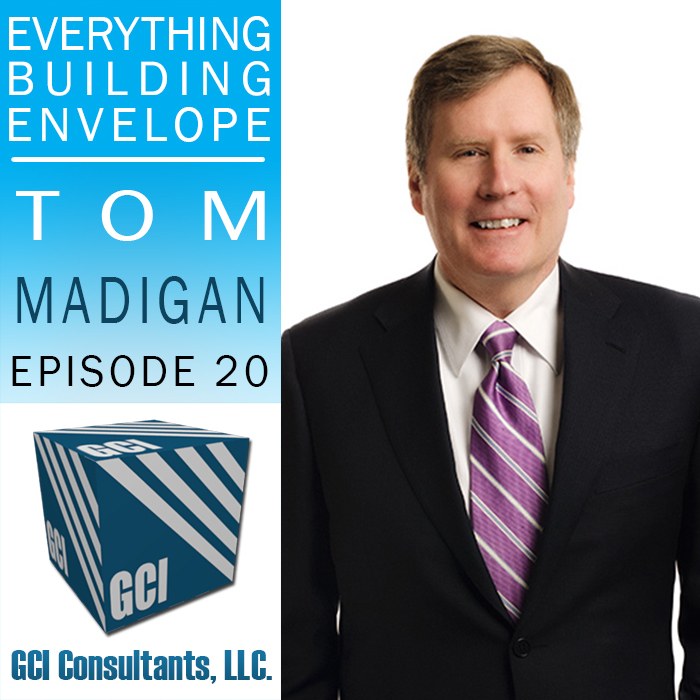
About The Everything Building Envelope Podcast: Everything Building Envelope℠ is a dedicated podcast and video forum for understanding the building envelope. Our podcast series discusses current trends and issues that contractors, developers and building owners have to deal with related to pre and post construction. Our series touches on various topics related to water infiltration, litigation and construction methods related to the building envelope.
https://www.everythingbuildingenvelope.com
*** Subscribe to the show and leave us a Review on ITunes!
The Everything Building Envelope Episode Transcript:
Paul: Welcome back, everyone, to the “Everything Building Envelope” podcast. This is Paul Beers. I want to remind everybody, first of all, before we get into today’s topic, that we have a newsletter, the “Everything Building Envelope” newsletter. And if you would like to subscribe to it, please text the word “building envelope” to 22828. So it has technical articles and other things of interest to the building envelope community. Again, for the “Everything Building Envelope” newsletter, text “building envelope” to 22828.
I’m really excited about our guest today, Tom Madigan. Tom is a lawyer. He is the Chairman of the Construction Practice Group at Buchanan Ingersoll & Rooney. Buchanan is a national law firm and has six offices in Florida. And welcome, Tom.
Tom: Thank you, Paul.
Paul: So, Tom and I have worked together in the past. Of course, he’s the lawyer, and I was the expert, and we’re old friends in that regard. And he’s a great guy. And I think it’s really gonna be a very interesting podcast for everybody. So, Tom, before we get going, maybe you could tell the listeners a little bit about yourself?
Tom: Sure. I’m a construction lawyer. I’ve been practicing 30 years now. I am a litigator handling both the prosecution and defense of claims, many of which involve building envelope performance as well as delay claims and other performance disputes arising from construction of high-rise residential, commercial, and industrial projects across the United States. I’ve done a lot of work in the Southeastern United States on issues of water intrusion. I’ve also done work in the Northern United States on water intrusion and air intrusion and energy performance. And my work as a litigator has also given me a perspective on how to avoid some of the problems that I’ve seen. I also advise clients on the front end in terms of contract negotiations and then during projects to try to avoid disputes or mitigate them once they arise and keep them from turning into full-blown litigation.
Paul: I think that that’s really a great word, “avoid.” I know that that’s probably what the listeners are most interested in is not being involved in a long energy-sapping, expensive dispute, but rather do what needs to be done upfront to try to stay out of it.
Tom: Yes. I think that is everybody’s goal, with perhaps the sole exception of the lawyers handling the litigation.
Paul: And maybe the experts.
Tom: And maybe the experts.
Paul: So we were talking about risks and risk management. And, today, we’re gonna talk about effective allocation and management of performance risk in the building envelope and construction. And, Tom, you know, you’ve done a lot of work in buildings with building envelopes, water leakage, air filtration, things like that. Does the building envelope represent a disproportionate amount of claims on buildings?
Tom: It does in the respect that when you have a building that doesn’t perform properly and it leads to litigation, even when it’s not exclusively related to the building envelope, the building envelope seems to be involved. So, whenever there’s a water intrusion problem with a building, you can almost guarantee that the building envelope designer, supplier, installer of all the materials and systems will be named, along with the roof and some other elements. It doesn’t always turn out that the envelope was the source of the water intrusion, but those parties always get dragged in.
Paul: Yeah. Occasionally, I do seminars, speaking gigs, and things like that, and one of my favorite lines starting out is “What’s the easiest way to screw up a good construction project?” And it’s to have water leaking in at the end of the job. All hell breaks loose usually when that happens.
Tom: Well, and I think that the building envelope, with some exceptions, is typically a combination of various materials and systems. And that brings with it integration and coordination challenges, which, if not designed correctly and not installed correctly, create performance problems. So I think it’s also a product of the complexity of the building.
Paul: Well said. So let me ask you what’s the difference between risk management and risk allocation?
Tom: Sure. So risk management involves those things that I think everyone is typically familiar with, and hopefully includes in their business organization: quality assurance and quality control measures; tsupervision, inspection and testing. All the things we do to make sure that the work is of good quality and doesn’t have deficiencies. Or to catch them and correct them. And then on the far end, it involves insurance, to manage the financial loss if the risk comes to fruition.
Paul: So that’s risk management. So what would risk allocation be?
Tom: Risk allocation is simply…and here, we’re talking about contractual risk allocation…it’s the assignment of responsibility for a particular risk. Which party, contractually, will be responsible for making sure that a particular element of the building performs in accordance with the needs of the owner, and will be liable if the end result does not meet that performance requirement.
Paul: For example, say that there’s water leaking into a building, and there’s a litigation, and everybody that’s involved with the exterior of the building is named as a party. Let’s just say stucco, waterproofer, window manufacturer, and others. Is it the window manufacturer saying, “Look, my windows were perfectly fine. And even though the water is coming in near them, it’s not my fault”?
Tom: Now, that is what I would call after-the-fact assessment of responsibility. What we’re talking about with risk allocation is on the front end of the project. When the team is being assembled and the work responsibilities are being divided up through the contracts, determining which of the various trade contractors and suppliers and design professionals are going to be responsible for which elements.
So for example, to use your example where you’ve got a building envelope that involves both EIFS and window systems. Contractually, who is responsible for making sure that the window system integrates properly with the EIFS so that you don’t have a source of water intrusion at that junction. And if you do, who is called on to make it right.
Paul: So I think we all understand why risk management’s important. But why is risk allocation so important?
Tom: Because who you allocate the risk to plays a big part as to whether it is effectively managed at the end of the day. The goal of risk allocation is to place responsibility with the right party; which is the party who is in the best position to manage or mitigate the risk, or to avoid it entirely. Because that increases the chances of successful risk management.
The other goal is to place liability with the person who is best able to avoid the risk. Because that is simply equitable. And then to place it on the party who is in the best position to correct or remediate it, or to carry the financial burden of its failure of performance.
If you allocate the risk to a party who is not in a position to effectively avoid or mitigate it, or who can’t bear the cost of the risk if the performance fails, it just increases the probability that the risk is going to come to fruition, and it’s not going to be adequately remedied. And you’re going to, for example, end up in a multiparty litigation with everybody pointing fingers at each other.
Paul: But isn’t the thought that the designer is always responsible for design and the contractor is always responsible for construction?
Tom: So, in very broad general terms, that’s true. That relates to the traditional design-bid-build process, particularly in competitively bid public projects. But that’s only a general proposition. It’s not an absolute rule. Even in design-bid-build projects, where you have an architect separately contracted to the owner, and a GC under a different contract with the Owner, the responsibility can differ depending on whether you have design specifications or performance specifications.
You know, design specifications are where the plans and specs tell the contractor exactly what to build, what materials and products to use. Akin to a blueprint or a roadmap. The contractor in that circumstance, is responsible to build in conformity with the design. If the construction conforms with the design, but it doesn’t perform as the owner intended or needed, that’s not the contractor’s responsibility.
Performance specifications, on the other hand, simply set a performance requirement that the contractor must meet. But the contractor has discretion on how to best meet that requirement. He has some discretion in the choice of materials, perhaps, in the choice of systems, certainly, and in the approach to the construction. But he then bears responsibility for those choices. And if he doesn’t meet the performance requirements at the end of the day, it’s the contractor’s responsibility.
And, you know, frankly, most private projects are a combination of both. And it’s sometimes not clear whether the specifications are design specs or performance specs; whether the responsibility lies entirely with the designer, or whether it’s been delegated in some respects to the contractor, or exactly how much detail with respect to design is required of the contractor in the shop drawings and coordination drawings and submittals. Those things aren’t always clear, and they’re often the subject of litigation when things go wrong.
Paul: We see a lot of that at GCI Consultants on the construction projects we’re involved with. When a contractor takes on design responsibility or risk, how do they allocate that at that point?
Tom: Could you repeat that question?
Paul: When a contractor takes on design responsibility, how do they allocate their risk?
Tom: So the first key is for the contractor to understand that he’s taking on a design responsibility and to knowingly assume that responsibility. You know, if the building envelope component of the project is design-build and the contractor has the resources and the expertise to take on that responsibility, that’s great.
The biggest problem I see is where a contractor doesn’t understand how much design responsibility he’s taking on. You get disputes over what the purpose of the shop drawings are. The architect is expecting the contractor to provide a lot of missing design detail, to show how systems will be integrated, to show details on joinery, to show details on integration, both of different systems and with the surrounding conditions. But the contractor doesn’t understand that’s what’s expected of him. He thinks he’s just providing shop drawings that show, you know, product detail, and he’s not prepared to take on the larger design responsibility. So that’s the first key, to understand the risk that you’re assuming and make sure that you’re prepared to manage it and perform as required.
The other element that comes up often is where a contractor may agree to take on design responsibilities with the expectation that he’s going to rely on a subcontractor or a supplier to actually do the design work. He’s not actually going to do the integration details, or the design details. He is going to rely on the system manufacturer, but is then not clear in his or her dealings with the system supplier , so that the system supplier does not understand what the subcontractor expects. As a result, it doesn’t commit the right personnel or attention to the application engineering and coordination. Or the contract between the trade contractor and the supplier doesn’t reflect the allocation of design responsibility to the manufacturer, because it is a standard form contract of sale that says something like “We’re just the supplier. We just supply the materials in accordance with your takeoff.” “Application engineering is excluded. Shop drawing preparation is excluded.” So the contractor is taking on a risk it isn’t in a position to perform, and has not effectively allocated the risk downstream to the party that it is relying on.
Paul: Yeah, because if you have a scenario where, you know, let’s say that the design is vague, maybe intentionally vague, with regards to certain systems. And the contractor passes it on to a supplier or a sub or whatever without really adequately covering all the bases, shop drawings, submittals, things like that. Correct me if I’m wrong. They’re effectively letting the subcontractor ultimately design it and probably not properly allocating the risk.
Tom: Right. What happens is a couple of things, you know, because when something goes wrong…you know how this works…it flows downhill, right?
Paul: Yeah.
Tom: So if the building envelope doesn’t perform, the owner looks to the GC and the architect, because the first question is typically, is it a design problem or a construction problem? And with your hypothetical, the architect may say, “Well, I allocated design responsibility to the contractor.” The general contractor then turns around and says, “Okay, Mr. Glazing Subcontractor, I allocated responsibility to you. I don’t care if it’s an installation problem, if it’s a design problem, if it’s a product problem, because you’re responsible to me for all of those things.”
If it is a product problem, or if the subcontractor was relying on the manufacturer to do the design details and coordination, the subcontractor wants to now look to the manufacturer to offload that liability. The problem is that the manufacturer says, “Well, but our contract doesn’t allocate that liability to me. I say I’m not responsible for those things. So it doesn’t matter that you might be responsible to the general contractor for. I’m not responsible to you. I disclaimed those things contractually. The liability stops with you.” Even though the subcontractor may not have done the work, may have been relying on the manufacturer to do it, because the contracts did not line up with the actual allocation of liability, the subcontractor finds itself holding the bag.
Paul: And hence the dispute?
Tom: Yep.
Paul: So what are some of the performance risks that need to be allocated between the architect and the contractor with respect to design of the building envelope?
Tom: So, we just touched on a lot of them in that example, but it is things like starting with determining what the performance requirements are for the building based on its intended use, and based on regional and local code requirements. Where you are [Florida], you have enhanced performance requirements in coastal regions. Who is responsible for, in the first instance, determining what the level of performance is required for the building envelope and its constituent parts? Then, who is responsible for selecting the products to meet those requirements? Who is responsible for making sure that the various components are compatible with each other, and for detailing how they are going to be integrated into the complete envelope system?
You know, Paul, we’ve both seen building envelopes that have combinations of stucco, masonry, brick, metal panels, curtain wall, window wall, sliding doors, storefront. Who is responsible for making sure that each of those individual components meet the performance requirements, perform together, and are erected in the right manner?
Paul: Lots of opportunities for problems there.
Tom: But, you know, an often overlooked piece of that is the definition of the scopes of work and the sequence. And that’s an allocation issue. Is that all going to be specified by the architect? Is the architect going to specify the order in which the various components are installed? And who is responsible for flashing in which areas? Who is responsible for which caulking? Who is responsible for which integration details? Or is all of that going to be left for the general contractor to determine in how it breaks up the subcontract packages? And who is going to be responsible for making sure that the sequences are followed and the work is performed in the correct order so that the people responsible for integration can actually do what needs to be done before the successor work comes along?
Paul: Yes. Doesn’t that often or usually come down to how the contractor buys out the project as far as, you know, which subs are doing what?
Tom: That’s how it is implemented. But, you know, it has to be thought about up front, with not just respect to who’s going to give the best price, but how is this actually going to be constructed. And then during the project, there is the management of making sure that the contractors are getting to the work when it becomes accessible to them and performing their work that is predecessor to somebody else’s follow-on scope of work. You know, so you don’t have somebody coming back, trying to put flashing in after the windows have been installed.
Paul: And on top of that, we’ve got the natural tension that exists in any project between the scope of work and the budget.
Tom: Right. And that is another element of risk allocation. You know, there has to be a proportionality between responsibility and the cost of that responsibility. You know, if an owner is looking to a contractor, or an architect is expecting a contractor, to take on design risk, then they ought to be paid for that. That’s a cost.
And, you know, maybe going design build on the building envelope is the most cost-effective approach, and maybe it’s not. But you have to weigh those things. You have to weigh the potential risk of non-performance versus the cost of buying that risk or selling it to a particular party, and make an informed decision.
The real problems arise when risk is forced on someone, when it is done in a less than clear fashion, and that person doesn’t price the risk into their work. Because if they haven’t priced the risk in, chances are they’re not going to take the steps necessary to manage it effectively.
Paul: Kind of like if you want this job, you’ve got to meet the budget.
Tom: That’s always an element. And, you know, the old saying is, you can have…what is it, “Fast, cheap, or good, you can have two of the three.”
Paul: That’s right. But cheaper is always the one that I see. So what are some of the things that should be taken into consideration when deciding the best way to allocate risk in the design and construction contracts?
Tom: So, we’ve talked about some of them. Certainly, it starts with determining which of the parties – the designer, the general contractor, the glazing subcontractor, the manufacturer and supplier – which one is in the best position to avoid or manage the risk of non-performance. If it is a product manufacturing issue, obviously the manufacturer is in the best position to manage that risk. If it is an installation issue, the installer is in the best position to manage that risk.
Where it gets trickier is where things become…you know, the intersection, product selection, integration of different systems where you have multiple parties involved and there is a need to coordinate their efforts and to oversee their performance to make sure that each does what is required of them. And that’s when you need to look at things like who has the expertise to identify risk, to manage it, to correct it.
Obviously, if it is a pure engineering issue, it is the design team that holds that expertise, and has control and authority. You know, in a typical contracting situation, where the owner contracts with the architect and contracts separately with the general contractor, the architect and engineer’s ability to manage and control the subcontractor, to hold them to the design requirements, is limited. They do not have contracts with the general or subcontractors, and, most importantly, they don not control the purse strings. They do not hold the checks. That is the owner or the general contractor.
You know, sometimes, there are licensure requirements or certification requirements that dictate where the risk has to be allocated. If design drawings have to be signed and stamped, then it is the professional who signs and stamps them and puts his expertise behind the work product and warrants that it is accurate and will perform. With product certifications it is the manufacturer who tests the product and obtains the certification, and represents that the product will perform to that certification.
And then the last thing we touched on was there is a comparative cost of allocating risk. If the owner or GC is going to allocate risk to one of the parties with whom it contracts, then the contract price ought to reflect that risk in order to ensure that the party has the resources and the motivation to manage it.
Paul: So what are some best practices with allocating risk between the design and construction contracts as it relates to building envelope?
Tom: First and foremost are clear documents. If the specifications are going to delegate design responsibility to the contractor for an element of the building envelope, the documents need to make that clear. It needs to clearly specify which elements of the design are to be detailed out or finished by the contractor, so the contractor knows what is expected of it and, again, can price it into its contract.
So, you know, the documents need to be clear as to what is expected. The level of detail required in the shop drawings. If the contractor is to prepare design detailed drawings, what standard will be applied. If there are coordination drawings required, what do they cover. You know, there is nothing wrong with delegating those elements of design to a contractor, and there is nothing wrong with a contractor assuming those responsibilities. But both parties [the party delegating the risk and the party assuming it] need to understand what they are requiring and what is expected of them.
When there is design delegation, it is still important that the architect-engineer be responsible for review and approval. I think that it is also a good idea to contractually require the architect and engineer and the contractor and the appropriate subcontractor or supplier to mutually inspect the work, or do a mockup, and to accept the implementation of the delegated design into the architectural specification.
Specifically with respect to a building envelope, if I am advising an owner, one of the things I will suggest for a large construction project, particularly one that is intended to have an architectural pizzazz to it, and might have a complicated building envelope, is that when you are negotiating with the architect, or when you are interviewing the architect, I want to see a demonstrated expertise in building envelope design. And if I am not comfortable, I would consider contractually requiring the A-E to have a sub-consultant for the building envelope for the building envelope. And, obviously, that is a cost that will get passed to the owner.
The other thing to consider is single-source responsibility for the building envelope. Here, we’re talking about a design-build contract for the building envelope itself, that provides a single source of responsibility for both design and construction. You know, so when things go wrong, it eliminates the typical finger-pointing.
Paul: So let’s shift over to risk management. What are some examples where failure to properly manage the design and construction process can increase the risk of non-performance?
Tom: The big one is what I call “Frankenstein” designs or specifications, that mix-and-match components or system details or get revised, either because the architect has a particular concern from a past project or as part of the value-engineering effort. Whenever you are using multiple materials and systems as part of the building envelope, or are making revisions to standardized details, it is critically important that you involve both the manufacturer and the installer and get their input and approval. There is no surer way for an owner to end up with a lot of finger-pointing than when you have a building envelope that is the product of a whole bunch of value-engineering efforts where system components have been changed or revised and the original manufacturers and suppliers won’t take responsibility because, in the end, it is not the system they tested and warranted.
Paul: What are some of the best practices in risk management to avoid or decrease the risk of non-performance?
Tom: So, again, when we are talking about building envelope systems, particularly those that might integrate various materials or various separate systems from different manufacturing sources, integration and coordination is really the key. And there are a number of collaborative design tools now available to help with that effort.
BIM is probably the best known, Building Information Modeling. It allows for integration of shop drawing and product information into the architectural design. It will give you a depiction of the specific performance capabilities of a product in the design drawings. It will incorporate that information. It will incorporate the shop drawing details into the original design drawings, so everyone has a complete design showing all of the components of the building envelope. It will help to detect clashes between those various components at the design stage, so they can be resolved.
There is submittal management software to help track product submittal or shop drawings and their review, rejection, return, re-submittal, and ultimate approval. You know, that becomes very helpful in projects that experience delays, because it is when a project gets delayed and everyone’s hustling and trying to catch up or to avoid falling further behind that shop drawings don’t get submitted. Or they get submitted, but they get only a cursory review. Or they never get resubmitted, and noone follows up. Or product information is not closely evaluated and potential problems are not detected.
Kick-off and coordination meetings are an old-fashioned management tool. They allow you to work out all the integration and sequencing issues before the work actually starts, get everybody on the same page. Mockups and field testing of complicated building envelopes are invaluable. They allow you to actually build the thing in a smaller scale and test it to make sure that it is going to perform the way it is intended.
Paul: Those are many of the things that are near and dear to our hearts at GCI Consultants as we work on projects, you know, showing everything clearly. We used to get these flat details, 2D details, for corner conditions where a lot of materials are coming together. And there was really a lot of guesswork to try and put it all together and have it work and then getting everybody together at the beginning of the project, the beginning of design, and also the beginning of construction to make sure that all the parties know each other’s roles and are on the same page and working together.
And then, you know, doing a mockup, a lot of times, it can just be an in-place mockup on the building, as early as possible and testing it so that, if you do have a problem, you identify it and solve it before, you know, a year later, everybody’s getting ready to move in and, all of a sudden, you got to go back and do a remediation program.
So, Tom, really interesting. And, you know, I think we’ve still got a lot of things that we could talk about, particularly as it relates to the building envelope and performance and disputes and whatnot. Would you be up to doing a part two of this podcast to kind of delve a little deeper?
Tom: Sure, absolutely. It would be my pleasure.
Paul: Great. Yeah, that would be wonderful, because I know it’s really interesting. It’s great stuff. I would like very much to keep charging into it or diving deeper into it. So we’ll do our next episode. It will be a continuation of this one. And, Tom, again, thank you very much, and I really look forward to doing that with you.
Tom: Thank you.
Paul: So thank you, everyone, for listening to the “Everything Building Envelope” podcast. I wanna remind you again that we have the “Everything Building Envelope” newsletter. And if you’re interested in getting on the list, please text the word “building envelope” to 22828, again, “building envelope” to 22828, to receive the building envelope newsletter.
And that ends this episode of the “Everything Building Envelope” podcast. Thank you for listening. And this is Paul Beers saying so long, till next time.
About GCI Consultants: GCI’s building envelope professionals provide consulting services to ensure clients receive maximum value and return on their investment in the firm’s services, which include:
- Engineering Services
- Design Assistance
- Field Testing
- Quality Assurance
- Forensic Evaluations
- Roofing and Waterproofing Consulting
- Litigation and Claims Consulting
- Façade Assessments
- Catastrophic Damage Evaluations
- Due Diligence Surveys
http://gciconsultants.com
Be Social With Us-
https://www.facebook.com/gcibuildingconsultants/?hc_ref=SEARCH&fref=nf
https://www.instagram.com/everythingbuildingenvelope
https://www.linkedin.com/company/gci-consultants-llc?trk=biz-companies-cym