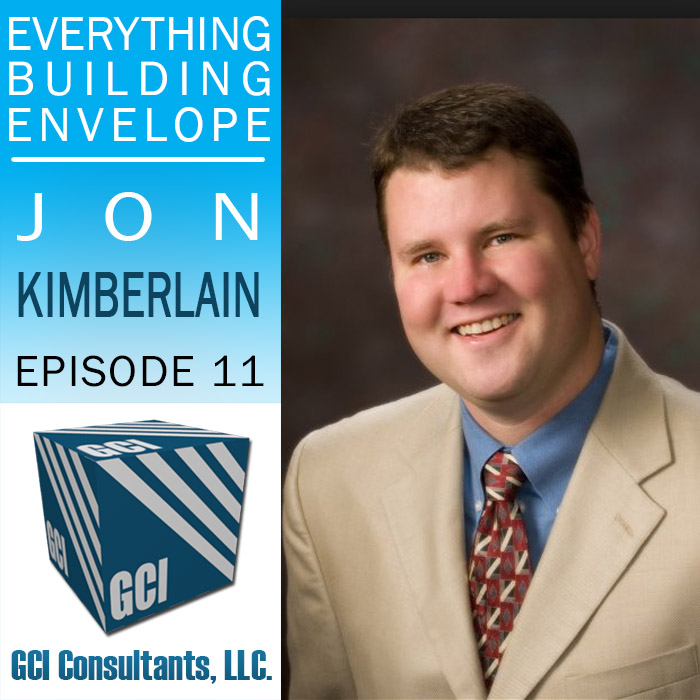
About The Everything Building Envelope Podcast: Everything Building Envelope℠ is a dedicated podcast and video forum for understanding the building envelope. Our podcast series discusses current trends and issues that contractors, developers and building owners have to deal with related to pre and post construction. Our series touches on various topics related to water infiltration, litigation and construction methods related to the building envelope.
https://www.everythingbuildingenvelope.com
*** Subscribe to the show and leave us a Review on ITunes!
Paul: Welcome back, everyone, to the Everything Building Envelope podcast. I’m very excited today to have as our guest, Jon Kimberlain with Dow Corning. Jon, welcome to the podcast.
Jon: Thank you. It’s an honor to be invited and speak with you today.
Paul: Yeah, well, I know you’ve got lots of good stuff that the listeners are gonna be interested in. So before we get into that, why don’t you just tell everybody a little bit about yourself and your background and we’ll go from there?
Jon: Sure. Thank you, Paul. Hi. My name’s Jon. I am a Senior Application Specialist at Dow Corning. I’ve been with them since 1999. And worked in several different roles, all related to sealants and materials that are used in the high-performance building industry. I’ve been out in the field since about 2004 working as an Application Specialist and helping people design and fabricate buildings using silicone sealants. I’ve written several papers on different aspects of performance of the sealants and contributed to several industry guideline documents like the GANA Sealant Manual. I used to build houses with my father when I was younger, and I’ve never stopped wanting to participate and figure out how things work in the building industry since.
Paul: Great. I think most people know this but for those who may not, can you just talk a little bit about Dow Corning?
Jon: Sure. Dow Corning is a fully owned subsidiary of Dow Chemical. It was created in 1943 when scientists at Carnegie Mellon actually discovered a unique property of silicone polymers. And in trying to figure out what to do with those, they created a joint venture between Dow Chemical and Corning Glass and found uses for silicones in military applications and health and beauty care and construction. And continues to this day, as a very innovative company in the use of silicone materials in everyday life.
Paul: So we’re gonna talk about silicone sealants today. Can you just sort of tell us about what that encompasses as far as the sealants themselves and complimentary materials?
Jon: Yeah, I’m happy to do that. We have several different sealant types, things that are used in weatherproofing that are specific to substrates like masonry and stone versus aluminum. We have structural glazing sealants that are both one and two-part that allow people to either build glass buildings in the field or in shop. And then we also offer complimentary products in things like primer, which enable faster adhesive build in these applications. As well as architectural coatings to help prevent through water penetration on things like EIFS and stucco.
Paul: So from where I come from, it’s good to have everything coming from the same family and even the same manufacturer, because it gives you a better chance for kind of a comprehensive solution. So with the sealants… So let’s just talk generally about silicone, first of all. What are some of the benefits of using silicone as compared to maybe some of the other options that are out there?
Jon: Well, what’s interesting about silicone sealants is that they are highly durable. And the first ever use of a silicone sealant in a weatherproofing application was actually in 1958, and it was in a building in the Midwest that was exposed to high cold temperatures, a lot of snow, a lot of rain and a lot of sunlight positioned on one of the Great Lakes up there. And that material was actually removed in 2013, not because it had failed but because the owners of the building wanted to update the look of the façade. And so we were actually fortunate enough to get some of that material and take a look at it. And it was still elastic, it was still stretchy, it was performing as intended. What we did find what was interesting is that in the few areas that had failed, it was actually an application issue where the material wasn’t applied as it should. You could almost imagine that somebody was taking and putting the sealant on there and using their thumb to tool it into this weatherproofing joint.
So really, the durability is one of the calling cards of the silicone sealants compared organic materials which had a tendency to weather and lose its performance characteristics over several years to maybe a decade or two.
Paul: I just counted on my hand and it sounds like it was over 50 years old when it was removed.
Jon: Yeah. Dwight D. Eisenhower was the President when this material was applied.
Paul: Wow, wow. You know, you just reminded me of something, one of my pet peeves. You said that somebody might have tooled it with their thumb. I know this is kinda jumping around a little bit, but that’s really not the way you’re supposed to do it, is it?
Jon: No. And it was interesting because we did a literature review for this paper. I have a friend Brett, with WJE in Chicago. And they have a great library of historical documents. And we had several historical documents. And what was interesting is we didn’t see a whole lot of industry guidance of how to apply materials. And I think over time, one of the benefits of the longevity of this material, we’ve seen things like ASTM and GAMA and these other organizations develop procedures and processes to design into all materials in an appropriate way.
Because even though the amount of material that’s going into these applications is minimal from a volume and price, they play a critical role in the performance of the building, not only in year one but later on down the line in trying to prevent water, and it helps with energy for seeing also that you have don’t have uncontrolled air losses and things like that. So yeah, it was interesting to see the history of how this material was applied and imagining what people were actually doing and just trying to slap it on there in some instances.
Paul: Well, bad news. They’re still doing it, I think, in some instances. And you know that probably better than anybody. You’re a field engineer so I assume that you go out and see some projects maybe that are in premature failure. Is that right?
Jon: I don’t have any projects that have issues on them at all. Everything is roses. I’m kidding.
Paul: That’s good. That’s good. That’s Utopia.
Jon: Yeah. It’s interesting. And this is like…you know, I mentioned that I used to build houses with my dad. One of the things that has kept my interest in that is that you run into situations where things were not designed properly, or installed properly. And you’re developing kind of this forensic analysis on where things went wrong has been a part of why I enjoy doing what I’m doing, and get to see the various problems associated with it. And I think from what I’ve seen typically, it’s really where the applicator doesn’t follow the published procedures or follow the design via the project drawings, is where a lot of the challenges come in.
Because it seems simple that we’re just putting caulk up on a building, but, you know, a lot of this is really high end stuff, the chemistry involved in making sure it’s compatible with the different substrates and the different primers that may be needed, doing things in the order they’re supposed, like, putting the backer right in after you prime the surfaces. I mean, all these things are important and require a high level of degree of mechanical ability.
Paul: So basically, you just covered the point I was trying to get at is that the failures, probably not always, but almost always are application related, not something’s wrong with the material.
Jon: Yeah. And some of that too is…as Dow Corning, we have always offered up the ability to have blueprints provided to us or our project drawing. Especially important in the structural glazing applications where we have to have these drawings to review to ensure the material is a sufficient dimension to carry loads. We also take a look and make sure the weather seals look appropriate as far as minimum recommendations. Really, I think that kinda helps facilitate that design process to ensure, at least on paper, things look like they’re working like they should.
Paul: So let’s go through the process, say for weather seals on a new construction project. So the first thing you would have to do, I think, is select the proper material to the application. So why don’t we start with how one would go about doing that and then what happens along the way as far as making sure that it’s gonna be…you know, the joint design is proper and it’s gonna stick to the substrate and all those kind of things.
Jon: Okay. So, in our technical manual, we actually have a list of several different substrates and the different sealants that we offer as part of helping select what material may be the best choice for the substrate. And it includes things like, how do you clean the surface, whether it’s solvent or personal brush and dust? And then typically, if a primer’s needed. And so that would help guide an architect or a design engineer in selecting that. And a lot of times, we have materials like Dow Corning 790 which is very good with cementitious-based products like masonry, stone, things like that. Where if you’re looking at 795, it’s probably more appropriate for glass and metal.
So being able to use that chart can help you select which material is needed. And I think the most obvious next step is that a mockup needs to be built. Because we don’t have control over the substrates that are used in the field. And a lot of substrates can be highly variable. I mean, not all the concrete is the same mix from region to region and even just locally. And not all the surfaces of the metal are consistent. So it’s really important to ensure that the sealant’s gonna stick to the material and that’s it’s supposed. And that’s accomplished through a field adhesion testing on the mockups.
You can also actually submit samples of the substrates to us and we can do testing in our laboratory as part of this warranty process for the weather seal applications. And we can help validate whether the sealant’s gonna stick to it, whether primer’s needed. You know, are you gonna do this bristle, clean this with bristle brush and dust? Or is it gonna require a solvent? Those types of things.
Paul: We talk about adhesion testing. There’s also issues with compatibility science with some of the other materials that the sealant may come into contact with. Is that right?
Jon: Yeah, actually. Yeah, we’ll do compatibility testing. So things like natural rubbers that can be in gaskets or setting blocks, they have plasticizers in that material that can freely move about from the setting block or gasket into the sealant. And these plasticizers are organic. And what happens is they’ll come to the surface of the sealant and they’ll oxidize and turn brown, creating kind of a really poor looking, poor aesthetic condition at the outside of the façade. So we also do that testing to ensure that you’re not gonna see potentially aesthetic issues. As well as we test the adhesion to make sure that these plasticizers are not influencing the adhesion of the sealant to the substrate.
Paul: We’re talking about stuff that you do getting started with a project. Dow can review drawings, you do mockups, adhesion testing, compatibility testing, those sorts of things. So now, actually, we’ve been through all that and we’ve got good confidence about the materials we’re using. I wanted to ask one more question though before we get to that. Can you talk a little bit about joint design or joint profile and the use of backer rod and bond breaker tape?
Jon: Sure. So in a conventional weather seal, typically we see something that’s like a butt joint. And what we wanna see in a good design is that the joint is shaped like an hourglass. We wanna see that mainly because what the hourglass shape does is it maximizes the contact between the sealant and the substrate and reduces the thickness in the middle joint. Which, when the joint moves, it reduces the potential stress distributed within that joint to prevent overloading one side or the other to prevent failure in that. So that backer rod plays, not only a critical part in helping define the joint, but it also plays a critical part in helping define the geometry in the joint of that.
Paul: That’s good. That’s good. So the follow-up to that is, seeing, you know, misconceptions in the field about backer rod and things like that, backer rod…and if you could just briefly talk about. Backer rod is for joint profile and does not help with waterproofing, aside from making sure the sealant joint’s the right size. In other words, backer rod isn’t part of the waterproofing process. Agree or disagree?
Jon: Yeah, I agree. I mean, it’s only there…it’s only useful through the cure. Once the sealant’s cured, it really doesn’t provide a lot of function. Unless it’s like a horizontal joint where you’re having to put a real stiff material in there so you’re not getting any punctures or issues with somebody in a high heel pushing through the sealant and falling and causing ankle issues. But yeah, for the most part, the backer rod is just there for the cure cycle.
Paul: So we’ve got our materials selected and we’ve designed our joints and we’ve gone through all the preconstruction submittal and review process. And now we’re out in the field and we’re actually installing the material. What kind of review… Well, first of all, obviously, contractors, subcontractors should have their own quality control measures set up and training and whatnot, you know, having skilled applicators make sure everything goes in right. But what kind of support can they get from Dow and the distributor during the installation process?
Jon: Well, we have a very strong partner network with our distributors. And part of, you know, this warranty process is that someone from Dow or someone from our distributor will come out and do field adhesion testing periodically through the construction of a building to ensure not only that the materials form an adhesion to the different substrates, but also looking at the geometry of the joint to make sure that it is appropriate. The hourglass shape where it’s maximizes the contact on the sides versus having a thinner section in the middle.
And all of our distributors are trained on how to do an appropriate field adhesion which includes…you know, may not think about it but if you have a joint that’s metal to masonry, I mean, those are two different types of substrates. And so the masonry might require primer where the metal does not. And you have to be able to isolate the sealant in such a way that you’re actually testing the adhesion to each surface independently versus testing kind of a composite reaction of the two substrates.
Paul: So all of this… I just wanna tell the listeners, because we run into this a lot… Well, let me ask you one pretty easy question first. What’s the charge for all this? What does Dow Corning charge the customer to do reviews and field support and things like that?
Jon: It’s actually…there is no charge. It comes with part of, again, kind of this warranty process of weather seal and structural glazing applications. So it’s built into the product as part of that whole process.
Paul: It’s free?
Jon: Yeah, it’s free.
Paul: Yeah, so everybody listening to that? All this that’s really good practice and really something that should be done on every project, there’s no additional charge for it. And so many times it’s not done, it’s kind of mind boggling that it’s not even a cost issue, it’s just a question of kind of understanding what needs to be done and facilitating having it happen. And I can remember projects that we’ve worked on…I’ve worked on with Kevin Dunphy, who’s the Dow rep in South Florida, where we went back on some old projects and I was trying to determine if it was…whose material was used. It was a project where the sealant had gotten concrete overspray on it from a building next door. We were just trying to figure out whose material was on it and it was a very prominent [inaudible 00:19:16] that had done the work originally. And Kevin went back and researched and basically, they had not done any warranty, any of the stuff we just talked about. It was really surprising.
But I guess that’s the way things work sometimes. Can you talk a little bit about, speaking of warranty, what the warranty options are for the customer and the end user with the silicone sealants?
Jon: Sure. For weather proofing, we offer a limited performance warranty of 20 years, which essentially states that there would be no through water penetration in the area where that sealant is applied. And there’s some caveats. You know, it has to be applied properly per our published recommendations. And you can go to www.dowcorning.com and search for our America’s Technical Manual for those recommendations. The warranty, you know, has got things like acts of nature, things like that, that are not included in the performance warranty.
But if you look at it, really what we’re saying is, “At a minimum of 20 years, we expect that sealant to perform in weather sealant applications.” And obviously, like I was talking about, the first use of that weather seal, in reality, the sealant’s probably gonna last quite a bit longer. As long as it was designed and applied properly. On the flipside of that, we have a structural glazing warranty. And it is a limited performance warranty up to 20 years. And what that guarantees is, as long as a structural glazed curtain wall assembly has been designed and applied properly with our sealants, the sealant will retain the glass or in-fill in the frame for a minimum of 20 years.
Paul: So what has to be done in order…I know these warranties sound great, but you don’t just automatically get the warranty if you buy material from Dow. What exactly has to be done in order for the warranty to be valid?
Jon: So that’s an important point. The warranty’s actually issued for the address and the location of the project. Like you said, it’s not you just buy a tube of 795 and all of a sudden you’ve got a 20-year warranty. And so what happens is, especially for structural glazing applications, we require drawings to be submitted so we can review and ensure that the structural joint dimension is adequate for the design loads. We also require samples to be submitted of the different substrates that are gonna either be structurally glazed or in weather seal. And what we do is we’ll test for adhesion compatibility. And we also have an ability to test for stain for sensitive stones.
And without that testing and without that project review, there will be no warranty offered. So it’s a critical part of the process of this construction fabrication. And what we hope to see is that all this is done prior to the building being commissioned. Because part of this testing and things and these drawing reviews helps…it’s another set of eyes on the project to ensure that there’s nothing that potentially could be a fatal flaw in the performance of the building moving forward.
Paul: So if you’re building the One Main Street skyscraper and you go through the whole process and the warranty is actually issued specifically saying it’s the One Main Street skyscraper. So, technology is really advancing these days. You know, we see a lot of things going on in the construction industry, which, honestly, I believe is a little slow to get going on some of this stuff, but they are. I mean, you go out in the field now and superintendents have iPads with the plans and, you know, see it’s a lot easier to collaborate and have information available and things like that. What are some of the technology advances that you’re seeing in the sealant industry?
Jon: Well, one of the things that we’re being asked on a frequent basis is providing data to allow designers to use finite element analysis in their designs. Especially for structural glazing applications. Because we have a lot of folks globally that are pushing the boundaries of what a façade is. I guess from a classics point of view, most curtain walls envision as a frame with a piece of glass in it. And people trying to use glass as structural members. And so these are complex things to calculate and it requires heavy computing power. So we have invested quite a bit of time and effort to help develop that data.
And what it’s done is it helped us…it’s given us insight in how sealants perform. I think the other thing, it’s helped us come out with a new type of structural glazing adhesive. Because one of the new technologies or new trends is to go into point fixed glazing facades where they only means of attachment are the corners and midpoints versus the entire perimeter in kind of your conventional structural glazing. One of the challenges with those point fixed systems are you actually have to drill through the glass. And really, I think it’s well-established on how to do that properly. I think for a lot of people the question becomes, if you’re drilling through the glass and that’s a sealed IG unit, is it gonna lose gas? Is it going to condense? What’s that unit gonna look like in the future or how is it’s energy performance gonna maintain itself?
Well, with this new structural adhesive, which is 10 times the allowable stress of conventional structural glazing…so is you design structural glazing, you use an allowable stress of 20 psi to come up with a joint size. With this, it’s 200 psi. So it allows the use of minimal contact points using point fixed systems at a higher strength, but part of that is is that it requires some heavy lifting from an engineering analysis to do that. But what it accomplishes is is it doesn’t disturb the integrity of the glass, you don’t have to drill through it. And also, I think gives it a cleaner appearance where you see the entire glass façade versus something sticking through that. Which I think, architecturally, gives a lot of freedom in the design and the appearance of the glass.
Paul: So what’s the attraction with point fixed systems? Why are designers gravitating to that?
Jon: Well, I think there’s a couple reasons. One is is that glass is getting bigger. I mean, if you go to some of these trade shows, and as you’ve seen some of Eckersley, O’Callaghan’s work across the globe with these Apple stores, you’re starting to see pieces of glass that are 20 feet by 40 feet. And why that is, I think is people want uninterrupted views in their building. And so when you look at these large pieces of glass, they may require very large or thick mullions which kind of architecturally interrupt the view and may not be the aesthetic that they want it. So I think it’s kind of pushing that idea towards that point fixed where you’re minimizing the interruption of the attachment points from around the entire perimeter just to specific locations on the interior of the façade.
Paul: Yeah, you know, these Apple stores are really cool. I was out in Santa Monica, California and there’s one there. And basically, the roof and the…it’s in like a shopping mall. So the sidewalls are other stores. But the roof and the front of it is basically all glass and there’s some big pieces of glass, structure glazed mullions, things like that. You can tell they’re making lots of money just in the way they’re putting it altogether. Our consulting practice, we’ve always had it this way but we’re seeing the desire for bigger and bigger pieces of glass. And it’s a challenge, but they are getting bigger. And you get into markets like hurricanes where you’ve really gotta have a lot of structural capacity to withstand missile impacts and things like that, that’s where architects still don’t always get what they want.
The new facades are obviously very impressive. Where do you see things going from now with your industry? What’s the future?
Jon: Well, I think it’s going to be more sophisticated designs incorporating these larger pieces of glass. I think if you look at a lot of these projects like that glass slide on the face of the building there in Los Angeles, I think you’re gonna start to see glass being used as a functional piece of a building more so than just a window to the outside. And I think that’s gonna require a lot of heavy engineering and oversight to ensure that things are fabricated properly. I do think that glass is still an extremely valuable material in the building industry. It’s one of the few things that allows people to interact with the outside while still being in a controlled environment.
And I think when people build buildings, they wanna be able to have that interaction. And so I think of things that will allow us to do it like dynamic glazing to help control with energy that’s used in a building. And I think even in the future, we’ll see probably interactive displays where you almost have a computer screen or an iPad that’s the size of the window wall where you can interact with different things beyond just that look outside.
Paul: Technology is really exciting. I mean, it’s really getting to the point where we’re getting into things that are just futuristic movie stuff a few years ago and now we’re actually getting into it and doing it, and, you know, virtual reality, artificial intelligence and all those sorts of things and they’re real. We’re all gonna be using them and it sounds like outer space maybe right now, but five years from now, we’re probably all gonna be using them. And when we have this conversation again five years from now, it’ll be a completely different conversation. Stuff that we say is coming will be kind of old school.
Jon: Yeah.
Paul: So, it’s a lot of fun. So thank you very much for coming on today. I mean, really, really interesting and I think it provides a lot of really good value to the listeners. You know, the one thing that you said, what really resonates with me being in the business that I’m in and I think will resonate with the listeners, is that the importance of weather seals and things like that in keeping the water and the elements out of a building. I mean, the success of a project can live or die on that. It’s really important and it’s really interesting. And you guys are big players in this and very well respected. I know we work with Dow on a lot of projects. I really thank you for the insight and the wisdom and I think it was really good stuff.
Jon: Well, and let me thank you for the opportunity. This has been a pleasure talking to you. And if there are any listeners out there that wanna interact with me, have questions about it, feel free to provide my contact information to them. I’m always happy to talk silicones and building science and things like that.
Paul: Yeah, so that’s a good point. Why don’t you tell listeners how to get more information about everything that we just talked about? I know you referenced the technical manual. Where do they go and what do they see?
Jon: Yeah, they can go to our website, www.dowcorning.com. That’s D-O-W-C-O-R-N-I-N-G. I can be reached at jon.kimberlain@dowcorning.com. If they go to the website, there’s a lot of interactive displays of information that’s tailored to somebody that’s more architecturally focused versus a fabricator. And it has information on warranties, testing capabilities. And we publish a lot of white papers on different building science aspects of our material. So there’s a deluge of material on the website. But if they can’t find something, you know, they can feel free to contact me to further assist.
Paul: Great. Great. Well, that’s a really valuable resource. So once again, thanks so much for a really interesting podcast.