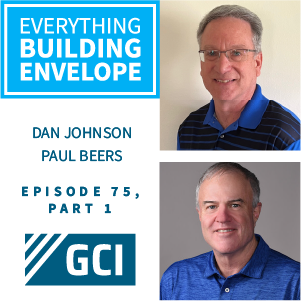
About The Everything Building Envelope Podcast: Everything Building Envelope℠ is a dedicated podcast and video forum for understanding the building envelope. Our podcast series discusses current trends and issues that contractors, developers and building owners have to deal with related to pre and post construction. Our series touches on various topics related to water infiltration, litigation and construction methods related to the building envelope.
https://www.everythingbuildingenvelope.com
*** Subscribe to the show and leave us a Review on ITunes!
Paul: Hello, everyone. Welcome to the “Everything Building Envelope” podcast. This is Paul Beers, CEO and managing member for GCI Consultants, and I will be your host today. I thought it would be interesting to talk with our very own senior consultant, Dan Johnson about his experience in the world of windows. Dan joined our team of experts in April this year, and is a strong addition to our team. So, Dan, welcome.
Dan: Yeah, thank you, Paul.
Paul: So, Dan, why don’t you tell our listeners a little bit about yourself, and then we’ll go back and do a deeper dive?
Dan: Okay. Thank you, Paul. Yeah, and I’ll be glad. As I mentioned, you know, thanks for allowing me to join GCI. And, kind of, my experiences. My college education is I was engineering and technology with a quality management emphasis. And then when I graduated college, of course, the typical, you need the experience, and so I got a job as a test technician with Twin City Testing Corporation.
My role there, I was their laboratory air, water, structural, and acoustical technician. We tested anything from doors, windows, to interior walls, exterior walls. And then also, I was responsible for doing the field testing for windows, and doors, and curtain walls for air infiltration and water penetration testing, and also, the acoustical testing in the field. I was there for a couple of years, and then when architectural testing wanted to expand into the Midwest of the United States, they contacted me to assist. And there, we built a lab. That was in 1990. And that lab, we did the full series of testing for air, water, structural for window and door manufacturers. We also tested on insulated glass and also safety glazing.
We were a small lab at the time. We had… I’ll be honest, we had three employees. But as we grew, my responsibilities also grew along with that. So I was responsible for, initially, you know, for basically all of the field testing, which ranged from, you know, quality control testing, all the way through forensic evaluations. And then as we grew, we outgrew the space. And we moved into a larger space, which allowed us to expand into the thermal testing realm, which thermal testing is basically, you know, determining your U-values and your condensation existence factors based on the NFRC and AAMA test procedures. And so I assisted our company, and we built the thermal chamber. And at that time, it was Saint Paul, Minnesota.
And then also, run, did the installs, the evaluations. I became the person responsible charge for NFRC. And then also along with thermal testing, we expanded into more of the insulated glass testing, which we tested mostly for the Insulated Glass Certification Council, and then also for ALI and MAM [SP] for their certification programs.
We lasted there for about 15 years. During that time, we were purchased by Intertek Testing Services. And then we ran outta space once again, and then we moved into a new building. So then, during that time, I assisted in design and did the full move to a new building. And one of the biggest reasons for the move there was we were able to… We had over 30 feet of interior wall or ceiling heights. We expanded into the full-service mockup testing also.
And so during that time, I was the person responsible in charge for thermal testing, the air, water, structural testing, the mockup testing, and the insulated glass testing. And then also, I grew into managing more of the field testing. Prior to that, I didn’t… I don’t have an exact count, but it’s definitely thousands of field-testing tests that I performed personally. And then I’m also an administration master professional certified individual, and so which allows me, you know, to do a full review of both residential and field quality control testing, and then also to continue divulging into the AAMA 511, which is the forensic evaluation.
And then one thing that I forgot to mention is during this whole time, I was also… A few of window manufacturers. So I was their expert when it came into litigation, you know, potential litigation, and those types of cases.
That’s, kind of, a background on my work history, which goes, kind of, hand in hand with the actual hands-on. I was and still am a representative with various trade organizations. I’m currently on the Demonstration and Glazing Industry Alliance. I’m the co-chair of the Method of Tests Committee, which what that involves is we review all the different test procedures. Primarily, the field test procedures, but pretty much all the test procedures. We just continually review them and change them as they need to be revised and they need to be changed. Then I’m also a member of the E6 Committee with ASTM International, which the E6 Committee, you know, deals primarily with the exterior building components of the building, which goes along, you know, with my FGIA associations. So that’s, kind of, a recap of my history. I don’t know if there’s anything you’d like to talk, you know, a little bit more in-depth, Paul?
Paul: Well, there’s a lot [inaudible 00:05:36] but that’s impressive. You know, I know that you did have an experience with the lab field and whatnot, and then the litigation work as well. Let’s try to break this down a little bit, and let’s just talk about some of the things that go on in the laboratory. You mentioned several times air, water, structural. So can you just talk a little bit more about why do they do that, number one? And then number two, what’s involved with that?
Dan: Yeah. So, yeah, most definitely. I apologize for, kind of, breezing over that a little bit. When I mentioned air, water, structural, that’s just, kind of, a synonym for the certification testing that is done by window manufacturers. And the reason that you want to have quality control testing done and certification testing done on by window and door manufacturers for their products is, you know, every window manufacturer has a full team of engineers, and they’re continually designing and making new and improved window products.
In order to confirm and verify that those window products are to industry standards, which the industry standard right now is NAFS, which is National American Fenestration Standard. Which is, kind of, when I mentioned air, water, structural, that is, kind of…it’s more than just air, water, structural, air infiltration, water penetration, and structural performance. So those are the three main components that gets tested to in order to determine the performance levels, performance grades of different window and door products.
So the way it’s set up is a window manufacturer will have a new design they want to bring into market. They will typically both have… They have a bunch of their R&D testing done already to, kind of, get most of the bugs worked out. But then they’ll send it to a certified and accredited lab, which is the one that I manage and work for. And the lab would test it to the industry standard, to that mass standard.
And then you would test it for air infiltration, which is typically done at 1.57 PSF, which is equivalent to a 25-mph wind. And then also if it’s a higher-level architectural-grade window, then you’d test it with 6.24 PSF, which is a 50-mph wind. You test it both for infiltration, which is, you know, the air being drawn into the building. And then also exfiltration, which is the air being exhausted from the building. And then you measure the amount of airflow that occurs at simulated wind speed, and that gets converted into cubic feet of air per minute per square foot of window opening. And there is…based on the different performance levels, there’s a certain amount of air that can leak through the opening in order to pass the test.
Once you have passing tests for the air filtration, then you move on to the water penetration testing, which what that entails is you dry a static load from the outside of the window in to simulate different wind speeds and test pressures. During that time, there is a water spray that is put on the exterior of the opening also that is approximately eight inches an hour of rainfall. That’s a really heavy mist is basically what it is. And then you run the test for a residential-grade or light commercial grade. You run the test for four five-minute cycles, which what a cycle is you have five minutes with water spray plus pressure, then you have one minute where you reduce pressure to zero to simulate, kind of, you know, let the window, you know, relieve itself. And then five pressure, one-off, five pressure, one-off. And then five pressure. And then you complete with the one-off. And during that time, you can’t have any water overflow the interface of the window opening or through any frame corners. And this is done at various test pressures to determine what performance grade. Of course, the higher the test pressure, the higher the performance grade.
And then once the water penetration testing is done, and then you go into uniform load structural testing, which basically what that is you increase the amount of pressure to simulate the wind speed that the window is going to be rated at. So, like, if you have a design pressure of 35 PSF, which would be a PG 35 in the industry. You test it for a 35 PSF, you measure the deflections on the key components. For most grade windows, the lower the residential and light commercial grade windows, it says four information only. But then when you get to the architectural grade window, then your window can’t deflect more than the length of that member divided by 175 in order to get a passing result.
Then once you have your 35 done, then you go to one and a half times that, which is called the structural overload. And that structural overload testing is done more or less as a safety factor. You know, the window is designed for that 35 PSF performance grade because it has both air, water, and the load deflections. But then you wanna make sure that, just as a safety factor, you’ve got 1.5 times that.
So, for example, we’re using a 35 PSF, for example, 1.5. So you test it for a positive 52.5 PSF load on the window for 10 seconds. And during that time, you can’t have any excessive permanent deformation, or you can’t have any components that break. And then after completion of that, then you’ll do the negative, which, you know, negative 52.5 PSF, which is you’re trying to blow the window out of the opening. And then the same criteria. You can’t have any excessive permanent defamation, and can’t have any breakage.
So once you pass those three key components of the NAFS standard, if the manufacturer is happy with the performance grade that they received, then you move on. If they want it to go higher, then you inch in your way higher at 5 PSF increments. But it has to pass both the water penetration at that higher level, plus the structure performance at that higher level. Once you get to the level that the manufacturer would like to rate their product at, then you move on to the forced-entry resistance test.
What you’re trying to do is you’re trying to manipulate the locks with a few different components and tools, and then you also put force on the locks just to make sure that they’re structurally solid. So if somebody wants to break in, you know, the homeowner can feel confident that window and door are going to be able to sustain different modes. There are four different classifications, you know, for forced-entry resistance. And you have a grade 10, 20, 30, and 40, and each one being a higher grade.
Once you’ve passed forced-entry resistance, there are several different component-type tests depending on the type of product that if you have a double hung window, you do operate at force, and you do a couple of different other torsion tests. And then if you have a crank-out casement window, there’s a side load test. And there’s a couple of other tests to make sure that if you happen to leave your window open and a heavy gust of wind would blow, it’s not going to break the hinges, and the operator, and blow the window off.
Once all the testing is completed, what the test lab would do is they will actually cut up the window and then compare the key components of the window to the manufacturer’s drawings. Basically, we wanna make sure that the window that was tested is the window that they make every day. So there’s typically…you have your stash component, and your frame components, and your structural members. You’ll compare, you know, a half a dozen of the key measurements on their drawings, and then verify that they’re within tolerance. And if they’re within tolerance, the test lab will write up a test report detailing how the window was made, all the test results, and then also include a copy of the approved drawings, or rather, the verified drawings. And then that will get submitted to the manufacturer, who in turn will submit that to a certification body.
And then the certification body, basically, they’re responsible, you know, for the follow-up quality control checks that are done, which are basically in-plant inspections. There are several certification programs out there that will do follow-up inspections to confirm. They’ll take the test report that the lab wrote, and then they’ll confirm that during their inspections that the windows that are being made on the manufacturing lines are the same as the window that was tested.
Paul: It’s very rigorous.
Dan: I’m sorry. Go ahead. It definitely is. And the reason is you wanna make sure, you know, that the consumer is getting a quality product. And, you know, the way to get a quality product is to make sure that you have third parties. You know, the test lab is a third party that is checking up on the manufacturer. And then the certification agency is the third party that is making sure that the test lab is doing things correctly, and then also doing the follow-ups. And so you wanna make sure, you know, not only for a consumer but the two key components that are vital for the consumer are typically the water resistance of the product, and then also the structural load of the product. Because everybody knows, you know, once you get water in the building, then you gotta, kind of, go to the next level and try to figure out what’s going on. So, you know, the more robust the products can be, you know, the less likely that water will be, you know, damage during a windstorm of the product.
Paul: So let me ask you a couple of questions about the water and the structure, which are the two main things. On the water side of things, I’m gonna put my expert hat on for a second. And, you know, I’ve been in hearings and whatnot where opposing experts, who may or may not be window experts, make statements like, “Oh, windows are supposed to leak.” Is that true?
Dan: No. No, windows are never designed to leak. Quite often, I get those same questions. And quite often, it all depends on the definition of leakage, I guess. This is probably the way of looking at it. I’ve been in several depositions where it’s a horizontal sliding window or it’s a horizontal sliding patio door. And during a storm, water is visible in the sill of the window. But it does not overflow into the residence, but there’s water visible. So some homeowners and i.e. experts say, “Well, that’s water leakage. ” And it’s really is not.
The sliding window product is, kind of, made to accumulate water, and the sill height or the cavity of the sill, depending on the rating that you wanna have, the performance level you want will have various levels that water can only be pushed up so high depending on the wind speed that’s out there. And then once the storm is over, it just drains back out. So, yes, water can be visible in those tracks during a rainstorm. But is that considered water leakage? No, it is not.
Paul: So what’s the exception to that rule with regards to wind storms? So if you have a window that’s rated… Well, your example of the 35 PSF certification pressure for a window, is the water test pressure also 35, or is it different?
Dan: Very good question. Yup. For laboratory testing, if you’re testing a residential or light commercial window, your test pressure is done at 15% of your design pressure. So, for example, the test pressure on our PG 35 window, your laboratory test pressure would be done at 5.25 PSF. And then once you get into the field, just due to different applications, and installations, and just different field components, the water test pressure that you would conduct in a field test for AAMA 502, 503, or 511, you know, any of those documents would be done at two-thirds of that laboratory test pressure. Or for this case, it would be done at, you know, 35.
Paul: So if you’ve got a window that’s got a water test pressure of 5.25, what is that about in miles per hour, if you know?
Dan: 5.25 would be right around 40 mph.
Paul: Yeah, so somewhere in that, give or take. So if you had a wind-driven rain storm with 60-mph winds, what could happen?
Dan: The window product could leak. And the reason I say that… I’m not saying that it would leak, but the potential would be there because, you know, the window wasn’t designed, in that case, designed for that storm that was out there. Most window manufacturers, you know, have different series of windows that are meant for different areas of the country, or different environmental conditions. So, like, in the case that you mentioned, a 60-mph wind, if it was a PG 35 window, that storm would be above what the window was rated at, so there is a potential that it would leak, yes, just because it’s above the… I’m not saying that it would, but there’s a potential that it would.
Paul: Yes, if you’re in an area like a coastal area where you could get 60 mph wind-driven rain, obviously, it would be appropriate to have a higher-rated product in that environment. And likely, the code would require a higher-rated product, is that not true?
Dan: Yeah, that is correct. Yeah. You know, kind of, the guideline is ASCE 7, which doesn’t really give the water performance rating, but it’ll give, you know, the minimum structural rating of, you know, the products, and walls, and roofs, and the whole building that would be needed for that geographical area. And then based on that, and then you can backtrack and figure out what the actual water rating would be.
Paul: Yeah. So on the structural rating with the safety factors [inaudible 00:20:32] a window that’s rated at 35, and it’s tested to 52.5 at the 1.5 safety factor. Why isn’t it rated at 52.5 since it passed the test?
Dan: It’s rated at the 35 because that’s the performance level of the pride that the unit should be able to sustain a 35 PSF storms for….or should be able to sustain many, many of the 35 PSF storms. So because it’s rated at that, so if, you know, anything that 35 PSF or below storms that occur, the window should continue to perform at the level for many of those storms. The 52.5, the 1.5 times that, as we mentioned, it’s meant as a safety factor. So if it gets a numerous 52.5 PSF wind loads on it, then, you know, it’s not meant, you know, to perform after that wind speed. It’s meant to stay in the opening, and keep the homeowners and everybody safe.
Paul: So you had mentioned…was it NAS standard?
Dan: NAFS, National American Fenestration Standard.
Paul: NAFS, which used to be ANSI/AAMA 101?
Dan: Yup, it’s the North American Fenestration Standard, yeah. It used to be AAMA 101. It still is AAMA 101. It’s just that NAFS is, kind of, the shortcut for it instead of saying it all out, yes.
Paul: Yeah. So NAFS is where it lays out all this criteria for certification of products, is that correct?
Dan: Correct, yeah. NAFS lays all of the test methods and test procedures that are required to satisfy a product. And then the certification programs. Each one will have their own individual criteria that they have above NAFS. But, yeah, NAFS is the industry standard that envelopes the test procedures that are done.
Paul: And who are the organizations that are involved with publishing or keeping up with that document?
Dan: There are three organizations, one is FGIA, which I had mentioned, it’s the Fenestration and Glazing Industry Alliance. You have WDMA, which is the Window and Door Manufacturer Association. And then you have CSA, which is the Canadian Standard Association. Prior to… You’re gonna catch me on the exact year. I can’t think of the exact year off the top of my head, but there were two. In North America, there were two different testing standards out there. Canada had their own standard, and then the United States had their standard, AAMA. And then the two countries saw so much alliance, that’s when they developed NAFS, and just all three organizations are working together now.
Paul: And then you also talked about once you complete all the testing, then you go to a certification organization, or I guess that’s what I would call it. What are some examples of who that might be? Obviously, AAMA is one.
Dan: Yeah, AAMA is one, WDMA, which their certification program is called Hallmark is another one. Keystone Certification is another. You have, NAMA, North American Manufacturer Association. And then there are a few other ones also. Like, for example, you know, Miami-Dade County has its own program, but their program doesn’t test, you know, to the NAFS. But those are probably the key ones.
Paul: They all use some of the basic standards, and then maybe put their own wrinkle on it?
Dan: They all have passive tests. For all of them, the product has to be tested to the NAFS standard and pass the NAFS standard for all of those programs. What they’ll do is they’ll… Probably the differences are, you know, the frequency of retesting, you know, to verify that the windows are still being made. You know, it can be once every 10 years that a window gets pulled off a line and sent to a lab, or once every four years. You know, each one has their own wrinkle there. And then the other wrinkle is basically, you know, the frequency of inspections that are being done.
Paul: So let’s shift gears. You mentioned thermal, and I know thermal is becoming more and more… There’s a bigger and bigger emphasis on thermal from the way things used to be. So tell us a little bit about the thermal requirements and the testing that’s done. I know there’s calculations also. Because nowadays window manufacturers not only need the performance criteria, they also need the thermal information as well, is that right?
Dan: Correct, yeah. So thermal is primarily being regulated through NFRC, which is the National Fenestration Rating Council. The way that window manufacturers will get their product thermally certified is it’s initially done through computer simulations. You know, so what a window manufacturer will do is they will send all of their window drawings along with profile drawings, the assembly and profile drawings. They’ll send their drawings in electronic format to an NFRC-accredited simulation lab, and then they’ll also have all of their different types of glass options that they want to offer. Yeah, I still remember one which just amazed me. Probably about 10 years back, there was a manufacturer that had 3,112, that number sticks in my head, 3,112 different glass options that they offer in their window products. When I say glass options…
Paul: Wow.
Dan: …that means, you know, different types. Yeah, it was wild. When we did our report, it was wild. So that’s why computer simulation, you know, came out probably about 20 years back. Prior to then, you had to physically test every product in order to get the U-value ratings. Now, it can be done by computer simulation, which really streamlines it. Once all of the different glass options are put in, then the computer, kind of, just crunches the numbers out. It’ll have a U-factor, a solar heat gain coefficient, and a visible light transmittance factor, you know, for each of those different glass options. So you’ll have this large matrix of glass options with those ratings. And then what gets done is the manufacturer, along with the simulation lab, will typically pick one of the best U-value rated product glass option. And then that option will get manufactured and sent into the test lab, who will install it into a thermal chamber, which is a different name for it, it’s a guarded hot box. And we will test it for NFRC 102.
And that test procedure is, basically, you’ll have a perpendicular wind on the… Let me backtrack a little bit. The chamber is two rooms separated by a wall. On the one side, you have, you know, the room is kept at a cold temperature, typically right around zero degrees along with a perpendicular wind being blown on the product that is installed in that wall. On the opposite side, you’ll measure the amount of energy that it keeps…you know, to keep that room at 70 degrees. And then that amount of energy gets converted into your Watts, and then it gets converted into a BTU per hour, per square foot, per degree Fahrenheit temperature difference between interior and exterior, and then which is your U-value. And then that U-value is compared to the simulated U-value, which as long as they’re within tolerance of each other.
If they’re within tolerance of each other, that means that the window manufacturer can actually make a window with the way their drawings show, and the way they were simulated. So if they match, then the window is torn apart once again, compared to the drawing just like a water-structural program. And then the test report of that product line is validated. So then what the manufacturer will do is they’ll send that simulation matrix report to a certification agency, who will, in turn, upload all that data, you know, to a certified product directory, the NFRC [inaudible 00:29:03].
And then consumers can go into that directory. And depending on the location and the requirements that they have for the residents, they can pick and choose the window and glazing option that is needed, you know, for that location. It’s to help the consumer, you know, to give it an even playing field since all manufacturers, if they have to simulate and test to the same standards, they’re all rated through the same procedures. Then they can pick and choose the one that’s best for their location.
Paul: So you mentioned consumers. So if I’m a consumer, you know, all these terms I don’t know what they mean or what they’re for, so let’s go through that. What is a U-value?
Dan: A U-value is basically the amount of energy that conducts through a product. That’s pretty simple terms, but it’s basically the amount of energy that transmits through a product. So the lower the U-value rating, the better the product is at not allowing heat to transfer through.
Paul: So the U-value is basically… I mean, is that, kind of, like, insulation as far as, you know, the better it is, the more resistant it is to heat or coal going in or out?
Dan: Correct. Yeah, basically, the U-value is the reciprocal of the R-value. Yeah, so if you have an R-value, you know, of insulation. You know, like, you have an R-30 wall, your U-value would be 1 divided by 30. You know, so that’s what your U-value would be. So, yeah, they’re basically the same thing. They’re just reciprocal of each other.
Paul: And then you mentioned solar heat gain, what’s that?
Dan: Correct. Solar heat gain is the amount of heat that transfers typically mostly just through the glass. So it’s the amount of heat gain that the product will allow from the sun, basically through solar radiation. If you put some low emissivity-type coatings or tints on a product, it will deflect the solar radiation back out of the building. So your solar heat gain will be less, which is what you need, you know, for the southern half of the United States. For the northern half of the United States, quite often, you want it to have… You know, in the cold months, you’d like to have that solar heat gain. You know, so there’s different types of coatings that will allow the solar radiation to come through in order to assist in heating up your homes. So depending on where you are in the country, in the southern portion of the United States, you want to have a good solar heat gain coefficient. And then in the northern half, you want to have it so it allows some through.
Paul: So the Minnesota glass is not the same as the Florida glass?
Dan: No, it is not. No, the Minnesota glass will typically have, you know, your… It’s a low-emissivity coating. Typically, they’re selective, so they just allow certain rays. And it will allow the solar radiation to come through. And then when it tries to go back out of the window, depending on the [inaudible 00:32:11] it’s on, it’ll bounce it back to keep the energy to stay inside your home. In the south, you don’t wanna have that solar heat coming into your residence, into your home, so it’ll block it right away and keep it from coming in.
Paul: You know, I put new windows in my house in Florida maybe five or six…maybe even longer than that, six or seven years ago. And, you know, they weren’t that old, they had tinted glass at the time. And the new windows had the low-E coating on it, and it was a very noticeable difference when the sun hit it. With the old, the tinted glass, the sun would hit it, and the room would get hotter, and hotter, and hotter. And the low-E glass, you know, really did a nice job. You could still feel the heat coming through, but not nearly as much as before that.
Dan: You know, technology has come a long way. You know, I remember back when… The house that I’m in right now was built in the ’60s. And when we moved in in the ’90s, it had this clear glass, you know, because, in the ’60s, there really wasn’t such a thing as any type of low-E. And, you know, right away, I put the windows. After the first winter, I should say, we put all the windows in, and you can definitely tell the difference now.
Paul: And then the third thing that you mentioned was visible light transmission?
Dan: Correct. Yes, that’s basically… When you had mentioned about your windows from five or six years ago, they probably had a fairly heavy tint on, which deflects, you know, the visible portion, you know, of the sunlight out. But you still have your infrareds and that type of thing, which is what low-Es work on, is more in the infrared portion.
So the visible light transmittance. You know, depending on the type of building that you have, and where you’re at, they’re typically done via the tints that are put on the glass, and that’ll just collect out the visible portion of the sun rays. It does assist with some solar heat gain, but it’ll assist with user comfort, you know, so it’s not always bright in your house. You know, it also assists with some shade of the different furnishings inside your home.
One of the kind one of the tradeoffs that you need to look at is where it’s been shown that for a person’s health, you want to have as much sunlight as possible, so you don’t wanna make it too dark if you don’t allow any sunlight in. Because then if you make it too dark, then you have to turn the light bulbs on, on the inside of your home, so using energy then. You know, so it’s, kind of, a catch-22. But, yup, the visible light transmittance is basically the blocking of the visible light of…
Paul: I know. You know, from thinking back to my projects that I’ve worked on as a design consultant or a construction consultant, solar heat gain and visible light transmittance are a big deal with architects. They want to, you know, obviously, keep the heat out or in wherever the project is. But at the same time, they want to have as much natural light as possible. And not too much. You know, not too much so it’s bright. You know, there’s always… You hear these horror stories about, you know, people move into a building, and it’s reflecting off the one next door or whatever, and now they all have to wear sunglasses sitting at their desks. But to get that balance right is a really big deal I know with architects these days as far as energy. And then, as you said, the user comfort.
Dan: Yeah, correct, yup. Commercial structures, that’s probably one of the larger things. Yeah, you’re correct.
Paul: One other thing that you mentioned when you were talking about thermal testing, in the beginning, was condensation resistance. Is that a rating, or how does that fit in with everything that we’ve been talking about?
Dan: Yeah, the condensation resistance. There’s a couple of different ways that it’s being determined. It’s actually more than a couple, but the main ways are NFRC is doing it via simulations, it’s NFRC 501. And then there’s also the AAMA 1503, which is a physical test. But, yeah, it’s a rating. It’s a comparison rating for the AAMA 1503. It goes in numerical five increments. And the higher the number, the better resistance to condensation that the product has. And the test is done… Basically, while the U-value test is done, the condensation resistance factor test can be done also. And the way it’s determined is you put different thermal couples, and we attach them to the interior of your window or door on the glass and then also at key locations on the framing of the door. You know, so you measure the temperature of the interior surfaces of the product. And then through calculations, then your CRF, your condensation resistance factor is calculated. And like you mentioned, you know, the higher the number, the more resistant to condensation that product is. It’s not saying that condensation won’t occur. it’s just saying that, you know, as a rating system between product A to product B, if product A has a CRF number of 40 and product B has a CRF number of 45, the product B will be more resistant, you know, to the potential condensation developing.
Paul: So I think about all of this, and I think the average consumer… I know the average consumer and I think maybe even a lot of professionals don’t really grasp how much technology is involved with windows, and doors, and all the things that are evaluated, and all the things that need to be considered. And, you know, it’s more than just looking out through a piece of glass, and we open, and close it, and walk through it. There’s a lot of other factors. And this has been really interesting. I have a lot more that I want to go over with you, and I think that this is just screaming for a part two to this podcast. What do you think about that, come back? Because I want to go through all the fieldwork, and the expert work, and things like that, so I was thinking maybe we’d do that in another podcast. Is that okay to you?
Dan: Yeah, I think that makes total sense. Yeah, it’s always good to have, kind of, the background information, which, you know, I believe the background information is more of the laboratory and design, and that type of aspect. And then, you know, a podcast too could be, you know, how is that actually taken into the field for different types of settings, so that is correct.
Paul: And that’s where it all can go haywire, correct?
Dan: Exactly. Because I get asked all the time, “What windows should I put in my house?” And, you know, I say, “You know, it all depends on the look that you want.” And then I also tell them, “You can have a lower performance grade window. If it’s installed perfectly, it will perform great. But you can have a high-performance grade window in the lab, and if it’s installed poorly, you’re gonna have problems.” You know, it all comes to fruition in the field.
Paul: Yup. Well, listen, Dan, you did a great job explaining some pretty complicated technical stuff, and making it real and understandable, so I thank you for that. And I look forward to the next part two of this. And thanks so much for your time today, and, as they say, “We’ll do it again.”
Dan: Thank you for having me. And like I mentioned initially, it’s been a pleasure being on board with GCI Consultants, and I’m looking forward to more, and more, and growing. Thank you.
Paul: We’re all super excited about it. So I’d like to thank everyone for listening to our podcast today. And I invite you to take a further look at GCI Consultant Services on our website at www.gciconsultants.com. You can also reach out to any of our experts at 877-740-9990. I’ll say it again 877-740-9990. Send us any of your building envelope consulting needs. Thank you once again. I look forward to talking with you again, and, Dan, also, on our next episode on our “Everything Building Envelope” podcast.