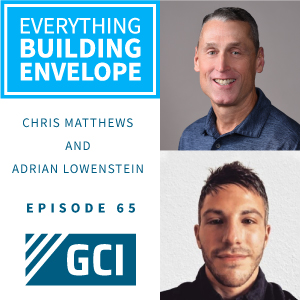
About The Everything Building Envelope Podcast: Everything Building Envelope℠ is a dedicated podcast and video forum for understanding the building envelope. Our podcast series discusses current trends and issues that contractors, developers and building owners have to deal with related to pre and post construction. Our series touches on various topics related to water infiltration, litigation and construction methods related to the building envelope.
https://www.everythingbuildingenvelope.com
*** Subscribe to the show and leave us a Review on ITunes!
Chris: Welcome, everyone to our “Everything Building Envelope” podcast. I’m Chris Matthews, president and principal for GCI Consultants, and I’m your host today. I’m really excited to have as our guest, Adrian Lowenstein, who is the national business development manager for Skyline Windows, based in the Bronx, New York. We’ve got some interesting topics to cover today, which include energy codes, current requirements, sustainability trends in the industry, and some of the differences we see in the northeast where Skyline is based versus the southeast where GCI does a lot of our work. We’ll discuss those and some of the different technology trends we see in the building envelope today. So, Adrian, welcome. Let’s start off by having you tell our audience a little bit about yourself, and then we can jump right into our subject matter.
Adrian: Sure. Thanks, Chris. So hey, my name is Adrian. I’m a licensed professional engineer here based out of New York City. My background is on the facade consulting side. I have a lot of experience in the high-rise curtain wall and window wall sector. And now, I’ve found myself coming over to the dark side on the manufacturing side with an aluminum manufacturer, aluminum fenestration manufacturer named Skyline Windows. We’ve recently celebrated 100 years in business. So, we’re very excited to be sharing and discussing some of the current challenges we’re facing with the new energy codes, and how we’re going to be addressing some of our new builds when it comes to new construction and existing buildings. So, I’m very interested to hear how that’s affected your business and the market in the southeast, and maybe how we might end up meeting somewhere in the middle.
Chris: Sure. Great. So, we were talking a little bit before we started recording and talked a little bit about the work that you do, the energy code, things that you’re seeing currently in the market. So why don’t you just talk to us a little bit about how you see the new energy code affecting design decisions. What you guys are experiencing from the window manufacturer in the work?
Adrian: Sure. So, I think recently sustainability and energy codes have gained a lot of attention. I think in the past, we always were striving to build high performance, but there were no real, true ramifications. And now that we have more outcome-based energy codes, where the energy usage intensity of existing buildings is being measured, meaning we’re sitting here and reading energy bills, and applying thresholds as to how buildings are supposed to perform, all of a sudden topics are being taken much more seriously. And we’re reassessing how we’re building our buildings, how we’re looking at the building as a whole in terms of how the enclosure and how the mechanical systems are interplaying with one another. And it’s definitely gotten the attention now that it deserves. We’re seeing questions like, how much glazed area do we want to have on our facade? Should we look at technologies like triple-glazed instead of double glazing? It definitely feels like there’s a paradigm shift going on in the industry. And it’s sparking a lot of interesting conversations.
Chris: And we’re seeing that in Florida as well. Probably over the last three to four years, I would say is when we’ve really been seeing that shift, as you said, that paradigm shift more toward a focus on the energy performance. As we were talking about before the podcast, we’ve got the additional layer in Florida and the other hurricane-prone regions of the impact on glazing requirements but five, six years ago, everything in the southern part of Florida was laminated glass, 9/16-inch laminated glass, no insulating values at all. But as the energy codes came into play, now we’ve got…not triple glazing yet in Florida but now we’re seeing insulated laminated glass requirements to meet the energy requirement as well. So…and of course, in Florida, our big thing is keeping the cool in where in the northeast where you are, it’s usually more a concern about keeping the cold out. So…
Adrian: Of course, I think that main difference is that, you know, we’re a heating-dominated climate versus a cooling-dominated climate like you said and…but I think there’s this misconception in the industry that U-value of the system isn’t as important in Florida. But if you think about it in the summer, all of that solar gain that you’re getting, it’s going to be very hard to maintain a comfortable interior environment. And it’s just going to require a tremendous amount of cooling load on the building. So I think that’s more of the challenge that you’ve faced down there.
Chris: Sure. And that’s…as you were saying, that gets into more than just the glazing system itself, but how much glazing is there going to be on the exterior building? How does that affect the HVAC system and design? You know, I can remember over the years, the different projects we’ve been involved with, where, you know, these people sitting in these offices and, you know, they just can’t get comfortable because of the type of glass and the limited insulating value. And no matter what they’ve got the AC set on, people who are near the windows or curtain wall, or whatever it may be in an office building are just…you know, it’s just uncomfortable because of there was no concern at that time about, you know, the U-value, the energy performance of these systems.
Adrian: So interestingly in California with…they had their Title 24, where there was a mandate. I believe it was in the early 2000s, maybe in the late ’90s, where all of a sudden, you couldn’t put a new piece of glass in that was monolithic. Every new piece of glass has to be an insulated unit. I guess when did you see that shift in Florida? And do you still see monolithic units going in and things like non-thermally broken framing?
Chris: Yes. In fact, in South Florida, still, primarily, most of the stuff is not thermally broken, most of the systems are not thermally broken. They’re just starting to look at that as one of the ways to meet the energy requirements. And even the glass itself, I don’t remember exactly when, but I’m going to say it’s been only in the last four or five years that it’s gone to the insulating glass in South Florida. So it’s definitely behind…we’re definitely behind some of the other areas as far as the energy constraints. And some of that was because the hurricane wind-borne debris impact codes came into play in the mid to late ’90s. And there was so little product availability that the main thing was just to get manufacturers who had tested products that could meet the impact requirements. And then, it’s only been recently that, you know, they’ve added that additional layer now to start to address some of the energy stuff.
Adrian: So let me ask you, Chris, with some of the aggressive structural and design pressure requirements on these fenestration systems here in…especially in Canada, and in the colder climate regions, we’ve seen some nonmetal manufacturers come out like UPVC, and perhaps fiberglass, just as a way to meet the thermal requirements and to perform at these aggressive energy targets. So one of the constraints that we’ve seen, especially in mid to highrise applications is that they don’t perform in a similar fashion or similarly to that of aluminum. And you don’t get that same strength to weight ratio and some of those structural characteristics that you would look for in aluminum. So have you seen any of those materials, I guess, explored in the market? Or have you, you know, experimented with any of that in commercial applications?
Chris: [crosstalk 00:08:24]. Yeah. I’ve seen it. Well, not so much commercial applications, because I think of the structural issues that you were mentioning. But I have seen in some…maybe say like kind of mid-rise type projects, where there are some manufacturers now, some…maybe some kind of local Florida manufacturers that are doing some stuff with fiberglass, PVC, those kinds of products, mostly I’ve seen in, like operable windows for…and as I said, mid-rise, apartments, those kinds of things. We’re seeing a lot more of that where they can meet the structural and impact requirements, because they’re relatively low loads, as opposed to a high-rise building but then get the energy efficiency. So we’re seeing some of that, but in all of the commercial, you know, high-rise, any of those types of projects, it’s still all-aluminum stuff here. Are you guys seeing that up in the northeast as far as, is it still predominantly aluminum when you’re talking, you know, high-rise, more substantial systems or there’s some other products as well coming into play there?
Adrian: Well, the limiting factor at the moment with aluminum systems is the thermal performance. Obviously, the long-term durability and structural performance is there, and it’s proven out. In all I’d say 99%…particularly, it’s all-aluminum and curtain wall and window wall. In some punched window applications, we’re starting to see some nonmetal applications. You know, for decades now, just because of the energy requirements, we’ve been putting in thermally broken systems. Every new project has at least a double insulated glass package with one Low-E coating. Now we’re seeing ultra-warm edge spacers. I mean, the technology is really ramping up just to meet the energy requirement. And every project we look at now, essentially, from the design team, they’re looking at a cost performance, you know, analysis on what a double versus triple insulated unit will look like. Can we even achieve our performance requirements with an aluminum system? So we are reaching we’re close to reaching a threshold with aluminum at the moment just to meet the new U-factor requirements. And that’s why we have to look at upgrading our glass technology and glass package if they want to design a highly glazed facade per coat.
Chris: Sure. And what are some of the trends you’re seeing? We’ve talked some about the aluminum and the structural components of these glazing systems. But what are you seeing as far as trends with the glass product and coatings? What are you seeing in your area as far as those?
Adrian: So, something that’s been introduced recently is, I’ve seen a soft Low-E coating now put on the interior surface. So on the number four surface of the IGU. So, having that second coating on the glass is giving better solar heat gain as well as U-value performance. I think that would be potentially a concern in the southeast environment. Just from some consultants I’ve spoken to, there might be risk of condensation, just if you’re in a residential application and you have an interior environment that’s a little more humid, you might run a risk of having that interior surface of the glass be, I guess, running close to the dew point. So again, you would run risk of condensation. So, I think in the past, we’ve seen hard coats on the interior surface and design teams would stray away from that. But now, especially with double insulated units, we’re seeing a second coating being introduced. And then when we’re looking at triple it could be one, two, or three coatings. I mean, it sounds…it sounds almost out of this world that we’re having this conversation, and I can’t even imagine a monolithic glass unit going into a system here today. And it’s crazy that that’s still going on in Florida. And the truth is, it’s just…it shows how much the climate has influence on the performance requirements of the building.
Chris: And I think now we’re to the point where there probably are no new monolithic projects. There were some prescriptive ways around the energy requirements in the beginning, where they could do some things and maybe comply with a monolithic situation. But I don’t…I don’t think they can anymore. I haven’t seen any in the last probably three years, something like that. But it kind of, like you said, it just kind of blows me away that you guys are, in your area, looking at triple glazing and actually three different layers of Low-E if you’ve got a triple glazing situation.
Adrian: I mean, yeah. It’s a…and what I talked about; I think we’re a step back from where Canada is at the moment. I think Toronto and Vancouver kind of led the way here with going for the overarching goal of being carbon net-neutral. They’re looking to hit it by 2030. I know a bunch of the lower states are looking at 2050, particularly cities like New York, DC, Boston. So, we’re following a lot of trends, especially facade trends that we’ve seen in Canada. And I just wonder how quickly the rest of the country is going to be…to adapt it. But I mean, we’re looking at double-skin curtain walls up in Canada. Triple glazing becoming almost the norm, and a strong, strong focus on the facade first. Getting the facade right so that you don’t have such a heavy requirement on your mechanical systems. And, you know, if you’re looking at the design of a new construction building, the design team can have a heavy influence on those decisions. The challenge becomes when you’re looking at retrofitting an existing building. And I think you look at individual components like the lighting or the mechanical system, or the roof and you just want to optimize. But the challenge is, all these systems work in unison and if you don’t have the right facade in place, it doesn’t matter how much you optimize the mechanical system, you’re just going to be bleeding energy out of the building.
Chris: Right. And you were talking to me some about there are new requirements in New York and some of the other big cities in the northeast, actually looking at the existing buildings and the energy performance of those as well, right?
Adrian: Sure. So, we have something that was enacted in 2019, called Local Law 97, or the Climate Mobilization Act. And it essentially…it puts in a carbon emissions limit on buildings over 25,000 square feet. So they basically, depending on the type of occupancy, whether it’s a commercial office, residential building, hospitality, they’ll say, “This is your carbon emission limit,” or they call it in metric tons per square feet, “So this is your energy usage intensity. And anything that you are over that threshold, we’re going to elicit a fine, or in other words, a carbon tax on that building. So specifically, it’s $268 per metric ton, you are over the threshold.” So it’s aI was describing earlier, it’s become a paradigm shift because we’re looking at performance now more so than conformance. It’s not just, “Hey, you know, did you hit these LEED requirements?” or, “Did you build per the…per the energy codes?” We’re looking at how the building is performing. So, we’re looking at the Con Edison bills or your utility bills, and we’re saying, “Okay. What’s the energy usage intensity? And are you over the threshold? And if you are, then we’re going to fine you.” So it’s stringent. It’s a big deal. But it’s being adopted in other cities. And I think it’s really redirecting the attention to existing buildings. And all of those post-war buildings that were lapped up, you know, in the ’50s, ’60s, ’70s, now, there’s real ramification if they don’t comply. And they’ve given building owners a little bit of time. This law doesn’t go into effect until 2024. But it’s opening up the conversation to how to properly and effectively address these buildings.
Chris: And that’s something that we’ve not seen in Florida yet. But I’m sure as you said, it’s going to spread throughout the country. And it only makes sense if we’re concerned about energy performance, efficiency, consumption, all those things. You know, your existing building stock is…you know, there’s hundreds of years, or over 100 years worth of buildings versus what we build new each year. It’s just so many more out there affecting energy consumption. So, it makes sense that eventually, this is where it’s going to go. Have you been involved in actually any projects yet, where they’re looking at replacing exterior fenestration to try to come into compliance when this comes into play in a few years?
Adrian: That’s been the majority of our projects at the moment. When we sit here and look at doing either a window replacement or some type of curtain wall retrofit job, or they’re looking to over clad or maybe install some type of new rain screen, part of that design decision is going to be, “Okay. Are you going to conform with Local Law 97? And if not, how do we need to address or change this design?” I mean, everybody thinks about…we were talking earlier about all the new condo buildings that are being built in Florida. Now, the truth is, the minute that building gets their TCO, that becomes an existing building. So all the rows and rows of new high-rise buildings we see in South Florida along the water, those are all existing buildings. And if Florida has listed some type of local law where they put a threshold on how the building has to perform, you know, maybe there’s going to be ramification to, again, building with those monolithic glass units or installing the non-thermally broken frames. So yeah. I mean, that’s…all these projects in terms of retrofit and repositioning, that’s been an added component. Sure, we say, “Okay. If you put in all new windows, you’ll reduce your energy bills by this.” But there’s that added component, now we eliminate that fine component where you weren’t in compliance with this local law.
Chris: And very interesting, very interesting stuff. And with all of the focus on building performance now that there wasn’t 20, 25 years ago, it’s interesting to see that it’s going to evolve into how it affects all these existing buildings. Because we’re building them so much better now, right? I mean, the things…the new things being built now are so much better performing than what they were, as you said, in the ’50s, ’60s, ’70s. They weren’t even thinking about this stuff then. So…
Adrian: Yeah. I mean, I think the interesting or nice thing is that we don’t have to reinvent the wheel here. We have the technologies. And we…it’s still the same types of systems being specced, and designed, and installed now. It’s just now there’s a, I guess, a reason to purchase. There’s more of a reason to consider them, I’d say. And it feels like we’re headed in the right direction. I mean, in 10 years from right now, I don’t know what we’re going to look back at and say, “Why were we doing that?” but I think we’re continuously progressing in terms of envelope and just building performance as a whole. I’m curious, have you had any clients or requests on projects to do any type of lifecycle assessment or energy modeling, or energy performance assessment?
Chris: Yes. That comes into play now a lot more, again, a lot more than it did 10 years ago. But people are looking at the whole building performance now here, and I’m sure they are there as well. And doing those analysis from the beginning and looking at how all those systems work together. Yes. So, we’re seeing that here as well.
Adrian: Sure. I mean, I know it’s very popular, you go on the water and you want that all glass. I saw you guys did a number of high-rise condominiums there, whether it’s window wall with terraces and balconies, or if it’s a curtain wall. Do you think we’re going to head in a direction where we can’t have facades that are so, you know, 70% glazed systems, and we’re going to look at more opaque areas? Or do you think people are just going to start spending and they’re just going to start specifying higher-performing systems just to meet the energy codes?
Chris: Well, I think…I mean, and that’s an interesting question. And it’s kind of a dichotomy in that previously…the technology for the impact-resistant stuff, just like energy performance, has been getting better, and better, and better. The manufacturers can make bigger pieces of insulated laminated glass. There’s much more knowledge now about what’s needed to pass the impact…the missile impact testing, and cyclic wind load testing requirements. So, from the standpoint of somebody who’s buying a high-end unit on the beach, these people want the biggest expanse of glass, the biggest openings, the most beautiful view they can have. But then, on the other side of that, there’s all these energy performance issues as well. So, you kind of have a push in both directions here in that the manufacturing capabilities are better from the building owner, unit owner standpoint. They want the most big, beautiful view they can have. And the architects want to give them that. But then also, there’s these limits on how much glass can you have and still meet the energy requirements. So we kind of have a push and pull going on here right now. And I would think too, you know, kind of the same thing, if somebody is buying…building something, you know, a ski lodge on the…on the slopes of some beautiful mountain somewhere, same thing, you know, you want these big, beautiful expanses. But then, how’s that affecting your energy performance?
Adrian: Everything’s a push and pull at the moment. I mean, we get calls that we wanted to do a curtain wall building, but we’re considering a passivhaus project. And can we make that work? We don’t have the budget for curtain wall. Maybe can we make it work with window wall? Well, do we need to go triple glazing? And the whole, it’s just the back and forth of a trade-off at the moment and every project seems to come down to compromise. I’m curious if you’ve had an experience with any of the dynamic glass suppliers. I know you previously had View Glass, a podcast episode. I believe it might have been with Paul. We’ve done a bunch of projects with them up here in New York. I’m curious about the implications of a system like that in Florida, especially where solar radiant heat is a much bigger concern. So, if you’ve seen any traction, and if you think there’s a future for that type of technology.
Chris: I think personally, I think there’s a future but as far as…we’ve been interested in that and definitely, as you said, I had them as a podcast guest and I’ve seen some presentations and things about that. But so far, I have not seen yet a lot of traction in big projects including that. It seems to me that it’s going to happen. But we haven’t seen a lot yet. And I’m interested. So, you guys have actually had some projects that included the dynamic glazing?
Adrian: We’ve done maybe three or four high-rise buildings. No new construction, all retrofit buildings. But yes, either curtain wall retrofit, or very large, large-scale operable that…I mean, I’m talking 10 feet wide by 5 feet tall with dynamic glass. A lot of it was with the same building owner and developer up here. But I think the technology is intriguing. And I asked about it just because again, of the solar requirements and demands in Florida, I would think it would make for an appealing product even more so down there. But I see it as maybe being, you know, innovative, trendy play, and people have bought into it. And I think it’s awesome when you see it in person, it’s quite neat. I call it like a “Shark Tank” product where the type of thing that you have to see in person, and then you’re sold. But I’m seeing more and more of it. I mean, I’m not saying it’s on 25% of projects right now. But they’ve done some substantial projects up here in the northeast. And I know you guys had them on as a guest, so I’m just wondering. That’s one of the glazing technologies I wanted to talk about. I think something we can see in the future is a lot more of, A, dynamic glass. And then, the other one is vacuum insulated glass. I’m hearing a lot about it right now. A lot of glass manufacturers are, I guess, going pedal to the metal trying to be one of the first to market. But I think that could be a driver in helping us still design and build highly glazed facades while still meeting the energy code requirements.
Chris: Right, right. Yeah. And our thoughts were the same as yours as far as it seems that with the dynamic glazing, it’s a perfect fit for Florida, and any kind of a hot, sunny area. But you know, like we were talking about with the push and pull, it’s a…it’s a money thing as well, that right now, if they can meet their energy requirements in some other way, and our glazing systems are so expensive because of the impact requirements on them, I think a lot of people just haven’t seen the cost-benefit there to go with the…with the dynamic stuff. But, you know, like everything else, if some developer start using it, as you said, it’s really neat. And then, it’s going to be a thing of…the next developer is going to say, “Well, you know, I can’t compete if I don’t have it.” So if, you know [crosstalk 00:28:02]…
Adrian: Of course. I mean, someone recently told me that projects sell projects. So I think, you know, they got their first big win here. And I think that, you know, built up the momentum. And once you have a portfolio of projects to display, all of a sudden…you know, there’s some consultants and design teams that are reluctant to specify or try somebody…try somebody out unless they have a track record or a history of [crosstalk 00:28:27] performance. I think that’s the component. But I mean, between all of these…considering triple glazing, considering dynamic glazing, something we’re seeing now here in the northeast is bird-friendly glass. I don’t know if that’s something you’ve seen yet. But another local law we have, Local Law 15 here is that every new piece of glass that goes into a building has to be considered bird-friendly, which I’m not a glass expert, I don’t want to speak to the specifics, but in essence, to my understanding, the glass has to have a certain threat on it, so that the birds can see it so that they can limit the amount of incidents they have. At the moment, I think there’s been…I didn’t mean to laugh. It’s not a funny matter. They’ve had a lot of incidents, I guess, all over the country where birds have collided with glass. So that’s…we’re seeing that trend.
So again, I mean, all these discussions, everybody wants the highly glazed facade. Everybody wants views, and the big windows, and the big fixed light. And all these new glass technologies having to be bird-friendly, having to possibly be dynamic, possibly going triple glazing, all of a sudden, your glass cost per square foot becomes pretty astronomical. And it makes it challenging to push for other things in the building. I mean, again, like we spoke about everything is a trade-off. So just for highly glazed facades, as I was saying to me energy codes, I think we’re going to have to see…I don’t want to say a little bit more competitive pricing, I think as these things become more commonplace, possibly the price per square foot of some of these technologies will come down a bit.
Chris: Yeah. Right. And that’s what we saw. It’s very similar to when we saw the impact resistance requirements come into play in Florida. At the time, you know, there was all this almost hysteria about, you know, “We’ll never be able to build another house or building. It’s going to be too expensive. No one can ever afford it.” And of course, yes. There’s lots of research. There’s lots of development. But people learn and people find more efficient ways to do things. People see what’s working and what’s not. And, yeah, sure. It adds cost. But if the requirement is there, you know, the market will figure out a way. And that’s what…
Adrian: Of course, of course.
Chris: …you know, eventually.
Adrian: And that’s what I think some of these energy…I think some of these local jurisdictions, and what, like I said, Toronto, and Vancouver have done. And now we’re seeing it in Seattle, where you have, you know, envelope backstops related to the energy performance requirements. So, I think as we’re seeing more and more adoption like you were saying, everybody’s…it came as a bit of a shock, but everybody’s starting to adapt and figure it out. And that’s sort of what we do in this industry. So, I mean, you have…in the southeast, a whole set of other challenges, as you were saying, with the impact’s requirements. Have you seen a spike in consideration of…new consideration of natural ventilation or maybe more operable windows on buildings, particularly with…I don’t mean to go on a completely different tangent, but with COVID? And I think, people, desiring maybe natural ventilation through operable windows or maybe access to outdoor space, like balconies, or terrace? Have you seen any of those influences coming in on design decisions?
Chris: Well, I read about that kind of thing. But knowing our market and the way it works, I mean, there’s always been a big interest in the outdoor space, the balconies, the patios, those kinds of things. But in Florida, basically, the majority of people use their air conditioning almost all the time. So, you know, we have all the operable windows in our houses, and even the high-rises, you know, there’s operable windows, and of course, sliding glass doors, on all the balconies, those kinds of things. But as far as the natural ventilation thing, like I said, I read about it, but I just don’t think it’s very practical here. Because, you know, it’s just too uncomfortable from a temperature standpoint, the majority of the year in Florida.
Adrian: Yeah, I mean, I think once we get up here in the spring and fall, obviously, you have your windows open, 24/7. And even in commercial applications, it gets so hot on the interior from some of the solar gain, and just all the interior heating loads that sometimes you see it in office buildings, the windows are open in the middle of winter, which I guess is normal to you because in the middle of winter down there, it’s 50 degrees and comfortable. Interesting to hear where it’s going. And I’m glad to hear some of those trends are being picked up over time in Florida. I don’t know how soon we’ll see triple glazing down there, as you were saying, but it sounds like we’re sort of headed in the same direction.
Chris: Could be someday. Yeah. Well, thank you for joining me today, Adrian. You’ve been a great guest. Lots of interesting stuff that we talked about. I always enjoy…you know, as you said, we do work all over the country so…but I always enjoy talking to people in different climates, you know, big cities in the northeast. Those kinds of things are interesting because there’s a lot that we can learn from each other, as you and I have kind of been doing on this podcast today. So, I want to thank you again for joining me. Hopefully, this has been as interesting for our listeners as it has been for you and me. If any of our listeners want to reach out to you, why don’t you share your website address and the best way to contact you?
Adrian: Sure, I appreciate that. It’ll be easy to reach out to me personally. My LinkedIn, @adrianlowenstein. You can find us at Skyline Windows at skylinewindows.com. And if anybody wants to email me it’s alowenstein@skylinewindows.com. I thought this was a great conversation too, Chris. And it’s always good to hear a different perspective and something that you’re not used to. So, I really appreciate you having me on and I hope your guests enjoyed it too.
Chris: Great. Well, thank you. We also invite our listeners to take a further look at our GCI Consultant Services on our website at www.gciconsultants.com. And you can reach us at phone number 877-740-9990 to discuss any of your building envelope needs. Thank you, Adrian and thanks to our audience once again. And I look forward to talking with you next time on our “Everything Building Envelope” podcast.