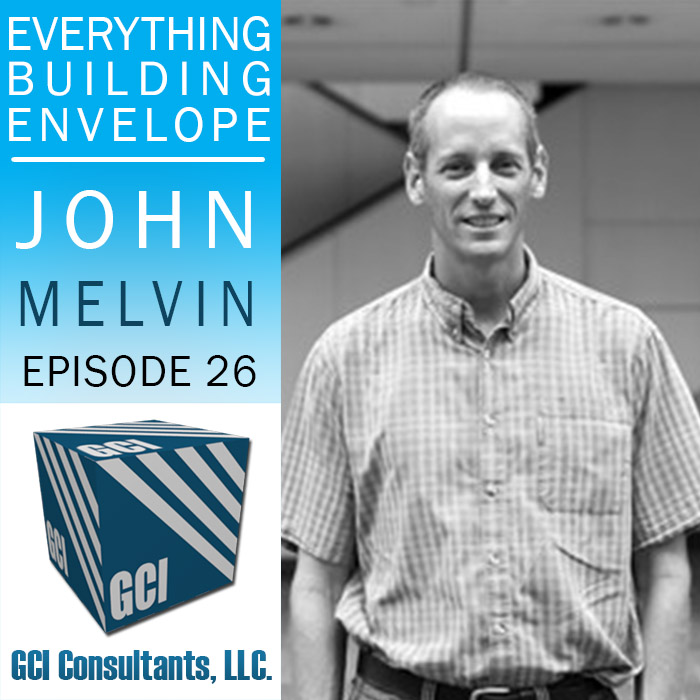
About The Everything Building Envelope Podcast: Everything Building Envelope℠ is a dedicated podcast and video forum for understanding the building envelope. Our podcast series discusses current trends and issues that contractors, developers and building owners have to deal with related to pre and post construction. Our series touches on various topics related to water infiltration, litigation and construction methods related to the building envelope.
https://www.everythingbuildingenvelope.com
*** Subscribe to the show and leave us a Review on ITunes!
Paul: Hello everyone, this is Paul Bears. Welcome to another episode of the “Everything Building Envelope” podcast. We’ve got a really interesting topic today. We’re gonna be talking about building envelopes and also mechanical systems and how they interact. Our guest is a really good friend of mine, John Melvin. Well, welcome John.
John: Hello, Paul. Thank you for having me.
Paul: Yeah, really excited about this. So, John, we’ve been going to an entrepreneurial coaching program together called Strategic Coach for like five or six years, is it?
John: That’s correct. Yes, we met in Santa Monica and really enjoyed our conversations.
Paul: Yeah. I think we can both say the program has had a really big influence on our careers and how we’re doing now. And then also, you know, we’ve had really a great group. There’s 4 or 5 of us that’ve been together the whole time. And it’s really been great to be able to bounce ideas back and forth and whatnot.
John: It sure has.
Paul: So as luck would have it, we’re in related but unrelated fields. You know, I’m the building envelope guy at GCI consultants and you’re a mechanical engineer. In fact, why don’t you tell the audience a little bit about yourself before we get into today’s topic?
John: Sure, Paul. So I’ve been a mechanical engineer for 25 years now and I have had my business, JM Engineering, for the last 15 years. And we are a firm of 10 full-time people and we have a number of virtual people working for us. We work in the mechanical, structural, and electrical consulting areas of building construction. We specialize in high-end residential projects, houses typically minimum of \$10 million a piece. And then also we do an awful lot of healthcare and educational work. So our markets that we work in are primarily the western United States. We are licensed all over the country. And we see a big variety of projects, both in our northern climate as well as in southern more humid climates.
Paul: Yeah, and I know you said that…well the high-end residential obviously, that’s a challenge in itself because the…you know, you always have high-volume spaces, lots of windows, things like that. And then, of course, the healthcare, that’s probably nothing more difficult from a mechanical standpoint then healthcare projects. They’re so complicated and whatnot. So you’re not doing the superficial stuff, you’re doing the real hard work.
John: Yeah, it is very challenging. You’re exactly right, the healthcare with the surgery suite and pharmacy clean rooms, compounding facilities. Air quality is extremely important. Same with the educational work we’re doing. We put a high emphasis on healthy learning environments for all these schools that we’re working on, making sure that the CO2 levels are not too high in the classrooms which allows the students to have a far greater learning experience.
Paul: Very cool. So, John, we’ve been talking a little bit before we did this and we were thinking it was a good idea to maybe talk about our two respective disciplines: building envelope and mechanical engineering and how they’re really very interrelated. But as we go through projects from design to construction and even operating those buildings after they’ve been built, there’s not really a lot of integration between the two. Do you see things that way as well?
John: Absolutely, Paul. The very first thing we do in a project once we have identified the mechanical systems that we are most likely to use is we go into our process of our engineering calculations to determine the cooling and heating equipment sizes. And that in large part is dictated by the building envelope. And at the time when we are starting our design, we don’t often times have all of the building envelope information that we need. The interior loads, the internal loads are pretty easy to identify with numbers of people and connected equipment. But building envelope and the mechanical systems are very much interrelated. And it becomes very important for us to know how tight the building is and what impact that has on the infiltration. That has a big impact on our ventilation.
Paul: So what’s the importance of integrating the building envelope and mechanical system design form the mechanical side of things?
John: Yeah, that’s a great question. So the building envelope is one of the bigger key components of determining the size and capacity of the heating and cooling equipment for a building. And it becomes very, very important. Small changes in insulation in the overall tightness of the building has a big impact on the chiller sizing, the boiler sizing, and the fan sizing. And one area that I think gets missed an awful lot of the time is an analysis of the building envelope and comparing that with what is required to heat and cool that building. And there’s often times trade-offs as to how much insulation can be used and where is the balance point of having the proper amount of insulation and the right envelope construction to balance the optimal boiler and chiller plant sizing.
Paul: Now can you also have situations where perhaps…and I’m just saying any mechanical engineer, not necessarily you guys but any mechanical engineer, where perhaps the mechanical systems could be…you know, assuming the envelope is gonna be XYZ when in fact it’s ABC and you end up with an over-designed or an under-designed mechanical system?
John: Yes, definitely. We have seen that in the past where we have gone into buildings that have needed retrofitting from the glass being changed as a value engineering process and they went with cheaper glass which then allowed a significant amount of solar gain into the space which then had an impact on the cooling capacity. At which ended up being a pretty big cost change in the end. And that was something that was not evaluated during the value engineering process. So the other issue that can happen is there can be assumptions made on the envelope to the point where the mechanical systems are significantly over-designed, which then the owner is paying for larger equipment than what is needed. And then what also happens is you can have equipment that is cycling on and off much more frequently because it is oversized. And that can have a big impact on the lifetime of the equipment.
Paul: So during design, what should the interaction be between the design of the building envelope and the design of the mechanical systems?
John: From our point of view, Paul, what I think the interaction needs to be is the load calculations need to be developed but then they need to be evaluated with the architect to have the architect look at different insulation and window systems to see if the envelope can be optimized for its given climate and also see if there’s a way that we can make our mechanical equipment smaller and find out if there’s a payoff and if it’s cheaper to put in more insulation in the walls and roof as opposed to putting in larger equipment.
Paul: Now, when you say cheaper that’s interesting because we see a lot of different attitudes with cheaper. Cheaper can be a \$10 million house is being built on spec. A lot of time construction cost seems to be the overriding issue. Whereas if you have a hospital or a school where you might have a long-term owner, they may be willing to invest more in the construction costs to save money over time with, you know, basically better energy bills or durability where things would last longer. So how does that play with working between the building envelope and the mechanical systems?
John: Well I think…first of all, this is something that–back to your question–is overlooked an awful lot of the time is when projects are designed, it happens an awful lot where a project comes in over budget. And unfortunately we get into a process called value engineering and I always refer to it as de-value engineering. And what people look at is just pieces of the project that can be taken out or changed or cheapened up, if you will, to bring the project within budget. And I think often times what’s missed is back to not having the proper amount of coordination between the envelope and the mechanical systems to really try and optimize what is going to be the most cost-effective solutions for the owner over the long-haul.
Paul: It’s basically a money grab.
John: It is.
Paul: Just speaking from the, you know, I’m asking all these questions about mechanical systems. So speaking from the building envelope side of things, we almost never interact with a mechanical engineer on the project. Now we go to meetings, you know, they’re sitting there, we’re sitting there. But basically they’re doing their own thing and we’re doing our own thing. They’re telling the architect what kind of glass they need to use as far as to meet the load requirements or what the calculations are based on and then the architects are picking the color. But we’re really not involved at all on that level. Who do you think…I guess…well I’ll tell you what I think and see what you agree. Seems to me there’s a better role that the architect could play here in trying to bring it all together into a global solution rather than we do our thing, you do your thing, and that’s how we get to the end of the road. And that’s why problems sometimes occur.
John: Absolutely. I think it’s something that should be done on just about every single project. There’s again, as you said, there’s usually not much coordination beyond we’re using the U-value for our windows and we’re putting in this much insulation in the walls and ceilings because this is what meets code, rather than, “Hey, what if we end up putting another two inches of insulation in the walls or roof? What if we look at going with a better performing window? Yes, it’s going to have this impact on the installed cost of the building but what impact is that going to have on the mechanical systems?”
And more importantly, for the owner, a lot of people own their buildings for a very long time. And what we find is some of these very simple adjustments can have a three-year payback or better. And that often times gets overlooked. And when engineers are doing their load calculations, at least the way we do it, the software we use, all of that information is built in. It is fairly easy to model the building over the next 20, 30 years and do a few comparisons on different windows systems and insulation systems to find out what’s going to work best.
Paul: And sadly that doesn’t seem to happen much.
John: No, it really doesn’t. But again, I think the team itself needs to be focused on what is best for the life of the building and how is that building going to perform. What’s going to give the building the least amount of maintenance and have the best efficiency for the dollars spent on it?
Paul: Seems like we should set a goal–we being the design team, with regards to energy and the envelope and mechanical systems and whatnot–we should set a goal for where we wanna end up and work towards that rather than what I see the way it’s being done now is we start in the middle and kinda work to the outside. And we end up somewhere but not necessarily…there wasn’t any intent to go anywhere, to begin with.
John: Absolutely, absolutely. And the approach we take is we, as a group here, we have in our process is we start every project with the end in mind. And when I say the end in mind, it’s 3 to 5 years down the road when the building is completed. And one of the questions we ask building owners whenever we have the opportunity is to take them into the future and ask them if we’re standing at this project in three years after it’s completed, what has to have happened for you to be really happy with this building? And you can get some great answers by asking that question but it’s a question that needs to be asked as a design team group, not just as an engineer or as an architect or as a building envelope consultant.
Paul: Yeah, really great point. It’s just the integration seems to be lacking.
John: Right.
Paul: Let’s talk a little bit about commissioning. You know, right now we’re still talking about design but…so commissioning, is it fairly common with mechanical systems?
John: Very much so. We deal an awful lot with commissioning. We do commissioning both ourselves and we work on projects that are being commissioned by a separate commissioning firm. And a lot of LEED projects require commissioning. It’s part of the LEED process.
Paul: So just to give everybody some background about what we’re talking about, that everybody in the audience may not be super familiar with commissioning, could you just kinda give a broad brush definition of what’s commissioning and kinda what’s the process for it?
John: Yes, so our two different kinds of commissioning according to LEED. There’s your standard commissioning and then there’s enhanced commissioning. What a commissioning agent is, is they are an independent third-party firm typically, that did not provide any design services. They are not contracted by the contractor, they are not contracted by the design team. Rather they are contracted directly to the owner. We typically like commissioning to happen in the enhanced format where the commissioning agent is involved at the very beginning of the project. And the commissioning agent will review the scope of the project and the design team will produce a document called “The Design Intent”. And basically what that is is a narrative of how the building is to be built, how it’s going to be constructed, the systems that are going to be installed.
And they use that document and track that throughout the project to make sure that these goals and intents are being met throughout the project. We find the commissioning as focused on mechanical systems, plumbing systems, and electrical, and some on the building envelope.
Paul: I was gonna ask you about that. You have been involved with projects where there’s commissioning for the building envelope?
John: Yes. And the level of commissioning that was done was they are providing documentation that the insulation was installed per the plans. The sealing of the envelope, the roofing systems were installed per the design documents. I have not witnessed any testing of the envelope, though, as part of the commissioning process.
Paul: There’s been an effort underway and a few years back and I assume it’s still alive. ASTM has been involved with this, the National Institute of Building Science, NIBS, and others in developing a commissioning process for the exterior building envelope. And we actually you know, tried to get involved with that. What we found was either there was no market or it was very commoditized where owners were doing it because they felt like they should do it but they weren’t looking into spending any money on it. And so, it was a superficial commissioning process at best.
What’s interesting is the scope of services that GCI Consultants provide. So when we first got into it, we said to ourselves, “What is building envelope commissioning?” In fact, I went to an ASTM meeting where it was kind of like a scoping meeting to start the whole process and try to understand what is this building envelope commissioning thing? And guess what? Nobody knew. And it turns out that the services that we deliver typically on construction projects, which is working with the design team, the architect and the design team during design, reviewing, shop drawings and submittals, performing inspections and testing, during construction, and then some sort of sign off at the end and documentation of the whole process, probably more so with when it’s so-called commissioning job than not, what we’ve been doing all along was actually commissioning. It just never became…it still hasn’t become a formal process for construction projects. And I don’t know if it’s the money thing or what. But again, the mechanical MEP stuff, mechanical electrical plumbing, obviously seems to be a lot more common than the building envelope.
John: Well, I think that it’s not embraced too well because people have this assumption that the project is being designed well and therefore it’s being constructed well and why should they have to pay a third party to go through and verify all of this work.
Paul: That’s a great point.
John: And in an ideal world you wouldn’t have to. But things happen on projects. Things get missed by either the design professionals or the construction professionals. And if I was a owner of a large building I would want that building commissioned fully. I would want the envelope commissioned. Is it sealed up? You know, if I’m paying to heat and cool this building, I want to make sure that all of the insulation is in place. I want to make sure that I’m not going to be having a roof that’s leaking or windows that are leaking over time. And the added cost for building commissioning is very small compared to these bigger fixes over the life of the project. And I think if commissioning is done well, the commissioning services will more than pay for themselves over the life of the project.
Paul: Yeah,
John: We’ve all seen and heard what lawsuits are like and no one wants to be in a lawsuit except maybe some attorneys. And I think that commissioning is a way for both an owner, a design professional, and a construction professional to give everyone a little bit better peace of mind that the project as a whole was done correctly.
Paul: Commissioning is a proactive rather than a reactive approach.
John: Very much so, very much so. We are very big proponents of it.
Paul: Yeah, I’ve had customers before, you know, contractors and owners that say, “Look, I’m happy I’ve spent a little bit of my warranty dollars up front to make sure it’s being done right and prevent the problem rather than having unhappy owners, tenants, building occupants, whatever, later on in the process.”
John: Correct. Absolutely.
Paul: So let’s talk a little bit about construction. You know, I said this is where the rubber meets the road and I know you were talking little bit about value engineering before which is…or value de-engineering, I think you called it. And…
John: De-value engineering
Paul: De-value engineering, I like that even better. So when getting into the construction phase of a project, you’ve put this really good design together and, you know, the project’s got the whole team in place, the contractor and the subs and what not, how does that go? I mean does that…do they normally build what you design or do they always build what you design? What happens during construction?
John: Well, that’s a great question. We find that really good contractors will want to have the design team involved throughout construction and have an active part in the construction process. We find sometimes less reputable contractors do not want to have engineers and architects and other consultants involved during the construction. And I take that as a bad sign. Again, back to what we discussed earlier in commissioning is, there are things that are missed during construction, either by the design team or by the build team. And I feel that it’s in every design professional’s best interest to stay involved with the construction process, whether they’re wanted there or not, to ensure that their design is being met.
Paul: If they’re not wanted, that’s definitely a red flag. We run into situations in the building envelope where the contractor, you know, usually the name of the budget, the schedule, the subs they work with, whatever, basically redesign the whole exterior wall system. You know, they get hired during pre-construction to put together budgets and the owner relies on that, usually very little information. So they’re doing a lot of the scoping themselves and then we get around when it’s time to actually build the building and then maybe it’s something seemingly innocuous, the weather barrier, fully applied waterproofing around window openings, let’s say, where the contractor didn’t put them in as part of their budget.
We get to the construction, they’re noted on the drawings or we note them in the submittal reviews and all of a sudden, the owner is calling up saying, “Hey, what is this?” And say it’s a 50 story building and it doesn’t seem like a big deal to put this stuff around the window openings but all of a sudden its \$750,000 being added to…it was a bad budget. So that happens a lot with envelopes. Do you have that happening also with mechanical system where your contractor, and I guess maybe the owner, redesign, re-jigger your design?
John: Yes, we have had that happen in the past, unfortunately. We had a project where the owner specifically requested that we were not to be involved during construction because he did not want to pay for our services. What happened on the project was the mechanical contractor did not install our design per our plans. This is a fairly complex geothermal heating and cooling system and I received a phone call from another consulting engineer about three years later who had been to the job site at the owner’s request to do an evaluation of the system, which had completely failed.
And the engineer called me to tell me that my plans were great but the project was not installed per our design. We then went to the project to verify this and the contractor had completely disregarded our plans. The contractor had taken many shortcuts and not installed a lot of the components thinking that it was overkill or redundant. And it caused several heat pumps to burn out over time. It caused tremendous amount of humidity build up in a few of the rooms and they ended up having a mold problem as a result. In the end, the mechanical contractor was sued for roughly \$100,000 for their defective work. And I feel like we could have saved all of that expense and pain to the owner had we been involved for a few thousand dollars during construction.
Paul: Do you find that when changes are made, is it motivated by money or is it ignorance? Or maybe just yes, yes and yes?
John: So we find that really depends on the contractor. We have contractors that will come to us with a change and it’s a very legitimate change. It’s something that will make the installation go better and actually be better for the project over the long term. But we also have contractors who don’t want to put something in and ask if they can make a change and it’s purely money driven. And they’ve bid the project but they want to put in a less inferior product. And we see that a lot.
Paul: So I guess the moral of the story here, and let’s say this would apply to the envelope as well is, if you’re gonna make a change perhaps you should run it by the designer of the original system?
John: Absolutely. I would definitely engage your design team first and foremost and ask them if they approve of it. And get a reason for why they think the change is good or bad. But I would definitely and always include the design team in any changes during construction.
Paul: Now, the second part of the construction thing is that obviously, even if the design is intact, everything needs to be done correctly. It needs to be installed properly, follow manufacturer’s recommendation, use best practices, all that kind of stuff. Do you…and I know the answer is gonna be yes but I’ll ask the obvious question. Do you run into those sorts of problems as well?
John: We do. And one thing that we require is on our projects, we require a factory-trained representative to start up all equipment. So you don’t just have someone out there thinking it’s all set to go and hitting the on switch and pushing the green button and hoping that it all works. We require these factory trained personnel to come in and they’ll do a complete check over of the system and make sure that…it’s also integral with commissioning as well of making sure that all of the connected components are installed the way that that manufacturers require them to be installed. Otherwise, yes. You’re going to get all sorts of problems if someone thinks that it’s installed, hits the button and walks away from it.
Paul: So let’s talk a little bit about best practices. I guess also we should talk about common mistakes that occur during construction. Let’s start with the mistakes and then we’ll go into the best practices. So on the envelope side of things, you know, the mistakes that we see are basically not paying attention a lot of times or having an untrained workforce. We may go through a whole project and design, a really nice building envelope, really careful with shop drawings and submittals, making lots of comments and, you know, making sure we’re all…have meetings, go through everything, make sure everybody is on the same page. And then we go out to do pre-construction meeting or subsequent third-party quality control inspections and the guys that are out there have never seen the design, the drawings, anything. They’re just putting it in the way that they think it should be done.
So all that good work that was being done upfront is basically ignored and guess what? Problems happen. We do a water test and water is leaking in all over the place. And it’s not necessarily bad intent, it’s just sloppiness and ignorance. And you gotta really be careful with the envelope–and I suspect you’re gonna be saying the same thing on the mechanical side–that everything gets done…you know, the best design is great. But if they don’t follow through…and the quality side, everybody should be involved with it from the installer to the supervisor to the contractor, the superintendent, the architect, the owner. Everybody needs to be…really be on it. And then you’ve got a better chance of not having an issue.
John: Absolutely. I find what works with us is having that pre-construction meeting with all of the trades that will be performing the work on our plans and having a discussion with them before they pick up a hammer or a drill or what have you and explain to them what our intent is of the system and how it is supposed to work and what the components of the system are doing. And I think if that’s something that is done with all trades at the beginning, that way the guys working in the field have a better picture and a better feel for what it is that they’re actually putting in.
But at any rate, it’s back to getting all of the subcontractors on the site, in addition to the general contractor, a picture of what it is that they’re building. So that, again, if they kind of have that same end picture in mind so that they’re not just putting a piece of pipe in, they’re not just putting insulation in, they’re building this building that is going to perform per this design we’ve put together. And I feel like if you can get some buy-in from the construction team, that goes a long way for the life of the project.
Paul: I think the keyword there is team. Everybody needs to work together.
John: Right.
Paul: So now, we have designed it, we’ve build it. Everything is good and it’s time for the owner to basically occupy and take over the building from the design and the construction team. And you mentioned hitting the little green button, so let’s talk a little bit about maintenance and operation of mechanical systems. What needs to happen for things to continue to go well?
John: Well, what needs to happen is the owner needs to have training with the contractors who installed the system. So we typically will involve the temperature controls contractor, the mechanical contractor, and the plumbing contractor. And they will spend a designated amount of time with the owner going through every system, system by system. And this is after we have done all of the testing to make sure everything is operating fine. But then the contractors will go through with the owner’s representative, whomever that may be, their head of maintenance if they have a head of maintenance for the project or the owners themselves and they will go through and demonstrate to them how each system works. And show them, if it’s an elaborate control system, how the system works, what functionality they have with the system and then also give them training on routine maintenance: items that they need to take care of or pay attention to. Simple things like changing filters, looking at if fans have belts, of making sure that the belts are tensioned properly.
The other part is making sure that the owner has a maintenance contract set up, ideally with the mechanical contractor who installed the system. But if not then he needs to have whomever is going to be doing his building maintenance involved with that training so that the maintenance personnel, again, can have a good and first-hand understanding from the installing contractors. We find that you can have a great project and have it be installed, everything is fine, it’s…everything is working wonderfully. But if the building is not maintained, you’ve just wasted all this time and effort putting in a great system. We had a simple case of a building a few years ago where we were called back because they were having these pressurization problems in the building. And so I got the controls contractor involved, we went and looked and there is all this air leaking in through doors and windows. And this is happening when that was -20° outside.
So what we found after going through and testing the whole system, we couldn’t find anything wrong. And so we got the owner back involved and asked him if he had had the system maintained and who had been doing it. And he assured us that his system had been properly maintained. What we ended up finding on this particular project was the filters in the main air handler for this great big building had never been changed since the building had been turned over. Yes, from the time it was turned over. They had done remodeling in part of the building after construction. These filters were caked completely full of sheetrock dust. And furthermore, the contractor who did the initial construction wrote the date on the filters, which is commonly done. So we could go and verify how old these filters were. And we took the filters out and put new filters in, turned the unit back on and all of his problems were fixed.
Paul: Voila.
John: Yeah, voila. Exactly. But he went through all of this headache thinking that the building wasn’t constructed right, the building wasn’t designed right, nothing was working. And the only one that was doing his job was the maintenance guy.
Paul: Which was actually the other way round.
John: Exactly
Paul: So is the maintenance guy the one who actually runs these systems or if they have a maintenance contract, who’s really in charge of running the systems? I’ve been involved in projects where the envelope has had issues due to negative pressurization and it was basically poor operation of the mechanical system. They’d actually designed it and pressurized in an addition to have built to this hospital. And then they opened the doors that led to the rest of the hospital and everything went to hell.
John: Right.
Paul: So who’s ultimately supposed to be watching after that, once the building is in the owner’s possession?
John: Typically it’s the maintenance department. Hospitals will almost always have a dedicated maintenance staff. And those guys from our experience are extremely well-trained and they know their systems inside and out. But that usually falls on them to, you know, it’s helpful if the building owner has some documentation in their hands to say, “Yes this was tested at the completion of construction. And the envelope wasn’t leaking, we weren’t negative pressure, everything was working just fine.” So that, at that point in time they can go back to maintenance and say, “The system was working, so something has changed since then.” And that happens. Damper motors will burn out or freeze up, linkages on dampers will become loose.
And it can be something as simple as that. It can be a wire to a damper motor that the screw on one of the wires was not tightened all the way and there is enough vibration to cause the wire to come loose. We’ve seen that before quite a few times. And again, it all comes back to the owner having some assurance from the design team and the build team, ideally from a commissioning agent, that his building is functioning the way everyone wanted it to when the keys are turned over to the owner.
Paul: Yeah, so you basically got a point in time where everything was good. I can see the benefit there because then you can say, “Okay, if it worked at one point, then what’s changed? And let’s go find that and remedy it.”
John: It makes it much easier to solve the problem if you know it was working fine at one point in time.
Paul: So I want to talk about maintenance on the building envelope. On the building envelope side, aside from roofs, there is very little or no maintenance typically. Now, that’s not to say that’s the case with every building but more often than not that is the case. Now roofs come with manufacturers’ warranties and they can be 10 to sometimes 20 years or longer and they require annual inspections by a third party or sometimes by the roofing manufacturer. And maintenance, and this is to maintain the warranty, which that doesn’t always get done either by the way. But if it is done then somebody is up there looking at it at least annually and is a problem develops then there’s an opportunity to correct it before it becomes a failure. Or even if there is a failure it’s isolated and not throughout the whole system.
What we see on the rest of the building, the walls, the windows, the ceilings, things like that, warranties are typically a lot shorter, particularly on windows and doors. You know, it may be a year or two for water leakage. Glass, insulated glass, laminated glass, things like that can be a 5 or a 10-year warranty but that’s just the glass itself. And then the wall systems usually is like a cornucopia of some warranty, some not. That the contractor may warranty it for a year, it may have sealants that have 20-year warranty, paint that has 5-year warranty.
So there’s a lot going on. What almost never happens is that there’s an annual inspection of the façade. It may be a one year later inspection but typically not an annual inspection. And what happens there…just like the roof. If they didn’t inspect the roofs, things start to deteriorate. Say the sealants are aged, have aged and started to have voids in them or birds are eating them or there is maybe a windstorm that causes some damage to the building or stucco cracks or whatever. It doesn’t get addressed until water is coming in the building, molds growing, your humidity levels are up, things like that. And it’s very reactive, not proactive
And I think it’s a real, there’s a real need to do better in that regard. Inspecting the façade of a large building can be very expensive because you can’t necessarily get easy access to a roof, you can walk around on the roof most of the time. You know, mechanical systems obviously are in their designated spaces. But if you’ve got a 10 story building, unless you’re Spiderman, you can’t get out there and look without a lot of equipment and whatnot. I’m hoping that now where we’re seeing drones being used a lot more…and in fact, we have our own drone, AIR GCI, that can actually go out on a regular basis, fly the drone and analyze the footage, see if any of these products have developed, any of these problems are developing. Because if you can catch problems early, you can correct them and stave off much bigger problems later. The saying is an ounce of prevention is worth a pound of cure and it’s very, very true.
So did you ever have situations, John, where problems with air quality or mold growth or whatnot, they call you out as a mechanical guy and it turns out something with the envelope is causing it?
John: Yeah, we do see that on occasion. And you’re exactly right, it becomes a reactive time rather than a proactive time, unfortunately. And I think that having the envelope inspected annually is a great idea because a lot of times, like you said, you know, mold often times does not show up in a building until two, three years after it’s completed. And if you have a one year warranty on a project and you stop doing inspections at that point in time, it’s not something that’s just going to show up right away.
So I think that you can be very proactive in having your envelope inspected on a much more regular basis. I think using a drone, and as technology improves, is going to be an incredible tool for you to use to doing envelope inspections. We have a drone ourselves and we use that for projects that we’re working on. Right now, we use it more for remodel projects, though we will fly it around the building and get documentation of what’s on the roof and what’s on the side of the building. But I think beyond that, it’s a tool that you can use with a envelope of getting very good high-quality images around windows. And whether it be on an annual basis or, in your case, after a very big storm event to do quick and accurate assessment of the envelope.
Paul: Yeah, it really works well. So, John, this has been a really great discussion. I mean, I’m passionate about this actually that I think we can do better in a lot of these areas. Having the guys on outside of the building and inside of the building working together to a common goal with an end result in mind from the beginning, I think you really have a better outcome for projects to what some are getting. You know, keeping small problems from becoming big problems and being proactive instead of reactive. So I really enjoyed our discussion.
John: I did too, Paul. This is a very great discussion to have.
Paul: So thank you so much for coming on the “Everything Building Envelope” podcast.
John: Well thank you for having me, Paul.
John, if people want to contact you how can they do that?
John: The best place, Paul, would be our website. And that is, www.jmengineering.net.
Paul: Great. And I can vouch for John. I know he’s doing a lot of cutting edge stuff with technology and a really great guy. So I would encourage anyone who is interested to please take a look.
Paul: And I’d like to remind everybody that if you’d like to subscribe to the “Everything Building Envelope” newsletter to text the word, “Building Envelope,” to 22828. Again, text the word, “BuildingEnvelope” to 22828. So, thank you, everyone, for listening. Really great topic we had today and I hope you enjoyed it. And this is Paul Beers saying so long until next time.