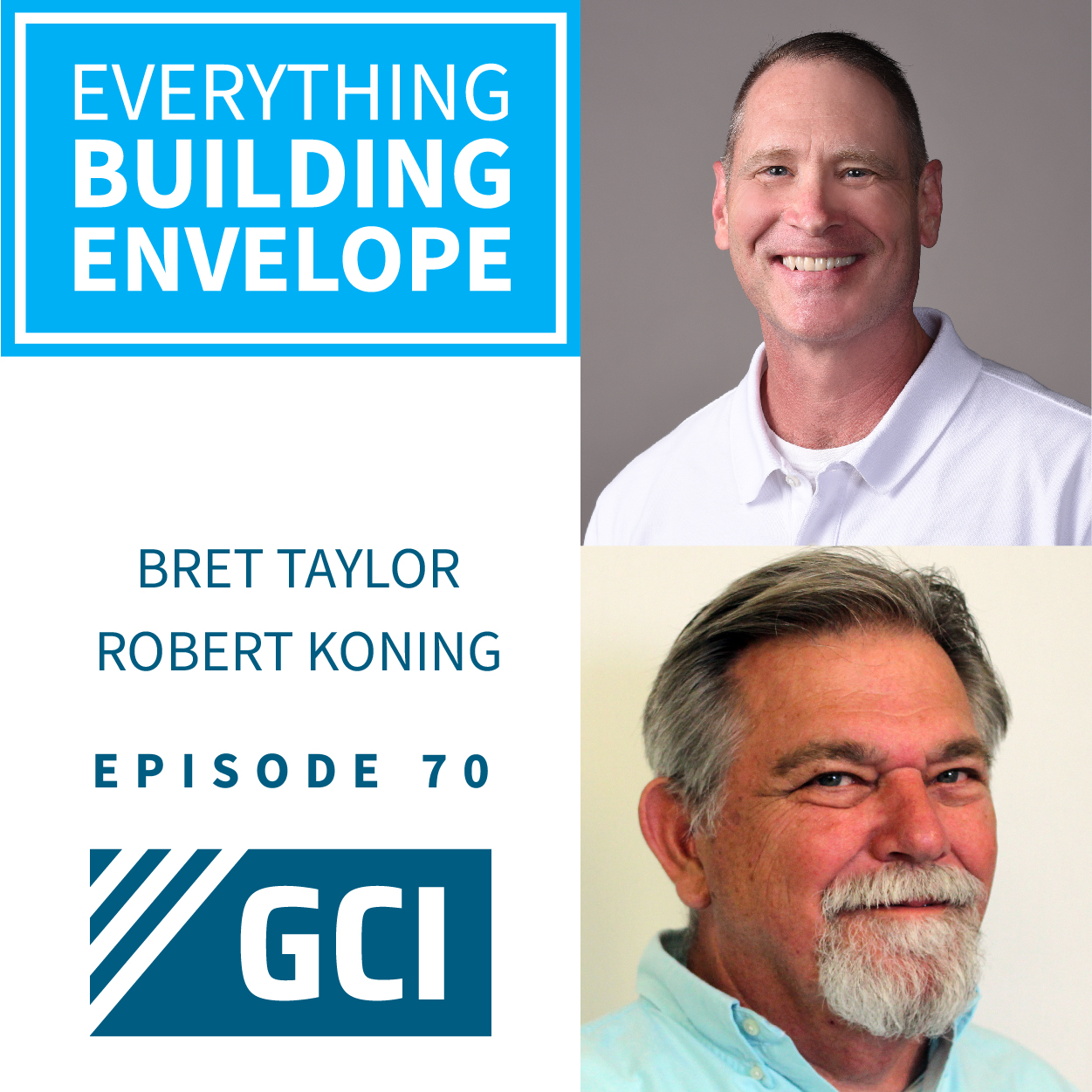
About The Everything Building Envelope Podcast: Everything Building Envelope℠ is a dedicated podcast and video forum for understanding the building envelope. Our podcast series discusses current trends and issues that contractors, developers and building owners have to deal with related to pre and post construction. Our series touches on various topics related to water infiltration, litigation and construction methods related to the building envelope.
https://www.everythingbuildingenvelope.com
*** Subscribe to the show and leave us a Review on ITunes!
Bret: Welcome everyone to our “Everything Building Envelope” podcast. I’m Bret Taylor, professional engineer, senior consultant, too, for GCI Consultants. I’ll be your host today, and I’m excited to have with us Robert Koning who is the director of the Contractors Institute, Stucco Institute, Building Officials Institute, and he’s also the developer of the Sealed Cladding System. And he’s a consultant in the construction defect industry as well.
Today, our topic is going to be the state of stucco. So, Bob, start off. And I’d like you to tell our audience a little bit about yourself, and then we can jump right into the state of stucco.
Robert: Well, Bret, I want to thank you for this opportunity to join in this podcast and be part of it. My history throughout my entire adult life in construction, I’ve really done nothing but that, has been involved in the roofing, waterproof, stucco, and plastering industry. That’s been my main forte. Today, my practice is pretty much limited to education and training at the Contractors Institute, and, as you said, the Stucco Institute, and the Building Officials Institute. We provide examination preparation and continuing education courses for the construction industry.
Historically, the stucco industry, as I was part of, that’s how I got into construction back when I was, after school, 16 years old, at a plaster mixer, and have never really gotten out of the stucco and cement-plastering trade. Still in it today, to a limited degree. But historically, we plastered these houses, we stuccoed these houses. It was a different process then, and we had no problems. Then, [inaudible 00:01:59] 2000, through some changes in the industry, or, should I say, some application of interpretations in the industry, we changed things, and then problems began, and are abundant today, for a myriad of reasons, some of them related to stucco, but most often, they are not.
Bret: Okay, excellent. Well, that’s an amazing life accomplishment you’ve got there with all the different institutes and your experience. I’m sure everybody is looking forward to hearing from you today. So, let’s get right into it. Let’s start with a brief history of stucco, just like you were mentioning earlier. About what year did you start, Bob, in stuccoing?
Robert: I started in stuccoing back in the late ’60s, when I began. And as I said, still in it today.
Bret: Well, that’s a good long time. And I’m going to take this opportunity to point out, too, that you were stuccoing in the ’60s. It was occurring before then as well. Stucco has been a viable cladding system in Florida, but…Florida since then, and before then, and continues to be so. And I think what we’re going to get into today is some of the items that we’ll cover. Some of the problems that have come up, like you said. Those don’t necessarily mean that stucco is a bad thing. It is viable. And if done properly, it can continue to be viable.
Robert: That’s absolutely true. When I started in this, I had the honor of being trained by a lot of old-time workers that were in the field. Today, we have the blessing of a lot of men and women working in the field. When I began my career, as you can imagine, it was largely men. There were a few women, but our workforce has expanded, thank God, and we have a lot of new talent.
But the old guard, so, I’ll just simply refer to them as “the old guard,” that trained me, all of their lessons were from trial and error what did and did not work. And the stucco or cement-plastering industry evolved to form a viable cladding that just performed flawlessly. Things were somewhat different then, when we started this originally. The houses inside were rock lath. I began my practice at the era of rock lath. Before that, it was wooden lath strips. But when I got in, it was three-eighths rock lath. And then we would come in and we would brown coat, which is a gypsum plaster. And we would take rods and straighten the wall out. And then we would go outside. The brown coat had to dry, so we moved outside. And we would scratch any of the wire around the house with metal lath. Then, that metal lath was not galvanized. It was plain black, with an asphalt coating sprayed on it, which, what we today refer to as interior lath. So, it was black lath. There was no rib lath then. It had been nailed on the wall by the plasterers, us. And we used interior nails, which were not galvanized, blue lath nails. And the pattern then was you spread your hand out, and you had to have a nail. If you put a nail on your thumb, then you had to touch it with the top of your pinky. That was about the spacing each way, on center. Of course, the back sheathing was either diagonal re-sawn 1 by 10, or plywood. And then it was covered with felt.
We hand-nailed that on, and then we scratched it, the plasters, then. I can remember my uncle telling me when I first learned to use a Hawken trowel, they would put the mud, the cement, on the board, so, mud boards. And we’d make a ring in the middle of it, put a little water in, and mix it with your Hawken trowel on the board, so that it was a looser consistency or viscosity. My uncle wanted it…all the old plasterers wanted it that way, because when you scratched it, you took that cement, and you used an up-down-up motion with your trowel. And he wanted to see that that cement was so fluid that it would push in through the lath and, to the degree it could, behind the lath. And you would form, like, a little river on the toe of your trowel, the toe being the front end, the heel being the back end. That way, he knew that it was completely fluid, and you were putting a coat on the wall that completely enveloped the lath.
His reasoning, I asked him why we had to loosen that mud up, was very simple. He said, I’ll never forget it, “Boy, you can’t have any pockets behind this. If you have pockets behind this, you’re going to have air. And when you get air behind it, in Florida, it’s got salts in it, and it’s gonna corrode the lath. So there can be no space behind that plaster and that lath.” And as for the nailing patterns, I asked him, “Why are we nailing it with this pattern?” Even back then, they knew. He knew. Because in storms, that suction pressure will pop that stucco. It’ll crack it if you don’t nail it at that frequency. So, that was the extent that was told to me.
Then we scratched that. And then we would leave the job, and we would come back a week or so later. And now, it was time to put the white coat inside of the house, which was simply lime and sand. So, you’d scrap the brown coat down, and now, you put a thin coat of lime and sand in over the gypsum plaster. And then you moved outside and put your second coat on the wall, and densified it. Then, we always densified the second coat of plaster. And that’s just with a float with a open cell, like a green…today, they’re green, but it’s an open cell. And you dipped it in the water and you rubbed it. Most of them were then sand-finished. You used a white float and you would sand finish it like you did on the inside.
Then, all of the corners were rodded. In other words, we didn’t use any beads. You’d hold a straight edge, and you rodded that. People who don’t know what that is today can go to the Stucco Institute. We have all the photos and the materials there.
And then, all consideration was given to the painting contractor. We had V tools, and we cut a little V around all of the openings. And you used a paintbrush, like a chip brush today, a cheap throwaway. And you would wet it. And you would go down that V cut, to soften the edge, so that the painter could use a spatula. And you cleaned the shoulder of whatever it was touching, so that when the painting contractor got there, he simply had to just rub a brush up and down it, or a rag. And he had a good bite, or a good shoulder, to seal on from whatever the penetration was, pipe, or a brick molding, or whatever. And the other side of the V, which was in the plaster body, had a soft edge so that his spatula would go down.
And the painters then would seal and apply the coating, by roller, to the proper mil thickness. They would brush all of these V tools, then put their sealant in. And then they would roll the first prime coat. And they would roll the second coat, at 2 mil thicknesses of about a minimum of 12, even back then. And they gauged that by the amount of coverage of the paint. And we ended up with a face barrier system that performed absolutely perfectly. The goal of that system then was to ensure that no bulk water, of course, and no vapor penetrated through that, that would get in behind your system, where the felt might wrinkle when the cement touched it.
And that system failed. I mean, that system never failed. It was flawless. And it was the one in the Miami code since I’ve been following the code. Someone told me it went in in 1932, but it certainly was in in the ’50s, all the way up until 2010, when it got removed by the Florida Building Commission, with the simple premise they’re trying to minimize the codes. And our reference codes today, which are the 926 and the 1063, have provisions “unless otherwise specified.” So it would allow people to continue following that protocol because of the “otherwise specified” provision in the referenced ASTM documents.
But that got lost along the way, and we started putting systems on for drain plane systems. And as my mother used to say, “You can’t be a little bit pregnant. You either are or you aren’t.” The same is true here. Either you have a functional drain plane system or you have a face barrier system. You can’t have a little bit of both. It doesn’t work that way. And so, we’ve got into some problems in the industry in that respect, along with some diminishing of other aspects, such as roofing, and painting, and sealants, and soffit, and fascia, which we’ll talk about later.
So, I guess, what I would say is that there was a complete lack of understanding [inaudible 00:12:04] 2000 and a transition after hurricane Andrew, when the engineers, rightfully so, became involved in designing load pass. There were people that looked at this then standard, the ASTM 926 and 1063, which are an application standard written by plasterers, out in the Midwest, for plasterers in the Midwest when you’re using three-coat stucco with a colored application finish over open frame. And they read that, and a lot of people just didn’t understand the difference, so they just said, “Well, hey, this is the way it should be put on. Let’s adapt to this.” And failures started. And they still are abundant today.
Bret: Yeah. That was a great description of how stucco is installed. And I was visualizing it the entire way. And as I was visualizing that, I was thinking about the different areas that could be done improperly, that would allow that, you know, face sealed system to not perform, as you mentioned. And then, can’t be a little bit pregnant. Once you in some way compromise your failed sealed system, and you’re going to have water coming behind the system and you’re going to compromise your overall integrity. Let’s talk about some of the areas that could fail. So, you were talking about scoring around the openings. Let’s talk about some of the areas that, if done improperly, could let water behind the system.
Robert: Well, I’m just going to call it the big three. That is, of course, the thickness of the coating itself that we put on the outside and the accessories. The two biggest failure points in accessories are plastic, or vinyl, or metal, corner beads on the outside corners, and control joints. Those are the big-ticket items. Remember, what we’re trying to do here… If you think of this, and we have data loggers, and tests, and data at the Stucco Institute, voluminous materials you can download free, but the concept is relatively simple, Bret. The ASTM documents are very, very good documents. And they were written for an arid region and a lower wind speed. So, if you take, first off, the first component in that is metal lath over a wood-frame wall. We’ll talk about over block later, but it’s a lot simpler over the block. But over a wood-framed wall, and you’re in an arid region, why… It’s open framing first, of all? And in some of our training materials, we show the National Weather Service data. So, you’re in, let’s say, Las Vegas or Nevada. And it’s 102 degrees average in August, you know? And the outside relative humidity is about 28%, and the rainfall for the month of August is 0.60 inches, less than an inch. And the inside relative humidity in the house is tried to be maintained up around 50% and about 75%.
So, if you just take simple diffusion pressure and you do this concept, you have this wall. And this wall gets wet. It’s three-coat stucco, and then the final coat is colored cement. That wall gets wet. First of all, the wall itself in a rain shower in Nevada is going to shield, I mean, just simply resist the bulk of the water. It’s going to run down the wall. A minuscule fraction of that amount of water is going to get through cracks and separations. And it’s going to migrate down behind the system, and it comes out the bottom weep screed at the crack. People don’t always understand that that weep screed has holes in it. They think those are for water drainage. They are not. Those holes lock the plaster in. It simply weeps. Remember, it’s a weep screed, not a drain screed. It weeps the minuscule amount of water that got through at the crack along the bottom. Before, we had vinyl, plastic as most people call them. They’re a plastic-based material. Before we had that, and we had metal, we had to wax the top of those flanges so that the lime wouldn’t bind into that and block that ability to drain at that crack.
So, this standard was written, again, with using lime, and sand, and cement. There was no pre-mixed type X then. So, the water would be shielded by the wall, and some would get through. The vapor never really wants to permeate through. And the reason of that is the relative humidity is lower outside than it is inside. So, when the rainstorm stops, immediately, you go back to 102 degrees. You’re back to 30% relative humidity, and the wall dries to the outside very, very rapidly. So it’s really hard to get any long-term or chronic moisture problems in a wall out there. It gets wet, it’s very incidental. Everything is trying to dry to the outside, and drying to the outside.
Now, if you move that scenario to Orlando, Florida, where the average August temperature is 94 degrees, the relative humidity is 86%, and the average rainfall is 7.5 inches, as opposed to a half an inch, now, you are just simply flooding that wall with water on a fairly constant basis. The outside humidity, of course, is above 90%, and it was 100% when it rains. The inside is being maintained about 55%, so all of the water and all of the vapor have a diffusion pressure to move inward.
So, let’s assume that the rain stops, and the relative humidity stays in the 90s for a while. It might get back down to the 80s. But it stays high. And now, all that vapor does not dry to the outside. It is pushing to the interior. There was a time when we used felt, and we had laps on the felt. And that vapor could migrate through, and then it would encumber either wood planking or it would it would hit a plywood sheathing with a perm of about 12 grams, perm rating is about 12 grams, and could pass through and be dehumidified into the system. Before air conditioning, the inside and outside were stable, so you didn’t have any difference in diffusion pressure.
So, now we’re moving. Well, with the advent of OSB and house wrap. The house wrap, at least, Tyvek, normal house wrap, the perm rating is in it’s 50 grams. Even stucco wrap is around 20 grams. That vapor moves through the house wrap, and now it encounters the OSB in its movement inward. Well, the OSB perm rating is 0 grams to 1 gram and has a silicone coating on it. And so, it stops there. And it just remains there behind the stucco system in mass. And then at nighttime, when we have the radiant loss to the nighttime black sky, the wall cools below the condensing temperature by about 10:00 at night and that vapor condenses behind our system. And then, we keep that cyclical.
We painted the house with the outside, with paints. We measured 74 houses in a recent study. The average mil thickness was 3 mil. Remember, and it should be 12 mil. So, the vapor passes right through, but now there’s no returning force. There’s no difference in diffusion that’s trying to get it to dry out. It’s still wanting to go to the interior of the house. And to make matters worse, we have a weep screed down at the bottom, and we’ve painted the crack. I mean, you can’t let the water out now, because this stucco system, as it’s contemplated in 926, well, everybody understands, was never meant to be painted. You have to do other accommodations with your termination point. So, now, we have the wetting, continual elevated relative humidity, behind the stucco system, behind the Tyvek, the Typar, and now we get fungal growth. And once we initiate that, we have problems. So, that’s a first, huge problem.
Second problem we have is the attachment of the lath. The standard was written in a low wind speed region, where straight-line winds then were 90 mph. And they said in the standard, to put the studs, excuse me, to put the fasteners of the metal lath 7 inches vertically up the studs, which are spaced 16 inches horizontally on center. And that’s fine. That works well. We don’t fail in withdrawal. But what happens in a higher-wind region, where the wind speed is over 115 mph Vult, or the wall pressure is in excess of about 28 pounds? Then, what happens is the fasteners don’t fail and withdraw. The stucco literally, in between that 16-inch space, bows outward from suction forces, and cracks.
If you think about it, if you, in a high-wind region, and you space 16 inches horizontally on a 8-foot-high wall, that’s, all of that area, I think it’s over 10 square feet, all of that area is now with no fasteners. It’s unrestrained. And so, you can see the flexure of the stucco is great, and that’s why we get a lot of cracking. We didn’t have that in Miami-Dade, and the reason is Miami-Dade always required two fasteners per square foot. Which means you have to put a row in between the vertical framing members.
One of the misunderstandings, fundamentally, of the text is why is it on the vertical studs? And why is that important? Because the standard was written for open framing. Where else are you going to put the fasteners, in open air? There’s no other choice. Even when the standard talks about sheathing, it’s talking about non-structural sheathing, such as Styrofoam, or Homasote, or asphalt-impregnated sheathing, or thermal ply. Any of those, that is done everywhere in the United States, except here in this high-wind region area.
So, now you understand, if you take those two precepts, you understand, over open framing, why the standard says, “In between the studs, you have to tie the lath of the wire with tie wire. You have to tie the lath, so, the metal lath, with wire, 9 inches in between the studs.” But, one sheet to another of metal lath, and it’s not over a vertical framing member, like in between the two, you have to lace wire in between the two sheets. Well, of course, if you didn’t do that, when you ran your trowel of mud up the wall to scratch it, your hand would simply go into the middle of the wall cavity. It makes perfect sense when you understand why those things were written. For instance, the increase in nail length to accommodate the sheathing thickness. Well, of course, let’s assume that we’re in Arizona. I show one in class that was actually done just a year or so ago in Arizona. And there’s three-quarter inch Styrofoam put on the outside of the studs. Well, if you didn’t…and there is nothing else, so you had to nail the lath through the Styrofoam and into the stud. If you didn’t allow for this, add the thickness of that Styrofoam to the required length of the fastener, well, the stucco wall would fall off. Of course, you have to do that.
But here in our high-wind region, and around the Gulf Coast, and in Texas, and, you know, up the East Coast to a degree, we require structural sheathing on the outside of the wall. Literally, a structural sheathing, a rated, with a stamp, for structural capability. And meaning, it has withdrawal value. When you cover the wall with a structural panel, the whole wall is the framing member. So you don’t have to go find those studs. For instance, the roofer doesn’t lay his shingle down and then say, “Okay, I’m going to increase my nails. And I’m only going to put the nails through the sheathing and into the top of the trusses, and I’m not going to nail in between the two.” You see the fallacy of that. So, those things, that cracking, has led to a problem because of the weakness in our fastening patterns.
Then, the accessories are a problem. The plastic corner beads were originally made for block. They weren’t made to go on stucco. You have to fully encapsulate them with plaster. And it’s hard to do that. On a block wall, it’s not as hard because it’s right tight against the block corner. In other words, the thickness of the bead itself, if it’s pushed tight against the wall, forms the ground for the thickness of the stucco. But when you move those up on a framed wall, and you’re trying to bump those out seven eighths of an inch, which people do, not interpreting the standard correctly, and that is three quarters, and the standards say that, now you have huge pockets behind that. You can’t get them full. And then the beads crack at the corners. That’s what they’re supposed to do. Sacrificial. And the water gets in that cavity and fills up and just, it’s caused billions of dollars of damage.
The control joints, likewise, have to be integrated properly. And it would take more time than we have to discuss the different ways to accomplish that. But, sufficient to say that recent tests by two agencies tested the corner bead every way, excuse me, the control joints every way you could install them, attached, not attached, tied, attached one side and tied on the other, behind the metal lath, on top of the metal lath. Every way. And there was no meaningful or measurable difference in the crack patterns, regardless of how they were put on, including the panels that had no control joints at all. So, people don’t have, a lost a concept of what these control joints meant to us in the industries, and why they were used. Especially over concrete block.
We’ll shift now to a block wall. Remember, the standard is for colored cement. And that’s always an eighth of an inch, the final coat. It’s not part of the system, it’s the color coat. The standard says so. So, if you were to put an eighth of an inch color coat directly over block, when it dried, you would see every horizontal block joint, and every lenle [SP], and every downpour. Because, unless that colored stucco dries at the same identical rate by suction, then the…what dries quicker dries lighter. So, we have to put a base coat over a block wall. And that base coat has to provide a uniform suction for the color coat. So we require, over block, a three-eighths basecoat, leveled out, densified. And we let that cure, so that when we put the color coat over it, all the suction is uniform into that three-eighths base coat, and you’ll have a nice pleasing color all down the wall.
Now, we can’t do that without that base coat. Now, if you think of the second problem with the base coat, and go back in time. We were actually using cement and lime. And then…we would use white cement and lime, and use buff if you wanted a light cream color. If you wanted darker, we would use a half a bag of white cement and a half a bag of gray cement. You could mix that. So, you could change your base. You could change your color coat to whatever you wanted.
So, now, think of this. Go back to the base coat. And we’re applying gray cement, and sand, and lime. And I’m in the middle of the wall, and I’m what we call “running tops.” I am up on sawhorses at the top of the 8-foot wall, bringing it down to 4 foot. And my key mud runner is working beside me, and he’s running the bottoms. But he has to be over to the left, because I’m standing on sawhorse or scaffold here. So, there’s a zigzag in the wall. We run out a base coat. The labor brings a new batch from a new mixer load and then mixes it. And we start running it on. And we don’t see any difference with our eyes, but the mix had been mixed five minutes longer, and the lime began to air and train and he used a few shovels more sand. What we don’t see is the fact that we’ve changed the suction properties of the base, by that air and training of the lime in that change of the sand. It’s minuscule. You don’t see it at this point. But when you run the color coat over it, you’ll see that Z type change in color in the wall.
So, to alleviate that, we put these control joints right down the wall. They control the thickness, and they control the density for the color coat curing. And we fill those in. And the reason of their 144-square-foot placement is because if you take 144, the beads were originally half-inch thick, and you multiply 144 square feet times a half divided by 12, the answer is 6 cubic feet. That’s the size of a standard stucco mixer. So, that one mixer load would fill the area of 144 square feet. And the next mixer load would go into the adjacent one. And when there’s a vertical break, you won’t see if there’s a slight minuscule change in color. You only see that if they’re blended.
So, by then extending those up into the frame wall, which serves the same purpose for controlling those areas, if they’re not integrated properly, hence, the paper is put over their flanges, and the flange and the metal lath do not become one by pushing the mud through them, then the water that gets in along their vertical crack line will go right behind the paper, and that’s the worst place to have it.
So, those are the big three right there. First of all, the lack of the required face barrier. If you’re going to paint it, you have to coat it. You don’t get to just spritz some things on and change the color. Number two, you have to anchor the sheet correctly. And that requires at least two fasteners per square foot. It always has. And then, accessories should be considered on residential homes with 8-foot-high wall. The vertical ones should be eliminated. Most consultants agree on that. If you don’t, you can put them in. But you have to make sure they are put in carefully and correctly. And corner beads should not be used. You should rod the corners with a, we call it a stick. It’s a magnesium L-shaped piece of metal. It’s just a straight edge. And one person holds it, and the other builds the corner so that the corner is solid cement. If you do those things, you eliminate, you know, a lot of the problems we’re having.
To just expand quickly on that, the stucco contractor is faced with a dilemma. We have a lot of problems where the soffits are being run and they’re not pitched back uphill. You know, when I started in the trade, all of the overhangs were 2 feet. Now, we’ve moved them back, you know, to a foot, 6 inches. The wall gets a lot more water that way. But what also happens is that the soffit, when we change from a square cut fascia to a plumb cut fascia, meaning it’s vertical up and down for the ease of putting gutters. The water runs down that face, comes off the roof in mask, runs down the face, turns, because the old fascia we used in wood, we made sure that stuck down at least three-quarters of an inch. The new fascia is just an L shape, and it wraps around. The water will run literally back the soffit, if the soffit is not tilted upwards towards the wall, and get behind the stucco.
Additionally, the edge metal, if it’s not bent by the roofer when he’s put on, in a sheet metal break… Remember, that when you go to the store, any roofing supply or big-box store, and you buy it, it’s at 90 degrees. It’s meant to go onto a square-cut fascia, not a plumb cut. If you put that metal on a plumb cut, you have to put it in a break and change the flange angle. If you don’t do that, the metal creeps back up, forms a flat spot on the shingles, and this is ubiquitous. There are class action lawsuits all over this. The water then gets on the shingle and travels laterally instead of continuing off the roof, leaks, goes in behind the subfascia, to the bottom of the soffit, runs back to the wall, goes behind the stucco. So, those problems abound. And they are probably at least a third of all problems we see are related to the soffit or the roof. And we’ll include in that the 4 by 6, what we normally say is a kickout flashing. That intersection of a horizontal soffit and fascia into a vertical wall that’s higher, builders have said, in desperate futility, to say, “I’m going to slide a piece of waterproofing membrane in between where that fascia hits that wall.” All’s you’re doing is moving the rot area down 18 inches. You solve nothing in doing that. That interface has to be water tight.
And the problems almost exclusively are in the 4 by 6. To the point that we’re developing a newsletter now to just remind roofers, “This is how you’re supposed to make a transition…” Let’s call it a kick out. Most people will recognize that. “…with tongs that hooks on, that will be water tight.” If you don’t do that, if you just use the metal over the top, it’s going to leak and it’s going to rot the wood behind it. And we know that. We’ve known that in the roofing industry for decades. And yet it still is not done. And when you see it done… Literally a six grader could do it. It’s not difficult. But if it’s not shown, you don’t know. And that’s, of course, probably the biggest, is a lack of vocational training in our industry.
Bret: Absolutely, Bob. And I could listen to you talk about this for hours. There’s so much in what you said. There’s a lot of detail. And, of course, the devil is in detail. And you were covering this at, kind of a… Some locations are very specific descriptions, some areas were the 30,000-foot view. Which I find, you know, very interesting. Hopefully, people are following along with some of that. We could kind of break this whole conversation into probably several different podcasts.
Robert: Right.
Bret: But you’re right. I mean, it comes down to some of the basics, which are attention to detail, proper installation, and some of the key points you focused on were the paint, the proper attachment of lath, and the proper installation and use of accessories. In other words, just because they exist doesn’t mean you should be using them in certain locations.
Robert: And we did, Bret. We put all these details, non-proprietary, in CAD files that you can download at the Stucco Institute, free. Now, the Sealed Cladding System. We went in to the laboratory, the accredited laboratory, and got all the ASTM 330, 331, and the E74 test done on the models, and got a Florida product approval. And people say to me, when they use it, they love it, “Well, thank you for inventing this.” I didn’t invent that. That system is identical…it is the Miami-Dade protocol that was in the Miami-Dade code, that was, let’s just say erroneously, for not valid reasons, taken out. So I just redid the Miami-Dade code, which I had plastered under all my life, and took it into a laboratory and got it.
And although that does mention materials, I don’t want to mention any materials by brand name, you’re free to substitute. You can use any… For instance, your waterproofing coating. You could use Behr, you could use Color Wheel, you could use Sherwin-Williams, you could use Drylok. You can use whatever you want, as long as the properties of the waterproofing are met and they’re online. You know, you do, as an engineer and architect does, approve equals. Just substitute whatever you want. And it’s any brand of type S mortar. So, the CAD details are there, including the roofing and the flashing details, so that you don’t get lost. There is a place you can go, at least in our estimation, “These are the old details at work. Here they are. They’re free.”
Bret: That’s good to know. And like you said, these are time-tested. And for whatever reason, we went astray for a while. And it looks like we’re going to try to pull people back towards what’s going to work. And we also have to focus in on the fact that, you know, proper application of your coating, which is what we’re talking about here, face sealed system, is key. You know, you can’t put down 3 mils and expect it to work over the long term.
Robert: Right.
Bret: And then the other piece of that is the maintenance. I mean, yeah, we have coatings on there specified at 12 mils. That should get you a pretty decent life. But in Florida, after several years of the heat and the intensity of the sun, you know, you still need to recoat your system after five, seven, you know, or so years, depending on the product that you used.
Robert: That is correct. It’s very important that you realize that in Florida, with a face barrier system, any crack over a hairline needs to be addressed, you know? It’s not like where we see all these crack gauges and comparisons that were written for colored stucco, what is and what is not acceptable in the width of a crack and the number of cracks on a system that’s going to be subject to rainfall amounts of six tenths of an inch a month, and has an outside relative humidity of 30%. You cannot apply that same thought process to Florida, with a rainfall of 7.5 inches in that same month, and an average outside relative humidity of 85% and inside of 55%. Those cracks will let more water in than the system can manage, and the results could be disastrous.
So I tell my homeowners, “Look, after every high-wind event, walk around your house, use a binoculars, or a monocular, or anything, and look carefully. If you have any cracks, or you see a crack, get your painter up, or you get up on a ladder, and simply brush some replenishing coating in there to bridge that. Hairline’s okay, because they’ll close up. But you can’t allow eighth-inch cracks in the stucco system and survive in Florida.
Bret: Even a minor amount of water intrusion can add up over time, and then… Kind of pulling this back a little bit and help people understand better, the concept of vapor drive is it’s going to go from hot to cold, high humidity, to low humidity. So, the water in the air will drive through a wall. Then, depending on the perm rating of that wall construction, it will drive it into your home. That’s why you have to continually provide dehumidification of the interior of your house. If you don’t, the humidity will build up on the inside, and you’ll have mold and mildew issues, so…
Robert: That’s correct.
Bret: That’s why if you go outside and look at your HVAC condenser, typically, there’ll be a pipe near there that will be dripping water constantly. That’s the water being pulled out of your home. And that water comes in through opening doors and windows, but also through vapor drive. So, if you do have that hairline crack in your stucco and/or your paint, that vapor drive will occur. And if you allow it to continue over a long enough period of time, you’re going to degrade your cladding. So, another kind of analogy to put out there for people is, if you’ve ever seen petrified wood that was pulled out of a lake or a river, if the wood is underwater and has no access to oxygen, it can’t rot. Similar sort of concept. If you don’t let water affect your stucco, and the lath that’s embedded into your stucco, then you shouldn’t have any corrosion issues, as long as it was installed properly. So it’s really key to maintain that coating over time, and/or, you know, the cladding and coating in general.
Robert: That’s so true. Every word is true. We took a building. I had a request from several engineers, friends of mine. And they were across the nation. And they just were confused, dumbfounded of this old methodology. “What do you mean you didn’t put control joints in, and what do you mean you didn’t put weep screeds in, and you went from block…” excuse me, “wooden frame, and brought the metal lath right down over the block, and stub nailed it in and had one continuous coat? Why, that’ll crack, and you have no crack relief.” So, finally, I said, “Well, you know what? I’ve got a building I did 35 years ago. It’s in a coastal region. I have photographs here of it being stuccoed 35 years ago. It’s with black ungalvanized metal lath, was attached with standard staples. There are no control joints in it. There is no horizontal weep screeds in it. It’s one continuous coat of stucco from top to bottom. And, just like the Miami-Dade protocol, the thickness over wood is a half an inch. It’s not three quarters, it’s not seven-eighths, it’s a half an inch. And I did it 35 years ago. And it has been painted, in that 35 years, twice. So, let’s go cut it open.”
And we did. And I put it all online, 35-year-old stucco system, performing perfectly, with no control joints, no weep screeds, and only a half an inch thick with ungalvanized metal lath. So, we cut it, and all the photos are online. I told the guys, “You tell me where you want it cut.” And we’d cut it and look at it. And, Bret, it looked like the day that I put it on 35 years ago. We took the photos and said, “It looks identical. There’s no rust, there’s no nothing.” But, the first time when we coated it after we stuccoed it, we properly sealed around all of the penetrations, and we rolled. Nothing special. We just followed the instructions on the can, to the required coverage per square foot. Which is generally, you’re going to get about 100 square foot, 90 square foot, out of a gallon. And you do that two times. And that’s what we did. And it’s remained flawless.
So, as you know, as an engineer, more so than I, you know, things are predictable. Stucco, plaster, and cement behaves the same way if it’s done the same way. So why would it behave this way on this building and a different way on a different building? And that’s because of the coating and the details that were not done on the other building. Moisture passing through the system and condensing behind it is not good, as you just pointed out.
Bret: Right. Yeah, maintenance, design. Installation is obviously potentially an issue in any construction. But certainly, proper integration is key. Maintenance is key. It all works together. There is no one thing that’s the problem. And I think that’s a pretty good segue right now. I wanted to talk a little bit about, in the last five or so years, there has been some stucco litigation that has occurred. And I wanted you to touch on that a little bit. Because, in my mind, I think it may be the easiest thing to see as an issue, was the stucco being the problem. And I know that’s not the case. I think it’s a combination of all the things we’ve mentioned that, for whatever reason, just weren’t working, and someone wanted to point the blame towards stucco. Can you address that?
Robert: Sure. And you hit the nail right on the head. Somebody had to point their finger. Now, if you look at the reasoning behind that, 40 years ago, 30 years ago, if you called an engineer out and you said, “I have this problem,” the engineer would set up diagnostic protocols and say, “Okay, we think this is it. This is our hypothesis. We think this window is leaking.” They would set up protocols to test the window. They would find a leak. Then they would install a repair protocol, do that, and then retest it, and validate it, and say, “Okay, look. Although, it may not be happening, we’re going to extrapolate that to these other windows or this other condition, and let’s just get it fixed.” The goal was to get it fixed.
In today’s litigious societies, there are evaluations that are being done, not to analyze or determine what is the problem and what is the solution to fix it. It is strictly, “How do we document the largest potential violation, whether or not those violations are in any way related to what the alleged harm is, so that we can proffer the greatest amount of damages?” From the legal side, there is a percentage that goes to the legal team, so the higher the recovery, or damages, the more they make. And the ease for the person doing the evaluation is cut and paste, cut and paste, and charging the fee. Then they get money on the, what we call a back end of that, when there’s expert witness. When the defense, the contractor, and the stucco contractor’s attorney has to depose them, they charge huge fees for that. And that’s just part of the process.
But the people that involved is sometimes concerning. A lot of these lawsuits are born from a violation of Florida statute 553, that says, “If anybody violates the building code, then you have, any person injured by that basically has a right to sue that person in court, whether there’s privity or not.” The old way, the owner couldn’t sue the stucco contractor, because he had no privity. He had to sue the contractor, and the contractor would then enjoin. And that’s still done today. But this gives an owner a direct route at anybody if they violated the code. That’s only done, to my knowledge, in Florida. None of the other states do that.
So, here’s what happens. Well, if we can say the stucco is installed improperly, according to a reference standard, even though that reference standard may be interpreted different ways by different people, and even though it may allow that by its provisions of “unless otherwise specified,” I’ll go ahead and state it as a violation, and it has to come off. Well, wait a minute. What about the paint? Okay, why don’t we sue, and the painter? Well, remember, they’re suing under 553, a violation of the code. Guess what word doesn’t exist in the code? “Paint.” There is no requirements. You can get a CO on a block wall with no paint. You can just get a CO on bare blocks.
So, they can’t bring that person in. And if you think of the stucco over the frame, most insurance companies, well, all insurance companies say, to contractors, “We’re not going to pay for work you did incorrectly.” So, one would think, “Well, if the stucco man put the stucco on incorrectly, the insurance isn’t going to provide any money.” But there’s what’s called a rip and tear doctrine. If we can say that the stucco damaged something else, and we have to now remove the stucco to fix what was damaged, then the insurance company has to cover it. It’s called a rip and tear doctrine. So, now, we’ll challenge the spacing on the sheathing, we’ll challenge the ability of the staples to hold, now that the water has been in there, so that we invoke the insurance coverage.
Now, ironically, if you think of this… And I want to say this so that… I don’t want to mention anything specific. But let’s say that I am a builder and I am sued by somebody who said my stucco was bad, my weather wrap was bad, my flashing is bad, my windows were installed incorrectly, so on and so forth. And so, I’m sued for that. Well, what my attorney will do, my insurance company, will simply enjoin those other subs. And so, let’s say we have five subs. Each one of those attorneys for those five subs knows that even if they had a crystal ball, and could guarantee that they would win on a jury verdict, even if that were true, they’re going to go out of pocket probably at least $15,000. The insurance company is going to have to pay the lawyer, they’re going to have to attend the depositions, they’re going to have to pay for the transcription of the depositions. Then they’re going to have to go to court and be part of the process and get the verdict. So, even if that verdict was guaranteed to come back “not guilty” for the stucco guy, the out-of-pocket expenses to the insurance is at least $15,000. So, and that’s true for every sub.
So now, as a builder, I have five subs. I’m looking at the owner, who says this is $60,000 in damages. So, I go to my five subs and I said, “Look, it is going to cost you $15,000 to get out of this. I mean, it’s going to take you $15,000 to defend this, even if you get out ‘not guilty.’ So, look. Why don’t I take the risk out of it? You give me $10,000 and I’ll let you out.” So, I go gather up $50,000 from my subs. And now I go back to the plaintiff’s lawyer and I say, “Listen, you say it’s $60,000. Our experts say, ‘No, no, no. It’s not $5,000 worth of damage.'” And we banter back and forth. Then I say, “Look, I’ll give you $40,000 and you walk today.” So, they take the $40,000, and I just collected $50,000, and sometimes, $60,000 and $70,000. I make $10,000 or $15,000 off of the deal. So, it’s not really a big heartburn to me as the builder.
So, that has been happening. And the problem is the insurance companies now have started raising the rates, and the cost of construction is going higher because of it. Some of them aren’t even going to ensure the stucco contractors and the house wrap contractors. So it’s, the mess that that created, we’re now dealing with in a higher construction cost. So people now are saying, “Hey, let’s stop playing this game. Let’s find out what’s really wrong, and let’s get it corrected.” And many builders now are sitting up and taking heed and taking a proactive stance, to say, “Look, we don’t care what your expert says. This is what we’ll do to your house, and we’ll do it free of charge.” And most people will take that, because it really will correct their problems in most all cases, if they just properly clean, prep, and coat the building, and seal it up again. It’s really a “no harm, no foul,” in many cases.
Bret: Well, Bob, that’s a great segue into the last question, which is, what do you recommend we do as an industry to help improve the conditions on the ground for everybody? But, obviously, to promote stucco, which is, you know, it’s kind of a icon of Florida, I think. I love the material. I like the way it looks. It feels good, you know, it provides soundproofing, looks good. So what can we do as an industry to help get us past this time, and improve the quality of stucco?
Robert: Well, if you would’ve talked to me three months ago, I’d have probably given you a different answer. And the reason is simple, that our legislature just passed a law repealing all of the local competency card categories, in 2023. That’s the final date. So that means that we are heading to a date when there will be no requirement for a stucco contractor to be licensed, or a tile setter, or a framer, or a trim carpenter, or any of those trades. They will be able to work without licensure. And that’s going to present another level of problems that are going to be coming at us because of that.
So, the answer would be to, “Look, let’s get better training to the workforce.” Let’s do that. Let’s work with vocational education, which I think everybody’s on board now, “Hey, we need to reinstate this in our schools.” But, you know, you can go to almost any school and find a plumbing, an electrical, or a mechanical course. Those are what we call easy-peasy there. But where do you go to learn to be a block mason? Where do you go to learn to be a stucco contractor? So, we need to figure out a way to get these in the vocational schools, number one. Number two, we have to increase the licensure requirements. Let’s increase the requirements to get a stucco contractor’s license. Let’s develop a real and accurate competency test, so that they know how to put these systems on, and understand weatherproofing and waterproofing as a whole, rather than just their little segment. So, we need to increase that.
So, that’s all we can really do, unless there was some major change to where insurance, let’s say, were no longer, they’ve talked about this, no longer to become a requirement for subcontracting trades. Well, now a builder is going to say… Not all builders do this, so don’t I want this card blank, but some builders only look at the bottom-line price they get. And whatever is the best price is what they’re going to take. They rely on the fact that that subcontractor has insurance, and they make them sign an indemnity agreement in their contract, to indemnify them, so they really have no exposure. If that were removed, and subcontractors were not required to be insured by law, then the contractor might say, “Listen, it’s not a matter of money. I want to know that you do your job right, and when you leave my job, I don’t have to worry about suits.” So, from my classroom teaching, those are the three variables that we get. Increase the training in vo-tech, increase the minimum criteria to get the license, and thirdly, eliminate the requirement for subcontractors to be protecting or indemnifying the general contractor. Let the general contractor carry his or her own insurance, and let them negotiate and find the best subs. I don’t know if that’s the answer, Bret, but that’s what I hear from the people in class the most.
Bret: Sounds like a good start to me. And I want to kind of go back and circle back to what you said earlier as well. You know, the recommendation would be, I think, what we can do today on the ground is make sure you pay attention to the devil’s in the details, because it is. Make sure you detail around your penetrations through your wall properly, so that you can apply a proper sealant bead. Apply the proper mil thickness of your coating. Make sure your accessories are installed properly as well. But, basically, just focus on quality workmanship. But key in Florida is, ultimately, for Sealed Cladding System, you have to do the sealant and paint properly, otherwise you’re going to have areas that are going to be compromised because cracks open up in different areas, whether it’s accessories or in the stucco itself, and that’s going to allow bulk water to come behind your system.
Robert: Very well said.
Bret: So, Bob, wow, this has been really a great talk today. I appreciate you being here. In closing, I want to thank everybody else for listening today to our podcast. Bob, if the listeners want to reach out to you and your team, what’s your website address, and what’s the best way for them to contact you?
Robert: You can reach me at the contractorsinstitute.com. Just click “Instructors,” and my picture and email is there. Or stuccoinstitute.com is the same. Or I have a direct email. It’s robertk@koning.com. That’ll come directly to me.
Bret: Okay. Thank you, Bob. We’d also like to invite the listeners to take a further look at GCI Consultant Services at our website, which is GCIconsultants.com. You can also reach us at 877-740-9990, and we can discuss any of your building envelope needs. Want to thank everybody else again. Look forward to talking with you the next time on our “Everything Building Envelope” podcast.