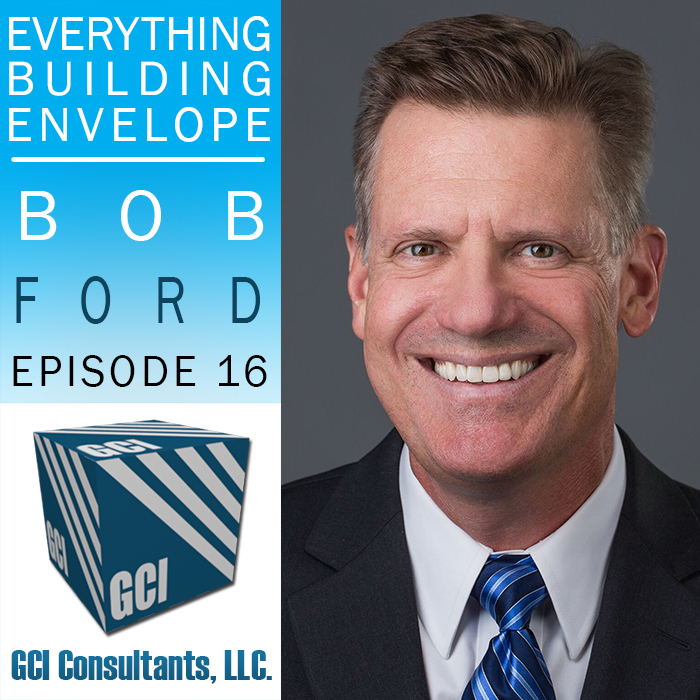
About The Everything Building Envelope Podcast: Everything Building Envelope℠ is a dedicated podcast and video forum for understanding the building envelope. Our podcast series discusses current trends and issues that contractors, developers and building owners have to deal with related to pre and post construction. Our series touches on various topics related to water infiltration, litigation and construction methods related to the building envelope.
https://www.everythingbuildingenvelope.com
*** Subscribe to the show and leave us a Review on ITunes!
The Everything Building Envelope Episode Transcript:
Paul Beers: Today we have as our guest Bob Ford, with Eastman Chemical Company. Bob, thanks for coming on today.
Bob Ford: Well, Paul, thank you for having me, it’s a pleasure to talk to you this morning.
Paul Beers: So you’re with the Advanced and Material Interlayers, is that right?
Bob Ford: Correct I am with the AMI group with Eastman Chemical, and basically what that is, Paul, is at the interlayer division of Eastman. Eastman acquired Solutia, which many of our listeners may recognize as a brand name of PVB, back a few years ago, and so we now are owned by our parent company, Eastman, and I’m with the interlayer division.
Paul Beers: And what we’re going to be talking about today, is laminated glass.
Bob Ford: That’s correct. Several applications we’ll go into and obviously our podcast here is more architecturally oriented, so that would be the focus.
Paul Beers: Yeah, so, when I have people asking me like customers or lay people, whatever, about laminated glass, I always say, hey, you know, it’s the stuff that’s in your car windshield, basically.
Bob Ford: Hey, you’re exactly right.
Paul Beers: And then they get it.
Bob Ford: A lot of the applications we have within the automotive market has actually moved beyond the windshield, and we can touch on that here this morning.
Paul Beers: Okay, yeah, that is interesting. So, before we go onto that, won’t you just tell the audience a little bit about who you are, and then, you know, a little bit about yourself?
Bob Ford: Yeah, so I’ve been in the glass industry a little over 15 years. I’ve worked for both the fabricator side of the market, with inter-pane glass back in the early 2000s, and most recently with Viracon, where I was their North Florida and Alabama architectural rep about the last 6½ years. But Viracon’s certainly one of Eastman’s biggest customers, as are Oldcastle and Trulight, and other glazing fabricators within the United States. So within Eastman, as I mentioned I’m in their advanced materials division, and I handle accounts on the East Coast of the United States and Canada. I basically work with the laminators to help them use our products more efficiently and get them into market.
Paul Beers: Great. Now let’s just jump right into laminated glass. We talked about this a little bit, but let’s just kind of talk about it, you know, go, go back and just run through the basics so that the listeners are on the same page with us. So, what is laminated glass, and, and how is it made?
Bob Ford: So, laminated glass is a composite material that consists of two or more layers of float glass. They can be various thicknesses, eighth-inch all the way up to half-inch wide, and then the interlayer acts as the glue or the sandwich in between the layers to form a cohesive unit. So the process basically starts with laying up two or more lites of glass with an interlayer in between them and that interlayer can be PVB, or it can be ionoplast, or it can be glass-clad polycarbonate laid up in between the lites of the glass. It is then run through an oven and a nip roller which heats the glass to about 160 degrees, and then compresses it through the nip roller somewhere between 80 and 110 psi. So once the glass unit comes through the nip and the oven process, it’s then placed in an autoclave, where it’s in there for about 3 hours. There’s about an hour of ramp-up time and it’s held at a temperature of somewhere between 275 and 300 degrees Fahrenheit for about 45 minutes, and then the glass is cooled, and what happens on the other side of that, is a piece of glass that has very special properties, the biggest thing being is most of the applications that we’re going to discuss is that, that composite retains glass shards and pieces should the glass be broken.
Paul Beers: When we talk about laminated glass, that’s not just all this stuff glued together, is it?
Bob Ford: Well, the laminated glass that we’ll talk about is, if you say “glued together,” you know, the glass is laminated and then autoclaved together, so yeah, it can be a 9/16th piece of glass, it can be used in an insulated unit, down here in Florida where I am, the hurricane code requires laminated glass, but the energy code often needs you to have an insulated piece of glass as well, so we can incorporate a laminated unit of glass into an insulated application.
Paul Beers: So Bob, what I was trying to get at was, when you think of taking all these, the interlayer, the two lites of glass, and you go through this process, it’s not just like it’s adhesively stuck together, I mean, I know I’ve seen where people try to pull it apart, and it’s like all integral together. Is that correct?
Bob Ford: Yeah, it isn’t anything like applying a glue or anything like that where it could be pulled apart. When a glass goes through this process, the interlayer binds with the glass, and basically what you have is, it’s a new product, it’s a composite product, with the properties that make it stronger, as well as much safer than standard float glass.
Paul Beers: So we talked a little bit at the beginning about the applications being automotive and architectural, and I’m interested, and I’m sure the listeners are about the automotive uses, just kind of a quick summary, just so we understand where things are there, which probably crosses over, or will cross over into architectural, and then we’ll jump in on the architectural side.
Bob Ford: Well that it does, and a lot of the applications are similar in principal, so what they mention on the outset of automotive really began in the windshield. The windshield and **** are still probably our largest volume market, and the way we go to market with that is we’ll work with big laminators like Carlex or AVC, who then will sell that product to Ford, or BMW, or whatever automobile manufacturer it might be, and, again, windshields ****, are important, but even that has changed. A lot of vehicles now have heads-up displays, and a lot of our newer projects, and more most interesting projects are actually within HUD units, and basically what the PVB does is it allows, or rather I should say prevents the ghosting of the image within a heads-up display there’s a small projector, which projects various information onto the windshield of a car, and what the HUD does, is basically, the HUD PVB will allow that image to be more sharp for the driver and prevent ghosting along the edges. In other parts of the vehicle, acoustics is one of the biggest growth areas that we see in automotive PVB. For awhile, architectural, or excuse me, acoustic skylights were kind of a premium product on only the higher-end models of cars. Now we’re seeing acoustics throughout the offering of automobile manufacturers like Ford, for example, and a lot of that growth, Paul, is really from the fact that, you know with their cell phones now, and being safe and hands-free driving and hands-free communication, not hands-free driving, but hands-free communication with your phone is very important, and in order for that to happen, when you’re speaking into the cabin of your car, and you’re listening on the speakers, you need a quieter cabin, so that’s where these acoustic products that really help make the, the cabin quieter, and to allow hands-free devices to work more effectively.
Paul Beers: Yeah, and you know we talk about the crossing over into architectural markets, I know acoustics are big and getting bigger, you know as things urbanize, with areas that we have more people on the planet, acoustics is becoming more and more important in the architectural market as well, which is where laminated glass began, even before the hurricane market they were using it in airports and things like that, so, are there any other crossovers from automotive that we’re seeing now, or we may see in the future?
Bob Ford: Yeah, I think acoustics is probably the biggest one that kind of translates back and forth. If you think of the idea of a windshield, that if something is to hit it from the outside, obviously the driver doesn’t want glass flying into his face or the passenger’s face, so the fact that the laminated windshield will retain those glass pieces, that thought process, if you will, translates into security as far as bomb blasts, it transfers to hurricane applications. It’s hard keeping the building envelope intact, and not allowing glass to fly into the building, so I would say that the basic technology of the laminated glass is probably the biggest crossover. Getting more specific to that, I would say yes, acoustics, and that’s becoming a growing segment of our market as well. I think something like 90 percent of the world’s population inhabits 10 percent of the land, so that automatically is going to bring us toward people in closer proximity together, and though we love our fellow man, we sometimes like a little bit of privacy as well, and as you mention in highly urbanized areas, high-rise buildings, the use of acoustic glazing is more important because it does provide more occupant comfort, and it also increases the sellable cost of buildings and rental spaces if these buildings have acoustic, better acoustic performance it’s just a more pleasant place to live and the owners can get more money for that.
Paul Beers: I’ve got a future guest coming up that’s gonna be talking about retrofitting hotels, and one of the big drivers for them is the acoustics, and they did a job, I know, they were telling me about in New York City, where they retrofitted the windows with laminated glass, and it made a huge difference for them, and for the property they could get a return on their investment just because they had better rooms, and they could basically charge more money for them.
Bob Ford: That’s correct, and I think the same design thought goes into hotels that are located in or near airports. Obviously, with jets taking off day and night, you typically see some really aggressive acoustic applications there, and within acoustics, the way PVB works, is it basically breaks up the sound wave. Glass itself is fairly rigid, so that rigid medium is going to transfer that sound wave pretty cleanly. The PVB is a softer material than the glass, so it disrupts that wave, provides dampening, and that’s where a lot of aesthetics is of laminated glass comes from it’s not only a thicker make-up, and a bigger barrier to get through when you combine two pieces of glass versus one, but you also have that dampening effect as well.
Paul Beers: So, let’s run through the list of the, you know, the architectural uses for laminated glass, and why they’re used for various different effects, and then we’ll go back and visit each one and talk about that a little bit more. So what’s the big list of reasons to use laminated glass?
Bob Ford: Well, within our company and the industry we like to refer to that as the Six S’s, and that would be Security, Safety, Sound, Solar, Storm, and Style. You know when a lot of the low-e coatings out there that a lot of our fabricators produce and use, solar’s probably a little bit lower on that list, because frankly, low-e coatings do a much more efficient job of controlling solar heat gain coefficient, or solar heat gain. However, on the security side, that’s probably one of the most important growing trends right now, as far as bomb blast goes and forced entry, but safety is also very important too. Safety’s probably the most generic usage. When we’re in a building and we’re talking about safety glass on the interior you know our ANSI, Z91 standard allows us to use just regular tempered glass, so that if that glass breaks, it would break in very small pieces, and won’t seriously hurt anybody, but laminated glass also qualifies as a safety glazing, and again, like many things we’ll talk about today the ability of the interlayer to retain the pieces of broken glass and make it ideal for a safety application.
Paul Beers: You know, the Six S’s, what I was just thinking about when you were going through them, is, if you, let’s say you pick one of them, say, let’s just say safety, you get the other five S’s along with that, in some degree on every single application, but do you not, well maybe not storm, because that’s designed specifically for that, but you get a lot of the, if not all of the other S’s every time you use laminated glass, do you not?
Bob Ford: That’s a great point, Paul, you’re absolutely right. So, let’s talk about as an example, one of the most rudimentary makeups that we’ll have for a laminated glass unit, so two pieces of quarter-inch glass with a 60-gauge PVB interlayer, and that product is fairly typical for both safety applications that I mentioned earlier in interior partition. It can be used for a handrail from a blast standpoint, you know, .060 PVB probably covers the majority of blast requirements for courthouses and airports and other buildings like that. Obviously there are specialty buildings, like embassies, that have higher degrees of blast requirements to them, but if you have a piece of .060 PVB in your glass, you have basically what’s in, I would argue, 70 percent of the blast application out there, which is just .060 PVB. As far as sound goes, .060 PVB will provide a very good improvement in STC, or sound transmission class, when compared to say, quarter-inch float glass. And then finally with style, when I refer to style, I sometimes speak about the colors that are, are available within the PVB family. Most of us who deal with float glass every day, you know, that if we’re buying float glass, we’re kind of limited to greens and blues and greys. Most of the major float manufacturers out there, even their specialty products, like Guardian’s crystal gray, or PPG’s solar blue, are basically in that blue, green, gray family. So, within Saflex’s PVB interlayers, we have reds and yellows which can be combined over 10,000 different colors available to provide a myriad of colors, like oranges, and lime green, and bright reds, and different shades of blue that typically aren’t offered in float glass colors, so when we speak about style, that’s kind of what I refer to is color. And again, all of those can be combined with our standard clear PVBs, to build a makeup, that would be appropriate for a hurricane application.
Paul Beers: We have a lot of architects in our audience, I know and this color discussion I’m sure is going to excite and interest them a lot, because it can take you out of the ho-hum, as you say, blue-green-gray spectrum, and pretty much give you anything you want, is that true?
Bob Ford: Yeah, it really is. The different base colors that we have really allow you to mix and match, and we have a website, vanceva.com, that your audience can visit, and you can see the various base colors that are available. We have earth tones, as well as more vibrant colors, and by putting up to four layers of these colors together, you can literally create thousands and thousands of different shades. To add to that, we also have products that provide opacity, or I should say interlayers that provide some opacity to glass, so if you have an area where you need privacy, you still want to get some natural light in through the window, but you want to have an obscured view, our cool white and artic snow interlayers, for example, will allow you to, I guess, diffuse the light, is the best description, and they can also be combined with color, so you really have quite a few options, if you’re an architect, that wants to go beyond the standard pallet of greens, and grays, and blues, that you find in float glass.
Paul Beers: Really exciting. One thing I want to just jump back on that I had thought about when we were talking before was, you mentioned the solar, that the low-e coatings do such a good job these days, and you can have low-e coatings in a laminated glass unit, correct?
Bob Ford: Yes, that is correct. Most of the time, and if we’re talking for the majority of the country that’s using, from the hurricane standpoint, you are required to use insulated glass. So, the basic makeup would be your quarter-inch outboard lite, with your low-e coating on the No. 2 surface, that’s subject to the air ****. You then have your half-inch air space, and then your laminated unit on the inside. However, Paul, there are also applications where we want to use a 9/16th lite of glass, with a low-e coating and an interlayer, and in those cases yes, PVB interlayer can be put right up against many of the low-e coatings that are offered on the market from manufacturers like Guardian, Viracon, or PPG.
Paul Beers: Yeah, so not everything always works, but a lot of it does, and so an architect, or **** buyer would work with these manufacturers to find out exactly what they offer in that regard, correct?
Bob Ford: That’s correct, yeah. It would again depending on the performance required in your building as far as U-value goes, or solar heat gain and the colors that you want, because, as we know our low-e coatings will impart color, so we often have a little caveat that if an architect wants a red accent piece, or a yellow accent piece, make sure they get that sample with a low-e coating in place, because as you know, a lot of our low-e coatings that are most popular today, particularly the triple-filtered coating lend a little bit of a green hue to the glass, and that’s where, you know, we want to have a sample or a mockup done before so the architect knows exactly what they’re getting, and Paul, that kind of segues me into another area of that speaking of that green hue to the glass, I know a lot of our audience are trying to find coating and glazing solutions to kind of get rid of that green, so a lot of low-iron glass being used in the market today, and we actually have a structural product that is intended for use with low-iron glass that, goes more toward a slightly blue cast rather than a green cast, and it looks really, really nice when used in low-iron substrates.
Paul Beers: And low-iron just so we’re all on the same page here, low iron is like super-clear glass, that, would that be the right –
Bob Ford: Correct. Correct, and you might hear the term ultra-clear, and basically the process is that it’s further refined from standard clear glass, where more of the iron is removed, and it’s the iron in the glass, particularly when it’s heat-treated, that kind of gives it that, that greenish hue. So, when we pull more iron out of the float batch, we can get a low-iron product, and all of the major float manufacturers out there do offer a low-iron product. You may have heard of a, you know, PPG fired the Starfire, for example, so different manufacturers have their different low-iron substrate on the market.
Paul Beers: Now I just want to throw this out there not to be a downer, but it is more expensive, also.
Bob Ford: It is kind of that…you get what you pay for, and, yeah. So low-iron glass, typically will add in, if you’re using two units of it, or two pieces, **** typical one-inch makeup, you’re going to be looking at somewhere around $1.00 to $1.25 a square foot premium for each of those lites of glass.
Paul Beers: And I have to say, so I’ve worked on a lot of projects with consultants or with an architect that looked at low-iron, and in the past they’ve been budget-busters. They have a budget, they want the low-iron glass, and then they get the prices, and they can’t afford it, but it sounds like the delta has come down a lot, if it’s only $1.00 or $1.50 a square foot, it used to be a lot more than that.
Bob Ford: Yeah, Paul, actually, I think I actually misspoke there. That delta is closer to $2.00 to $2.25. The other thing I was gonna circle back to here, when we’re talking about laminated glass and in a safety application is heat soaking, and being able to prevent nickel sulfide in the heat soaking aspect of it is more the $1.00, $1.25 a foot. You are correct, I did misspeak, that the low-iron glasses are typically $2.00 to $2.25 a foot premium, based on a quarter-inch substrate, so that was my mistake.
Paul Beers: No, that’s fine but even that has come down from, I think what it used to be, so I think there’s more possibilities out there to maybe use that, and I know a lot of architects like that kind of a color influence that they’re looking for, so that’s good information.
Bob Ford: And especially if you’re looking at, you know, you look at the cost of the entire laminated unit, I mean a piece of inch and 5/16 laminated glass, depending on the interlayer, and the low-e coatings in the substrate, may be anywhere from, you know, 20 to 25 bucks a square foot. So you look at it from that aspect and the delta for the low-iron is not quite as big as jump as far as the percentage of the whole unit is concerned.
Paul Beers: That’s right. So, let’s talk about security, a little bit of more blast and forced entry. You know, the blast thing, unfortunately, has become a lot more prominent over the years, with the, the rural events, I guess I’d call it, being what they are. The forced entry, I don’t think laminated glass gets enough credit for how it performs in that regard, and if you just think about it, typically, like a storefront, you know, like a shop, you know, the thing in the past you would always have would be a tempered glass unit, and, **** a mischaracterization but everybody gets it, tempered glass I described as the glass that breaks into a million pieces, so if somebody breaks the glass, it’s basically on the ground, and there’s a big hole in the building, and laminated glass, what happens there?
Bob Ford: So that’s an excellent point. This is something that I think a lot of my folks, for example, about 2 years ago had, they live in down in Fort Myers, so they had hurricane blast windows installed in their home. You know, I think they were just thinking, yeah, you know, we’ll be safer in a storm, but as a secondary, benefit of it, is absolutely the prevention of forced entry. To go through a piece of tempered glass with a blunt object is fairly easy to do. I mean, tempered glass, as you know, is twice as strong as heat-soaked glass, which is twice as strong as regular float glass, as far as blunt impact, but you can break it fairly easily with, with a bat or some other implement. Laminated glass, on the other hand, you can go at that for 20 to 30 minutes, and you’re not gonna make any sizeable hole in it. The other thing is that, you know, in both areas where this glass is located, residential areas, you know, someone’s banging away at your sliding glass door with a piece of laminated glass is gonna draw a lot of attention. So, as a secondary kind of passive benefit is the security and safety from a forced entry standpoint is one that is very little thought of features of it, but absolutely is one of its strongest attributes.
Paul Beers: Yeah, and you know, I always said, if we were back when the hurricane market was developing, we were talking about the other benefits of glass, and you know, **** back then was, if you have I guess we’d call it an opportunistic thief, who was trying to throw a brick through the window or hit it with something, they’re gonna get tired and go somewhere else, because if it’s not going to work out then it won’t go well for them.
Bob Ford: Correct. And particularly in Florida you have a lot of part-time residents down here, and a lot of houses that are basically, no one’s living in them for several months out of the year. Those might possibly be a victim or a target for some thief, but, again the forced entry resistance of even regular .060 PVB, as most people are having laminated glass in their one- or two-story homes they have likely 090 PVB or an even stronger interlayer. Unless you have really specialized cutting tools, a saw, and things like that the average opportunistic thief, as you say, is not going to be able to make any kind of entry through a window like that.
Paul Beers: So people are thinking, “Well, what about if there’s a fire how does the fire department deal with that?” And they do have those sophisticated tools you just referenced, right?
Bob Ford: They do. They do. Yeah, I mean the glass, obviously, like anything else, it does have its limitations. I mean, for a thief with a crow bar or a baseball bat or a brick or a rock, yeah, he’s not gonna have any luck getting through it. A fireman, however, they have special equipment which basically allows them to saw through the glass, much like they would go through any other kind of wall and create an opportunity to get in or out of the structure. So, yeah, from a firefighting standpoint, they all carry that type of equipment on board so that they can get through that laminated glass fairly quickly. The average thief doesn’t have all that in the, trunk of his car.
Paul Beers: Yeah, no, no, no. My hope is that we don’t have any thieves listening to the podcast, so, but, another thing the fire department can do is they can chop through it with their high-tech axes as well.
Bob Ford: Correct.
Paul Beers: You know, the thing with the security applications, is gonna segue us into talking about storm as well, and that it provides passive protection, and maybe you’d talk a little bit about that, because that’s a really big deal as well.
Bob Ford: Yeah, so, again, one of the nice things about laminated glass is that it’s always there, 24 hours a day, 7 days a week, 365 days a year. Particularly for a storm application the alternative product as far as opening protection may include, boarding up your house with plywood, putting up hurricane shutters, things like that, but those do have their drawbacks, first of all is that if you’re boarding up your house for the winter, the summer, rather, to go back north, it’s pretty obvious to people looking at your house from the outside that you’re not home. The other aspect is the difficulty of storage and putting up those shutters every time a storm comes in can be a bit difficult, particularly for some of our older population, that doesn’t want to be up on a ladder, or pulling these heavy pieces of metal or vinyl or other materials out of their garage, so laminated glass is always in place. It’s always there working, and it’s just a very logical solution, particularly you know, Florida has a lot of retired folks out here, and that just gives them good peace of mind that their home is protected from a variety of threats.
Paul Beers: So I live in Palm Beach Gardens, Florida, I’ve had this house that I’m in now for I dunno, 10 or 12 years. It was built to the new code, and it was provided with removeable storm panels, which work very well, but I have to tell you, every time a storm comes, it’s a major undertaking to get them out of the garage, and get them set up on the house, and if you hire somebody to do it they’re gonna charge you, like, a thousand dollars or more to do it, and it’s a major hassle, so you start thinking to yourself, if a storm’s approaching, is it gonna hit, should I do it, shouldn’t I do it? So, last year I decided to put hurricane impact windows in throughout the house with laminated glass, and, you know, it wasn’t inexpensive, but we did it, and got rid of all the shutters, which was great, and so this year, Hurricane Matthew was approaching the east coast of Florida, and it was a big deal. They thought it was gonna hit West Palm Beach, and it, you know, ultimately it didn’t, but I was on vacation in Morocco, hiking, when all this was going on, so, you know, obviously I’m concerned. I didn’t have a lot of connectivity, I was texting my son and whatnot, but the great news for me was, we were good. All we had to do was make sure the doors were closed, doors and windows were closed and locked, and we were ready for it, and I have to tell you, the, the difference, the peace of mind, and the confidence that it gives you to have that passive protection all the time, and with the breaking and entering and whatnot, it really makes a lot of sense if you live in an area that needs something like that.
Bob Ford: You’re, you’re absolutely right. I know when a storm is coming like that, you know, having lived in Florida since the late 90s, I’ve seen a lot of hurricane reports on the news, and when a storm is coming your way, there’s a lot of other things to do, like having a plan if you need to evacuate or take care of pets or if you’re going to stay, stocking up on your water, and food, and all those things. There’s a lot and life gets really busy when a storm comes in, and if you don’t have to put up hurricane shutters, that’s one less thing to worry about. I know I can also offer a kind of a personal story here. Before my folks down south had gotten their hurricane windows in, they had shutters up, so when my folks go north I came down to help my father remove them, and he had the old metal panels that screw in, which work very well, they also tend to be very heavy at times, and sometimes a little clumsy to handle. I ended up dropping one of those on my foot, so about you know, 30 minutes later, and 14 stitches later, I had a nice permanent reminder on my right foot of the benefits of laminated glass versus hurricane shutters, so, a lot of the products are now becoming so much more affordable as far as windows go, and I think that anyone who either is a part-time resident, or let’s face it, a lot of us travel for our jobs, and if we have a storm, we might not always be able to get there to put up those shutters, so having laminated glass is absolutely good peace of mind.
Paul Beers: In 2004, I was in Seattle doing water testing on some hotel projects as an expert witness assignment, and I had my son with me at the time, he was helping out, and I remember we went and paid a lot of money for a plane ticket, took the red-eye home, which is not part of my normal DNA, and flew all the way back to Florida so we could put our shutters up, and it’s insanity, basically, but the whole plane from Seattle to Atlanta was loaded with people going back to Florida for the very same reason. It’s really interesting.
Bob Ford: Yeah, it’s you know, as I am now in my mid-40s, and I really don’t want to find any reason to get on a ladder if I can help it, maybe to put up Christmas lights, but that’s about it. But handling those panels, and the weight of them, it’s just that laminated glass is a much simpler solution, and is there a, more of an investment up front, absolutely, but I think all the benefits that it provides just really makes it a good investment.
Paul Beers: And then on the business side of things, you have people that may be responsible for putting shutters up, if you have shutters on your facility, have families at home, they have the same worry, all the same worries we just talked about, so it makes, even, maybe even more sense, in commercial and multi-family applications, you know, not to mention when you get up in the air above the first floor, to have the passive protection so that that’s just one less thing to deal with, because these things sneak up on you. I’m out in Morocco, clueless, and all of a sudden there’s a hurricane about to wipe out south Florida, and I wouldn’t have been ready for it, so it really it’s compelling, I think.
Bob Ford: And the thing that they can change their track so quickly, and their intensity so quickly. I remember when Hurricane Wilma came through south Florida back a few years ago, and it was kind of off the coast, it really didn’t look like anything that much, and then all of a sudden, it just ramped up into a pretty damaging storm, so, yeah, you know, with hurricanes we are very good at or getting better at predicting where they’re gonna go, and how strong it’d be, but there’s still a lot of randomness out there and chance, so, better to be protected, and again, laminated glass is one less thing to worry about when that time comes.
Paul Beers: That’s right. So, for hurricane windows and doors and commercial systems, what has to happen to actually become a hurricane window, for a product to actually be a hurricaner, and they use, by the way, “hurricane proof,” I hear “hurricane-proof windows,” and that’s not a good term, and in fact Will Smith, who works for us, just wrote a little blog article for us last week talking about the misnomers that people need to understand, even with the hurricane windows, that they provide protection, they keep the hurricane out, that doesn’t mean that they’re shatter-proof or anything like that. But let’s just talk about what does it take to be called a hurricane rate, or a rating for hurricanes or wind-borne debris, with a window or glazing system.
Bob Ford: So, it’s basically two components. So we can talk about hurricane-resistant glass, I think is a better term, and like you mention, Paul, hurricane-proof indicates that the glass won’t break. I’ve had, you know, architects have asked me before, “Well, you know, if it breaks during the hurricane then we have to replace it,” and I tell them, “Yes, you’ll have to replace that window, but it’s better than replacing your entire building.” So when we’re testing, we’re basically looking at their framing system, now that can be most of my life is spent in the commercial segment, so that could be a curtain wall, that could be a storefront, that could be a fixed opening, or it could be a residential window. So, when we talk about the testing, we need the framing portion, and then the glazing in-fill that goes in it, and basically the main part of the glazing in-fill is the laminate, or the laminate interlayer. As the testing goes, glass, if it’s annealed, and heat-strengthened or fully tempered, it’s not necessarily manufacturer-specific. You could be getting your glass from Cardinal, or Guardian, or Viracon, or Oldcastle, Trulight, whoever. It’s the interlayer that has to be tested with a specific framing system. So what they’ll do is they’ll build a mock-up of this, and it’s also gonna be size-dependent, so you’ll have a given size, and it’ll end up in the commercial size of things, most people test up to about a 40-square-foot piece of glass. So let’s say we have our five-by-eight test specimen, it’s either gonna be, insulated-laminated, or just laminated glass, and there’s two different tests, Paul, that we do. The first one is called a large missile, and that’s meant for any glazing that’s from ground level to 30 feet in the air, and this is typically a 90-gauge PVB, or it could be a specialty higher-performing interlayer, an ionoplast material, or a composite PVB, and basically during the test, it’s comprised of two components, the first is an impact portion, where they fire a 9-pound piece of two-by-four lumber at 50 feet per second, which is about 34 miles an hour, and they impact, the glass with that, and then the second test is the cycling, and that’s basically to replicate hurricane winds that could last, you know, 4 or 5, 6 hours if the storm moves through your area, and that requires positive and negative cycling with 4,500 cycles each at varying degrees of the test pressure, and basically that impact and pressure test, if the glass makes it through that, it will be determined to be passed as a hurricane assembly, and so, again, we have to be cautious of not just putting any piece of laminated glass into any framing system. That piece of glass being an interlayer makeup must be tested specifically with that given framing system.
Paul Beers: That’s a great point, too, the magic glass doesn’t just make it into a hurricane window, it’s gotta go through this design and testing process, and then it’s actually gotta be approved, put in the product approval system, the State of Florida would be one, and I know Miami-Dade County was the first one, still **** leadership position there as well, so people often ask me, you know, ” I’m looking at getting new windows for my house, or for my building, what do I do?” Well, the first thing you start with is getting the Florida building codes, or Miami-Dade product approval listing, and make sure that it’s **** testing, make sure that it meets those required wind blows **** for your project.
Bob Ford: That’s correct. I often have worked with some architects on retrofits and, you know, they want to see if they can get away, and it typically doesn’t happen in Florida, since the market’s been so developed down here, but you know, “Hey, we want to remove this existing quarter-inch glass and put in hurricane glass in the same frame.” Well, that would certainly mitigate the potential damage, yet it would not be considered a hurricane-resistant system. Again, that word “system” means glass tested with a specific framing system.
Paul Beers: The other thing I was thinking about when you were talking about the hurricane glass, what about tornados? I know there’s not a certification program, but I’ve often thought, well, not thought, I know this is just instinctive, that you see these tornados, we’re getting into tornado season, and well actually it’s the springtime, but coming up, and every year there’s these horrible tragedies where towns get hit, you know, I remember Tuscaloosa, Alabama was one, and I’m trying to think where the other was, I think, Kansas. We had hospitals that were badly damaged, and I thought and wondered, why, like if you have a hospital in Tornado Alley, why wouldn’t you put in a hurricane-type of window which would give you a much better chance of surviving, whether it’s rated or not. Have you seen any projects where that’s been done?
Bob Ford: Yeah, well we have something down here, when I mentioned different large-missile impact, we also have something down here what are called “essential facility,” and those are what they refer to as “Level E” glass. And as I mentioned, the standard large-missile test fired a 9-pound two-by-four at 50 feet per second. With the Level E, that two-by-four is fired at 80 feet per second, or about 55 miles an hour, and what that requires, Paul, is a, a hardier interlayer to handle that impact. Now, if you’re going from that to a tornado there’s a FEMA standard out there that I think they want the missile to be fired, the two-by-four, at something like 100 miles an hour, and that is an incredibly difficult test to pass. We have done some and worked with some of our partners to try to create double-insulated makeup basically creating almost like bullet-resistant glass, to be able to resist something like that, like a 9-pound two-by-four at, at 100 miles an hour. You know, as far as those buildings that are in Tornado Alley are subject to that, you know, if you get the right tornado hitting you unfortunately, there’s probably not much that glass, you know, if you got caught in a 4 or 5 tornado, it’s just, there’s not really a whole lot of building material out there that can withstand that. With that said, laminated glass would do a lot and would go a long way to mitigating some of that damage. Again, the idea of maintaining and keeping those broken glass pieces in place, adhered to the middle layer, and try to protect the building envelope would certainly be a benefit in a lot of cases where hospitals and first responders and folks like that, when their buildings are subject to a storm like that.
Paul Beers: Yeah. And I’ve just thought that the hurricane window probably works in a lot of other areas, not a failsafe, but certainly a epic improvement over not doing anything.
Bob Ford: Absolutely. Correct. Again, a lot of the other benefits we talked about with laminated glass particularly the acoustics, and a lot of hospital settings that would have an added benefit, and from a design standpoint, particularly a lot of the children’s hospitals that we’ve seen that are going up, architects are often using very bright colored windows interspersed amongst the curtain wall and again, you can accomplish all those things with laminated glass.
Paul Beers: So this segues into my closing question, which relates to the architects and owners that are listening to the Everything Building Envelope podcast, why should they use laminated glass?
Bob Ford: Well, I just think it provides so many different benefits and again, depending on the application you’re talking about, but, basically, it’s an enhancement over standard float glass. Again, from a color standpoint, your pallet of colors is completely opened up to you. As far as from a security standpoint, if you’re designing for hurricane, and you’ve got 90-gauge PVB in your building, guess what, you’ve probably got serious blast protection already in place as well, as well as very good acoustic, as well as prevention of forced entry. So, I think this one product just has so many attributes about it, when applied to the architectural market, that, you know, laminated glass is more expensive than regular glass. I mean, if you’re comparing a 1-inch insulated unit to an inch and 5/16th insulated laminated unit you know, you’re talking several dollars a square foot more. However, all of these other benefits that come along with it, you know, just give you a really good bang for your buck as a designer, and I think we’ll see this trend continue for the projects that we see on the horizon.
Paul Beers: It’s a very, very good performing glass system, basically.
Bob Ford: Yeah.
Paul Beers: So, Bob, thanks so much for coming on, it was really interesting, it was insightful, it was thought-provoking, I thought it was great, and it’s really good to talk about this, and let the listeners know, some of or a lot of this stuff, but to really be able to hear the whole picture, and then give them something to think about going forward.
Bob Ford: Well, Paul, I appreciate you having me, and I did want to thank you for one thing, that the fact that we’re recording this November the 7th, you didn’t ask me any political questions, so, I thank you for that. I was waiting for one of those, though, and the only thing I was going to add, was that something both sides of the aisle, you guys agree on here, is that actually, Saflex interlayers are used to protect our nation’s most prized items and charter to freedom, that being the Declaration of Independence, the U.S. Constitution, and the Bill of Rights. All those, if you go to the National Archives you’re going to view them beneath layers of Saflex, laminated glass, so a lot of applications perhaps you don’t think of every day.
Paul Beers: Good stuff. So, thank you, everyone, for listening to the Everything Building Envelope podcast, this is Paul Beers, ’til next time, so long.
About GCI Consultants: GCI’s building envelope professionals provide consulting services to ensure clients receive maximum value and return on their investment in the firm’s services, which include:
- Engineering Services
- Design Assistance
- Field Testing
- Quality Assurance
- Forensic Evaluations
- Roofing and Waterproofing Consulting
- Litigation and Claims Consulting
- Façade Assessments
- Catastrophic Damage Evaluations
- Due Diligence Surveys
http://gciconsultants.com
Be Social With Us-
https://www.facebook.com/gcibuildingconsultants/?hc_ref=SEARCH&fref=nf
https://www.instagram.com/everythingbuildingenvelope
https://www.linkedin.com/company/gci-consultants-llc?trk=biz-companies-cym
https://twitter.com/GCIConsult
https://www.youtube.com/channel/UCAbJ9V54HlezvRPFD39Zopg