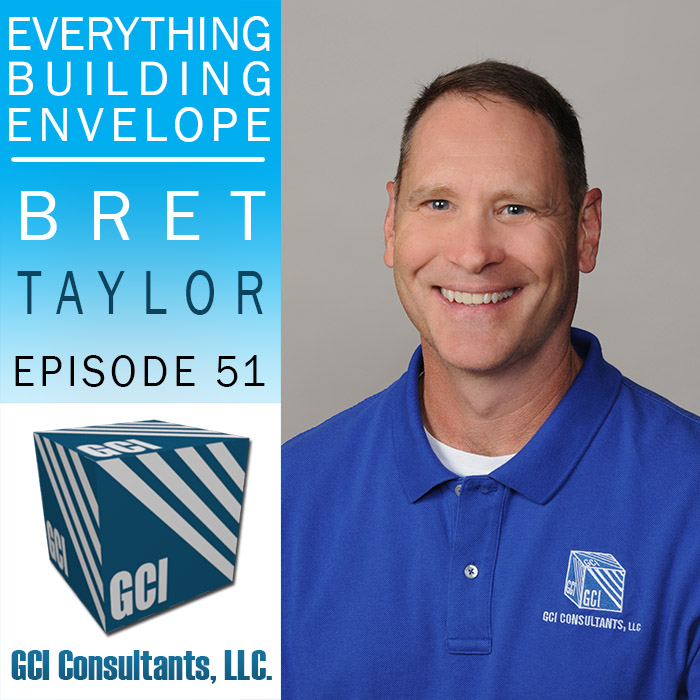
About The Everything Building Envelope Podcast: Everything Building Envelope℠ is a dedicated podcast and video forum for understanding the building envelope. Our podcast series discusses current trends and issues that contractors, developers and building owners have to deal with related to pre and post construction. Our series touches on various topics related to water infiltration, litigation and construction methods related to the building envelope.
https://www.everythingbuildingenvelope.com
*** Subscribe to the show and leave us a Review on ITunes!
Will: Hello, everyone. Welcome back to “The Everything Building Envelope” podcast. I’m Will Smith, president of GCI Consultants, and I’ll be your host today. Now, with me is Bret Taylor, a professional engineer and senior consultant, too, here at GCI. Bret is one of our consultants that also provides litigation support services. And today, we’re going to be talking about GCI’s approach to the providing this type of service. But Bret, before we get into the details of this, we probably have some people that listened the last time you were on, and maybe some that didn’t. So, maybe you can just give them briefly a little summary about yourself and your background.
Bret: Okay, sounds good. I’m Bret Taylor. I’m a professional engineer of 26 plus years, graduated NC State, University of North Carolina. I got my start like most engineers do in the design and drafting part of engineering and worked my way up, then started my own business, and did typical consulting for a while. Gradually, over time, that morphed into the forensic field where I would get calls from people to come investigate their building for different issues. Oftentimes, water’s involved, so that sort of led me to migrate into the building envelope arena. And so, today I found myself with GCI doing building envelope consulting.
Will: Great. Thanks, Bret. Now, today, we’re going to be talking about the topic of field water testing in forensic investigations. And water testing is a subject that we discussed in our podcast many times before. And in fact, Paul Beers and Jason Bondurant did a podcast just a few months ago about this. But today, we’re going to look at it in a little bit different perspective, that is, we’re going to be talking about water testing and forensic investigations as part of litigation.
Now, let me introduce this first by saying that GCI’s objectives in litigation support services are generally the same regardless of what side of the table our client sits on. Now, whether a plaintiff or defendant, we want to investigate a claim and render an opinion no matter how pleasing or how painful it might be to the client. And at the same time, however, we recognize that there’s a difference between the obligations of a plaintiff and the defendant.
Bret: That’s right, Will. The plaintiff has the burden to prove the defect in the case. And unfortunately, sometimes the building owner sees water coming in from an event, whatever that event may be, and they tell us that it appeared but that does not tell us exactly where the water is entering. So, we have to determine where it’s coming in, why it’s coming in and demonstrate that a problem actually exists that’s actually related to a construction defect in order to assist the client. And that could be, that water entry point could be anywhere, it could be the roof, it could be the wall in several different locations. It could be through penetrations to the wall, be it a window or a vent. It could be the sealants, it could be the paint. It could be maintenance or combination of all these things. So, in order for us to testify in a construction defect case, we need to identify and prove that defect.
Will: Okay, that’s good, Bret. But how is this, what you just described, how is this obligation different from the obligation that a defendant would have if they’re defending a case?
Bret: Well, the defendant doesn’t have the burden of proof. You know, in our court system, you’re innocent until proven guilty. So, they don’t have to prove that there’s a defect for the plaintiffs. So, they obviously can investigate the claims being made at their level, but they’re not required to prove the case against them.
Will: That’s true, but we often see water leakage that occurs and the plaintiff applies testing that sometimes implicates the wrong parties, ain’t that right?
Bret: That’s true. That is true. And so, at that point in time, perhaps, the defendant might want to do their own testing to illustrate that the test, that the plaintiff’s testing was done improperly.
Will: Right. In fact, you know, I can speak from some experience in this. I have been involved in some litigation cases in the past where an investigation wrongly implied fault to somebody, but it ended up costing a lot of money to a lot of different people, For example, one case in the town of Palm Beach involved a large estate in which the owner lodged a lawsuit against the developer and several of the defendants in it. It was a case that, actually, it went to trial and it was tried over several months. As a matter of fact, it was a multi-million dollar case.
We happened to represent a window installer in that particular case. And our position was that the plaintiff’s expert who did testing almost every single window and door in the home just simply did it wrong. It was improper, it did not recreate the leakage that the owner was complaining about. In fact, they made new leakage occurred in some instances. And it went it in a, like I said, to a trial for several months and instead of a $7 million jury verdict for the owner, they got a verdict in the low five figures, which was actually awarded because of what the jury considered to be bad advertising on the part of the developer. It had nothing to do with the windows and doors.
The exact opposite of that, I just seen…saw occur on a project down in Miami. Yeah, it went to trial just a month ago. And in that one, it was another large single-family home in which the owner’s consultant recommended that the owner have testing done but they never did it. So, they never proved that the cause of the leakage. And again, it went to trial, and in that case, I represented a window manufacturer on the defense, and we got a defense verdict.
And then another one I can tell you about is a large, multi-district class-action lawsuit, which involved 14 plaintiffs, you know, unnamed plaintiffs in 11 states. The plaintiffs’ expert performs the testing once again. It implicated the window manufacturer, but it did it wrongly, and they ignored all the other causes of water leakage into the building, which were clearly apparent, but they used the wrong test method and the test procedure and implicated the wrong party. And eventually, it got before the judge. And the judge throughout the plaintiffs’ expert’s report excluded it in its entirety.
So, it’s just three examples of occasions where one party in a case can be really very severely jeopardized if a testing agency or consulting firm goes about doing a poor job. So, Bret, let’s talk about, a little bit about what makes an inspection and testing proper? What is a good guideline, a good thing to follow here?
Bret: Well, there are different standards to follow. We can kind of get deeper into that. But let’s start out by talking about, in general, about a window or a door product. So, they are manufactured products, they’re manufactured to certain standards. And they have different performance requirements based on the type of unit that you buy. So, not all windows and doors are the same. They’re not all going to perform in the same way. So typically, what we get involved with in these forensic investigations are water leakage issues. So an analogy there might be, and most people are familiar with car doors and they have a gasket around the edge of the car door. And most people have probably been seen on TV a car that drove into a creek during a hurricane or a flood or whatever it is, those vehicles, they flood. So it’s got a gasket on the door, it keeps the rainwater out when you’re driving down the road. But if you inundate that vehicle, ultimately, it’s going to leak into the vehicle.
So, the same thing applies to windows and doors. If their performance level is exceeded, they can leak. So, one has to consider the conditions in the field, and you have to follow proper protocol in order to develop a testing program that’s going to actually properly test and discover where the water intrusion occurs.
Will: That’s all really good. And I admit, I’ve seen that, you know, the example you gave is a good one. You see that on the news often, and oftentimes, the example you’re talking about, the expectations of performance of a window are entirely different from various owners. So maybe this is a good point to talk about some of those guidelines of water testing and how they apply, particularly, you know, we’re talking about legal situations here, and why it’s important in a legal case to not just go out and put the window in a puddle, but maybe, for example, but maybe figure out a way to do it, right. What kind of standards are we looking at?
Bret: Right. So, there’s a couple of different groups that we referenced commonly. ASTM is one of them, and then AAMA the other one to. So, ASTM is known by a lot of folks. AAMA is not so known and we can talk about those two different entities separately.
Will: Okay, that’s good, Bret. And maybe before we discuss those important points of these standards, like you said, ASTM is well known, and maybe AAMA is not. Explain to our listeners a little bit about these organizations in their standards, ASTM and AAMA.
Bret: Okay. So, AAMA is the American Architectural Manufacturing Association. So, it’s an organization that publishes guidelines and standards related to the manufacturer application, installation, and testing of windows and doors. And then ASTM used to be known as the American Society of Testing Materials, but since then, gone global, and now it’s just known ASTM International. So, ASTM International is an organization with 12,000 plus members, it publishes guidelines and standards for many different things, anywhere from household goods to aerospace, and this obviously also includes building systems and their components such as doors and windows.
Will: Okay, super. So, when we’re called to investigate water leakage in a claim in a legal case, let’s talk about how these two organizations fit in and into the investigation.
Bret: Okay, well, probably the best place to start is ASTM E2128. So, that one is the standard guide for evaluating water leakage of buildings and walls. And then another one AAMA 511, which is the voluntary guideline for forensic water penetration testing of fenestration products. And for those of you guys that don’t know, fenestration is windows and doors essentially.
Will: Okay. So, you also, you know, a little bit, you mentioned, earlier you mentioned forensic. Explain to our listeners what’s meant by that, and how it’s different from other types of investigations.
Bret: Well, there’s a couple of definitions that are kind of floating around there. I guess, one definition could be more of a legal definition where it states that forensic implies that it’s in support of litigation. But I think over the years, forensic has morphed into being synonymous with investigative consulting work. So, ASTM E2128 references forensic in its verbiage, and AAMA 511 also references forensic in its title even. Those two standards just imply that forensic is for the purpose of investigating a condition in the field. In this case, we’re investigating water intrusion through fenestration products, it doesn’t have a specific definition, necessarily. It’s kind of broad.
Will: Okay. So, let’s talk a little bit more now about doing an investigation, and let’s say, it’s in a case that’s in litigation, whether we’re working for a plaintiff or a defendant. We already discussed the various organizations and the standards that may apply. And we talked about how the burden of proof is actually upon the plaintiff in these cases, but there are occasions in which a defendant may also want to go and do a thorough investigation and maybe even testing. So, let’s talk a little bit about, for example, these standards. So, let’s talk about the purpose of doing an investigation. Why should we do an investigation following a guideline such as, you mentioned ASTM E2128, why use 2128? What does it afford the user?
Bret: Well, in general, the intent is that there’s a laid-out protocol there that allows the user to craft an inspection or forensic evaluation that can not only recreate the leakage that’s reported to exist but also do it in a way in which someone else can repeat what they’ve done. So, it affords the other side an opportunity to test if they would like to in the same manner, so all parties can test in a similar way.
Will: So, it is an opportunity then to do an investigation that’s systematic, but reproducible?
Bret: Correct.
Will: Okay. So, doing that investigation, there are certain steps that the guidelines recommend, but they’re not all required. Is that correct? I mean, you can’t necessarily do every one every time?
Bret: That’s correct. And as long as you’re following the intent of the standard, that you’re capturing the data that needs to be captured to recreate the leak and illustrate where that leak is coming from, I think that would follow the spirit of the standard.
Will: Right. Okay. And, for example, as I understand it…For example, one of those things that it recommends that you do is, it’s called a document review, in which the investigator collects all the construction documents, like plans, specifications, performance records, all that kind of stuff that dealt with construction of the building. And remember, you mentioned building fenestrations, but of course, when we’re doing an investigation where we can’t just focus our eyes only on the fenestration, but we need to look at all of the building components that surround the windows, doors, and the wall construction, the exterior wall cladding in the finishes, the sealants, and all those kind of things. So, they’re asking you to collect all these documents. But in my experience, I don’t know about you, but in my experience, usually, those documents are not available. They often don’t exist. Have you found that to be true?
Bret: Absolutely. And that’s…so, even a lot of documents show construction that may not be consistent with as-built conditions either. And there could have been remodeling that had been done, repairs, maintenance, those types of things. So, you have to evaluate the conditions you have in the field with whatever documentation that you can acquire. And then with that information, hopefully, you can piece together the existing construction and perhaps some of the issues that could be occurring.
Will: Right. And you mentioned…you said one of the conditions in the field may not be the same as what was originally intended anyways. And one of the things that the guideline recommends is getting a service history of the building and the components. Is that where this falls in, service history?
Bret: That’d be part of it. Absolutely, one needs to figure out as best they can where the issues are reported to be. Some of that’s going to be within the service history document in the building, the maintenance records, so that’d be part of it. And then going back to the document review, one also has to figure out what the design concept is, so is it a drainage plan, is it sealed surface barrier system, is it a mass-wall system, you know, and what the cladding material is requirement for the installation, that particular cladding material. So, you’re trying to develop an overall understanding of how the wall should have been built, how it is built, and then also how it should be performing.
Will: Right. And each one of those things that you mentioned, like a drainage system, a surface barrier system, mass wall, and so forth, we could have a whole separate podcast on each one of those. So, we’re not going to go into all of the details of that today. But the point is that before or as part of an investigation, you need to understand how the building is supposed to be working.
Bret: Correct, correct. That’s right.
Will: All right. Okay. And then, once we have this background information, then we can get into doing the inspections, testing, so forth, analysis, and all these other things that go along with that. Let’s talk about testing for just a minute. And again, according to the guidelines that are published by ASTM 2128, for example, what should be the objectives of someone? If you’re going out there to do the testing, what are you trying to do by that?
Bret: Well, at the end of the day one is trying to recreate the leakage that’s been reported to occur or if the investigator can observe it themselves, or even if they can…if there’s no indication of where the leakage is coming in, if they can visually discern it, what they think is going on, they take all that information, they try to figure out, you know, where it’s occurring and try to recreate that leakage.
Will: Okay. There’s, in the standard, it talks about tracing leakage paths. And as I understand this, the way I try to explain it to people is when you’re standing inside the building, and you see water collecting on the inside, let’s say, it’s at the bottom of the wall, it is collecting on the floor. That tells you where the water appears, but it’s not telling you how it got there from the outside of the wall to the inside where it’s appeared on the floor. And that’s where the standard says, “Trace the leakage paths.” How do you go about tracing the leakage path?
Bret: Well, the short answer, I guess, is isolation. But, I mean, I’ve had instances in which even isolation didn’t do tracing the leakage justice because water travels or can travel in places that you may not think. But ultimately, what we want to do is we want to try to isolate the wall conditions so that we can test it incrementally. And then by doing that, we can hopefully isolate the entry source of the leakage.
Now, in the cases in which it’s not immediate around the opening, you may have a crack, let’s say, you know, a few feet away that you’re not aware of, water could be getting in through the building cladding in that location and traveling towards the window unit, and even manifesting, like you said earlier, at the floor and you may not even see it around the window unit.
Will: Right. There are occasions in my experience that the only way you can, even if you do the isolation like we talked about and we’ll probably talked about in a little bit more detail, a lot of times the isolation…for the benefit of the listener, what we’re talking about here is applying covers strategically on the outside of the building so that the various areas are not subjected to the water spray when you’re doing a water test. So, you’re only testing certain areas, in that way, you’re able to more better define the location where water is entering the wall on the outside. But even when you do that sometimes, for example, let’s say, you have a wall that you’re testing that’s 10-feet wide, and you narrow down to a section of the wall that’s only 1-foot in width. So, that tells you that water is coming in at that general area, but it’s like you talked about earlier, if we’re talking about a drainage design, water that’s coming into the wall, let’s say is getting past the stucco at that point is supposed to be collected and drained backed out. But if it’s not, it’s coming in, there’s still a defect that’s causing that to occur. And my experience is, the only way you can find that defect is often to do destructive testing, where you need to remove stucco or remove drywall in the inside and take part walls, take out windows, whatever, in order to find what is the defect that’s causing that leakage to occur. Do you agree?
Bret: I agree. And part of the standard actually requires that the drywall in the interior is removed around the windows. So, when you’re doing testing, you can observe the conditions where the water may be coming in, and sometimes, you do have to remove the cladding and the window. I’ve gotten lucky a few times, and actually I’ve been able to isolate, that was a kind of a unique situation [inaudible 00:24:07]. Yeah, typically, you got to do DT.
Will: Okay. So, let’s talk a minute about those tests. We’ve thrown a lot of things out here. ASTM has a test method out there. Explain basically what that is.
Bret: E1105 is ASTM water test method to chamber test. Essentially, it specifies the chamber that needs to be built and a spray rack that needs to be built and calibrated so that you can apply water to the outside face of the building. The chamber allows you to put pressure on the wall assembly and the pressure differential. You’re trying to recreate the wind conditions that are reported to have occurred when the leakage was occurring.
Will: Okay. And that comes from ASTM 2128. Also, they say that you’d need to recreate those conditions, but then, there’s the document by AAMA out there, AAMA 511, that gives some guidance for how to do that, right?
Bret: Right. So, AAMA 511 is the volunteer guideline for forensic water penetration testing of fenestration product, and that references the ASTM E1105 test method. So, they work in concert, so to speak, but 511 gives you a little more information in terms of performing a forensic evaluation using the ASTM E1105 standard test.
Will: Right. And it even gives you examples about how to determine those pressures to be used to recreate the wind-driven rain, I think, research the weather records, and all that kind of stuff. So, it gets into more detail that you don’t have in E1105, so that’s a big help.
One of the things that I think we ought to talk about here briefly is types of tests that might not be appropriate in doing. I mean, we see it happen all the time where, in fact, I mentioned examples where people did testing improperly. Give us some examples there of what type of things could be improper testing?
Bret: Well, improper application of the standards. So, for example, when you’re building up a building and installing windows that are new, there’s a standard that apply or several actually that apply to those products. One of them is AAMA 502, and that’s a specification for field testing of newly installed fenestration products. And that standard says, in a nutshell, that these products as they’re manufactured and they come off the assembly line, are going to perform at a certain rate with respect to water resistance. But when they’re installed in the field, we’re going to give a one-third reduction in that factory performance, because of the transportation, the installation, the effects of installation on the product being slightly at aplomb, those kinds of things.
So, that new standard would apply only if once you have been given your CO for the project, then that window is now considered installed and you can’t use that standard after that time. Sometimes, it applies a little bit further on. It’ll extend to six months after being installed, if you haven’t gotten your CO yet. But the purpose there is that’s a new product. Once you’ve gone past the new product stage of installation, you’re migrating into the forensic realm, and you have to use the AAMA 511 standard to test if there’s any leaks for that product. So, let’s kind of tie that together so it makes more sense.
So, if you install a new product, you have to use AAMA 502 to test it according to the required pressure for that particular product. If it fails, then you would correct whatever the failure is. And assuming that minor correction that you’d make, maybe it’s just adjusting the window or whatever, and it passes and you get your CO, after that date, if leakage occurs in that same product, it would become a forensic evaluation because it’s gotten CO or its past six months page. Let’s say that the window was installed a couple years ago, obviously, it’s past its six months and gotten its CO. So, now you’re starting with AAMA 511 to begin with.
Will: The six months is…
Bret: Yeah, cutoff date.
Will: The cutoff date. Okay. All right.
Bret: Yeah, that’s the cutoff date provided by the standard 502. So, if someone where to test an existing window that already passed the six months cutoff or gotten its CO, and they use that 502 standard, and test it to its newly installed field, water-resistive pressure, that would be an improper proper application, and they may be creating a new leak versus recreating leakage that’s occurred in the field. So that’s why AAMA 511 is important because it gives you the criteria that you need in order to evaluate the conditions in the field that created the leak, and then use that standard to test and rediscover or recreate the leakage.
Will: Okay. How about…I see this happen often is somebody goes out there with a garden hose and a spray nozzle, puts it on windows or whatever, is that appropriate?
Bret: Yeah, those are not appropriate on operable windows. They could be used as diagnostic tools but not an operable window. And that could create a new leak in an operable assembly.
Will: Okay. So, that gets back to what we were talking about earlier, when you were saying recreating leaks versus here we’re making a new leak. And, you know, there’s a paragraph in ASTM 2128, in Section 10 of that document that I always think is quite interesting. It says, “Creating new leaks during testing may be useful information, but it is not a valid assessment of the existing leakage problem.” So, basically, that’s saying you can go out there and test. And if you look at 2128, it lists out several different testing methods. But it’s basically telling you that unless you recreate the leakage, anything else is really of not a much value because you’re making leakage occur that would not normally occur, and your objective should be out there to find what’s going on by recreating the leaks, right?
Bret: Correct.
Will: Okay. And then another thing that I’ve often found is, in 2128, which is kind of telling about this whole issue is, in one of the appendixes to that document which deals specifically with windows and doors, it states, “Make a careful distinction between leaks caused by windows or glass metal curtain wall systems and leaks that originate from other wall components that appear to be window or curtain wall leaks on the interior.” Windows are often wrongfully blamed for leaks because the interior symptom of a leak appears at a window even though the cause is elsewhere. This gets back to what we were talking about earlier. You might find water on the floor. It could be right below a window. But unless you do the testing properly, you’re not going to know whether it was a window or a flashing defect or a sealant defect or what the defect is. Is that right?
Bret: Or a combination of all those.
Will: Or a combination of all. That’s right. So, I guess what we’ve talked about here are various aspects of testing and how to use those in a litigation. And I guess these are just some examples. Getting back then to, we talked briefly about isolation, explain that a little bit more detail.
Bret: So, that could also be used inappropriately, or, typically, it’s not done at all. And that would be the appropriate part because you’re not making sure that you’re testing recreates the leakage, then you could have several different entry points that apply to different components of the wall construction. And you’re not defining why the water’s coming in and where the water is coming in. So, the lack of or improper use of isolation would be another inappropriate testing method.
Will: Yeah, that’s all true. And another thing that I see happen quite often is people use improper pressure differentials. And what I mean by that is, we talked about the need to recreate leakage at the conditions which have occurred in a forensic evaluation. And oftentimes, we’ll see a firm go out and want to do water testing based upon performance standards when the windows were brand new, or they just totally ignore the weather conditions that have been known to occur. And they test it at weather conditions that far exceed anything that’s ever been experienced at the project site and they create leakage, which again, is leakage that is not representative of what’s been known to happen.
Bret: That’s right. And sometimes, if the pressure that has occurred in the field and you’re trying to go back to that wind event, if it exceeds the product capability, then you’re supposed to go back and test at lower pressures before you test it to higher pressure to demonstrate that wind event did exceed the capacity of that window, and they don’t necessarily do that. So yeah, those are some good examples of how consultants, you know, fail to comply with the recommended guidelines, and the results just weren’t good for their client.
Will: Right. And I think we’ve seen several cases where either a plaintiff or defendant ends up spending a lot of money chasing a case by hiring an investigator and consulted firm, and then they see that money go to waste because of the failure to execute an investigation that’s in general conformance with the published guidelines.
Bret: That’s right. So, I’ll summarize, the litigation matters where water leakage is alleged and requires some pretty much a methodical investigation. You’ve got to follow the guidelines, at least the spirit of the guidelines, which is the majority of them. There’s some flexibility in utilizing the guidelines given your unique situation in the field, but you have to follow the spirit, and have a reproducible testing and trace the leakage that describe the type of investigation. So, that testing differs from the testing that’s used in new construction in that thing. A lot of people aren’t necessarily aware of that, and that’s what makes the difference between forensic testing and new construction testing.
Will: Right. And failure of a consultant firm to do an investigation or perform their work in a manner that generally complies with these guidelines ends up placing their client’s case in jeopardy.
Bret: That can happen, absolutely. Well, Will, that was fun. I enjoyed the talk today. I appreciate it, big issue, and that’s something that we here at GCI deal with every day. I’d like to thank everyone that’s listening on the call today. If you want more information about GCI consultants, we’ve got some videos and things like this podcast on our website that show water leakage testing. You can find that at www.gciconsultants.com. And that’s consultants with an S. If you’ve got some specific problems that you’d like to talk about, you can reach out to us today at 877-740-9990. And again, that’s 877-740-9990. Thanks again, everybody. I look forward to talking with you next time in the future on “Everything Building Envelope.”