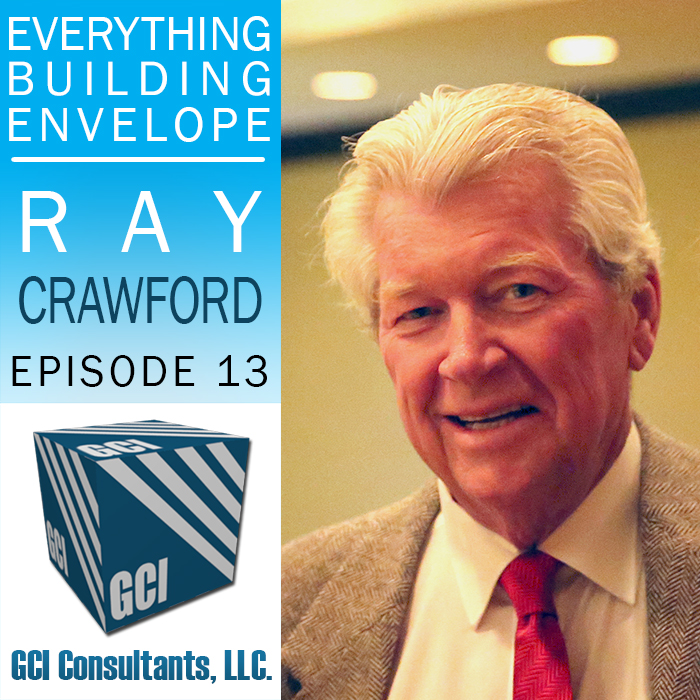
About The Everything Building Envelope Podcast: Everything Building Envelope℠ is a dedicated podcast and video forum for understanding the building envelope. Our podcast series discusses current trends and issues that contractors, developers and building owners have to deal with related to pre and post construction. Our series touches on various topics related to water infiltration, litigation and construction methods related to the building envelope.
https://www.everythingbuildingenvelope.com
*** Subscribe to the show and leave us a Review on ITunes!
Paul: Hello, everyone. Welcome to the “Everything Building Envelope” podcast. Really excited about today’s guest, Ray Crawford with Crawford-Tracey Corp. Ray and I have been working together for quite a while now, and it’s always been a good experience. Ray, thanks so much for coming on the podcast today.
Ray: My pleasure, Paul.
Paul: So, as I said, Ray, obviously, we go way back with each other, probably longer than we care to admit. So just for the benefit of the listeners, why don’t you tell them a little bit about yourself and Crawford-Tracey Corp.?
Ray: Well, I started in the business back in 1968, started working. Crawford-Tracey Corporation is a family business. I started working for my dad back in 1968. That’s when, basically, our company started doing unitized, pre-glazed, four-sided structural glaze. I started off in the back of the facility sweeping floors, cutting glass, doing mirrors, building frames. Kinda my dad made me start at from the floor up, which at the time, I was pretty disappointed. But I didn’t understand what he was thinking back then, but right now, I understand it.
Paul: Yeah, that’s always good to have the background to…I mean, you get to learn about the whole business from A to Z. I mean, I kind of have a similar background and no fun at the time. But as you look back on it, it was probably a good way to go.
Ray: Oh, it definitely was, Paul, it definitely was. And we started, when I got in there, I kind of worked my way up through the years. I became President of Crawford-Tracey Corporation back in 1992, so that’s been quite a while ago also. What’s that? Twenty-four years ago. So I had the opportunity to utilize what I learned from the ground up, which has been instrumental in allowing a lot of the decisions and a lot of the design changes and everything that we utilize here is the practical experience of it.
We’ve been manufacturing, as I said, we started with one of the first four-sided structural glazed unitized systems back in 1968. We found a lot of benefits to the product back then. As I’m sure you recall, there was a lot of concerns with the use of structural silicones for retaining glass dead-loads on them. And at the time, GE was the big product but Dow Corning came into market about that time, and we have kind of stuck with and been a real ally of Dow Corning products. And found out over the years, and I know you recall the issues back then with your acetoxy sealants and the deionized water anodizing processes that were required. And things have evolved quite a bit with the current neutral cure and accelerated silicones. It’s just made a big ability of the product to grow and mature as the industry has changed.
And in ’92, after Hurricane Andrew, whenever the new impact requirements came online, the structural silicone and silicone itself, became a bigger instrumental part in retention of glass, whether it was four-sided structural or captured specifically more so on the large missile impact arena. And it’s continued to go. And we have utilized and incorporate the four-sided structural glaze because we could do the face-sealed barrier wall system that we’ve developed. Which we give and provide 100 psf water resistance to our products that allows us to create an envelope protection that all of the rainscreen or pressure equalized manufacturers cannot even think about getting close to.
Paul: Yeah, that’s a very impressive number and I wanna get into that more as we go on. But let’s back up a little bit just for the benefit of our listeners. Let’s talk about some of the basic stuff. So you say, “Pre-glazed unified curtain wall,” so how does that work?
Ray: Well, what this provides and facilitates is we’re able to…we’ve manufacture and glaze all of our frames and components here in our prime factory. Big advantages to that, Paul, one of the big things is the quality control. A lot of the manufacturers do the field glazing of stick built and stick assembled systems on the job. When they do that, as I know you have experienced through your business and we’ve seen it time after time, the field contamination, all of the dust and dirt that gets into the cavity behind the glass.
Not to mention what happens if it’s not pumped that day, they let it sit overnight or over the weekend and then come back the following day and try and pump the joint for the temped [SP] glass that’s been put in place but wasn’t caulked, the contaminated substrates the dust, the dirt, the condensation, everything goes there. Not to mention the fact that in Dade and Broward County, there is a exclusion of field glaze four-sided structural glaze within the HVHZ, or high-velocity hurricane zone.
Paul: So you do everything in your factory and you have, obviously, a lot of quality control and a process and everything. So then, once you build these units and it’s the glass and the frame all in a pre-glazed configuration, how do you actually get it out into the field and installed? And how does that affect the schedule doing it this way as opposed to field erection?
Ray: Okay. To make a comparison to a type of construction a lot of people are used to and see, it’s almost like pre-cast concrete except we can get a little bit more onto a truck. What we do is the unitized panels are palletized. They’re put on prebuilt skids with supports. They’re loaded onto a flatbed tractor trailer. They’re strapped down. They’re trucked to the job site. They’re offloaded on the job site. And then, typically, depending on the size, if they’re bigger curtain wall panels, they are erected using lifting hooks or power cups. And they’re lifted and erected in place using either manual cranes, crawlers, or tower cranes to put them on the job.
Paul: I’m trying to remember. You have a video on your website that kind of shows a building being erected. Obviously, it’s sped up with the crane and all that. Don’t you?
Ray: Yes, we do. Those were the Florida Hospital [inaudible 00:07:47] Apopka that we did up in the north part of Orlando.
Paul: And if anybody wants to take a look at the video, what is your website address?
Ray: It is www.crawfordtracey.com. That is C-R-A-W-F-O-R-D, T-R-A-C-E-Y dot com.
Paul: And that’s a pretty cool video so if you’re interested, I’d recommend taking a quick look at it.
Ray: We’ve got that, Paul, and we’ve got a couple other videos of more conventional curtain wall and different installs. We try to continue to add items for the people to view.
Paul: Good. Good. And what about schedule? How does this work with the construction schedule?
Ray: Oh, typically, it has a big benefit to the schedule. The advantages are that we, with the incorporation of guaranteed sizes, we can prebuild the panels, get them all out to the job site. Prior to the panels and the fabricated components reaching the job site, we would have the welder and the receiver plates of the layouts all done so that when we get out there, we could just zip along and close in the building much faster. It screams through the install compared to a stick built, because everything’s all done. When we get out there, we just hang it up there and run across the building.
Paul: Yeah, so I mean, clearly, there are some big benefits. I remember saying, you know, that I really… I think I’ve said this before, actually, and then voted on it that the stick built method, these days, is kinda like being in the Dark Ages because the pre-glazed, unitized is so much more efficient, so much better quality and just benefits galore with it.
Ray: Oh, yes. And Paul, we were on the topic a few minutes ago of the four-sided structure glaze. In addition to the high-performance of the weather seal, there’s additional multiple components and advantages to that. One of the additional items is the fact that we typically do it with the intent of no penetrations from the exterior of the glazing plane into the interior, which allows a higher degree of performance. We don’t even require thermal breaks. The system with the glazing, specifically if it’s insulated on the outboard side, the performance of the glass is what dictates the performance of the system and you don’t have the issue of all the thermal transmission by pressure bars, screws, fasteners, or mechanical means trying to put the capturing of the glazing into the building. Along with that, the penetrations typically cause areas for water infiltration or failures later on.
Paul: So with this kind of a system, you’ve got, basically, all of your framing is on the inside and your glass is on the outside, and it doesn’t need a thermal break because of the design of the system. And you’ve got the insulated glass and/or sealant provided the thermal barrier.
Ray: That is exactly correct. Now, if the designer has the desire to have exterior accentuated parts or decorative trims on the outside, what we typically do in that case is we structurally silicone those trim components to the outboard without breaching the envelope and/or the sealant joints. So we use the same reasonable means of structurally siliconing the trim caps or decorative pieces to the outboard as we do putting the glass onto the framing component.
Paul: Yeah, so it’s a very efficient system. I guess, with that then, even though it’s a structurally glazed system, you can actually put trim on the outside and have it look like a traditional framed system if that’s what the designer wants. Correct?
Ray: That is definitely correct, Paul.
Paul: So let’s talk about this 100-pound-per-square-foot water rating that your systems have. Can you give a little perspective on what is typically seen? Let’s talk a little bit about that. What the typically rating is for commercial glazing assembly, just industry standard type of system.
Ray: The industry standard that’s typical from all of my experience has always been 15% of maximum positive pressure. And normally, no less than 6 psf. That’s minimal. If we get here in Florida, and you have…which has, just to interject, a much higher positive typical pressure than the rest of the country. But if we’re using 100 psf as an average, and typical highest, everybody wants to achieve 15 psf positive. Now…
Paul: For the water test pressure?
Ray: Yes, sir, that’s correct. For the water test pressure. They don’t make it meet the requirements of 100% of the positive, they reduce it down. The reason they have done this is the original or older designs of the pressure equalized or rainscreen systems couldn’t even come close to that, either by means of the problems with the exposed joinery back in the backside or the head pressure or sill differentials that they would try and do it, they could only get maybe up to 15 psf.
Paul: So the real world [inaudible 00:13:37] 100 pound per square foot structural load, which is a significant number. And I know people, listeners outside of Florida are probably thinking, “Wow, that’s a big number for a glazing system.” And actually, the numbers even get higher than that. But you have 100 pounds per square foot for wind load and you have 15 for water, what happens when you get really high winds like a tropical storm or a hurricane? Or what can happen?
Ray: Well, Paul, you know along the east coast of Florida and some of the other areas, you can get thunderstorms in the afternoon where you can get in excess of 60 mile per hour wind gusts with the presence of rain. And as you know, I think…what is it? Somewhere around 65 or 68 psf, water pressure is what the equal to 15 psf water resistance is. So typically, what that means is, as was found out after all these new impact systems were in market and everybody keeps come and tell me, “Well, that’s hurricane-proof.” Well, first off, is we know it’s hurricane impact resistant. But the water resistance didn’t evolve to the degree that the impact in envelope protection did.
So after Jeanne and Frances and the storms back, Wilma, in the low 2004, 2005 came after this new industry and new products were on the market. And they came through the area, sat over a few of the areas and pounded them with water. And everybody was scratching their head. And I’m sure you were involved in some of the litigations they’re saying it shouldn’t have leaked. Well, they were designed with minimal water resistance, so there were leaks. And going back to it, we see that 100 psf water resistant is the normal highest positive pressure, that’s the reason we tested to 100.
Paul: You know, it’s an issue and still an issue. Will Smith, who works for my company, GCI Consultants, and is actually a prior guest on the podcast, wrote a blog article in the last month or two, which is on our website, gciconsultants.com and was addressing the very issue of hurricane glazing systems and what to expect of them. People think, “Oh, the glass is never gonna break.” Well, not true. If it gets hit with debris, it might break. The window opening’s still gonna be okay. You’re not gonna have a breach. But the other big thing, probably the biggest, is the water leakage issues which I think caught the industry by surprise. And as you said in ’04 and ’05, all these hurricane impact systems got 100-mile-an-hour wind driven rain and they leaked. And obviously, that’s not something you want to happen but it does because the standards are lower.
I’ve always said that for water leakage, the standards aren’t designed for the environment. They’re designed for what the industry’s able to product as far as systems. And, you know, 15 pounds per square foot is a challenging number for a conventional type of glazing system.
Paul: Yeah, Paul, definitely. And some of the things and the reasons we did this was we do a lot of healthcare projects and a lot of technology buildings. And those are the type of facilities that are not ready, don’t want or not set to deal with moisture, moisture getting into the building, the condensation creating issues with what is known as “sick buildings.” The attorneys have just gone bonkers are pursuing mold mitigation. You know?
Paul: Yeah. So how on earth…everybody’s having trouble getting the 15, how in the world did you get to 100?
Ray: That goes back to what I was saying, Paul. We always had the ability to do it, we finally just brought it up. It’s our standard design. The only difference is we finally tested it. I had run it up many, many….almost 30 years ago and done a test and took it up there, and there was no problem. And we finally decided, “Let’s go ahead and do the testing on all the systems.” The big problem we had is, as I’m sure you know, Paul, most of the consultants don’t have the field equipment to do anything near those pressures. In addition to that, the test labs that we originally approached, their chambers wouldn’t take that on their water, and their equipment wouldn’t get it up to it. So they had make modifications which we had to work with them to get it up to it.
The biggest challenge we see in field tests is the typical surrounding materials don’t achieve those kind of pressures.
Paul: Yeah, that’s funny, actually, that you mentioned that having the tests done at that kind of rating…it’s just something that hasn’t been done before. And I can see how it can cause the issues. So you actually took this into a test laboratory and had them run the tests for water, instead of the 12 or 15 pounds per square foot that the industry’s used to, you actually had them run it at 100 pounds per square foot. Which is a tremendously high load even without the water, and it passed.
Ray: Yes, sir. All of our systems.
Paul: Yeah, that’s impressive. Now, has there been a lot of interest in this since you…I mean, have you actually had jobs where you’ve separated yourself from the competition because of the water rating?
Ray: Yes, it has been a big advantage for us. As a matter of fact, some of our competition whose names I won’t mention, have been calling me a few names because they’ve had extreme difficulty getting even close. I know some of them tested to 50 psf. But as I’m aware of, nobody has gotten up to our 100.
Paul: So your system uses a single seal as a moisture barrier?
Ray: That is correct. It’s a face-sealed barrier wall system, as we like to call it. And it is a single silicone seal. The advantages are and the condition exists that the glass being on the face of all of the components, we have the simplicity of design that all of the weathering is done by the glass or the sealant. With a four-sided structure glaze, you have a glass to sealant to glass condition, or a glass to sealant to surround condition. Everything else is behind the glazing. So it’s either the glass or the sealant that’s doing the work. We don’t have the exposed framing joints and all of the typical conditions that are subjected and normally the big problems on the water infiltrations.
Paul: So when you compare a single seal to a dual seal, I mean, doesn’t dual seal sound better than single seal?
Ray: It sounds better, but as we’ve studied it and coordinated with the designers and the teams and even Dow Corning, one of the problems that [inaudible 00:20:52] created is if you use a completely sealed dual seal within a glazing system, where there is a failure of the frontline at a higher point, you can actually retain all the water between and within the two sealant lines which would not be good for insulated glass, it would not be good for laminated glass, it would not be good for the health of the building with the propensity of the surrounding concrete or cementitious materials to uptake the moisture.
Paul: You mentioned laminated glass, I know that’s used a lot in the hurricane impact world, particularly in south Florida and coastal areas. Have you had any issues with laminated glass? I know it’s sensitive sometimes to compatibility of surrounding materials. How do you overcome that with using sealants and glazing accessories and things like that? Have you had any problems or… Because I know that they’re out there. I see them all the time. So have you had any problems? And if not, how do you avoid them?
Ray: Okay. Paul, first off, we have not had problems with the basic systems. Now, I will say, at the onset of the hurricane impact glass when everybody was experimenting with glass clad polycarbonates and some of the other products, the polycarbonates with the urethane inner layers and bondings had problems initially from crazing when you’re using your solvent cleaners. Because the polycarbonate was in high tension. Also, over time, the urethane had a tenacity that did not allow a good difference of expansion between the plastics, the polycarbonate and the glass. And we understand that in the industry, the polycarbonates started crazing from the ultraviolet exposure and other things.
But as far as the conventional either PVBs, polyvinyl butyrals, ionoplast, or even the Century Glass original products, we haven’t had an issue with compatibility of the sealants we’ve used because we’ve coordinated with both the inner layer manufacturers and the sealant manufacturers to make sure that the incorporated products were appropriately compatible.
Paul: And you just reminded me of something else, you’re talking about the laminated glass inner layers. Which ones are using in your systems these days?
Ray: Our use goes everywhere from NA condition where we’re required to meet standard large missile glass. We have two inner layers that are capable of being used. One of them is what they call “the Vanceva storm” which is a polyvinyl butyral with the incorporation of an additional material. That one is nice in the fact that it is a little bit more competitive, but it doesn’t seem to meet the pressures in the higher performance that we need in some of the more tenacious products or special products, which we would then use, what was originally the DuPont, now is Kuraray’s product which is the ionoplast or what they call the “Century Glass.”
That has the ability to meet a higher pressure and also gives us the ability to meet what we call the “E Missile” which is an 80 foot per second 2×4 for the larger special products which are the essential facilities.
Paul: And that 80 foot per second… It’s funny, because you and I are working together on a project where this just came up on Friday at a hospital, which is an essential facility. So 80 feet per second as compared to the standard requirement of 50 feet per second. So what is your glass configuration for the… An 80 foot per second is a much, much higher load. It’s not linear. I mean, the force is greater than the 50 foot per second missile, which is [crosstalk 00:24:51].
Ray: Yeah, Paul, round numbers. The 50 foot per second is 34 miles an hour. The 80 foot per second’s around 50 mph. But as you noted, it goes up exponentially. The energy transfer of the glass is phenomenal. If we take the standard large missile glass compliant that meets and passes the standard 50 foot per second 2×4, if we shoot that with the 80 foot per second 2×4 I’m gonna tell that, typically, the 2×4 just sails through it without even slowing down too much. The heavier composite, the inner layer is what makes the difference. If we have a monolithic laminated product of two lights [SP] of quarter inch glass with an inner layer, if the 090 ionoplast, which is the Century Glass or the 077 Vanceva Storm meet it, in order to meet the 80 foot per second, we would need to go to two layers of the 90 to make it 180. Almost 3/16 of an inch of polymer plastic that goes between the two pieces of quarter inch glass to stop that 2×4. And then, ultimately pass the 9,000 cycles.
Paul: And the reason I served on the ASTM committee that developed these and the reason they have this really high load on what they call is an essential facility, the job that we’re working on together right now that has this is healthcare, it’s a hospital. And the theory being if you’ve got patients in the hospital during a hurricane, you need to design to a higher level as opposed to, say, an office building where it could be evacuated and you’re just trying to have the structure survive and protect the contents.
Ray: Yes, sir, that’s correct.
Paul: Yeah. So, you know, the codes are changing every few years. Big changes in what you’ve seen recently have been energy-related, have they not?
Ray: Other than the essential facility in Florida, throughout the nation, the energy codes continue to evolve to a higher performance standard.
Paul: Yeah. What’s being done, basically, to comply with these standards as they go up?
Ray: The components are the framing system and the glass. The glass being the majority of the fenestration and the framing being the smaller component. But the glass is the first item that needs to do it, the U-values and the Solar Heat Gain Coefficient, depending on how you’re trying to establish your energy performance. And then in addition to that, you have to keep your framing component from transferring the energy that you’re trying to keep out into the interior of the envelope.
Paul: So the practical end result is with U-values, which is basically insulation, we’re seeing insulated glass units where maybe they weren’t required before, and the Solar Heat Gain Coefficient, which is basically…my layman’s way to say it, is bounce the sun of it and not have it come through, we’re seeing high performance coating. So that system that you’re building is really pretty technologically advanced. It has insulated glass. It has laminated glass. It has high performance coatings, typically low-E coatings. It’s thermally broken. A big difference probably from when you became president back in the ’90s, huh?
Ray: Oh, big difference, Paul. Big difference. And it’s continuing to be more and more prevalent. And it’s really humorous because it’s not that we’re trying to sell anything and I’m sure the same on your end, but we still have people, almost like down here on the hurricane end, “Well, you don’t need this.” And I’m still even getting owners of buildings and developers that they argue and they don’t want to put the time and money or money into it to use the far superior glass on this.
Paul: Well, money. I’ve said this in other podcasts and, you know, money, it’s all about money, time and budget. And obviously, in a for-profit situation, you wanna spend as little as you can. And if you’re spending… As the requirements get more stringent with hurricane and with energy… With hurricane, if you live where there’s hurricanes, you should probably build to resist them. And I never understood why people didn’t wanna do that. But it’s the money thing. And with energy, it’s the same thing. And there is a return on investment over time and user comfort. It’s just a better system all the way around.
Ray: Yes, sir.
Paul: So really interesting discussion, Ray. And I thank you so much for coming on. I know it’s really interesting. And as I said, we’ve worked on quite a few projects together. I was just thinking, you know, we finished the Daytona Speedway project this year or last year, I can’t remember exactly when that was. But that was really cool. And we’re doing all of Florida train stations together and some healthcare. And you’ve kinda got a really, really great portfolio of work throughout Florida and certainly an industry leader as far as the performance and whatnot. And I look forward to doing some more cool stuff together.
Ray: Paul, thanks for the kind words. And I’ve gotta say that there’s a lot of consultants out there today that are people that, well, lack of better statement, they scare the heck out of me. I’ve got to say that typically when people ask me, “Do you recommend a consultant?” I always go straight to you, Paul, because you’re a team-spirited, high-quality involved person that does your job for the concern of the building and the customer.
Paul: Well, thank you. Thank you for that. So we’re starting a new Building Envelope newsletter and if you’d like to get on the mailing list for that you can text the word “buildingenvelope,” B-U-I-L-D-I-N-G-E-N-V-E-L-O-P-E, all one word, buildingenvelope, to 228-28. So again, text buildingenvelope to 228-28 to get signed up for our monthly Everything Building Envelope newsletter. It’s gonna have some good stuff in it, technical and of interest to the building envelope community and people that are interested in it.
So thank you, everybody, for listening. It was a really great episode. I found it very, very interesting and Ray was great. And until next time, this is Paul Beers saying, “So long.”