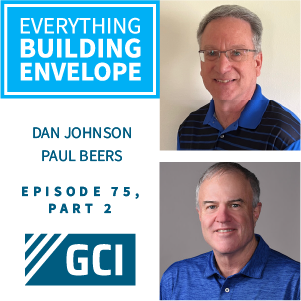
About The Everything Building Envelope Podcast: Everything Building Envelope℠ is a dedicated podcast and video forum for understanding the building envelope. Our podcast series discusses current trends and issues that contractors, developers and building owners have to deal with related to pre and post construction. Our series touches on various topics related to water infiltration, litigation and construction methods related to the building envelope.
https://www.everythingbuildingenvelope.com
*** Subscribe to the show and leave us a Review on ITunes!
Paul: Hello, everyone, welcome to “The Everything Building Envelope Podcast.” This is Paul Beers, CEO and Managing Member for GCI Consultants and I will be your host today. We’re gonna do Part 2 of a podcast that we started last month with our Senior Consultant, Dan Johnson, and dig deeper into the topic of windows and doors and testing and whatnot. Dan joined our team of experts in April of this year, and he’s been a really strong addition to our team. So welcome back, Dan.
Dan: Yeah, thank you, Paul.
Paul: Yeah, so we had a really interesting discussion, there was so much to talk about that we decided that it’d be good to have a Part 2 here. And I’m really excited about that. Just for those that may not have listened to Part 1, maybe you can give a little run-through of your background before we get into today’s topic.
Dan: Yeah, definitely, I’d be happy to. I graduated with a BSc. degree in engineering technology with a quality control emphasis. And out of college, I went right into the building and construction industry as a test technician for a number of years testing windows and doors for air-water, structural performance, acoustic performance.
And then as I progressed in my career, I’ve built a couple of different laboratories for architectural testing and then one for Intertek Testing Services, continuing in the air, water, structural testing of windows, doors, curtain walls, mock-ups. And then also in the thermal testing for U-value and concepts and resistance factor testing. A little over 34 years of experience in both laboratory and field, quality control, and forensic testing and valuation services.
Paul: Cool. So let’s talk a little bit about…so you’ve been with GCI now for what like about six months, I think, and coming up on six months. So what have you been doing since you joined GCI and what’s your role at this point?
Dan: My role at GCI has been a new position has kind of been evolving. I’ve been assisting with not only the GCI podcast and blogs, but as I’ve become acquainted with GCI customers, I am the window expert for GCI Consultants. And what that entails is basically going on-site, reviewing claims that are potential litigation claims, and just confirming that the windows and doors have been installed correctly, tested correctly. And then assisting window manufacturers in the final result of litigation claims, depositions, court appearances, or testimonials, and that type of thing.
So the role is continually evolving. I’m also just, you know, with my testing background and becoming…I’m accredited for field testing, so I’m assisting with that transition. So I’m working with training our technicians and the other consultants.
Paul: So on the consulting side, who typically would be your client, or who would hire you for a GCI assignment?
Dan: Typically, it would be either the window, curtain wall, storefront fenestration, product manufacturer, or their representing attorneys who would hire me.
Paul: And so you also mentioned that you’re helping GCI with AAMA accreditation for field testing, which is something we’ve never had before. Not necessarily needing it for forensics and things like that, but it does provide another layer of depth that we’re really, really excited. So, thank you for helping us with that. And obviously, that’s right in your house.
Dan: Yeah, I think that’ll just give GCI another set of credentials because basically, you know, being accredited, that just kind of shows that we do ongoing training, and our quality control system is what is ISO accredited and it adds credentials to the testing that we do both in new construction, you know, quality control type testing. And then also like you said it’s not needed for the forensics, but it gives some of our technicians, you know, that they have been trained on the proper processes and how to perform the tests.
Paul: Yeah, very cool. So last episode, we talked a lot about laboratory testing with your wealth of knowledge there. Some of the different tests that were required, air, water, structural, and some of the other tests. And we talked about some of the standards organizations and things like that. What we didn’t get into that I’m really excited about talking about today is fieldwork, field testing. So we were in the lab in the first episode and now Part 2, we’re gonna go out into the field. How’s that sound?
Dan: It sounds great. It’s just a natural transition. Like we mentioned on the last podcast is that you can have a phenomenal window that test great in the laboratory, but if it’s not installed correctly, then you will potentially have issues. And to determine where the issues are is through laboratory testing and investigations. I mean field testing investigation, I’m sorry.
Paul: A question that I’ve been asked many times by consumers and even contractors is, if a product is tested in the laboratory, why do I have to do a field test now?
Dan: Like I’d mentioned field testing basically it’s a quality control check to verify that there wasn’t any damage to the windows during shipment and also during installation. And it’s also to verify that the installer installed the product correctly per the manufacturer and code regulations. It’s more of a quality control check just to verify that everything was done correctly. The second mention you can have a great laboratory-tested window, but if it was not installed correctly, you still will probably have issues.
Paul: And the other thing that comes to mind is the laboratory, obviously, that the window is installed in a certain way in accordance with the manufacturer’s instructions. But it couldn’t possibly account for all the varying field conditions that you would have with, you know, surrounding conditions of maybe stucco or wood siding or brick or a variety of other things. So can the field testing account or evaluate that interface as well?
Dan: That is correct. A typical laboratory test you’re testing the product only. So everything interior of the installation is what you’re testing. So in a laboratory test, you’re really not testing the different sealing or flashing techniques that could be accounted for and/or should be accounted for in a regular field application.
So yes, the field test is not only testing the window product itself, but it is testing the different variations in building construction because as everybody knows during the construction, there isn’t a perfect surround opening, you know. So the installers use the various flash and sealing techniques and the field tests is just to verify that they’ve done it correctly.
Paul: Yeah, so we’ve been talking about water testing. What other tests can be done in the field or would be recommended for an evaluation?
Dan: Yes, depending on the location, i.e. your weather conditions you can also run an air infiltration, and an exfiltration test just to verify that all the weatherstripping contexts are correct and then your product performs per industry standards.
There are also a few other more on the forensics end of it, you know. You can do frost point testing on the insulating glass with ASTM F574 I’m sorry and 576 that you can do just to verify if there are issues with glass that your insulating glass is fogging up some, you can make a quick frost point just to verify that the seal has not broken down from a previous storm or from the age of the product.
And then there are also different dynamic type of testing that can be done where you can actually put a dynamic blower on the outside and do a water investigation test also. But yeah, it’s done only water penetration but you can do air filtration frost point just do some destructive type. You know, take it off to have more forensics but take it off exterior components just to see how everything was installed and then flash if it was done correctly.
Paul: You mentioned in the first episode some of your credentials and one of the things that you said was you’re a fenestration master professional, and I believe that’s an AAMA certification. Can you talk a little bit about that?
Dan: Yes, I am. Basically, what that entails is there’s…I don’t remember the exact number of segments, but it’s close to 20 different segments of the window and door and installation in the, you know, facets. That the person that needs to review and learn goes all the way from just the basics nomenclature of the products, all the way through the different types of sealants, the different types of finishes on different products, all the way through the different types of installations that can be done. And then also going through the various test procedures, kind of highlighting the different test procedures.
And then once you’re done with that training then you take an exam. And you have to have a minimum of 80% correct on the exam. And if you are, then you’re considered a fenestration master professional. And then what that credential entails is for your AAMA 502 and 503 tests, they require that you have a master professional on staff that is reviewing and training of your technicians and all of the reports.
Paul: My understanding is there’s not a lot of AAMA master professionals out there, is that correct?
Dan: That is correct. Of course, the AAMA credit test agencies that are out there will have at least one on staff. And there are several window manufacturers that have sent their lead field people for that training also. But yeah, I don’t know the exact number, but yeah, there isn’t a lot.
Paul: Yeah, I thought I had heard like 125. I mean, like, you know, in the general scheme of things, not a big number.
Dan: Correct.
Paul: Let’s talk about some of the test methods that are used in the field. You just mentioned AAMA 502 and AAMA 503. And I know yesterday, you mentioned AAMA 511 as well. Let’s talk about 502 and 503 first, and then 511 which is a forensic standard we’ll save that for last.
Dan: AAMA 502 we just completed…I happen to be the chair of a task group that just did the revision of a document. And we just completed that in 2021. That test procedure is…I’m gonna get the exact title for everybody. It’s Voluntary Specification for Field Testing of Newly Installed Fenestration Products.
So basically, that is more of a quality control-type test procedure. It’s for both air filtration and water penetration. And when we say newly installed, we mean that it’s probably they have been installed within six months.
So, like we started the podcast, it’s a quality control test procedure to confirm and verify that the windows and doors have been installed per the manufacturer’s requirements. Typically, what ends up happening is I’m installing a five-story apartment building, for example, it may have 400 different window or door components. What the architect will do is say, I wanna test X percent of the units as they’re being installed to verify, you know, the different crews, the different individuals are all installing them correctly.
So that X percent, you know, could be from 1% to 3% or sometimes higher. You know, so as things are being installed at 50% of installation is what I recommend is test one or two. That way you can catch things if there are issues you can catch them before everything is completely done. And it’s a lot easier to…you know, say a step was missing in the flashing, for example, it’s a lot easier to fix it on the fly before everything is installed.
The other requirements for the 502 is you test air filtration for ASTM D783, which is, you know, the standard test method for field air leakage. And then for the allowable, if not specified by the architect, AAMA 502 recommends that the allowable is 1.5 times what was listed in the performance requirements section of the project documents. And the reason for that is just to account for field conditions.
And then the water penetration testing is done per ASTM 1105. And kind of in line with the additional air leakage allowance AAMA 502 unless the architect specifies differently, they recommend that you test it two-thirds of what’s listed in the performance requirements section for the test pressure.
And then there’s different areas of water leakage that have definitions in the document, you know, just to kind of verify, you know, if things are leaking and if water is visible if that’s going to an issue or that.
And then AAMA 503 we’re actually in the process right now of revising that document. It’s in the final ballot so the new documents should be coming up here, this year is the plan for publication. And AAMA 503 is the Voluntary Specification for Field Testing of Newly Installed Storefronts, Curtain Walls, and Sloped Glazing Systems. So where 502 was meant for basically window and door products, AAMA 503 is meant for the commercial fixed type of products.
And basically, it has the same requirements. We tried to mirror each other in these rewrites. It sits for…it’s been installed within six months of installation. And have the same air filtration and water penetration requirements, you know, 1.5 times allowable and then also, you know, two-thirds of the product performance section requirements.
So those are basically the two quality control procedures. There is one other…the one that is out there it’s AAMA 501.2. Many may know that as the hose spray test method. So basically that is done without a pressure differential across the product, it’s just done on the exterior, you know, with a calibrated spray nozzle.
One thing that I’d like to highlight for everybody is to make sure that that test method is meant for non-operable products. And I should say even more than that non-sashed products. You can have a fixed window that has a sash that is fixed in place. That test method is not meant for that it’s meant storefronts, curtain walls, and sloped glazing systems. It’s a nice quick quality control check.
Paul: There’s some controversy around that one in my view and how to properly use it, you already…you’re all over that, you already hit on it. But, you know, the title…and the most recent addition to that is AAMA 501.2-15, is that correct?
Dan: That is correct. Yep.
Paul: Yeah, so the title is Quality Assurance and Diagnostic Water Leakage Field Check of Installed Storefronts, Curtain Walls, and Sloped Glazing Systems. So that seems to be…basically the way the title reads it seems they’re limited to commercial rather than residential type of applications. Is that correct?
Dan: It can be used for residential applications but like I mentioned it would have to be on a direct glazed product. Because it spells out in the scope pretty clear, scope of purpose that it’s not appropriate for [inaudible 00:19:59] and operable components. Operable windows and doors. So if you have just a direct glazed fixed window, it can be used on a residential product but not anything that has a sash.
Paul: So you mentioned just backing up into…come back to 502 and 503 for a second. You had mentioned that the test method used there is ASTM E1105. Can you talk a little bit about what that is and how it relates to the AAMA standards?
Dan: Yeah, sure. ASTM E1105, it’s the water penetration test. It’s the test method that tells you how to perform a static pressure differential water test. So basically, the way the test is done is you build a chamber either on the interior or the exterior surrounding your product that you wanna have test, that you’re testing. And that chamber is built typically…it can be done many ways, but it’s typically built out of wood framing with a clear plastic attached to it.
And that is attached, you know, to this round of the window or curtain wall, whatever you’re testing. And then you have a blower system that can either…if you’re on the interior side, will create a vacuum between that plastic chamber and the product to simulate your different wind speeds based on the performance criteria that’s listed in the project specifications.
And then there’s a method A and method B that is performed. So you can either have a straight 15-minute static test where you’re pulling the pressure the whole time. Or you can have a cyclic static test where you have five minutes with pressure applied, one minute where the pressure is released, five where they’ll apply it, one is to be released.
And then the whole while during this testing, there is a spray rack that is put on the exterior side of the product that will apply a uniform water spray across the entire opening. And the water sprayed you have to be between 4 and 10 gallons per hour per square foot when you do the calibrations. But that is equivalent to approximately 8 inches an hour of rainfall. It’s not a driven water spray it’s more of a misting type water spray.
But you are definitely saturating the exterior of the opening that you’re testing along with that static pressure vacuum that’ll draw simulating the wind. So that’s how you get the different test pressures and different criteria. You have the exact same water spray, but you increase or decrease the vacuum that is being applied depending on the conditions that you wanna test to.
And then during that testing, the reason we use clear plastic is you wanna be able to make observations on the interior side of the product including, you know, the rough openings surrounding it to see if any water leakage is occurring.
Water leakage could be from air leaks that are in different weather strip joints. So you’ll have a bubbling effect that’ll splash on your plastic pipe and that would be to the interior of your home. Or it can overflow the seal, or you could have a frame corner that may leak that may have been broken during transit. Or you could just have water that keeps out as current from the installation.
So that’s where a lot of the…when we mentioned about the training that is required, you know, having your technicians being trained to be able to diagnose and figure out where the water is coming from is very critical.
Paul: So you mentioned the water spray rack and the 8 inches per hour that they face have based it on in the past. I noticed in the latest version of ASTM E1105, they don’t reference that any longer. And in fact, they have an addendum that says, you know, that there’s been objections to that being too severe in the past and it’s really not intended to replicate anything only to be a baseline to compare products. Do you concur with that?
Dan: Yep. I agree 100%. The calibrations that are done on the spray rack it’s a catch box that are one-foot square sizes, and then you put that in three different locations of your spray rack depending on the size of your rack. And then each of those areas has to be within, you know, 4 to 10 gallons per square foot, and then you have to have a total of 20 before, you know.
So the 8 inches I’ll be honest, I don’t know exactly how that was calculated. I’ve never done it myself. That’s just what from the years of running the test, that’s a number that I’ve always been told, you know. So it’s more of, you know, having your spray rack calibrated for your gallons per hour per square foot.
Paul: That number came long before you or I were ever involved in this. And we’ve been around for a long time.
Dan: I agree.
Paul: It was an old deal. And I guess the other thing to just kind of add on to that is that the water spray that’s supplied from a calibrated spray rack does not look extreme. I mean, it’s kind of a uniform spray that goes over the entire assembly. And I can just speak from personal experience living in Florida that I’ve seen actual rainfalls put a lot more water in place than the spray rack does. So 8 inches sounds like a lot, but the reality is anybody’s seen the spray rack, it’s really not severe.
Dan: Yeah, it sounds like a lot but it’s more of a…depending on the type of spray nozzle that you have. But it’s more of a real heavy misting [inaudible 00:27:11] to make sure that your exterior of the product is saturated is basically what it is. Yep, you’re correct.
Paul: Is it possible to use ASTM E1105 by itself without reference to any of the AAMA standards?
Dan: Yes. The ASTM 1105 is a standalone document. It’s actually…you know, it’s kind of, you know, bizarre or maybe not bizarre. But it’s actually the other way around you can’t do AAMA 502 without 1105. So, 1105 is basically the base document and it just tells you how to perform the test.
Paul: Yeah, it doesn’t tell you what pressures to use or things like that. So, it’s a test method, not a specification, correct?
Dan: That is correct.
Paul: So let’s segue into AAMA 511.
Dan: Yeah, AAMA 511 basically is the forensics version of the documents. I was actually elected to the task of chairing that one. We just did the rewrite on that one also. So the actual title is “Voluntary Guideline for the Forensic Evaluation of Water Intrusion at Fenestration Products.”
So, basically, this procedure is meant…you know, I guess, there’s several different reasons. If during your quality control testing you do see leakage then you kind of go into AAMA 511 and use 511 as more of the investigative to find out what exactly…to pinpoint where that leakage happened.
Another reason for 511 is like we mentioned before 502 and 503 are meant for products that are within six months of installation. After six months, then you have performance 511 which is a little bit more involved. The prep is more involved. And then also for the forensics end of it when previous water leakage has been observed, you use 511.
You know, when I mentioned the 511 is more involved the reason it’s more involved is basically what…you have to do your homework prior to the testing. So, if at all possible, you wanna interview the building owners to find out exactly where and when water leakage has occurred, you know, has been observed I should say.
So, you know, say during the month of July, there was three occurrences where water leakage was observed and during…you know, so we can get those dates, and then you can do the investigation back to find okay, what was the exact windspeed during that rainfall? You know, to determine what the average wind speed was.
The next step is to look at if that storm occurrence happened to be above the performance level of the product that was installed, well, you know, then you gotta kind of put your thinking hat on. Okay, the storm, you know, was more than window or door, you know, was certified to so it wasn’t a once-in-a-lifetime occurrence. But yeah, that’s kind of where the homework has to be done.
And then this AAMA 511 it’s based off of ASTM E2128 which is, you know, the ASTM International method of doing the investigative testing on a facade. Yeah, it’s more of…AAMA 511 is more of the investigative forensic portion of testing as documented.
Paul: You mentioned…well, let me ask another question first. So AAMA 502 and 503 are for the first six months as a quality control check during or immediately after construction. So what is AAMA 511 say about when it’s appropriate to use that document?
Dan: In the scope, it doesn’t 100% spell it out exactly when. It’s appropriate to use it basically after six months of installation, and if water leakage has been observed. If water leakage has been observed, then you go into 511 which kind of gives us step by step process of figuring out where that leakage occurred at, was it a pinhole in the weather barrier, was it a window frame corner? It kind of gives you where to dig in and gives kind of a guide on how to dig in.
Paul: Now let’s talk a little bit about…to bring this all together. Let’s talk a little bit about forensic investigation, which is one of the things that you might be tasked with on assignment, you know, now that you’re at GCI. So what are the…if you get a call from a potential client, or you get hired on a project that, you know, maybe it’s a litigation maybe it’s not, you know, there’s always the threat seeing the world we live in now.
But say, you know, [inaudible 00:33:21] and that office or hotel or whatever, and, you know, we’re getting water leaks. [inaudible 00:33:30] guy goes out there and he’s cocked and hasn’t fixed them, and we don’t know now, can you help us? What would your approach be to a forensic investigation of water leakage and kind of like what you do in the beginning into actually getting into the fieldwork?
Dan: Okay. Yeah, basically the steps that I follow is during that initial phone call just gather as much information as you can. Quite often the phone call will come from an attorney. So, they won’t have a ton of information that they can tell you verbally initially at least.
But kind of the steps is, you know, I ask for all of the basic project documents that they have available just to kind of, you know, see the as-built, that can kind of assist a person into figuring out where to dig in if there is an issue. You know, instead of just going haphazard at it look at all the project documents, which are the drawings and the project specs.
And then kind of talking to the building owner, and do an evaluation of the design concept because forensics can not only be because of water intrusion it can be because of, you know, vapor drive or different things like that, and it might not even have anything to do with the rainfall. So, just figure out what the design concept that the building was meant for.
And then interview as many people as possible that are in the building that have seen and/or experienced, you know, the issues that are being investigated. This is quite often, you know, the building maintenance people. You kind of get determination of the service history, you know, that has occurred on the facade, and also the leakage or, you know, the issues history so you can kind of start setting up a game plan.
Once you have kind of a good idea of the design concept and the service history that is going on, then I like to perform just a visual inspection. Where if you need to you get up in a man lift or, you know, swing stage, or whatever is needed, and then go and do an inspection just to find out, okay, based on all the data that we’ve collected visually, is there something that really jumps out at you.
And then if there’s something really just kind of jumps out at you, then you determine if you need to do investigative testing. And the investigative testing can be either destructive, or it can be non-destructive, you have to make a determination there. The non-destructive testing is like…well, we were talking about kind of doing the ASTM E1105 water spray testing or doing some 501.2 water spray testing. And just kind of…along with isolating different areas just kind of okay, try to recreate the leakage that has been occurring.
And then once you complete your non-destructive testing, then you can look at it and figure out okay, should we start tearing things apart? And then, you know, start taking the exterior and/or the interior off layer by layer and find out okay, we know we have a water entry occurrence happening in this upper corner of this storefront window area.
Let’s start digging to find out okay, was something that’s left once in the flash and incorrectly, was a ceiling joint missed. Just digging in and finding out what is actually wrong. And then once you have that done, then you do an analysis. And then that analysis can be, you know, just kind of stating what we saw, or it can get as involved as giving…I like to say repair A, B and C. Suggested you know, repair methods. Let’s repair A just kind of making it work. B is more involving and costly. And then C is basically sometimes just tearing it out and putting it back in again and doing it correctly.
One of the biggest things that I didn’t highlight but I should have is when the non-destructive water spray testing when that is being done, the purpose of that is to recreate a known leak. That’s why that service history portion is so important to identify where leaks have occurred.
You know, there’s been too many times where I’ve been out on investigative testing, you know, and we’re testing one area because that’s the area that has leaked over time, then all over sudden by the test facility agency, there’s an aha moment. We have a leak that never ever leaked before in the past. And they say, “Oh, we got a leak over here.” And you can kind of say, well, that’s fine, but that has never leaked in the past. So that means that you’re potentially over-testing that area. But the purpose of the AAMA 511 and ASTM 2128, is to recreate known leakage points.
Paul: So when there’s a leak it could show up in a lot of different places, obviously, you can see maybe water running down on the inside of the window or glazing system. You could have, you know, a very common area where you see water often is near the bottom frame corners. You could have it an operable product maybe being blown in, percolating in over the seal. You could have puddles on the floor, you could have ceiling stains on the floor below, a lot of different possibilities.
So, what do you need to do when you’re testing to basically be able to…say there’s water paddling on the floor and then you do a non-destructive test and the puddle shows up on the floor. What do you need to do to figure that out?
Dan: Basically it’s a step-by-step process. What you need to do is…at least the steps that I take is I make sure…you know, once we recreate the leak make sure that everything is dried out and the leakage has stopped. Then start from the lower points, do water spray testing at the lower points, and progress your way upwards on the facade. And then the whole time basically isolating different areas.
Ideally, you wanna test one…you quite often have an idea of where this water is coming in. So on the exterior with different types of sealing techniques using, you know, tape sealing plastic is isolate on the exterior so you’re only testing one component or one joint at a time.
And then as you’re testing really start from the bottom. Of course, you start at the top and it starts leaking or you don’t know exactly where that leakage occurs, you start at the bottom, work your way up. And then as you get to a certain elevation on the exterior facade then you can pinpoint okay, this is where leakage has occurred.
And once you recreate that leak then the next step would be to start digging in and potentially doing some destructive, you know, just kind of digging things apart and seeing, you know, exactly what’s behind the stucco metal panels or whatever you have
Paul: I know a sore spot a lot of times when we’re going in into occupied buildings typically residential, it is…or fear or maybe by the people who are, you know, the owners or whatever whose windows and doors are being tested with removal of interior finishes as part of the testing process. Why is that necessary and why is it important?
Dan: You pretty much have to tear the interior part. What I like to do is basically pull up all of your sheet rack or casing returns, you know, surrounding the opening your seal stool for your investigative portion. And then you want to pull your sealants and different things like that that are between the window and the rough opening.
If you can get a decent visual there, then you don’t have to go any further. But sometimes you have to go further and you have to start cutting out the interior sheet rack walls typically below the window openings. So you can get observation to the interior of the exterior sheathing of the building.
The reason for that is as you’re running these water tests, you know, you may just have a pinhole in the sealant or flashing tape, you know, maybe 4 inches up on an alien flange jammed. And then as you’re running the test, you know if you have the interior already taken out, you can actually see the stream of water, a trickle of water that could be coming in.
So by having the interior, you know, pulled out for the forensic evaluation testing is very critical in order to determine where…you know, because it’s one thing to know where the water enters the building, but then it’s another to see where it’s actually visible on the interior side also.
Paul: So what goes, you know, for better or for worse, what goes hand in hand with the forensic work oftentimes is a dispute or what I like to call it the blame game. But probably a more eloquent way to say that would be attributing responsibility to, you know, whoever maybe didn’t do things correctly, that would cause this issue. So that’s where obviously, expert witness work comes in. And, you know, as I say for better for worse, it’s kind of a natural extension of all this. So can you kind of maybe run through some of the things that occur when you’re a litigation expert on a case
Dan: Basically when I’m a litigation expert what I look at is okay, I look at the project drawings, and then I also look at the manufacturer’s drawings and installation instructions and drawings. And then as we do the investigation just kind of keep on peeling back the onion so to speak. Is okay, was this installed per the project drawings? If it was not, okay, then which trade in this building was responsible for what portion of the install and the weatherproofing? And then kind of just keep on digging back and find it okay, which trade and what was responsible for what area.
And then just keep on expanding onto that system seeing okay, you know, what was it…like my main area of expertise right now is in the window industry. You know, was it or wasn’t it a window issue? If it was well, you know, then, of course, then you talk to…my customer would be the window manufacturer and say here’s where some of the issues were.
But if it wasn’t, then I just keep on digging back and digging in and finding out okay, which areas of the actual installation and the construction of the building weren’t done according to the project specs and according to industry standards.
Paul: And then on the litigation side typically, would you produce a report with your finding?
Dan: Yes, depending on where it works, you know, at what stage of litigations, then yes, it’d be a report either disputing or contradicting or agreeing to, you know, the initial plaintiff report, you know, with all of their findings. Or just a report basically stating okay, here’s exactly what I saw, you know, here’s exactly how it was installed and what the testing showed. And then issue that report to the customer which can be used, you know, for the litigation portion of it. Yes.
Paul: And just briefly, tell us about your experience with the litigation process, depositions, trial testimony, things like that.
Dan: Yeah, as far as my experience, like I said I’ve been doing the forensics and litigation work for probably about…I don’t know the exact first one was about 20 years back was the first one that I got heavily involved with. And it’s basically just gathering all the facts, all the data, making sure that everything is correct.
And then if the mediator can’t…during mediation if things can’t get resolved, well, then it gets into the deposition stage, you know, where you’re basically being interrogated and asked questions by all the different sides’ lawyers just to kind of see where…so that they can determine where I’m coming from and more or less my experience.
And after the depositions, you know, the multiple sides, you know, can it come to a resolution, then it does come to the litigation portion. And then basically get on a stand and basically backup all of the test reports that I’ve written, and everything that I’ve seen and just, you know, give my side of the story.
Paul: And you’ve testified in court before?
Dan: I guess I’ve done it about half a dozen times, yes.
Paul: It doesn’t usually come down to that but sometimes it does. And that’s a whole different ballgame, I guess, than anything else. You had mentioned…just to wrap things up. You mentioned that you were involved in…we talked about the AAMA standards, some ASTM standards. Can you just…you mentioned you’re involved in some of that, it sounds like you’re very involved. Can you just kind of summarize that as well?
Dan: Yes. At GCI we’re members of the FGIA, which is the parent organization for the AAMA documents. And I’m the vice chair of the Method of Tests Committee. That committee, what we basically…you know, as the title says we oversee all the different tests procedures, and test methods that AAMA looks at and produces.
So the ones that I’ve been very heavily involved with is the revisions of AAMA 502 and 511, which those two we have just recently completed in ’21 and ’22. AAMA 503 actually, within the week now we’ll have the ballot and the resolutions on the ballot. So that one should be coming out in 2022. And then we’re going to start digging into the AAMA 501.2. And basically, all the documents are very well written good documents, but as everything else over time, things change and you always wanna refine and make them better.
So, that’s kind of my involvement with AAMA. And then also I’m on the Installation Methods Task Group and committees just to kind of review their different installation guidelines, you know, that they have. Then I’m also a member of the ASTM E6 Committee, which the…E6 Committee along with a lot of other things, it basically entails all the different, you know, building facade testing methods and procedures and guidelines and that type of thing.
So I’m on that committee which the meetings come up fairly shortly. You know, we’re just continually revising and refining, and making all the documents more user-friendly is basically the best way of saying it. Because myself included once you get a bunch of techy individuals in a room, you can make them pretty difficult to read. So our approach now is to kind of, you know, make them more user-friendly.
Paul: Yeah, sometimes you need to have…some of them can be really difficult. So that’s a really good charge is to try and make them simpler. Dan, you’re a wealth of information, really interesting and we’re super excited that you’re part of the GCI team now. And I think we both agree that it was really a good fit. And also thank you for doing not one but two podcasts to kind of go over everything. So it’s been really great and thank you so much.
Dan: Yeah, it’s been my pleasure. And it’s only been a few months, but it has been a great job transition. And I think that GCI and myself I think we complement each other very well.
Paul: Yep, agree 100%. So thanks again. So in closing, I would like to thank our listeners for listening to our podcast today and I invite you to take a further look at our GCI consultant services on our website. You can find that at www.gciconsultants.com. You can also reach out to any of our experts at 877-740-9990 to discuss any of your building envelope needs. Thank you once again. I look forward to talking with you next time on our “Everything Building Envelope Podcast.” So long everyone.