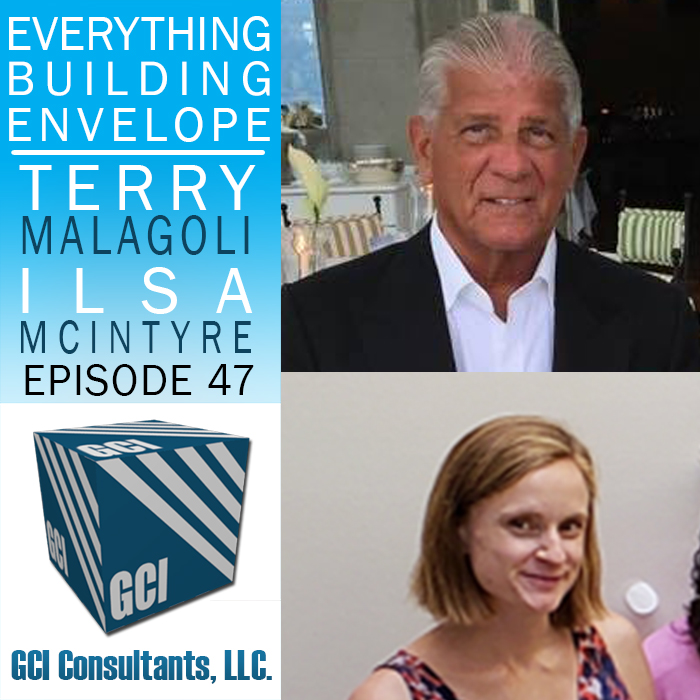
About The Everything Building Envelope Podcast: Everything Building Envelope℠ is a dedicated podcast and video forum for understanding the building envelope. Our podcast series discusses current trends and issues that contractors, developers and building owners have to deal with related to pre and post construction. Our series touches on various topics related to water infiltration, litigation and construction methods related to the building envelope.
https://www.everythingbuildingenvelope.com
*** Subscribe to the show and leave us a Review on ITunes!
Chris Matthews: Welcome to the Everything Building Envelope Podcast. I’m Chris Matthews, Vice President of GCI Consultants, and I’ll be your host of the podcast today. I’m very excited today to introduce our guests, Terry Malagoli and Ilsa McIntyre of Infrared Testing, Inc. based in Chicago. They’re gonna talk to us today about all the exciting activities and current events related to Infrared Testing in the construction industry and beyond. Welcome, guys.
Ilsa McIntyre: Great, thanks for having us.
Terry Malagoli: Good morning, thank you. Uh, my name is Terry Malagoli, I’m the, um, Founder and CEO of the company. I started this company in 1990 and, uh, from a fledgling little seed and today we’re a multi-million-dollar corporation and we, um, are a global company working all over the world. We have in Chicago 14 people in our office and we have 18 people in the field. Uh, they’re scattered across the country from California to Florida to New York. We have a team that actually, uh, travels outside of the country for us on a constant basis and we’ll do inspection in China, India, Europe, Australia, and pretty much what we cover.
Chris Matthews: Interesting, great. All right, so, let’s talk some about how your work interacts with the building envelope and maybe some areas beyond. So, what is the role of infrared and envelope inspections related to building commissioning, for verifying new construction and reducing liability?
Ilsa McIntyre: Well, infrared is really sort of an essential part of the toolbox for building commissioning, and building commissioning is getting to be, uh, a much bigger thing especially as states and companies and governments are focusing on going green initiatives. Uh, more states like California with California’s Cal Green Code are starting to require building commissioning for all new, uh, larger, non-residential projects. Um, it’s also essential for, uh, things like lead certification and what building commissioning is, is it’s a full sort of top-to-bottom systems check quality assurance process that compares the design and functionality of the building. It assesses the new construction prior to occupancy and sort of top-to-bottom the building envelope and then inside all functioning of the systems, and where infrared comes into play in this is both from an electrical, uh, standpoint as well as a building structural standpoint, the envelope of the building and the roof.
Chris Matthews: Oh, I was just gonna add that, and we’ve been involved with that at GCI, not from the in-, the infrared standpoint, but doing some of the envelope commissioning work related to other types of testing and assessment of the system. So, I’m familiar with that as well.
Ilsa McIntyre: Exactly, exactly, and, you know, not just new constructions actually, it’s getting to be a thing for recommissioning as these, uh, historical buildings are redeveloped for additional uses to sort of convert the building to its new uses, and we go in and check everything with that as well. I don’t know if you’re familiar with continuous commissioning which, I guess, has been developed out of Texas A&M University. Sort of as buildings are, you know, becoming more technological they developed a system to sort of quantify energy use to continually increase not just as the building was being built and redeveloped but sort of re-evaluate continuously the increased efficiency in building operations –
Chris Matthews: Nice, yeah.
Ilsa McIntyre: – whereas the initial commissioning and sort of recommissioning focuses on verifying design, uh, continuous commissioning looks at the total overall efficiency, especially with the subsystems, you know, and the new technology you have the IOT connecting all your equipment and, uh, thermal imaging really compliments this technology to pinpoint problem areas with further precision.
Chris Matthews: Great, yeah, very interesting. So, how does the infrared envelope testing add value to green initiatives saving programs, I think you were kind of touching on that.
Ilsa McIntyre: Yes, so, again, you know, it, it’s necessary for things such as lead certification but the building envelope inspection from an infrared standpoint really came into use in the 70s and 80s, and this was a time, um, where they really saw fuel price increases, and so it became necessary both from mostly a cost standpoint to make sure that you’re not leaching energy out of your building, you know, from air leakage, from improper window sealings, you know, from roof problems, and, you know, they estimate that excessive leakage from problem areas can as much as double energy use. So, the energy systems lab, again at Texas A&M University in developing their continuous commissioning systems, estimated that as much as up to really like a fifth of energy consumed in an average commercial building is waste and caused by poorly operating systems. So, uh, the infrared standpoint is to try and reduce that energy, both leaching out of the building envelope, and then from an electrical standpoint leaching out of the electrical system.
Chris Matthews: Right, and I see that from my work in the building envelope, you know, that that airflow through the walls is something that wasn’t always looked at historically, but now as you say, everyone’s realizing that this seals and airflow are costing people a lot of money –
Ilsa McIntyre: Oh definitely.
Chris Matthews: – over the long term.
Ilsa McIntyre: I can see it even in the, in my building. I live in sort of a converted, it was a clothing manufacturer actually. The building was built around 1900. They converted it to lofts in the 1990s and this was before sort of, you know, retrofitted all this, this, these building parts and now we’re sort of having leakage out of the window sealings and around the outer part of the masonry, and I think that our heating bill for the last month, especially with how cold it’s been in Chicago, has been over $200.00 just for the month. So, we’re certainly feeling that as well.
Chris Matthews: Yeah.
Ilsa McIntyre: We need an infrared inspection **** building.
Chris Matthews: Yeah, there, there is a real world example of how it affects you right there. So, how does the IR imaging, uh, kind of related more to the work that I’m familiar with, how does it detect failing window seals, faulty or missing insulation, um, things that might be invi-, invisible to the naked eye in an inspection?
Ilsa McIntyre: Sure, sure, so, what we’ll do, um, a lot of times we get called up from clients who think that they have a problems somewhere but they’re not sure or, you know, sort of like I said with my building, they, you know, just are encountering, like, massively expensive utility bills, and so, they’ll call us up and we’ll come up and set up the building to an inspection. Um, what we want to do is we create a negative pressure inside the building by altering the HVAC system. We want to make it either, you know, if it’s cold outside and we’re doing the inspection in winter, to raise up the heat in the building to make it quite hot or vice versa in the summer, and that way what we’re looking for is it can be anything from faults in insulation, interior air sealing, and faults in the moisture retardation systems. Each type of insulation has a characteristic thermal pattern, something like, you know, with an injected foam insulation, what we’re looking for is sort of that cracking and shrinking. Um, it can be from poor installation from the get go, and we see faults in, you know, brand-new buildings, and again, that’s sort of what we’re looking for from the commissioning standpoint, and then certainly in older buildings as these insulation systems start to wear down as moisture starts to get into, um, you know, the moisture retardation system starts to fail, that’s when we really see it.
Chris Matthews: I had some experience with a similar project. It was a hospital building with a large curtain wall, and they had done some infrared testing that was indicating, it was in Florida, it was a warm climate –
Ilsa McIntyre: Right, yes, humid.
Chris Matthews: – and, right, and they were, they, they had concerns about air leakage through the curtain wall and had done infrared testing and identified some, I guess, localized problem areas within the curtain wall, and then we were able to use that information in the, uh, report from the, from the thermographer to go to those specific areas and identify what the problems were and help them to resolve those, because luckily for, in this case, it wasn’t a systemic thing that was throughout, it was more isolated locations, but the infrared was great for, you know –
Ilsa McIntyre: Exactly.
Chris Matthews: – you’ve got problems in these ten areas, and then enabling us as the experts to go up and put our eyes on it and figure out what was going wrong rather than looking at this 40,000 square feet of curtain wall inch by inch and trying to, trying to –
Ilsa McIntyre: Exactly, right.
Chris Matthews: – figure out e-, even if there’s a problem, you know, so.
Ilsa McIntyre: Right.
Chris Matthews: Yeah.
Ilsa McIntyre: And, yes, the infrared testing, you know, in the end once we do pinpoint the problems, obviously we’ll have to sort of get into the walls to, for corrective measures, but this way, um, it can be sort of a good way to estimate costs before you get involved and commit, overly commit to a larger project than needed, but the infrared really, a lot of times we get calls from clients who think they have a problem or what they think is actually, uh, a water leakage problem in their building is really, as you said, an air leakage problem, and the air –
Chris Matthews: Mm hmm.
Ilsa McIntyre: – as it’s coming into the building, especially in more humid clients, climates, hits, uh, you know, a certain material that it leads to condensation and that’s where you’re starting to have the moisture build up rather than moisture coming in directly into the building, and that can be sort of hard to, to ascertain and guess on, especially, um, if the problem is going through, you know, an indirect pathway such as through, you know, anything like a plumbing chase, an interior wall, rather than coming in directly through, you know, a failed window seal.
Chris Matthews: Right, and isn’t that usually the, that the IR is kinda, well, at least in the envelope, in the work that I’ve done, that the IR is kind of the first step in identifying here are your problem areas, and then usually you need to go in, like in the case that I had mentioned, then you’re gonna go in with some more in-depth visual analysis, or maybe some destructive testing or something to figure out –
Ilsa McIntyre: Exactly.
Chris Matthews: – okay, here’s the problem area, and then what are we gonna do to confirm and come up with some, with some solution. Is that kinda you guys’ approach, uh, when it comes to the envelope?
Ilsa McIntyre: Exactly. It’s a, it’s a good first step from the envelope, also with problems with roof systems. Rather than, you know, literally tearing your building apart, removing wall-, all the interior/exterior walls to sort of get the lay of the land of, you know, I know I have a problem on the roof. Again, you know, the moisture being **** referred from somewhere else, so, you know, I don’t really know how much of the roof is damaged, and with the, the infrared scan we can sort of give you an idea is it 10 percent of the roof, is it 2 percent of the roof, is it really just a couple of problem areas, or is it better just to replace the entire roof?
Chris Matthews: Right, and, and you guys had mentioned that you’re getting heavily into the drone, um, type inspections when we were talking before the podcast. I would think that the drones are very useful for the roof inspections in a lot of, a lot of situations.
Ilsa McIntyre: Oh yes. For the roof as well as the envelope it’s really sort of revolutionized what we do, and we’re just very excited that our drone division is, is really taking off, literally, and, uh, both literally and, um, physically. So, what we do is, especially in the urban areas, we have certified drone pilots now and we, um, and they make drones that are outfitted with thermal cameras, and instead of the way we used to do these inspections, um, especially for the high-rise buildings, you’d have to find a series of buildings nearby and have people strategically located on various roofs. You’re sort of, like, becoming, like, Spiderman, having to jump from roof to roof just to get good angles and views of the entire building, and now –
Chris Matthews: Mm hmm.
Ilsa McIntyre: – with the drones we really get that full 360-degree view, um, especially just, you know, if there is various overhangs of buildings or multiple roofing types, um, we can really jus get in and see every corner.
Chris Matthews: Yep, right, great, and the, and we have used probably, certainly not to the level of expertise that, that you guys have, but we, with some of that similar stuff with IR in looking at roofs where people believe they have a problem, I’m trying to find where there may be some moisture, and then typically doing some, same as I was talking about earlier, confirmation testing where we do some core samples or something to find, okay, is there actually moisture under there, um –
Ilsa McIntyre: Yes, exactly.
Chris Matthews: – but a great tool to either indicate areas where there may be a problem or rule them out either way.
Ilsa McIntyre: Exactly –
Chris Matthews: Um –
Ilsa McIntyre: – before you even have to get to the destructive core sampling.
Chris Matthews: Exactly. You don’t, you don’t want to do, you don’t want to punch anymore holes into the roof than you have to, so.
Ilsa McIntyre: Exactly.
Chris Matthews: Um, so, back to the energy issues, how much can energy loss disrupt building heating and cooling distribution, and how does that impact utility costs?
Ilsa McIntyre: Right, so, like I said, you know, and that has sort of been quantified as the with Texas A&M and their continuous commissioning and saying that, you know, 20 percent of energy consumed in a building can be wasted. So, you know, that’s just sort of money that’s being thrown away, but even going beyond that, you know, you’re sort of decreasing the longevity of every system in your building by having this energy leach out. Right from the start, you know, things like building commissioning can find HVAC systems that are sort of hampered by design problems, by insulation problems, that result in either extensive energy use and just, you know, things like uncomfortable buildings for the inhabitants, and then, you know, as you get to have the problems with air coming into your building, building up moisture, you’re, you know, leading to things such as, you know, the sick building syndrome that your workers are just becoming physically sick from things like mold problems.
Chris Matthews: Right, right, exactly, and that, and that obviously we deal with that a lot from the water side as well.
Ilsa McIntyre: Exactly. Yes, you know, excessive energy consumption can increase your utility costs, but, you know, if you attach onto that the indirect costs of, you know, if your water pipes are freezing up, you’re having issues with your fire sprinkler systems, again, you know, problems caused by mold, by condensation, the water intrusion, um, and then you’re, you know, of course opening yourself up to, um, liability from the building inhabitants.
Chris Matthews: Sure yeah, yeah, the whole sick building thing that you mentioned. So, how can the IR testing, um, be used to evaluate current masonry conditions and control costs on repairs?
Ilsa McIntyre: Sort of like we were talking about with the roof inspection. Um, the envelope it works the same way. Um, we really go in for the client’s both, um, if they think they’re having a problem with **** we recommend, um, doing every couple of years and it’s starting to get codified, I think Chicago is starting to pass some laws that they require, um, masonry inspections, um, every, Terry, can you help me out, is it –
Terry Malagoli: Two years.
Ilsa McIntyre: – every year, every couple of years?
Terry Malagoli: Yeah, it’s every, every 2 years.
Ilsa McIntyre: So, this is something that we go in and, um, with the drone again it’s really simplified and, um, beautified, honestly, the whole process that we can get these, these beautiful views of the entire structures of the out-, of the building, and also a really helpful study of trying to get a baseline condition of what, how, you know, how much of an undertaking is this masonry repair project? Do we sort of have to go in and redo the whole thing or is it just some spot, spot repairs.
Chris Matthews: Right, and I’m familiar with those requirements. A lot of the big municipal areas in the, um, now, you know, we have, we’ve got aging buildings and this is a, a huge concern is that the –
Ilsa McIntyre: Exactly.
Chris Matthews: – masonry facades, um, are not going to last forever, and –
Ilsa McIntyre: Exactly.
Chris Matthews: – um, you know, you’ve got to assess ’em. You don’t want to wait till things start falling off the building.
Ilsa McIntyre: Exactly. So, its’ both from an inner standpoint, it’s not an option to ignore. You have air and moisture coming into the building which creates problems inside, as we’ve already gone over, but outside as you just said, you can have, you know, serious injuries caused by, you know, falling masonry, falling tile from the outside of a building and, you know, you’re opening yourself up to a huge amount of liability from that.
Chris Matthews: Sure, yeah, right, right. Well, lots of areas that the, that the IR is useful. Um, some I’ve had experience with and, and certainly some, even in the envelope that I’m really familiar with and some areas that I wouldn’t have had thought about at first. You guys had also mentioned, I think it’s kind of interesting for our audience, some of the work you’re doing related to inspections of power grids and how, and wildfire risk, those types of things. Can you talk about that a little bit?
Ilsa McIntyre: Sure, sure, yes. This is something that we’re really excited about, especially with our drones and, and energy savings and going green. Um, something that’s really on people’s mind a lot, um, from an electric standpoint is with the wildfires out in California, um, how much of that can be caused by problems in the transmission distribution lines, and what we could do now, and we have been doing for large companies is going through and inspecting miles and miles of overhead and transmission lines for false, uh, using our thermal drones, before they contribute to things such as wildfires and, um, are obviously very destructive, um, to property and to, um, to people.
Chris Matthews: Right, yeah, very interesting, yeah, another application that, uh, obviously is, is very important, uh –
Ilsa McIntyre: Exactly.
Chris Matthews: – we’ve seen it, seen it in the news a lot recently for sure.
Ilsa McIntyre: Yes, and getting back to sort of the, the spot, isolating hot spots before they lead to bigger problems. Obviously it’s something that before it leads to, you know, the bankruptcy of a company or, you know, such as PG&E –
Chris Matthews: Right.
Ilsa McIntyre: – it’s something such as, you know, repairing, you know, certain cutouts before they, you know, take down the entire system.
Chris Matthews: Yes, well worth the investment to get someone like you out there to test these before it’s a much bigger problem. Well, great, I really appreciate you guys joining us today. Why don’t you tell our audience how to reach you and talk to you further if they have questions or, or need your assistance.
Ilsa McIntyre: Thanks, Chris, it’s been a real pleasure. We have a website. We’re just at www.infraredtesting.com. Happy to reach out, we have some really cool samples of all our drone studies, uh, electrical, building envelope, roof, roof inspections. We’re happy to speak with anyone and, um, discuss services in further detail.
Chris Matthews: Great, thank you.
Terry Malagoli: Want to give ’em our phone number?
Ilsa McIntyre: Yes, and our phone, we can be reached also by phone at 312-670-5005.
Chris Matthews: All right, thank you, that, uh, concludes this podcast. We will be talking to our audience again soon.
Ilsa McIntyre: Thanks, Chris.
Terry Malagoli: Thank you very much for the opportunity.