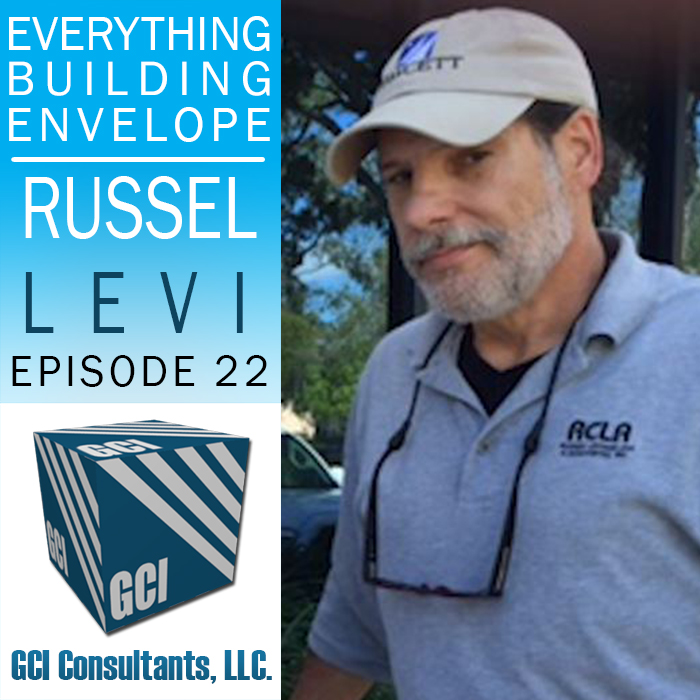
About The Everything Building Envelope Podcast: Everything Building Envelope℠ is a dedicated podcast and video forum for understanding the building envelope. Our podcast series discusses current trends and issues that contractors, developers and building owners have to deal with related to pre and post construction. Our series touches on various topics related to water infiltration, litigation and construction methods related to the building envelope.
https://www.everythingbuildingenvelope.com
*** Subscribe to the show and leave us a Review on ITunes!
The Everything Building Envelope Episode Transcript:
Paul: Welcome back to the Everything Building Envelope Podcast. I am really excited about our guest today, Russell Levi. Russell just started working with GCI, he brings a lot of knowledge on the roofing and waterproofing side of things. Welcome, Russell.
Russell:Hi Paul, good morning.
Paul:Yeah, really glad to have you here, and you know, we’ve, obviously, been working together for a little while now and I’m very impressed with your knowledge and abilities on it. We’ve got some difficult roofing projects that we’ve got started with, so I thought maybe that would be a good thing to talk about today. It’s interesting, we are well into the teens on the podcast episodes, and we haven’t talked about roofing yet. So, I know that there’s a lot of interest with that and the listeners will really wanna hear what you’ve got to say. So, before we do that, can you just tell us a little bit about yourself and your background?
Russell:Well, I started a roofing consulting company, by the seat of my pants, in 1986, after opening a new engineering office for a structural engineering company, back when. And I had my own company for 25 years in the Baltimore, DC, area, and structural engineering company for 9 years, under the same roof there. And most of our clientele is up and down the East Coast. We did a good number of projects in Florida, as well. But we also had to put up with things like snow and ice, and freeze and thaw conditions that you’re not so accustomed to, here, in Florida. But, for the most part, roofing principles apply the world over, and there are some advantages to certain types of roof covering systems. And we say “roof covering systems” to distinguish it from roof, which refers to the entire assembly of the structure, etc. But most of my clientele, a good mix of private and public… We’ve done a lot of work with both new construction and also existing construction, in coming up with plans to retrofit existing roofs, whether we’re removing them and rebuilding them, or redesigning them. So, we’ve had a lot of experience on coming up with solutions for existing issues, as well as new construction, and value engineering and just value. That’s what I do.
Paul:And that’s exactly what you jumped into with us here at GCI Consultants, is we’re working on a really large project, a big roof. It’s actually in Texas, not in Florida. We are addressing some issues that they’re having and how to get them the best value going forward with the repairs. So, today we are gonna talk about the advantages and limitations of PRMA, IRMA design configurations for roof covering systems. And what I wanted to ask you before we even dive into that is, could you talk a little bit about what, these are obviously acronyms, PRMA and IRMA are?
Russell:Right, well PRMA, the acronym, I think these have been around probably 25 years or so, is Protected Roofing Membrane Assembly. Where IRMA… And some people remember it by Inverted Roofing Membrane Assembly, or, it really means, Insulated Roof Membrane Assembly. But the key word here is it’s inverted. In other words, it’s an upside-down roof.
As you know, most design configurations for roof covering system is, you have your roof deck structure, you have your insulation layers, mechanically fastened or adhered, and then the membrane goes on top, whether it’s a built-up membrane or a single ply membrane, etc. So, you have roof deck, insulation, membrane on top. In an inverted system, the membrane goes directly on the roof deck. And then the insulation goes on top of the membrane, and then the insulation, which is an extruded polystyrene, you know, the blue board, like Dow STYROFOAM, or the pink board, like FOAMULAR, which is impervious to moisture, of course.
So, you have roof deck, membrane, insulation on top of the membrane, and then there’s a filter cloth, and then there’s a ballast. And it could be a crushed stone, or it can be concrete pavers, or a combination thereof, that holds the insulation down in place to keep it from floating or blowing away. And so there are many advantages of this type of configuration. So PRMA or IRMA really refers to a configuration. It doesn’t refer to any certain proprietary product. So, that configuration can be used, and it’s also often used on plaza decks, terraces, protected balconies, in a waterproofing situation that’s insulated. So, there are many advantages of this type of configuration, and there are also some limitations.
Paul:So, when you say limitations, one thing I was thinking when you talked about ballast, is that that’s a big no-no in high wind areas because, well with gravel, particularly, it can become flying debris. Is there a workaround when you get into high wind areas, to not have that issue?
Russell:There is. We’ve done many coastal… You know, along the East Coast, and Maryland etc., where we use concrete pavers. And along high wind uplift areas along the roof perimeters, sometimes there’s additional pavers, there’s additional weight, or even strapping, that you actually attach them to one another so they can’t go anywhere, and it’s proven very effective. And it’s actually… When you tackle the ballast situation on a high wind or coastal situation, it’s really a huge advantage, particularly on that type of roof, that’s subject to possibly hurricane projectile damage, impact damage, etc.
One of the many advantages is the membrane never sees the light of day, it’s never exposed to the weather directly, and it’s also fully adhered to the roof deck. So, if you have a puncture, if you have a hole, you know exactly where it is because moisture doesn’t travel between the fully geared membrane and the roof deck. Whereas in a conventional system, you punch one hole in the membrane and you can chase it forever, it will drive you nuts.
But, there are other limitations with regard to ballast. There are other limitations in that…due to the fact that one needs a ballast, the roof deck structure, the structure must be able to hold the weight of the ballast, which is never any less than 10 pounds a square foot. And depending on the pavers, or what you’re using as ballast, it may have to put up with 15 to 20 pounds a square foot. So, usually these types of configurations go over the top of concrete decks and/or I put them on metal decks too, where we add a substrate to the existing metal deck first, like a gypsum board, etc., and go to that. But many roofs are designed for a ballast load, but may not have a concrete deck, so those are workaround’s.
Paul:So, you’re talking about adhering the membrane directly to the deck?
Russell:Right.
Paul:Does the deck have to have a slope to it, or can you put it on a no slope or a flat deck?
Russell:That’s one of the beautiful things about an armor roof. You can definitely put it on a sloped deck, but in… Many older buildings, for instance, for whatever reason, have a dead level, concrete roof deck. You find that a lot in DC, Baltimore, and the Northeast concrete structures, but also coastal structures, as well. And so, the beautiful thing about this PRMA, or this inverted configuration, is that, as long as the roof drains are in at deck level, or slightly sunk into the deck, as they should always be, the water is removed from the roof by displacement.
So, what happens, imagine you have a dead level deck, you have membrane, and say you have three inches of standing water. Well, you put the insulation board, this extruded polystyrene, which actually has small channels cut out along the edges, and then you ballast it, so the water’s actually displaced. It has no place to go, displaced by the insulation, and the insulation isn’t buoyant because it’s held down by the ballast. So, the water perks down, and it’s directed to the drains, at the drainage level, at the membrane level, so the water is literally displaced. Like if you have a cup of water, you put your fist in it, and you push it down, the water comes out, it has no place to go because it’s displaced.
So, that’s one of the great advantages of, well, for a retrofit situation, and it’s a huge savings, as far as the cost of construction in coming up with lots of tapered installation, which is very expensive and labor consuming, as well, to install.
Paul:So, the insulation here, the EPS board, is that tapered or is that also flat?
Russell:Well, let’s distinguish, there’s extruded polystyrene, and there’s expanded polystyrene, and extruded polystyrene is what we’re talking about. It’s a closed cell, it’s more dense, and it has a much higher compressive strength, typically, than expanded polystyrene. So, extruded polystyrene, the pink stuff or the blue stuff, is impervious to moisture. It can be exposed to moisture indefinitely, and it doesn’t affect it whatsoever.
Whereas expanded polystyrene, as we know it, typically… Amoco sells these little plastic beads, with an air bubble inside, and they sell them to everyone. And when they’re suspended in a blast furnace, the little bubbles expand and make a little bead, the beads are compressed into a big block and are cut into all sorts of different shapes with a hot wire in the shaping room, and opened cell. So, the expanded polystyrene is an open cell material, which is derivative, typically, of Amoco’s small plastic bead, with an air bubble that is super-heated, the air bubbles expand inside the little plastic bead, that’s what’s called, “bead board.” The beads are compressed into a block, and they’re cut with a hot wire at varying compressive strengths and so forth. But expanded polystyrene, or EPS, is not impervious to moisture and it will eventually absorb moisture, and collect and retain moisture. Whereas, the extruded polystyrene, the closed cells, is not. So, that’s the difference in material.
Paul:So as far as the drainage goes, just so I understand this, are you saying everything’s flat then?
Russell:Well it certainly can be. And more times than not, in inverted system, the roof deck is either very low slope or is dead level flat. So, either way, when you have the membrane on the deck, insulation on top of the membrane, and then ballast to hold it down in place, the water is literally displaced. It perks down through the joints, in the pavers, or in the stone, perks down through the insulation joints, but it has no place to go other than be directed, or squeezed down, to the drains, if you will. And to help facilitate this, the insulation boards have a small groove cut out along one edge, typically. Such as Dow RN Board, which has been the standard for that type of thing. So, at any given time, you may have just a moisture…a film of moisture on the membrane, but the membrane is never exposed to the daylight or directly to the weather, so it’s literally displaced to the drains. And it’s a very effective way of draining a building, a roof that has little or no slope. It’s probably the most effective way.
Paul:Interesting. Are there advantages related to the ease of construction and construction cost with this kind of system?
Russell:Very much so. For instance, in a new construction situation, I’ve been involved on a number of high-rise, high profile projects, where we literally cut the cost of the new roof in half. And one of the great things is, when you have the roof decks, it’s concrete, it’s made its 28 days, or it’s cured out, you can get dried in in a hurry. You put the membrane directly on the deck, and you put some temporary protection on it, but you’re dried in, immediately. Whereas in a typical new construction project with insulation beneath the membrane, it gets damaged, it has to be fixed during construction, it has to be protected very carefully.
It’s much easier to protect a membrane that’s directly on the deck and then, you know, once any staging or construction traffic is done, you inspect it, anything that needs to be fixed, you fix it, and then you put the final layer of insulation and ballast on it, and it’s a done deal. In a replacement scenario, the same is true. Where whatever you’re removing, you’re tearing off, you may be tearing off multiple layers of materials, or maybe a lightweight insulating fill, or tapered insulation, or wet insulation, etc. But you tear it off, dry it out, and get your new roof membrane back down and get dried in very quickly.
And, again, the construction cost, just with the materials, is significantly less. And your tie-ins, when you’re removing and replacing… Of course, when you’re tearing off an existing roof, you can only tear off a section at a time, and whatever you tear off that day you have to put that back, watertight the same evening before you leave, and you have to tie it into the old roof. And that’s problematic, transferring moisture from the old roof to the new roof, if it’s conventional. So, there are many advantages to ease construction and construction cost, both in a new construction situation and in a roof replacement situation.
Paul:So how does it perform long-term and what kind of maintenance do you need to do, those sorts of things?
Russell:Well, all roofs need to be maintained, and the best maintenance is a routine, documented inspection. It’s also typically required for all manufacturers, really. But the long-term performance aspects are great because, again, the membrane is completely protected from UV, from foot traffic, from equipment, etc. It never sees the light of day, so as long as you’re keeping the drains clean, and, of course, they’re exposed, and as long as you’re doing inspections of the ballast, to make sure nothing’s shifted or moved, etc., there’s virtually very little maintenance, whatsoever, because the membrane is protected, thus the protected roofing membrane assembly. So, there’re great advantages, as far as the long-term performance and with minimal maintenance requirements.
Paul:I know everybody’s really into warranties. What kind of warranties are available with these types of systems?
Russell:Well, it really varies from manufacturer to manufacturer. I’ve gotten 20-year warranties on PRMA roofs, typically nothing longer than that. Some manufacturers, because it’s not their mainstay, they will warrant them for 10 years, or 12 years, or maybe 15 years. But one of the bugaboos in the warranty requirement is that if a manufacturer, or anyone for that matter, needs to go chase a leak someplace, then somebody has to pay for removing the overburden, for removing the ballast, which is laborious. And so, the cost of taking the ballast off, storing it temporarily, finding leak, fixing same, putting ballast back, depending on where the culpability lies, there can be a squabble between who pays for it. So, the manufacturer shies away from that particular aspect, and, sometimes, limits their warranty.
That said, I’ve never seen an inverted roof perform less than the time that I’ve been in business, which is going on over 30 years. We’ve never had… To my knowledge, they’re all still working, and for that reason, because they’re protected. And so, the paper warranty is not, perhaps, as long, in some cases, but the performance outlasts most any warranty these days. So, given that and the variety of different types of membranes, I’ve used both asphalt and coal tar pitch, built up membranes. I’ve used hot, rubberized asphalt monolithic membranes, and other types of fluid-applied membranes. A two-ply, torched down, smooth surface modified bitumen makes a great armor membrane. And many, many of those roofs that we’ve done in the early 90s, late 80s, early 90s, they’re still performing, they’re still working because those bituminous products are protected.
Paul:Interesting, and as I’m thinking about this, one of the things that we see a lot these days, on buildings, is where they try to make the roof into a functioning surface or a usable area for the building occupants. Particularly, you get into these luxury apartment, hotel, condos, where they want people… They wanna be able to use the roof because obviously there’s a lot of sun up there, and you’ve got views and whatnot. And it seems like this type of application, I know you mentioned it’s not only for roofing, but for waterproofing, and actually when you get onto the roof, I guess I would say it’s a hybrid of the two. It’s gotta serve as a roof, do all the form and function that a roof would provide, and protection, but then people are walking around on it. And it seems to me that in this situation, the ballast, I guess, would be pavers or concrete tiles, whatever. So, do you see that type of application with these systems?
Russell:All the time. In fact, the protected membrane assembly is ideal for high rise construction where you have planters or built-in seating, or lighting, promenade areas, or wherever you have pavers in a roof situation. So, let us remember, there’s a fine line of distinction between the definition of a roof covering system and an insulated waterproofing system. And the roofing industry and the waterproofing industry make this distinction. If you have the exact same membrane, the same roof deck, the same insulation, so far, it’s a roof. If you put a stone ballast over the filter cloth on the insulation, it’s a roof covering system. Whereas, if you put the filter cloth down, and then you put a protection board or pedestals, and you put pavers down, it’s a waterproofing system. And so, there’s a difference in semantics, but one of the greatest advantages in the scenario that you’re describing are flashing heights because particularly in high-rise construction…
I was involved in a new construction project in Chevy Chase, Bethesda area, when… These were premier condominiums, high-rise buildings, and we saved well over a million dollars right out of the box by converting their original design, before it was built, to this configuration. So, as we know, as we go up, floor-to-floor, every few inches we can save from floor-to-floor, gives us an opportunity to…they add-up. We can add another floor, we can do different things.
So, flashing heights, which are traditionally 8 inches along your perimeters and penetrations… Well, if you’re starting a flashing height in a configuration that’s conventional, you already have four or five inches of insulation in the membrane on top of it. So, that reduces your effective flashing height at thresholds and penetrations, and walls, etc. Whereas inverted system, you’re starting right down at the concrete deck. So, if your threshold, stepping out of the slider, can be reduced, you can have a taller door, or you can have a lower ceiling, etc. So, it opens up many, many advantages with flashing height, plus, the flashings are also, architecturally, concealed very easily, in that scenario, regardless of the wall system, whether it’s masonry, or precast, or EIFS.
So, what it does is it gives us the opportunity to also conceal and protect the base flashing membrane. And so, a typical scenario is, from the deck up, concrete deck, membrane, insulation and pavers, and the membrane flashing, by the time you’re at that height, you’re already five inches up to the wearing surface, to the pavers. And your membrane base flashing is tucked in behind it, along the edges, and it’s neatened up with a metal cap flashing along the perimeters, and it’s a done deal. You never see a roof membrane, you never see membrane flashings. And so, architecturally, it’s a dream. And the same way with your drainage elements, with your scuppers, whatever, your roof drains, they’re all concealed, you don’t see them. And so, architecturally there are advantages there. And the drainage elements are also protected and remain functional for many of the same reasons. They’re concealed, they’re doing their job, debris stays out of them, etc.
Paul:It sounds like a nice clean design.
Russell:It’s a very clean design. And it is the most used design, that I’m aware of, in that type of scenario.
Paul:And how does this type of system work if you have, what I would call, a busy rooftop, a lot of equipment, pipes, draining? I think of hospitals, or industrial buildings, things like that. A lot of complication, I guess, would be what I would call… How does it work in those scenarios?
Russell:Well, here again, for the same reasons, or similar reasons we were just discussing, typically, HVAC equipment, mechanical equipment, is going to be mounted on a curb. So, for curb-mounted fans or curb-mounted equipment, base flashings on the curbs are also mostly concealed. So, by the time you get to the top of it, your ballast is cut out or distributed around these things, so again, they’re protected. And then with the metal counter flashing that tucks down behind your ballast and your filter cloth, again, the flashings around this equipment are, for the most part, protected. So, if you have your metal counter flashing tucked down behind your ballast, the membrane flashing beneath it, which is… In any roof covering system with a lot of equipment on it, those flashings tend to be the most problematic things because of all the penetrations associated.
When those flashings, the primary membrane flashing is protected, and its counter flashed with the proper metal counter flashing that’s tucked down into the ballast, or beyond it, again, the flashing never sees the light of day. So, they’re easy to inspect, they’re easy to maintain, etc. Where you have single pipe penetrations, and so forth, the pipes may have to be extended a little bit more, say more, maybe an inch or two, at best. Typically, though, it’s ideal for that scenario. If you’re carrying piping, or gas lines, or conduits, across the roof, then putting them on top of intermittent pavers, or blocks, instead of on top of the roof membrane in a conventional configuration, there again, these things that are sleeping on the surface are sleeping on the surface of the ballast, rather than the membrane, with the insulation underneath it.
Paul:We’re seeing a lot, in buildings that we’re building these days, we’re seeing a lot of specs for TPO and EPDM roofs, and I’m guessing it’s because it’s probably budget friendly for probably a good way to say that. How does a PRMA roof compare, cost-wise, to some of the other options that are out there?
Russell:By and large, a TPO, or EPDM, PVCs, these types of single ply membranes are rarely, if ever, used in an inverted system. They’re almost always used in a conventional configuration. So, while the actual cost of the roof membrane is less, the cost of the insulation and the labor, particularly, to install all that in a conventional configuration, still comes up higher than a better, thicker, more resilient, protected membrane and the extruded polystyrene on top of it, and the ballast. So, in that scenario, if you have a wide-open warehouse or a lot of roof production type of roof to cover, then TPO or single ply membrane is still going to be more cost-effective than designing a building to take an inverted system.
So TPOs and EPDM… The EPDM market has waned dramatically in the last ten years, with the onset of TPOs and PVCs. But you’ll still find many loose-laid, ballasted, single ply membranes in a conventional configuration. In other words, a metal roof deck, insulation, EPDM, a filter cloth, and then stone ballast on top of that, in a conventional ballasted configuration. And in many of those cases, Paul, those buildings are not… Those are one or two story buildings. You know, schools, shopping centers, R&D. Those buildings are not built to necessarily handle an armor roof, but they were also built to handle that 10 to 12 pounds per square foot of ballast done in a conventional configuration, so they are convertible, case by case. And it’s definitely worth something looking into, depending on the use of the building and the economy.
Paul:So, then an inverted roof can go onto a metal roof deck?
Russell:It can, but, here again, buildings that were built up through, I’m gonna say the early 2000s, many of them were built, specifically, with an inexpensive roof covering system in mind, and the least expensive thing going there for a good 15, 20 years, was a loose-laid ballasted single ply membrane. And, typically, before TPOs and PVCs caught on in a big way, it was EPDM, synthetic rubber. And, of course, EPDM has a great elongation capacity, but as far as a long-term performance, in my opinion, EPDM doesn’t hold a candle to the more modern, single ply membranes that are reinforced, PVCs and TPOs. And, of course, most EPDMs were black, so if they were exposed, they were a huge heat gain. Whereas most TPOs, etc., we see these days are white, so they’re reflective. So, I don’t think the EPDM manufacturers would like me to say that they’re obsolete, but they’ll tell you themselves, their market share has changed dramatically, and for good reason.
But the net result of that, coming back to many of these buildings were designed to hold a 10-plus pound load per square foot on the roof, for the ballast, so many of them are converted. And I’ve converted office buildings, and condominiums, etc., with metal roof decks, where… And this is in roof replacement scenarios, where those metal decks were still flat, or they didn’t have enough slope to drain properly. And instead of investing a fortune in labor and materials of tapered insulation systems, and getting them down right, and fastened or secured to the deck, etc., we put a fire-rated gypsum board, fastened down to the metal deck, maybe reinforced it, and put our new roof membrane on that, and extruded polystyrene over top of that. So, we didn’t have to make that huge investment in labor, etc. We created a new substrate so that a membrane could be fully adhered.
And so, one of the key design issues, again, is in a protected assembly, in an inverted assembly, that membrane really needs to be fully adhered to the substrate. And, of course, again, one of the beauties is if you ever pop a leak someplace, it’s easy to find, because water doesn’t travel between a fully adhered membrane and the roof deck, particularly if it’s a bituminous product, a built-up membrane or a modified-bitumen membrane, or a monolithic hot melt, that sort of thing.
Paul:So, what are the limitations of when, where, an inverted roof and waterproofing system can be installed.
Russell:Well, here again, just to recap, remember when contemplating either new construction or a roof replacement, be it on a roof, or a parking deck, on a plaza deck, etc., the things to keep in mind is that one, the structure needs to be able to withstand the weight of the ballast. And, typically, in our higher-end areas, that’s gonna be concrete pavers, and there are many types of lightweight pavers. So, that’s the first and foremost consideration is your structural design and what the deck, be it a roof deck or plaza deck, what it’s designed to take in the first place. And, typically, these are concrete.
Another limitation is, the perimeter of the roof or the plaza deck must be contained, typically with a parapet, because you have stone or ballast and insulation on top of the membrane. So, that assembly has to be protected vertically from the side, as well. So, typically it’s gonna be installed on a construction that has a built-up perimeter. It doesn’t have to be a parapet, but it has to be a raised edge that is at least a few inches above the edge of the roof, and that’s a big consideration in high wind areas. So, if it’s a new construction, it’s built in. If it’s existing construction, we’ve done retrofits where we actually added height to the perimeter to contain the system.
So, those are the two primary limitations, is having a substrate that’s monolithic or being able to create a monolithic substrate, if it’s not already. So, concrete is ideal, or if it’s some other material, having a smooth, resilient substrate to place the membrane on. So, those are the two limitations.
Paul:Yeah, this’s really been an interesting, insightful, topic, Russell, and I thank, you, very much for coming on as a guest today.
Russell:My pleasure, Paul.
Paul:And I know, at GCI Consultants, we’re really excited to have you on board our team, bringing your wisdom and knowledge, and very excited about working on projects going forward and applying as such. So, again, you know, welcome aboard.
Russell:Oh, thanks for that. GCI has a lot going for it, so I’m really happy to help fill in this dimension across the board, Waterproofing and Moisture Protection Building Envelope. So, it starts with the roof and goes down, right?
Paul:That’s right. So, thank you everyone for listening to the Everything Building Envelope Podcast. I wanna remind the audience that we do have the Everything Building Envelope Newsletter, and if you would like to subscribe to that, please text the word, “buildingenvelope,” all one word, “buildingenvelope,” to 22828. Again, text, “buildingenvelope,” to 22828. Again, thanks everyone for listening and, till next time, this is, Paul Beers, saying, “So long.”