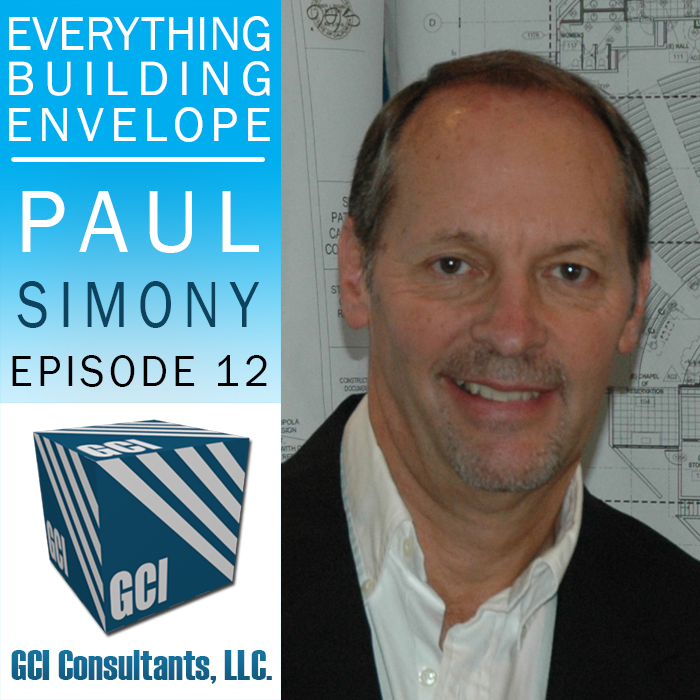
About The Everything Building Envelope Podcast: Everything Building Envelope℠ is a dedicated podcast and video forum for understanding the building envelope. Our podcast series discusses current trends and issues that contractors, developers and building owners have to deal with related to pre and post construction. Our series touches on various topics related to water infiltration, litigation and construction methods related to the building envelope.
https://www.everythingbuildingenvelope.com
*** Subscribe to the show and leave us a Review on ITunes!
Paul Beers: Hello, everybody. Welcome to the “Everything Building Envelope” podcast and today we’re gonna talk about skylights, which I think is really going to be interesting for our listeners. We have our expert Paul Simony, who has 30 years of experience in the industry and he is with SKYCO Skylights. We’ll tell you a little bit more about them in a minute, but first Paul…and welcome by the way.
Paul Simony: Thank you.
Paul Beers: Thanks for agreeing to be a guest today. So first maybe you can just tell everybody a little bit about your background and then we’ll talk about SKYCO and dive into our topic.
Paul Simony: Sure. I’ve been involved with the skylight industry for over 30 years both on the East Coast and West Coast. Worked for six different skylight companies during my career and I sit on several different code committee boards, ASTM Committee boards as well with regarding different aspects of skylight-related issues, fall protection and so forth. Also serve on [inaudible 00:01:28] technical committees regarding various performance criteria that’s outlined in the various codes and so forth, code standards.
Paul Beers: Great. We’ll tell everybody about SKYCO. I’ve got a little plug that we’ll read and then we’ll get into it so. SKYCO Skylights is an industry-leading industrial and custom skylight manufacturer located in Costa Mesa, California. SKYCO Skylights has a full range of products including industrial skylights, UL listed smoke vents, custom structural skylights, photovoltaic skylights and canopies and rooftop safety and security products. All of SKYCO Skylights products come with a 10-year warranty. For additional information you can reach SKYCO skylights at 949-629-4090 or via email at info@skycoskylights.com.
So Paul, you know, I think people probably don’t think about skylights enough. I know they’ve got some really great features and can add a lot to projects and architects in particular, you know, when they use them well they can really make projects. So why are skylights a must for large buildings?
Paul Simony: You know, I truly have a passion for skylights and natural daylighting and so forth and so many related issues concerning, you know, the utilization of skylights and bringing natural daylighting into buildings is obviously the energy savings. You know, you’re reducing your electrical cost. You know, lights out equals free light as we say. Other aspects, you’re reducing the carbon imprint, you know, reduce greenhouse gases. Codes require a certain amount of daylighting depending on the building type. California Title 24 requires use of skylights in conjunction with automatic daylight control systems in buildings that are 5000 square feet or larger, open space, single story. So code requirements are directing the use of skylights. [inaudible 00:03:33] is another source that recommends the use of natural daylighting, typically 2% to 2.5% of the roof area suggested. And another benefit is it enables architects to achieve lead credits in several potential areas such as the energy and atmosphere, to optimize energy performance, materials and resources, environmental quality for daylight and views, innovation and design lead credits as well to utilizing natural daylighting to improve performance, productivity and wellbeing for the occupants that are in these buildings.
Paul Beers: So talk about daylighting, a couple of questions there. Daylighting is basically, as I understand it, is letting the right amount of light in. So is it possible to have too much light coming in, I guess would be the first question?
Paul Simony: Yeah, that’s a key point. The codes require that the glazing material have a 90% or higher haze factor, and basically what that means is the diffusing property of the glazing materials. So what that does is it prevents, if you’re following the codes properly, it prevents high glare-y type of light coming into a building. For example, you typically do not want a clear dome in a warehouse because that clear dome is gonna bring too much glare and hotspots into the building. Retail is not a good spot for clear domes as well. So that’s why they’ve been really key on honing in on the haze factor because of the diffusing properties that that creates. So what they’re trying to do is they’re trying to integrate as much daylighting into the building but they wanna create soft, natural daylighting in there as opposed to bright glare-y daylighting. So that’s really a good point you bring up there.
The other aspect of it is that the codes also have various solar heat gain coefficient requirements depending on the region you’re located in. And the solar heat gain coefficient is the amount of heat that’s actually coming through the skylight into the building. And again, if you have a clear dome it’s gonna bring way too much heat into the building so it kinda offset the benefit that you would typically achieve if you bring skylights into a building and trying to save on energy.
Paul Beers: Yeah, so the energy savings would be basically that proper array or configuration of skylights and using, you know, the proper glazing material and whatnot. Then, basically, you don’t need to have a bunch of lights on all over the place. Is that…?
Paul Simony: That’s correct, yes. That’s really the goal. There’s issues regarding the amount of heat coming in, too, particularly in areas where you have, say, an air-conditioned facility because, you know, you’re trying to save energy now you’re bringing heat into the building so the air conditioning system has to work harder to cool that building down. So if the guidelines that are outlined in the building codes and in the actuary are followed then you should have a nice mix of natural daylighting combined with energy savings.
Then the other aspect is also the automatic daylight control systems, and what they essentially do is they are set up so they basically measure the amount of light coming into the building, and there’s different types of daylight control systems but essentially what they’re doing is measuring the amount of daylight coming in the building and it’s a pre-programmed system so when that foot candle level hits a certain point that’s designated when the system is set up then it will automatically turn the lights off and that’s really another very, very effective way of reaping the benefits of the energy savings.
Paul Beers: Yeah, sounds pretty neat. You know, I noticed when I go to large stores, say Walmart, Home Depot, like that, they use a lot of skylights and, you know, obviously for the very reason we were just talking about is to really, you know, give a better environment inside and not have to blast a bunch of artificial light all over.
Paul Simony: Exactly, yes. Yeah, there’s been studies done over the years, retail environments, for example, where they found that the amount of sales are higher in areas that have natural daylighting versus areas that did not.
Paul Beers: I was thinking, and I wasn’t gonna say it, but these guys know what they’re doing so if they’re using skylights, obviously a lot of it is about motivating people to buy their goods. So you wanna put them in the best possible environment and I’m sure that lighting has a lot to do with that and natural daylighting is probably the best way to go on that.
Paul Simony: Exactly.
Paul Beers: Talk a little bit about the various kinds of skylights. Maybe you can run through what kind of skylights are out there and available.
Paul Simony: Sure, I’d be happy to do that. So you’ve got basically some standard residential types: Fixed which is a type that does not open. Operable units, which allow ventilation for the interior space. Elaborate custom designs such as the monumental custom skylights. That’s typically what you see in more high-end residential houses. We do a lot of that out here in Newport Beach, in Laguna Beach, up in the Beverly Hills area. You’ve got high-performance glazing options available with high-performance glass and polycarbons and acrylics which are all helpful in meeting the energy code requirements, and then you’ve got various models which meet the International Building Code requirements for solar heat gain coefficients and light transmittance and new factors as well.
You get into the commercial/industrial side, you’ve got typically the 4×8 unit skylights are what you see in most of the large warehouse distribution type facilities and they’re used to daylight these large open areas. And then in conjunction with commercial/industrial types you have UL listed smoke vents, which are designated as a requirement by the International Fire Code. And basically what that is it resembles the appearance of a skylight but it has two doors that open up and allow the hot gases to heat and the smoke to ventilate the building automatically in the event of a fire in the interior space.
The other benefit of those besides the light safety aspect is that they also provide natural daylighting because we utilize the polycarbonate domes in those as well to bring natural daylighting in. So basically with the smoke vents you’re accomplishing two aspects of code requirements. You’re daylighting the building and also meeting the fire code requirements by safety. In other aspects you can also include louvered bases for air circulation. They provide natural gravity ventilation. So in non-conditioned buildings they’re beneficial to help reduce the heat load in the building and provide circulation for the occupants as well so it’s a much cleaner environment as opposed to a sealed type of a unit.
Paul Beers: Because heat rises so you’re basically letting it out.
Paul Simony: Exactly, yes. And you get into the custom skylights, you’ve got a full range of custom skylights that…you know, gables and ridges and polygons and so forth, you know, single-slope units. Those are typically what you would see in large commercial buildings, shopping malls are a very big area where those types of custom skylights are utilized. Again, those are also seen frequently in high-end residential homes as well. And then the newest area where we’ve gotten involved with skylights is photovoltaic skylights and that’s one I have a real passion for. Basically you’re taking a skylight of some type of configuration like a ridge or so forth and you’re placing the standard glasses in that unit with photovoltaic glass.
So the cool feature about that is you’re bringing daylight into the building, so you’ve got free daylighting coming in during the day, but in conjunction with that the glass is actually generating electricity which can either go into your grid system to offset some energy cost or it can go into a battery backup system or so forth to be utilized when the sun goes down at night. So you’ve got some really cool benefits there, and the other cool aspect about the photovoltaic skylights is that you get a 30% tax credit on the entire skylight system. So if you have a standard skylight with the glass in it you get zero credit off of that. If you put PV glass in there and now all of a sudden you get 30% off that entire skylight structure. So it’s a huge cost savings upfront and helps to reduce the ROI on the installation of a PV skylight by incorporating that 30% tax credit.
Paul Beers: Are people buying them at this point? Are you seeing them used much or what’s the trend with them?
Paul Simony: Yeah, we’ve done some nice projects. There’s been some…for example, we did the Apple store up in downtown San Francisco and that’s got a whole photovoltaic glass roof on it and it’s generating roughly about 16%, 17% of the energy requirements for the store. Novartis Pharmaceuticals is another large one that I was involved with in New Jersey and that had about 24,000 square feet of photovoltaic glass on the roof there. At the time, New Jersey also had a 20% state credit on photovolataics so Novartis was able to combine that with the federal and they got 50% off the entire PV glass skylight structure. So that was a huge savings for them. And then they also reaped the benefits of all the free electricity it’s generating over the next 25 to 30 years or beyond.
Paul Beers: Wow.
Paul Simony: And then the last item related to skylights is the safety and security products that we offer as well. Fall protection is a big issue with skylights, particularly in the warehouse type applications and retail applications and most commercial installations as well, and OSHA has specific requirements for fall protection systems. We also manufacture security burglar bars, which now meet the Cal OSHA fall protection requirements as of July 1st, 2016. So that’s something that was recently introduced into the California building code. And basically, the OSHA requirements require that the skylights or fall protection will support a 200-pound impact load. Cal OSHA and Washington State OSHA both require a 400-pound impact load. You know, the SKYCO skylights, 4×8 skylight, has been tested to an 800-pound impact load so we’ve recognized the need to provide additional fall protection requirements in our products that we’ve addressed that.
Paul Beers: So let me ask you a question about safety and security. You know, people…it seems like an obvious answer but I think maybe some of the listeners will be good to hear. So, you know, you have glass over your head. Is that safe?
Paul Simony: Well, skylights by code are required to have laminated glass in them, same type of glass that you would have in your windshield so if there’s any break it’s just not going to…you’re not gonna have shards of glass falling down from the skylight below. So basically, the codes require that you have laminated glass in those skylights. So the majority of the large glass skylights we do are all tempered outer glass insulated with the laminated glass portion on the inside. So it’s all designed for the safety aspect.
Paul Beers: So you’ve actually got three pieces of glass. You’ve got the tempered on the outside and you’ve got the laminated unit, which is two pieces of glass with an inner layer on the inside. So even if the tempered glass…you know, a tree branch fell down, broke the tempered glass there’s still lots of protection there to keep anything from coming down.
Paul Simony: Exactly. And in areas where you have [inaudible 00:15:23] for example, in Miami-Dade, the Florida building code requirements, you go with a polycarbonate inner layer in the laminated portion, which will prevent…they basically test the units to withstand a 2×4 that’s shot out of a canon and it can’t go through the glass. So that’s where the polycarbonate comes into play. So there’s a lot of different options out there for glazing depending on what type of code requirements you’re trying to address.
Paul Beers: Yeah, it’s pretty interesting. You know, I’ve often said that you can pretty much design for anything if you, you know, have the criteria and the will. So you can stop flying 2x4s, you can, you know, have energy advantages, you can have security, safety, you know, all those things and it’s pretty…the use of glass is really pretty amazing all the different applications you can put it in. Even see it in floors, in places like that and have quite a bit…So Paul, tell me how has the industrial skylighting evolved over the years. I know technology has really advanced and things are getting better and better. So what’s gone on to get to where we are now?
Paul Simony: One of the things that we’re seeing more frequently out here in the western region in the warmer climates is the louvered bases stuff for building ventilation in non-conditioned buildings, you know, providing fresher air for the interior space which is a benefit for the occupants and allows the roof structure to be ventilated reducing degradation from the buildup of moisture at the roof, for example. So there’s another added benefit there. Some of the issues with the old systems out there, the louver systems were prone to leaking and they were not effective at all against wind-driven rain, so consequently, you know, you get an incident with wind-driven rain and you’ve got moisture…water dripping down into the building.
And then there was also some poor sealant compatibilities there that have been addressed as well. We use a 50-year warrantied silicon seal around the perimeter of all our domes to seal up our units now to ensure that they’re not going to have any issues with leakage. And then some of the old systems were not subjected to any type of national test standards for performance criteria so that was a huge issue, too. And there’s still skylights out there on the marketplace that aren’t tested to any standards. You know, you’ve got these small mom-and-pop and type skylight companies and they’re just building stuff in small facilities and there’s no guidelines as far as test criteria so that’s always an issue as far as longevity and long-term performance.
Some of the new designs, for example, that SKYCO Skylights has introduced is we have a vortex louver, which is essentially a leak-proof louvered skylight that has an interior made out of rain baffle, which eliminates any water penetration. It comes standard with a bird screen, and then really the only option you can add to it is an insect screen or a dust filter if you so desire. So it’s one of the most innovative louvered units out there on the market today. A polycarbonate dome has been introduced as well into the marketplace. It’s much stronger as I mentioned. Our units tested to an 800-pound impact load. And we also offer 10-year warranty against yellowing and breakage, which is unheard of in the industry, so that’s how confident we are with the quality and strength of the polycarbonate.
And then, you know, polycarbonate is also beneficial in addressing some of the requirements for fall protection. We always qualify that with a caveat that if you’re looking for, you know, 10, 15, 20-year resistance against fall protection and it’s always very, very wise to install some type of either interior or exterior mounted fall protection system as well because polycarbonate, just like any of the other glazing materials out there, is a plastic material and it’s going to be subjected to potential UV degradation over many years. Also, environmental issues. You don’t know what type of chemicals and so forth could be contained in the building where they skylights are installed and all those things can impact the performance of the glazing material. So it’s really wise to install a secondary fall protection system.
And some of the old issues with the old systems such as the acrylic that’s not impact resistant, it was prone to cracking and getting brittle over the years. You need varying thicknesses required to meet the loading requirements per the code. So that was always an issue. And then some of the new designs that [inaudible 00:20:23] Skywave, which is SKYCO’s dome design, it’s also referred to as a parabolic shape, that actually adds more light transmittance into the building. It features 30% more light collecting surface area so you’re actually capturing more daylight during the course of the day. So it brightens up the building much more effectively than just a standard smooth dome would.
Paul Beers: So you call that a parabolic shape?
Paul Simony: Yeah.
Paul Beers: Yeah, what is that?
Paul Simony: It’s kind of like…it’s got ridges in it, so the ridges not only are providing more surface area but also increasing the overall strength of the unit.
Paul Beers: Oh, nice. So, you know, it’s funny. I did a project, it was probably 8 or 10 years ago, in Mexico, in Cancún, Mexico, and I think it demonstrated old versus new really well. They had acrylic skylights that have been there for quite a while. So along came Hurricane Wilma, would have been 2005. So they had all these skylights, like an array of dome skylights over the atriums that were, you know, outside the rooms. Basically, Wilma removed them. They were gone. They didn’t know if they were in the ocean, in the bay, whatever. You now, they were obsolete, obviously, and weren’t set up for those kind of winds. We had to go in and put in a new system and the two things that we talked about quite a bit was we put in…you know, we used a glass skylight system with aluminum framing. You know, it was very sturdy. In fact it was so sturdy we had to build new curb just to mount it.
The other thing was we had to use louvers because you’d have the heat buildup without them, especially in Mexico, a place like that. And that was when I learned about rainproof or rain-resistant louvers. And so we actually…they weren’t all part of the same system. I wish I would’ve known you guys back then. So we bought the louvers separately and we erected the skylight and everything, but I’m happy to say that, you know, hurricanes have come by there since then and obviously the skylight stayed on the roof. They were designed to Miami-Dade requirements. And even more relief to me was they didn’t leak. It’s pretty interesting because when a lot of people think about louvers, you know, they’ve obviously got air bents all through them. How can they be rain proof? Obviously, they can be so it’s a really, really interesting concept. We were talking about the industrial skylights. What else? Is there anything else that has changed or has evolved over time?
Paul Simony: One of the things that evolved in an effort to create a less expensive skylight, some manufacturers actually are producing what we refer to as a capless skylight where you don’t have an aluminum cap that’s holding the dome down in place. Basically what you’re doing is you’re forming a dome up that will sit on top of a frame and you’re screwing through the dome into the frame. So you’ve got a screw penetrating the plastic glazing material and then being screwed into an aluminum or a galvanized steel frame. And the big issue with that is you’ve got different expansion rates between the plastic and the steel or the aluminum. So during the cooling process parts of the day and then in the evenings you’ve got this expansion/ contraction going on. And what happens is where that screw is penetrating the dome and going through the dome, you start getting a different rate of expansion and it starts to cause cracks which then mitigate up into the dome itself, and there’s been a lot of issues particularly out here. There’s a lot of buildings that have cracked domes on the capless units.
Paul Beers: I was gonna say. It sounds like a low-price leader.
Paul Simony: Yeah, exactly. That’s exactly what it is. It does not meet any of the air and water and filtration requirements. It doesn’t meet AC16, which is the acceptance criteria that ICC Evaluation Services publishes. So it doesn’t meet any requirements of that. It’s just basically a non-listed cheap skylight that does not perform very well over long term. So that’s one of the things that SKYCO stays away from, but you know, unfortunately we do run into that issue when we’re bidding projects because, as you said, you know, it’s kind of a low-price leader and some of the competitors will try and use that to get their foot in the door and then they have to go back if they’re trying to get code approval and submit something that meets the codes. So the capped unit is really designed to meet all the requirements of AC16. It also is a stronger unit. It’s not going to have any screws penetrating the plastic, which is really not a very smart way to go as far as designing a skylight system, and also it can be tested and have an ICC Evaluation Service listing too to meet all the performance requirements.
Paul Beers: You know, it’s a sad reality is that some projects or some, you know, organizations are just after the lowest price they can get and, you know, sometimes you get what you pay for. And the ROI in the end probably isn’t anywhere comparable. You pay a little bit more upfront and, you know, it lasts longer and performs better and in the end you probably pay less, but some people are just so focused on the cheapest price and that’s where you get these, you know, like, what you’re describing here sounds like a junky skylight to me.
Paul Simony: Yeah, that’s exactly what it is. You know, and you have situations where you have developers putting up basically spec buildings and, you know, when the GCs are bidding these jobs they are trying to do them as economically as possible and, you know, if it’s something that’s gonna be flipped in six months or a year not everybody is concerned about the quality of the materials that are going into that building, but you know, your skylight is your first defense against the rain out there along with the roof obviously. And you know, if someone buys a building and they have got cheap skylights on there and, you know, six months after they purchase the building the domes start cracking and now you’ve got issues there. I’m sure a lot of buyers aren’t very happy with that kind of scenario. So, you know, personally, if it’s me, you know, I look at…you know, price is ever only an issue in the absence of value, and the capless unit definitely has an absence of value in my mind.
Paul Beers: Yeah, well said. It’s too bad that sometimes money is the only thing [inaudible 00:27:33]. I have customers…I know even when we put out proposals for consulting agreements they look at the bottom line. They don’t read the scope. They don’t, you know, see if it’s apples to apples. They’re just looking for the cheapest price. You know, usually you get what you paid for.
Paul Simony: Yeah, no question about that, and that’s a really, really strong point when you’re talking about skylights.
Paul Beers: You’ve mentioned the ICC-ES listings. Can you tell us…I know ICC is International Code Council, is that right?
Paul Simony: That’s correct.
Paul Beers: Yep, and that’s the code, by the way, they produce the International Building Code that we see pretty much…we see that code or variations of it throughout the U.S. and beyond, correct?
Paul Beers: Right. That’s right, yeah. So it’s starting to take effect. I know they’ve got a version for Dubai now. You’re starting to see it pop up in some of the Asian countries and even Mexico is starting to look at some of the sections of the ICC code and adopting those in various areas as well. Yeah, we look at the ICC Evaluation Service, which is a division of ICC. ICC-ES Evaluation Service section actually produces various acceptance criteria. So they actually have criteria that they develop the standards if you will. For example, with skylights they have acceptance criteria AC16 which is for skylights, unit skylights, and that has a specific air and filtration and water penetration requirements. They also test for structural loading and positive or negative pressure resistance.
So basically, if they’re certifying that your skylight is ICC-ES accepted then you’re getting a skylight that is the highest performing skylight out there. So we kind of look at that as the gold standard and then, you know, below that you’ve got other types of skylights like the capless and so forth. All that information that’s required for complying with that, that’s all required to be performed by a third-party authorized test lab. So not just the manufacturer saying, “Yeah, we meet those requirements.” You have to actually produce the proper test data and submit all that to ICC-ES in order to get your ICC-ES approval.
Paul Beers: Yeah, so SKYCO actually produces units, has them tested and evaluated to get the ICC-ES listing?
Paul Simony: Correct, yes. Yeah, that’s a way to ensure that the product you’re putting on your roof are safe and ensure they meet the high-quality requirements that ICC recognizes as extremely important. They also have the quality control requirement, which is another key aspect of ICC-ES. And they have a standard called the AC10 and that really provides for the traceability of all the materials used as well as the final quality control inspection documentation for every unit manufactured. So if there’s ever a problem with a skylight out there in the field there’s a label on there, an ICC label, on the skylight. It will tell you exactly when that skylight was manufactured. You can go back to all your records in-house and see what materials were utilized to build that skylight and then you can figure out, you know, what went wrong if something did indeed go wrong and then go back to the vendor and say, “Hey, we had a problem with this.”
If you’re just building skylights, you know, without any type of certification or QC requirements in place then there’s no way to trace anything back to anything. It really, really makes it difficult to ensure that the products that are going out there in the marketplace not only are gonna be performing at a high level of quality but also that there’s traceability on all the components that are going into that. Yeah, the other thing that ICC requires is it has to have a capped unit. They go through fire testing. As I mentioned, high performance air infiltration, water penetration requirements, and then structural testing. So that all translates to stronger and safer skylights.
Paul Beers: Yeah, so I just wanna throw a “me too” in there because, obviously, you know, my business, we consult with owners and architects and help them with designs and whatnot, and we insist on product certification because if you don’t have it you really don’t know what you’re getting. You know, you have somebody saying, “Look, this is good because I say so,” or somebody…Do you see much out there in the market where you’re competing against products that aren’t listed and how does that all play out?
Paul Simony: Yeah, that’s a huge problem out there. And you’ve got some manufacturers that are quoting and supplying roofers with non-ICC-listed skylights and the contractor thinks, you know, they’re getting a great product, but in reality there’s a huge liability there for everybody involved. You know, they’re not meeting the code requirements. I’ve seen cases out here where a roofing contractor is in the middle of installing a project with skylights that were not listed and an inspector came by and started looking at it, checked the labels on them, found out they were not listed and he had them remove all the skylights and they had to replace them with ICC-listed skylights that were code compliant. So that could be a huge liability for the roofing contractor, the general contractor. It could cause delays in the project and what have you.
The other issue is, you know, if they’re not tested and so forth you could start getting issues with the structural integrity. You know, we have a lot of high wind with the Santa Anas out here, so, you know, we have high wind-rated skylights that’ll address that. Price point is always a big issue because the non-listed models sometimes they do the bait-and-switch tactic where they’ll quote a non-listed unit and let the people or the architect or anybody involved assume that it’s listed. If there isn’t an ICC number it’s not listed and the architect, owner, and contractor is liable. So you have to make sure that everybody involved does their homework and their due diligence as far as what type of units are putting on these buildings. Just to be clear, there’s no capless industrial skylights available with and ICC number out there and that’s really critical for the contractors to know that and to make sure that if they’re getting capless units they’re not getting what they paid for.
Paul Beers: It kind of reminds me of what was going on in Florida when they were cursing out the hurricane codes there was folks that were selling window film and saying, “If you put the window film on your windows they’ll be hurricane-proof.” When none of them were tested or passed and to this day still haven’t and actually ended up with the attorney general chasing them all out of town, Florida state attorney general. It’s a buyers beware market, isn’t it?
Paul Simony: Yeah, that’s always been an issue, too, when you get these major hail storms going through, like, Texas and so forth. And, you know, with Texas being a right-to-work state anybody can go in there and start repairing roofs and replacing skylights and then once all the work is done these guys disappear and there’s nobody around to chase down a warranty if you have any issues with this. So it becomes a huge problem. So, you know, buyer beware is definitely a huge concern out there.
Paul Beers: If that ICC label is on it then you know what you’re getting.
Paul Simony: Exactly, yes.
Paul Beers: So let me ask you a question. Where do you see the skylight industry going from here? What’s coming up down the road? Where’s technology taking us?
Paul Simony: Well, as I mentioned, we talked a little bit about the photovoltaic skylights, also referred to as BIPV systems, building-integrated photovolataics, and that’s something that I’ve been really heavily involved in over the last several years through a lot of lunch-and-learns with architects all over the area. A lot of excitement in that area. The architects are very interested in it, and as the codes become more and more stringent on essentially introducing the percentage of the sustainability of the power that’s going into these buildings.
You know, for example Santa Monica just introduced code requirements that by, I think it’s 2020 or so, somewhere around there, that they’re gonna require that all buildings have at least 50% of the power is going to be achieved through sustainable power. So whether that’s the photovoltaics or what have you it’s becoming a requirement that the architects need to address. So building-integrated photovoltaics is a huge avenue to pursue for these architects to design skylights, for example, or even vertical applications, you know, storefront, whatever, with photovoltaic glass in them and a that’s pretty cool avenue to pursue.
And then in addition, you get your federal tax credit, which was just extended last December until 2021. So that’s another way to help save money and also encourage people to utilize the energy savings and reduce the carbon imprint. And, you know, it also brings some added value to the buildings as well because, you know, now a tenant goes into a building, if he’s leasing a building he’s got the free power generated by the PV aspects that are integrated into the building and the building owners are actually getting higher lease rates because of the benefits of the free power. So it’s a win-win all the way around and plus it’s saving energy and reducing the carbon imprint.
Paul Beers: Can existing buildings be retrofitted? I know they can. That’s a silly question. How can existing buildings be retrofitted?
Paul Simony: Well, we’ve seen cases where they have, say, old skylight systems. Say, like a long glass ridge in the skylight that may have the old wire glass in them. And you can go back and remove that type of skylight and replace it with a photovoltaic glass skylight. And you’ve got your 30% tax credit off that skylight as well as the added benefit of the free power that’s gonna be generating for 25 or 30 years or longer. So it’s pretty simple to do. I know there’s several projects going on right now. Back in New Jersey we work with one of the photovoltaic glass manufacturers and he’s got a project where they’re replacing 55,000 square feet of glass with photovoltaic glass on a large building out there and that’s gonna all be retrofitted.
Paul Beers: So Paul, thank you very much. Really interesting topic, and I know it’s thought provoking for the listeners, and I know it’s a really important component in the building. So it’s really great to hear all about what’s going on in the skylight industry. And again, thank you for being a guest today on the “Everything Building Envelope” podcast.
Paul Simony: That was my pleasure. And if anybody has any questions they can feel free to email me at paul@skycoskylights.com or contact me at my office at 949-629-4090 and I appreciate the time.
Paul Beers: No, it’s our pleasure. Thank you. So I wanna announce today that we have a newsletter that we’re beginning called the “Everything Building Envelope Newsletter.” It’s gonna actually have some informative technical articles in it about various topics, and if you want to get on the mailing list for the “Everything Building Envelope Newsletter,” which is gonna come out monthly, you can text “buildingenvelope,” it’s just like it sounds, all one word, “buildingenvelope” to 228-28. So again, if you want to subscribe to the “Everything Building Envelope Newsletter” text “buildingenvelope” to 228-28. Thank you everyone for listening. Until next time, this is Paul Beers saying so long.
Skylights and similar products.
Expert: Paul Simony, 30 Years Experience, sits on several boards,
Company: SKYCO Skylights
SKYCO Skylights is an industry leading industrial and custom structural skylight manufacturer located in Costa Mesa, CA. SKYCO Skylights has a full range of products including Industrial Skylights, UL Listed Smoke Vents, Custom Structural Skylights, Photovoltaic Skylights and Canopies and rooftop safety and security products. All of SKYCO Skylights product come with a 10 year warranty. For additional information, you may reach SKYCO Skylights at 949 629-4090 or email SKYCO Skylights at info@skycoskylights.com
- Why are skylights a must have for large buildings?
- Energy savings with natural daylighting
- Reducing the carbon imprint
- Codes require a certain amount of daylighting
- ASHRAE recommends the use of natural daylighting
- Enable Architects to achieve LEED Credits
- What kind of skylights are available?
- Residential
- Fixed
- Operable
- Elaborate custom designs
- High performance glazing options available
- Various models to meet International Building Code (IBC) requirements
- Commercial/Industrial
- 4×8 Unit Skylights
- UL Smoke Vents with Polycarbonate dome for natural daylighting
- Louvered bases for air circulation
- Custom
- Gable Ridges, Polygons, Flatglass, etc…
- Photovoltaic
- Skylights and Canopies
- Building applied photovoltaics
- Skylights and Canopies
- Safety/Security Products
- Fall-protection systems
- Security/Burglar Bars
- Residential
-
- How has the industrial skylight evolved over the years?
- Louvered bases for building breathing
- Purpose
- Lowers moisture
- Provides fresher air
- Allows the roof structure to be ventilated reducing degradation from humidity
- Issue with old systems
- The old systems were prone to leaking
- Poor sealant compatibility
- Not subjected to National Standards for performance
- New designs
- I.E. The VORTEX
- Leakfree
- Birdscreen
- Optional insect and dust filters
- Purpose
- Polycarbonate domes
- Purpose
- Stronger
- Last longer against yellowing
- Code compliant – Meet OSHA Fall-protection
- More versatility for solar heat gains, light transmittance
- Issues with old systems
- Acrylic – not impact resistant
- Prone to cracking, brittle
- Varying thicknesses required to meet loading requirements per Code
- New designs
- SKYWAVE design adds more light transmittance – features 30% more light-collecting surface area
- Purpose
- Capped vs. Cappless
- Purpose for capped
- Stronger
- Cracking of domes eliminated as there is not penetration through the dome
- Air and water infiltration – High performance
- ICC-ES Listed (Meets AC16 Standard)
- Issues with Capless
- Screw penetrates dome causing cracks
- Prone to leaking – no seal between dome and frame
- Air and water infiltration – will not pass
- NOT ICC-ES LISTED! Or tested to AC16
- Purpose for capped
- Louvered bases for building breathing
- How has the industrial skylight evolved over the years?
-
- Can you elaborate on ICC-ES Listings and why they are important?
- Recognized by building code officials as the “Gold Standard”
- Elaborate on what it is
- A way to ensure the products being put on a roof are safe
- Quality control requirements per AC10
- Requirements for ICC-ES Listing
- Capped
- Fire Testing
- High performance Air Infiltration and Water penetration requirements
- Structural testing for positive and negative pressure – Translates to stronger and safer skylights
- Some manufacturers are quoting and supplying roofers with non-ICC-ES listed skylights and letting the contractor and building owner believe they are covered
- This is a huge liability
- Will not actually meet the code requirements – may subject the GC or Owner to replacement costs to meet code compliance
- People fall though – Not tested to OSHA fall-protection requirements
- Bait & Switch tactic – It is done because a manufacturer wants to offer a skylight at a specific price point so they offer a non listed and let people assume it is
- If there isn’t an ICC # it is not listed and the Architect/owner/contractor is liable
- SKYCO’s ICC# ESR-3837
- To be clear there are no capless industrial skylights available with ICC #’s.
- Contractors need to know if they get capless they are not getting what they paid for.
- This is a huge liability
- Recognized by building code officials as the “Gold Standard”
- Can you elaborate on ICC-ES Listings and why they are important?
- The Photovoltaic, BIPV systems seems really interesting, can you elaborate on those?
- Difference between BIPV and BAPV
- Benefits of BIPV
- Federal Tax credit (30% extended to 2012)
- Energy savings and reduced carbon imprint
- Building value increase – free power for tenants
- Fun Projects where people have benefited
- Apple
- Tiburon
- Novartis
- What are the possibilities?
- Large skylights can be changed in BIPV by switching glass and adding the solar integration components
- Up to 40% Light transparency with Energy generating efficient glass
- Many Cities and States are adopting a 50% requirement for sustainable energy in new construction – this appears to be an expanding trend