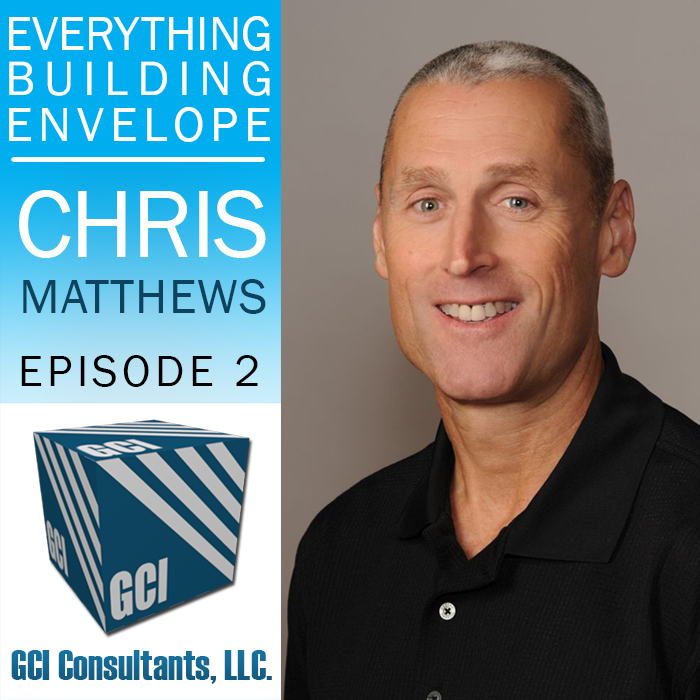
About The Everything Building Envelope Podcast: Everything Building Envelope℠ is a dedicated podcast and video forum for understanding the building envelope. Our podcast series discusses current trends and issues that contractors, developers and building owners have to deal with related to pre and post construction. Our series touches on various topics related to water infiltration, litigation and construction methods related to the building envelope.
https://www.everythingbuildingenvelope.com
*** Subscribe to the show and leave us a Review on ITunes!
Paul: Welcome everyone to Everything Building Envelope, Paul Beers here. And I’m really excited today to have as our guest, Chris Matthews, who I work with at GCI. And we’ve got a really interesting topic today, which is waterproofing exterior walls. It may not sound so interesting, but it’s pretty complex and there’s a lot of different items that I think our listeners will be very interested in that we’re gonna discuss. Chris, we’ve worked together for quite a while now.
Chris: Quite a while, yeah.
Paul: Yeah. And so, I remember when you came to work for us, you actually…had relocated up to Atlanta when we were trying to establish the Atlanta market, which we have done. You know, obviously we have an office in Atlanta now and you still go up there quite a bit.
Chris: Quite a bit, yes.
Paul: Yeah. So, it’s been a long and fun relationship working together. So, Chris, why don’t you just give us a little bit about your background and basically what you’re doing for GCI these days.
Chris: Well, I came into the construction industry right out of college and went to work for a large glazing contractor. So, that’s my background, is in the glazing end of things, and then evolved into other areas of the building envelope, then I joined GCI in 2002 and I’ve been working in the exterior envelope consulting arena since then. Been in the business now for 30 years. I remember when I started I’d go to meetings and, you know, the old guys would say, “Oh, we’ve been doing it this way for 30 years.” You know, 30 years was the magic number and now, unfortunately, that’s where I’m at. Hopefully, I’m a little more open-minded than some of those old-timers were.
Paul: Yeah. Please tell me you’re not doing what you were doing 30 years ago.
Chris: No.
Paul: So, let’s talk about waterproofing exterior walls. You know, when I think about that there’s two primary kinds of construction that we typically see, the what I’ll call masonry, which is a concrete frame with concrete CBS or concrete block infill. And then of course what’s probably a lot more of out there is the framing and sheathing type of systems, and it could be, you know, metal studs or wood framing or whatever.
So, is there differences in how you would waterproof those types of applications?
Chris: Yes. We see a lot of both types of construction and there are definitely very different approaches as to how to construct those walls, design those walls properly to prevent water infiltration.
Paul: So, let’s talk first about the masonry construction. I know, you know, and I hate to admit this back in the ’80s and ’90s when I was a window installer, they would erect the system and they would, you know…we would put the windows in and they would stucco and paint and caulk and we’d move on. And just there’s a lot of mass there, there’s a lot of stucco and concrete for water to get through before it gets to the inside of the building. And that generally I think was effective, but is that enough or do you think that maybe…or what’s being done nowadays as compared to 30 years ago?
Chris: Well, sure, and I remember the same type of construction you described. And there are still people who ascribe to that method and wanna do it that way. I think what we’ve learned over the years is that when you’ve got extreme climates, extreme weather situations, you do get water in around window and door openings. If all you do is paint the stucco and apply a beta sealant between the window and stucco. So, what we do now is…what we recommend is to try to address that opening before stucco is installed, before windows are installed, and install a fluid-applied waterproofing around the perimeter of the rough opening to provide a waterproof substrate at that opening.
Paul: So, when you say around the opening, is that just inside the infill where the window goes or does that go out on the wall, how far, you know…what’s the particulars with that?
Chris: Yeah. We go around the perimeter of the opening and typically we like to see it turned out 4 to 6 inches out onto the wall around the opening.
Paul: And why is that important?
Chris: Well, you can have cracking, you can have…any opening is a hole in the wall, so you can have a lot of imperfections and materials coming together there. So, we like to turn that out and waterproof that whole area so there’s no paths for water to migrate in around the opening.
Paul: So, then what?
Chris: So, once that waterproofing’s installed around the opening, the next step is for the window installer to come and start installing the windows and the doors. Those are installed with a proper space around the window between the frame and the CMU wall. And then the…
Paul: I’m sorry to interrupt, but what’s a proper space?
Chris: We like to see a minimum of three-eighths inch. A lot of jobs are designed either with more or up to a half inch, because construction materials vary. So, all the sealant manufacturers’ materials are designed for a minimum joint width of a quarter inch. But if you design a building to a quarter inch it looks fine on paper, but we all know out in the field materials vary and you can start to get joints that are too thin and don’t perform properly over time. So, we’d like to see a three-eighths to a half inch joint designed.
Paul: And so, that sealant joint, what kind of sealant do you typically use there? Do you have to use primers, you know, bond breakers, all that kind of stuff?
Chris: Well, we’d like to see a high-quality silicone sealant. It’s the most durable, it’s the longest lasting, and the best performing for the building over the long haul. And yes, we recommend preconstruction adhesion and compatibility testing of the sealant to all of the contact materials. But in this case, it would be the waterproofing material and the aluminum window frames, and then field adhesion testing as the sealant is being installed to verify that we’re getting the adhesion and performance that we need.
Paul: So, who would do this field adhesion testing?
Chris: Well, we can perform the field adhesion testing or the local representatives of the various sealant manufacturers can come and perform the testing, and we’ll be there and witness it.
Paul: Now, if a sealant manufacturer performs the testing, what do they charge for it and then do they, you know, just call it good and walk away or do they provide any documentation? How does that all work?
Chris: It’s a free service. So, definitely, something that should be done on every job. And the manufacturers provide an actual test report with a pass-fail rating on each of the substrates that the material was adhered to. And if there is a problem they will get involved and provide further testing and recommendations for what needs to be done to get proper adhesion. So, it’s a valuable process that costs nothing and definitely, we recommend it to be done on every job.
Paul: Sounds too good to be true.
Chris: Exactly. Right.
Paul: Okay. So, basically our window’s roughed in, it’s sealed to the structure, then I guess stucco?
Chris: Yes. Then the stucco is installed and the typical detail is for the installer to rake a groove…to return the stucco back toward the window. Not in contact with the window, rake a groove at the perimeter and then the stucco’s painted, finished in whatever manner it’s going to be finished. And then a second sealant joint, some people call it a beauty [inaudible 00:09:02] is installed between the window and the finished stucco to complete the installation.
Paul: And you mentioned that the stucco should not be touching the window frame. Why is that important?
Chris: Well, the stucco is a cement-based product and cement and aluminum don’t get along well. If cement and the aluminum frames are in contact over long periods of time and water’s added, which obviously would be at the exterior of the building, the cement-based stucco can corrode and break down the aluminum. So, they have to be separated, not just stucco and aluminum, anywhere that aluminum frames would be in contact with any cement-based material, there has to be separation or isolation.
Paul: Have you seen instances where maybe it wasn’t done, you know, they way that’s recommended where the stucco has contacted the frame?
Chris: Yes. Yeah.
Paul: And what happens?
Chris: You know, it’s a major problem for the project. It takes some time, you know, you’re not gonna see major results in three, four, six months, but after a few years of contact there can be major corrosion and breakdown of the aluminum to the point that you may have to replace everything.
Paul: Sounds expensive.
Chris: Yes. Definitely.
Paul: For something that’s really simple, right?
Chris: Simple. Yeah. It’s just a matter of an installation method and some materials, films, fillers, something to separate the stucco from the frame when it’s originally installed.
Paul: So, you know, the other type of construction that we’re talking about is the frame construction, I’ll call it. When I say frame, you know, people I think always think wood, but that could be metal studs just would be the…conceptually it would be a similar difference, same difference from a design standpoint, wouldn’t it?
Chris: Sure. Yeah. And you see a lot of the heavy gauge steel studs in bigger buildings, taller buildings, commercial buildings, versus the residential application. But we see both wood frame and steel stud framed all the time.
Paul: And then these framing systems would have a sheathing applied over it, which could be some wood-based product or some sheathing typically, correct?
Chris: Yeah. The three types we typically would see would be plywood sheathing, oriented strand board or OSB sheathing, and then in your steel frame construction, it’s typically a fiberglass-faced gypsum sheathing.
Paul: Yeah. And when you say fiberglass-faced gypsum sheathing, is there a paper-faced exterior sheathing available?
Chris: Well, yes and there was a time when that was the standard in the industry, but it has virtually no resistance to water. So, the fiberglass-faced products are much better at handling incidental water and preventing breakdown of the sheathing.
Paul: And most people are using them these days?
Chris: Yes. Yes.
Paul: Even though they may be a little more expensive?
Chris: It’s more expensive, but it’s widely accepted in the industry that that’s required. So, in the construction documents and in actual buy out of materials we see the fiberglass-faced used almost everywhere.
Paul: And then so, you know, with the exterior wall systems they could be clad with, I’m sure, different things like stucco, brick, wood siding, metal panels, stone, lots of different things, right?
Chris: Yes. Yes.
Paul: So, what keeps the water out in these kind of systems?
Chris: Well, in this type of system you have to design the construction and the wall details with the assumption that water’s going to get behind the different types of cladding systems that you described, brick, stucco, siding, panels. Every one of these, water can and in most cases will get behind that exterior cladding. So, the wall has to be designed to handle that moisture and there’s a weather resistant barrier, a WRB installed over that sheathing, both sheet type materials, wraps that people are familiar with, and then another option are fluid type weather barriers, fluid applied weather barriers.
Paul: And before we talk about them, just very briefly I just wanna touch on the fact that, you know, we’re talking basically about a drainage-based system. There’s also…you know, and they’re not very popular anymore I think because of a lot of failures, you used to see a lot of barrier systems. And can you just tell us the difference between what we’re talking about now, the drainage system and what a barrier system is?
Chris: Yeah. A barrier system in theory, on paper, it’s not that bad. If you’ve got a material that has a waterproof exterior plane and you install that on the building, and in a manner that you think no water will ever get behind it, it’s like a glove on the outside of the building and everything’s good. The problem is joints breakdown, there’s cracks, there’s penetrations, there’s other paths that people didn’t anticipate water getting behind these barrier-type systems, and once they did the material did just as good a job of holding water in as it did holding water out.
So, now you’ve got water behind that material, held in up against materials back in the time when these were most popular like these paper-based gypsum products we talked about. And you can have, you know, just catastrophic damage to the building. So, the barrier system, in theory, can be good and there’s still times, like you said, when it can be applied and done effectively, but by and large, we see the jobs designed with a drainage-type system that anticipates some water behind that exterior wall cladding. And with flashings and weather barriers installed in a manner to control it and get it back out of that system where it can’t damage those walls.
Paul: So, tell us about some of the different types of weather barrier systems that are predominantly being used these days.
Chris: Well, you know, kind of the old school is just the asphalting building felt, you know, they’ll see it in Home Depot in rolls and they put it on shingle roofs. But it’s just an asphalt impregnated building paper and it can work as a weather barrier. It’s got some weaknesses in that it doesn’t hold up well out in the sun and weather prior to the exterior wall cladding being installed. It’s easily torn. So, there are some potential problems with that.
You got the wrap-type of weather barriers, which is the most popular I think especially in your single family residential, that type of thing. There are some big names in the wrap type of barriers that people are all real familiar with.
Paul: Like Tyvek?
Chris: Tyvek is probably the most familiar. It’s like a Kleenex, you know, some people call it a tissue or Kleenex. A lot of people call any type of wrap Tyvek. So, most people are familiar with that and then what we see gaining more popularity and that we’re big advocates of, are fluid-applied weather barriers that are actually rolled or sprayed onto the exterior sheathing to provide that protection before the wall cladding goes on.
Paul: And why do we like that better than the sheet materials?
Chris: Well, there’s a lot of benefits to that. One difficulty with the sheet materials is sequencing in that everything on…the control of the water and the drainage of the water out from behind the cladding is so important to the longevity of the building. And to do that, everything has to be shingle lapped with each successive higher area lapped over the lower area, so that water flows down to a flashing location and out just like on a shingle roof. Each level moving up the roof is lapped over the layer below.
That can present a lot of difficulties, because of sequencing during the construction process, in that certain things may be installed before or after the wrap and creating conditions where those materials aren’t easily lapped in that manner. And where there are paths for water to get behind that wrap type of barrier. So, we’ve seen a lot of buildings with failures where that’s the problem, not that the wrap is not performing, but that there were paths for water to get behind the wrap and then cause damage like we talked about earlier.
So, the fluid-applied eliminates that issue. You can roll or spray on your main layer of the material and then if you’ve got to add something else, oh, I forgot, or sequencing or whatever, and you’ve got a condition with a negative lap, you can just add more of the material and resolve that. The other thing that we like about the fluid-applied is even if somehow water gets through it, behind it at a specific location, everywhere else it’s still adhered to the sheathing. So, you don’t have water running down behind the material and causing damage, you know, as gravity just pulls it down behind like we’ve seen so many times behind the wrap types.
Paul: And I’ve also, you know, seen and heard that another advantage of it is that you can color it so that you can actually when you do an inspection, you can confirm that you’ve got good coverage, because let’s say it’s yellow, you know, and you just make sure that there’s yellow everywhere.
Chris: Exactly. Yes. And they design it, just like you said, and the different manufacturers have their different colors, but they design it so it’s pretty much fool-proof in that if you see something reading through then you don’t have it on thick enough. But if you’ve got a constant, continuous color, whatever it may be, you know you’ve got the material installed adequately.
Paul: So, you know, as we’re doing this podcast and it’s…the construction industry is very busy now. You go through any city in the US and you see cranes and construction crews and whatnot. And, you know, so you’ve mentioned fool-proof and how does that help in times when it’s really busy out there?
Chris: Well, you definitely wanna make it as simple as it can be to get it right because there are so many materials coming together at the exterior wall and each of those materials taken on its own is probably very good. But there are so many joints and connections and intersections between all of these materials and in busy times there’s…people are spread thin, there’s not as much supervision, there’s maybe not as much experience in the actual installers, so you wanna make things as close to fool-proof as they can be to prevent all of those joints and transitions from becoming a problem.
Paul: So, in an exterior wall system, you know, I know one of the big problems there is can be openings in the wall system, windows, dryer vents, you know, hose bibbs, light fixtures, what kind of special attention needs to be paid in those areas? And I guess let’s talk about window openings first. What do you have to do in a window opening?
Chris: It has to be flashed properly with whatever type of weather barrier you’re going to use. The typical flashing materials for window openings in frame-type construction is an adhered membrane of…people call it a peel and stick, flexible type flashing. And this has to be installed properly around the window opening or any of the penetrations that you talked about, dryer vents, door openings, whatever the hole in the wall may be. It needs to be flashed with a peel and stick type material that ties into the weather barrier and creates a continuous protection, a continuous plane that won’t allow water behind the barrier, like we talked about earlier, or in at the holes in the walls that all of these penetrations create.
Paul: And you say it has to be done properly. Who provides the information on how to do it properly? Do you see it in construction details or do the installers just know how to do this? I mean, how does this happen so that it gets done properly?
Chris: Well, I see more and more now where architects are trying to address the proper flashing of openings and penetrations in their drawings. And we certainly assist when we’re doing design assistance work with trying to get those details right, but there are a lot of very fine details in getting that right. And so, it’s a difficult thing to draw and show properly. So, what we like to do is get out there and work with the people who are going to be installing this. And get the first of each of these type of openings and work it through, and have everyone agree that this is the proper way to install it and this is the way we’re gonna do every one on this job.
Paul: So, let’s just talk about that a little bit, the sequence of events. You know, let’s say that we’ve got a set of plans that may or may not show how to do this or how to do it properly. What happens from that point forward? There’s contractors, subcontractors, we’re ready to go, what do we need to do to make sure we have a successful installation?
Chris: Well, we like to get those plans right. Most jobs, they are right. Some of them may not be, but regardless you got to get that…that’s got to be communicated to the field, to the people out actually installing this stuff. So, what we like to do is get those groups of actual installers together and get them out on the job, and we’d like to see a mock up of some type constructed to where we’ve got the various conditions and materials that we’re going to be installing on this job and we just work it through. Because let’s face it, no matter how good those drawings are, a lot of these guys may never even see the drawings. And we’ve got to get out there and show them this is the way it has to be installed if we want this building to perform like it needs to, and here’s a mock up of window openings, penetrations, balconies, doors, whatever it may be. Here’s how we’re going to install in all those conditions and once it’s done, this is our reference point for the job.
Paul: You said windows, doors, penetrations, balconies, how do you get all that covered? You have to do…you know, does one mock up cover all or sometimes you have to do more than one mock up?
Chris: Yeah. I’ve seen some…and we’ve been on some projects where…and it could be a real process to try to put together a mock up plan that incorporates all the details on a project. So, we’ve had some that were very elaborate mock ups with a balcony and various wall claddings and window and door types or, as you said, you may have to do several different mock ups of different wall conditions and balcony to wall conditions. You know, and they could be very elaborate or they could be a series of more simple mock up details. And some of that may depend upon whether it’s going to be also an aesthetic mock up that really shows people how the building’s gonna look, which is not our big concern or if it’s just gonna be a functional type mock up, then it doesn’t really matter how pretty it looks.
And, you know, we’ve done balcony mock ups in the back of a pickup truck to get the details right.
Paul: Do they ever do these mock ups actually do it in the building?
Chris: Yeah. That’s a good point. Yeah. So, a lot of times depending upon the schedule or the, you know, site conditions, dollars, it may be that we just take maybe a corner of a building or a specific unit and accelerate it and get all the materials there and build an in-place mock up that then doesn’t have to be torn down. All the money’s going toward the end construction then.
Paul: So, when you say in-place mock up, does that mean…well, let me ask you this first. When should that be done?
Chris: Well, the earlier the better. We’d like to see a standalone mock up built and I bet on many jobs where the standalone mock up is built and we’re out there working on the details and they’re just, you know, starting to come out of ground with the walls. But if it’s going to be an in-place mock up it’s got to the first of each of whatever it is, window opening, door opening, balcony, it’s got to be the first one on the building. And like I said, we like to get the trades there a little before they’re ready to just run with their product installation. So, we can accelerate all those together in this one area of the building and get everything worked out up front.
Paul: So, you know, we do that and then how do we know if it’s gonna actually perform or not?
Chris: Well, what we wanna do is test it. We wanna do water infiltration testing, which is a big part of what we do. We like to test those mock ups whether standalone or in-place with an ASTM test that simulates a wind-driven rain. So, we think we’ve got it right, everything looks right, we’ve got it all installed, let’s test it now and make sure nobody overlooked anything, everything’s performing like it should. We like to do flood testing on the balcony waterproofing in these types of buildings.
Get water out there, test it, and make sure that our plan is solid and we’ve got a good path to move forward with the construction.
Paul: When you do these tests do they usually pass?
Chris: No.
Paul: You can say it. [crosstalk 00:30:02]
Chris: Yeah. Yeah. You know, sometimes they do, but, you know, a lot of times there can be installation problems. You may get everything installed properly, but something didn’t get…something with the window itself maybe was left out or a problem with it or some other issue that nobody even foresaw in all these installation details. So, you know, typically, you’re gonna get some leaks in those early tests and you’re gonna kind of work through that process to get things resolved.
Paul: So, when you say work through that process to get things resolved, you know, I’m assuming you do repairs and then you keep testing until you get it.
Chris: Yes. Yeah.
Paul: And what happens after that to make sure, you know…so, you’ve got one window that you know isn’t gonna leak, how do you make sure the rest of the job is gonna perform at that point?
Chris: Well, what we like to do is then conduct regular inspections throughout the installation process. So, we’re coming back on a regular basis, because we all know things can get off track, you know, different people can be on the job, someone can get confused as to what the details were in that mock up, whatever it may be. We wanna continue to inspect through that installation process and make sure that everybody’s still performing the way they were when that mock up was done. And then, we like to do some confirmation water testing as the installation continues also just to…as another way of verifying that everything’s still being done the way it should.
Paul: And when you do these confirmation tests, do you sometimes find…I mean, do they pass or do you sometimes find, you know, maybe there’s something going on that would have otherwise been missed?
Chris: Yeah. I think, you know, certainly more of those pass, because you’ve worked through some of those initial problems, but we still certainly see sometimes when there’s failures in those types of tests, where like I say maybe somebody’s screwed something up from what our original plan was to the current point or maybe we’ve got a different condition that no one foresaw in the mock up phase, some kind of a variation that’s causing some issues that we find during a test.
Paul: When you do these tests, you know, in the middle of a job or the end of a job, how do you know that that particular area hasn’t been given special treatment by the contractor just to make sure that they pass the test?
Chris: Well, and that’s certainly a concern. And we try to avoid that by selecting openings randomly. So, you know, obviously everybody knows a test is coming. Hopefully, everybody is installing every opening properly, but we’d like to have an area of the building where there are several openings and we can pick some randomly to represent what’s really going on, not as you said something that’s been kind of beefed up to pass a test.
Paul: And then with the testing…you know, what’s the ultimate goal with testing as you’re getting towards the end of the project?
Chris: Well, at the end what we’d like to be doing is coming out there and everything we test is just passing the first time. And that’s what we always recommend, is we wanna get to a point where we can pick any opening and we can test it and it passes the first time we test it.
Paul: And generally, you’d feel pretty good about things at that point?
Chris: At that point you do. Yeah. Sure. Nothing is an iron clad guarantee, but when you come out there and you’ve got several successive tests that passed on the first time, everybody has got a pretty good comfort level then at that point.
Paul: I know I’ve worked on projects before where, like, big buildings, you know, we’ve gone through this whole series and the testing went well and everything, and then they get hit with an extreme weather event after the fact. And I can remember one client in particular calling me up and saying, “You know, there was a big storm, tropical type storm,” and I can remember the owner calling up and saying, “I’m so happy I only had four leaks, you know, whereas if we hadn’t done the testing the whole building might be flooding.”
Chris: Right. Right. Yeah. Right. And if someone like that has been there in the beginning and seen that first test when maybe there were some problems, and they’re kind of doing the math in their head and saying, “Well, if we hadn’t done that, that could have been at a thousand openings.” And so, four is a pretty good number in an extreme event.
Paul: So, Chris, thanks so much for being a guest on Everything Building Envelope. I know that this…you know, the weatherproofing of exterior walls is a very interesting topic to a lot of our listeners. So, I hope that we’ll be able to get you back for some more episodes. I know there’s a lot of things that we can talk about with your expertise and that we can dig deeper into.
Chris: Yeah. Sounds good. I’d be happy to come back any time.
Paul: So, with that we’re signing off. Thank you everyone for listening to Everything Building Envelope and we’ll talk to you next time.