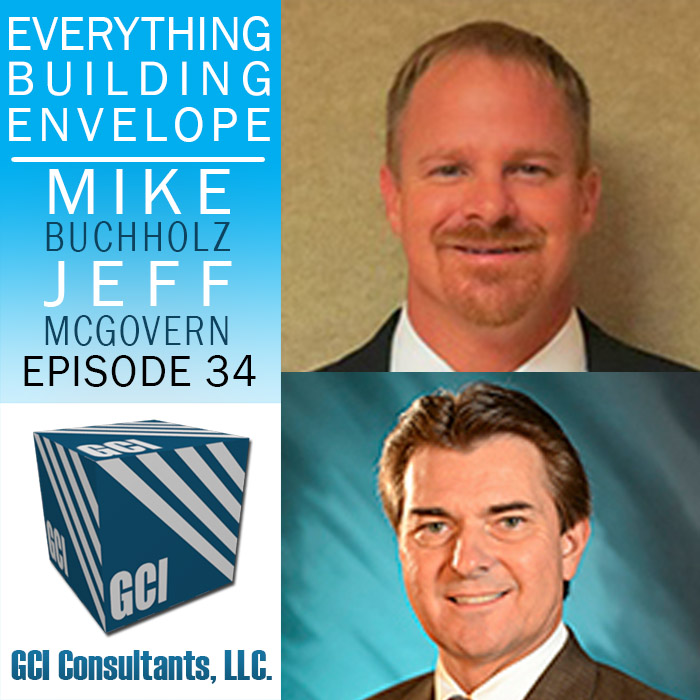
About The Everything Building Envelope Podcast: Everything Building Envelope℠ is a dedicated podcast and video forum for understanding the building envelope. Our podcast series discusses current trends and issues that contractors, developers and building owners have to deal with related to pre and post construction. Our series touches on various topics related to water infiltration, litigation and construction methods related to the building envelope.
https://www.everythingbuildingenvelope.com
*** Subscribe to the show and leave us a Review on ITunes!
Paul: Hello, everyone. This is Paul Beers. Welcome back to the Everything Building Envelope podcast. Today we’re gonna talk about glazing restoration or restoration of glazing systems, and I’ve got Mike Buccholz and Jeff McGovern from Tremco. Mike has already been a guest. Mike, thanks for coming back on.
Mike: Yeah. Thanks for having me, Paul.
Paul: Welcome, Jeff.
Jeff: Thank you. Thanks for having me, Paul.
Paul: So, Mike, why don’t you refresh everybody a little bit about you and Tremco, and maybe you can segue over to introduce Jeff as well.
Mike: Sure, absolutely. So Mike Buccholz. I’m the Southeast regional manager for Tremco Commercial Sealants and Waterproofing. I’ve been with Tremco 14 going on 15 years now. The first six years with Tremco, I was in the fire division, and then we rolled that division into our sealants and waterproofing business where we capture the whole building envelope, so for the last eight years or so, I’ve been on that side of the business. And I think, you know, what really separates Tremco is, and I know this is a bit of a cliché, but it’s our people. And we’re nearly a hundred-year-old company, and we’ve been focused on the commercial glazing, waterproofing, sealants market, for a very long time. Our field support folks have real-world experience as contractors, engineers, or consultants, and glazing is no different.
And I’m pleased to have Jeff McGovern joining us today. Jeff has a strong background, an actual reputation in the glazing industry. He was the director of regional operations with Architectural Testing, Inc., so ATI for four years where he was instrumental in creating impact tests for contracts. Prior to that, he had roughly 30 years working his way up through the corporate ladder with Trainor Glass. And he started in Chicago as a fabricator, then a field glazer, and learned all aspects of the commercial glazing industry, and eventually, relocated down to Florida where he continued to advance his career and become a vice president at Trainor. And while he was at Trainor, he was instrumental in numerous monumental projects in Florida such as the port of Miami, Kravis Center, Jackson’s Health Hospital, Memoirs Children’s Hospital, and a variety of others. And with that, I’ll turn it over to Jeff to speak a little bit more about how Tremco approaches the glazing restoration market.
Jeff: Thanks, Mike, that just made me feel old. Yeah, a lot of years in the glazing industry.
Paul: Welcome to the club.
Jeff: What’s that?
Paul: Welcome to the club.
Jeff: Yeah, exactly. So, yeah, thank you for that, and Paul, again, thanks for having me on here today. I think it’s kind of a very appropriate topic today since we’ve just had Irma kind of go through the state like a snowplow. So…but basically, yeah, as Mike said, I started out in the glazing industry, and when hurricane Andrew went through Florida, it kind of changed the codes. And it turned regular glazing contractors into, not only contractors, but we had to design our own systems. We became manufacturers. So with all of that background, you get a very in-depth involvement in your company and in your products that you make. Then went onto the test lab which I continued to test building products. And then I’ve been at Tremco for three years now. So with that, let’s get started.
Paul: Great. And Jeff, you know, you and I, I can give a me too into everything Mike said. You and I, obviously, have known each other for quite a while. Worked on a lot of different things together over the years, so I’m really excited to have you here to talk about some stuff today. And it’s funny, you know, you mentioned Irma, so we’re recording this, I don’t know when it’ll come out, hopefully soon, but within a, you know, probably a month or so. And Irma was about 10 days ago. What’s really interesting is we’re starting to really hear from clients and customers and whatnot, and big, big, big, thing, in the room, and from what I can tell, Florida is water leakage. I’m getting many, many, many phone calls with that. So, this is a very appropriate subject as far as that goes and… So let’s have at it. So what’s usually a failure mode for glazing systems?
Jeff: One that comes to mind immediately is improper installation, and, you know, there’s a couple of different ways. I mean, a lot of guys know how to install the system from the screws and put the glass in the hole and caulk the parameter, but a lot of integral critical seals are either missed or not followed properly per the manufacturer’s installation instructions, or poor or just not cleaning before applying sealants. So the systems, and we have a plus down here in Florida because we test most of them in the lab and get approval, so they’ve pre-been tested to meet certain design criteria, but if you don’t install them in the field properly, that’s where you typically see glazing failures.
Paul: So, it’s interesting you mentioned the testing, and I know, you know, it’s good that you have experience in the test lab and in the field. So just so that everybody understands, that when a unit is tested in a laboratory, you know, certain things are done to it with sealants and weather stripping and accessories and things like that. What’s supposed to happen when it’s installed in the field? Is it supposed to basically be the same thing or can you have variations? Or what’s the rules there, so to speak?
Jeff: Yeah. Sure. Yeah. It is to be installed per the way that it was tested. There are only a couple different substitutions that could be made, and they’re very minor. Perimeter sealants of a glazing system could be changed, if they’re even labeled on the test report, those items could be…attachment of a curtain wall to a building could be engineered whether it was with structural all angles or imbeds, those could be changed. Outside of that, you’re pretty much gonna follow what was tested. The aluminum that’s used, how it’s steeled, the size of the sealant bead that holds the glass in place, the type of glass that’s in there with the proper inner layer, and the fastening, all right? And along with that, manufacturers, once they get these products tested, should have installation instructions that get reviewed by third-party during the processes. Now, obviously, a lot of that gets missed, and thus results in some sort of failures between water or even structural failures.
Paul: So glazing systems, you know, there’s different kinds of system, and they function a little bit differently, but, you know, they’re all designed a certain way so that they’ll either repel the water or collect it and drain it back to the outside. Well, basically, so that they won’t leak, so why is it important to understand the glazing system before starting to repair it?
Jeff: The most common problems resulting in restoration work, usually, are just adding sealant over everything. And I remember listening to one of your earlier podcasts and you used the word, “Yes, baring silicone over a glazing system just doesn’t work.” You know, so to understand the glazing system, there’s so many different types, and they work in different ways. It’s important to understand how the system takes on water and evacuates water. Most of them are designed to take in water into the system and drain them out.
And, as you know, Paul, most glazing systems in South Florida, certainly before the hurricane impacted us and changed the codes here, were flush glazed storefront center glazed systems. Those systems are meant to have a pan underneath them. The water goes through the system, hits the pan, and evacuates out. A lot of times what happens with those is they put the pan down, and they put a frame in and they blow holes through it to anchor it, so now your pan that you created to hold water, no longer holds water.
So I can remember being in the glass world in my days with storefront framing, and we would almost end up wet sealing all of that product anyway to keep the water out. So kind of a poor design, so to speak, where it takes in water, but then it’s punctured so that it’s hard to seal that up, causes the problem. Understanding the glazing system also lets you to come up with a proper repair. A lot of times just smearing caulk doesn’t do the trick. And I can use an example from Irma of a call I got today of a building that was restorated, meaning it was wet sealed…we’re talking a little bit later on here…was wet sealed, but they didn’t address the horizontal to vertical intersections.
They did field chambers test on this building, and they passed along the way at a prescripted 12 bsf pressure. Well, Irma came, and they have several leaks this morning, and it’s coming through horizontal to vertical connections that they didn’t address. So there is a scenario where they possibly didn’t understand the glazing system or how it worked.
Paul: So, yeah, the storefront systems that you were talking about, you know, I always said they were designed to leak. And like you say, if you don’t understand how they’re supposed to capture all the water that gets in and gets it back out, it’s gonna be really difficult to repair it. So what’s the best way to determine what or how a glazing system is leaking?
Jeff: Well, AAMA has two field prescriptive tests. Both of them will expose leaks usually if there are. And one of them is AAMA 501.2 which is your nozzle, spray nozzle test. And then there’s AAMA 502 which is a chamber where you draw a negative pressure and putting a spray rack outside. I’m pretty sure that GCI does both, and I’d kind of throw this back at you, Paul, is, what would you guys do when you get one of those calls of a building leak? How would you determine what to do as far as figuring out where the water is coming from?
Paul: Yeah, and also, every situation is different. What we try to do, you know, first at GCI Consultants when we…when a leak, which we’re gonna be doing a lot of apparently after Irma, I know what we like to do first is just try and understand the service history of the buildings where we go out, and we meet with the people that are in the building or the maintenance people or the manager, I mean, the property manager, and hear their story. You know, water is coming here. It’s dripping out of this. It’s on the floor or whatever it is. And then we try to, as you say, understand what kind of system is in the building and how it’s supposed to work.
And then, you know, oftentimes, we go into either, well, a combination of destructive analysis. So that might be removing interior drywall so we can see really if the water is coming through the window or bottom of it or coming around it or whatever. And then there’s various ways to test it. We don’t really like the hose test. We like to use the AAMA 502, or also, ASTM E 1105 which Will Smith and I, Will works with me at GCI. We did an earlier podcast on that.
And basically there, you create the conditions of a wind-driven rainstorm so you can see what’s going on. Recreate the conditions that cause it to leak. Whereas water hose, you know, that doesn’t have the wind, so sometimes that’s, you know, maybe wouldn’t give you the same results, so we like to do that. And then once you see what’s going on, that’s when you guys can figure out, and you guys can help us figure out exactly, what’s a good way to fix it. What’s Tremco’s restoration approach with glazing systems?
Jeff: Well, the first thing to understand is, you know, we have a full line of glazing system products. Just from the initial design with glazing systems, designing gaskets, steels, internal, not only do we help with the engineering and design of that, but we manufacture those products. So we’ve kind of got a leg up, so to speak, where we’re helping in design but we also manufacture it, so we can help change the design to make it better for air and water infiltration.
As far as the restoration, we also make a whole line of those types of products. There is system overlay, silicone overlays that we can put over failed exterior systems. There is, obviously, we make silicone sealants to do the wet glazing. We make fixtured gaskets, so any type of custom gasket that would need to be replaced, we can do. And, you know, there’s also a product called Simple Seal which is extruded silicone sheet that can be used as overlays. So Tremco has all of those types of products to help the initial design of the system, and if there was repair needing to be done afterwards.
Paul: So you mentioned wet sealing, and I’ll say this, that half the buildings in America at this point have been wet sealed or more. It’s like, you know, any building that’s any kind of aged to it has probably had some sort of sealant application to, you know, stop leakage problems that either were earlier on or developed over time. And, you know, typically like on a commercial glazing system, they would cut back the gasket between the glass and the metal, and then shoot a bead of silicone around the perimeter of the frame. So that’s, I’m guessing you’re gonna say, that’s probably not the best way to do it. And what’s wrong with that? And, so why not? I guess is what I would say.
Jeff: Right, and yeah, I would say that that’s not the best. I would say that’s part of the approach of fixing or a restoration of a leaking system. The problem with the wet seal alone is if you did understand the glazing system, like you should before you get started with this, you’re gonna know that there’s other places for water to get in other than that glass to aluminum frame connection.
So you have intermediate to horizontal connections all over it, you also have silipans, possibly, that are involved. So you have to look at those also. Because once you “wet seal” you’re sorta all in. In other words, if you partially seal the system, you might actually make things worse. Where now, you’ve might have stopped some water from a location but let it in, and it’s still going to leak with, like I said earlier, maybe the internal seals were never done. So by wet sealing the glass to the aluminum, you’ll stop some of that, but you won’t attack all of the problems. So addressing all of the issues comes into play when you wet seal.
Paul: I love the way you just said, “Once you start you’re all in.” I mean, I agree completely. It’s really a good way to put it. There’s no halfway there wet seal, is there?
Jeff: No. And Paul, as I just said earlier. I mean, I was on a call earlier today of a building that they spent a lot of money restorating, it did not include attacking the horizontal to vertical joints, and it’s a building that’s, well before the HVHZ came into effect,.So it’s a stick-built system where the horizontal, the verticals, literally, let airflow through. So, you know, now, you’ve got a scenario where the perimeter of the building was redone. They’ve cap beaded or wet sealed from the glass to the aluminum. That was well and good, but the water actually just came through a horizontal to vertical connection. So by just cutting off the head of the gasket and shooting a bead around it, which we’d seen… I bet you, Paul, we probably see that a third of the time on projects if not more. That’s gonna help, but it’s not gonna solve your problems totally.
Paul: Yeah. If you’re gonna wet seal, you need to, obviously, seal everything. So you mentioned some of the products and materials that Tremco has that help with this, and could you maybe just kind of run through that? Like what you were just talking about with the metal to metal joints that weren’t sealed? Now, I know that you don’t… Can you just smear caulk over that joint, and would that work? Or is there a better way to do it?
Jeff: Yeah, right. There’s better ways to do that. A lot of times that gasket which becomes older, dry, brittle, cracking. The other big problems with it is it shortens up as it gets to the ends or the corners of the glass, and usually, that’s because guys stretched it when they rolled it in during the installation. So it will shorten up. Sometimes you could see it’s several inches shorted up. So obviously, the gasket that’s supposed to keep the water out is now got a big hole there to take it in.
So by just cutting off the head and caulking over it, you may be, a gasket that’s left inside, may just fall out, and there may be no compression from the aluminum to the glass. So we make a product called headless wedge which allows you to remove that gasket, and insert this new gasket that will be recessed for you to allow…allow you to put in a proper wet sealed bead joint structure. A lot of times with those top loaded gaskets that go into window systems, they are very large in size. So to completely cover them with just a wet seal, you would need to have a very large bead of sealant. And it’s just not the proper joint structure. So the headless wedge with the combination of a wet seal silicon usually will take care of that component of the system.
Paul: So we seal the glass to the metal, but I’ve seen that headless wedge. And it’s really cool because it gives you, you know, basically, it gives you a real nice looking sealant joint or a sealant joint profile. And so that seal does a nice job with the glass to the metal connections. What about when you get to the frame joints and what not where they come together, what’s the technique for sealing them?
Jeff: Sure, Paul. Tremco makes…we call them cruciforms which are actually are extruded punched out silicone shapes that would go over the whole intersection. Whether it was a four-way intersection, two-way, three-way, whatever the case may be, they’re made of silicone. They would be installed over the metal to metal joint before you did the wet seal so that you could tie the wet seal into it. The typical field approach to handling a horizontal to vertical intersection is usually just smearing a thin bead of silicon over it. And we all know that a bead of silicone, that’s a 16th to an 8th inch thick, that’s been smeared over a joint that has movement capabilities, does not perform very well at all. So these cruciforms allow you to cover up the intersections. They’re neat. They’re clean. They can be made to any color that you want because they’re made out of silicon. And it covers that intersection up and protects from the water to get it.
Paul: I love those things, by the way. We use them whenever we can and that they’re very effective. Because you can seal all those joints with regular sealant which involves a very, very high, you know, involves some bond breaker tape and a very high degree of workmanship. And that’s when it all comes apart with the workmanship. So would you say that’s another big advantage of the extruded silicone is that it’s easy to put on?
Jeff: Yeah, absolutely. And, you know, the cost involved in them outweighs the labor that you have to do to make a decent bridge of that gap. Like you said, if you build it up and put bond breaker under it, and to really make that look good, it does take a lot of work which takes time. So, you know, when you look at a cost of a cruciform, you know, you may think, “Well, a couple of dollars for each intersection, that adds up,” but however, the labor savings, and ultimately, the longevity of it, is going to be there.
Paul: It’s gonna work, too.
Jeff: It’s gonna work. You’re correct.
Paul: So let’s say I have a restoration job and it’s a big barrel skylight, and, you know, the aluminum’s all pitted and they’ve been chasing leaks around it since the day it was installed and trying to figure out if it should be replaced at this point or, you know, caulk it for the 10th time in a row. What to do with…? Using some of your materials, the headless wedge and some of the other parts and pieces, would that be a good alternative to try and actually fix it?
Jeff: Sure. Now, one thing and I know, Paul, you guys have been out on leaking skylight projects. What’s interesting about skylights is they become the catch-all of silicone and who knows what they squirt on them, but because most people can’t see them from the outside, there has been several renditions of trying to seal them up. And, you know, they’re just piling more sealant on top of more sealant isn’t usually the fix. So, yeah, the headless wedge works well with the, you know, the metal cover or cap to the glass, that would solve that problem pretty well.
Again, you’ll have to address the intersections which the cruciforms would definitely help you out there. And then also addressing, you know, the perimeter. I see a lot of skylights that, you know, they, you know, sometimes the only perimeter is the seal along a gutter or up against the wall. A lot of times that connection is a bad one. It needs to be looked at, and again, and like we said earlier, once you start wet sealing you better understand the whole system, especially, skylights that are made to take down water and run down a rafter and weep out at the bottom.
If you don’t address all of those problems, you could have a bigger buildup that you’ll seal and have more water in some cases. But the same thing goes true with [inaudible 00:23:30] and the skylight is a vertical glazed system, we, you know, we make the headless wedge. We make the sealants. We make cruciforms. We also make restoration overlay shapes, where we can extrude a silicon cap that could cover the entire metal system that could be detailed at the intersections, again, it’s all silicone, so it’ll stick with silicone sealant. It will also, as you said, this skylight could be pitted, damaged, paint needs to be redone, this could be extruded in a color that, now you have a new look finish on the outside of that skylight.
Paul: That is really cool. I never actually thought about that. Just to cover, you know, basically, using fitted shapes to cover the exterior because as you say, those things can be an epic mess by the time that, you know, renegade, or our maintenance guys up on the roof with different colors of caulk they bought at Home Depot or whatever. And, you know, a lot of times, skylights are invisible, but also, a lot of times they’re not. You know, it may be like the entrance to a building when everybody looks up the window above and can see them. So, you know, appearance is important, and that’s really slckk the concept of encapsulating it, basically. Is that what we’re talking about?
Jeff: Yeah. And Paul another thing on that, and in working either a glazing contractor or a caulk and waterproofing company who might do this work, they also say the same things. They spend most of their time cleaning off the stuff that’s been put there for years than they do actually fixing the problem once they have the right products and design in place.
Paul: That’s the same thing we do when we investigate. You know, sometimes you gotta get all this gook off before you can even start to figure, you know, and run a test on a mock up or a repair that’s got so much crud on it, you can’t get anything accomplished. You’ve gotta basically get it cleaned off before you can even start to address the issues. So doing a, you know, like fixing the skylight, any idea the ballpark cost of using Tremco’s approach versus putting in, you know, a new window or a new skylight?
Jeff: Yeah. Going back a few years from my estimating times at the glass company, but I can tell you that most glazing systems, even just take a fixed glazing system for a commercial building, you’re probably looking at the, you know, 80 to $100 a square foot cost for, you know, just that impact system and the installation. And that’s not including, Paul, any permits, any engineering, maybe some of the perimeter structure isn’t sufficient to attach new stuff into, so that needs to be looked at as a cost.
You also have a disruption with tenants, obviously, tearing out and replacing, so there’s relocation of people for a day or two or depending on the scope of the job. So, you know, you’re probably looking at 100 bucks a foot. So if you took just a 16 square-foot opening, a 4 foot by 4 foot, you know, you’re at 1,600 bucks just to put in a glazing system there. Not including all the other stuff I’m talking about. With Tremco, you’re probably looking at, I mean, if you got 32 lineal feet of repair to do around that window, whether it’s glass or metal and then perimeter, you’re probably looking at a third of the cost for doing that depending on what you did to cover it up. But certainly, the cost of a new glazing system far outweighs restoration work.
Paul: Yeah. And, you know and I think one thing you mentioned that’s really key is the disruption to the people in the building. That’s a, you know, there’s not just a dollar cost, there’s, I guess, I don’t know if I’d call it an opportunity cost or a headache of going through this and, you know, introducing all the protection you’ve gotta do and putting people on notice, the inconvenience. Like, you know, if you’re a office building owner, then you’re gonna have a, you know, you can possibly have angry or displaced tenants. So what we find is, anytime you can leave something in place and fix it, it, you know, from a cost perspective and from a logistics perspective, that almost, without question, always goes better to be able to repair rather than replace.
Jeff: All right. And, you know, working hand-in-hand, Tremco and usually, these types of projects involve companies like yourself, GCI as consulting, we can put together a package up front. We can do this to metals. We can show the testing that needs to be done if you’re using all of Tremco’s products. Now, you’ve got a single source, tested, warranted manufacturer to back up what we’re going to do, which eases the pain on a building owner, right? Where even if you tear it out and put something new in, there’s several players involved to getting that work done. And your warranty may not be as good as a restoration where you can get a single source out of it. So that’s just something to think about.
Paul: Yeah. And you know, Mike, when we did the last episode, we talked about the single source being such an advantage. And I know maybe the restoration may go beyond the glazing system, and then Tremco’s got a variety of products that will work for any surrounding or adjacent surfaces as well. Isn’t that right?
Mike: That’s correct. Yeah, we’ve got a full array of flushing systems that we can tie into here. And, you know, one of the things that I wanna make sure that I mention is the fact that all the concepts and the products and the systems and the approach that you guys have been speaking to, these aren’t just concepts. These are proven, tested, warrantable, defensible systems that we’re installing. And we’re writing fleet free warranties on these systems for up to 20 years. So it really comes with a bang for the bucks and really great systems.
Paul: Yeah. And a big benefit out of, obviously, like we’re talking about, doing it the right way, aside from just going out there and blindly applying material all over the place and then waiting for the next rainstorm to hope that it worked, which, usually, it doesn’t.
Mike: Yeah. I know. That’s correct. You know, we’re looking at coming up with a full system to conquer this restoration project. We work with consultants such as yourself, to make sure that as we’re reinstalling them we test the samples of the windows so that we can confirm that we’re getting the performance that we anticipate out of the prescribed system. And then that comes with a warranty, obviously.
Paul: Yeah, you know, the testing is good for everybody because then you know if it’s working. And then maybe if something isn’t completely doing what you’d hoped it would, it gives you a chance to figure it out, adjust it, and get it right before you do the whole rest of the building.
Mike: Absolutely.
Paul: So Tremco, I know has a lot of resources available as far as, you know, not only the materials, but, you know, how to use…how to best use them and specifications, and I’m guessing, details and things like that. Could you guys talk about that just a little bit about… If people are interested, you know, how do they get more information and what resources are available?
Mike: Sure, absolutely. You can access a lot of this information through our website which is www.tremcosealants.com. And we’ve got a full array of the information that we’ve provided as well. As you can get on there and you can see some videos of projects that we’ve actually done this overlay type systems with. And one specifically, for the Puerto Rico Convention Center, where we did a full overlay system on a convention center there. Where they had a giant skylight that had been leaking since they installed it, and you can see how we tackled that one.
But you can find more information there. Another way is we’ve got a rep locator on there where you can get in touch with Jeff McGovern who obviously, specializes in our glazing business. And we have other manufacturer representatives that can provide technical, local technical support, and they can be found through that website. And similar to Jeff, most of our folks have a lot of real-world experience that they can pull from and help with…helping you figure out, exactly, what warranty tested systems need to be prescribed for your project.
Paul: Yeah. Well, you know, Jeff said at the beginning, really good stuff. Very appropo with hurricane Irma having affected Florida and points beyond here in the last week or so. And I think, you know, there’s going to be a lot of demand for this with all the water leakage that we’re hearing about. So, Jeff, thank you very much for sharing your wisdom with us.
Jeff: Thank you, Paul, and I look forward to seeing you on the next one, I’m sure.
Paul: Yup, there will be a next one, I’m afraid. And, Mike, thanks so much for adding your insight and helping us get this all put together.
Mike: Yeah, absolutely. Thanks, Paul. I appreciate the opportunity.
Paul: So, thank you, everyone, for listening to the Everything Building Envelope podcast. Really interesting topic today. And again, I think it’s really apropos with what we’ve been reading about with all the storms of late, and so, please tell your friends about it.
We have a website where you can access information www.everythingbuildingenvelope.com. You can also subscribe on iTunes or Stitcher. And as we talked about, as to what the hurricane topic thing as relevant as it is, there are a lot of resources on our company website talking about hurricanes and hurricane recovery at www.gciconsultants.com So until next time, this is Paul Beers saying, thank you for listening, and so long.