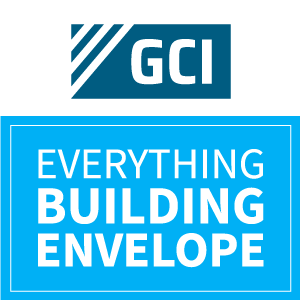
About The Everything Building Envelope Podcast: Everything Building Envelope℠ is a dedicated podcast and video forum for understanding the building envelope. Our podcast series discusses current trends and issues that contractors, developers and building owners have to deal with related to pre and post construction. Our series touches on various topics related to water infiltration, litigation and construction methods related to the building envelope.
https://www.everythingbuildingenvelope.com
*** Subscribe to the show and leave us a Review on ITunes!
Hello, everyone. Welcome to “Everything Building Envelope.” I’m your host, Paul Beers. “Everything Building Envelope Podcast” features topics of interest related to the exterior building envelope, including waterproofing, glazing, cladding, and roofing. We feature relevant topics and guests and want to engage you, the listener, with thought-provoking content. Please visit our website www.everythingbuildingenvelope.com where you’ll find access to each episode along with show notes and a special video section with bonus content. Today’s topic is “Hurricane Glazing.” The issue date for this episode is June 1, which coincidentally is also the official start of hurricane season in the United States.
I know this year, the forecast is for an about an average season and, you know, having followed this for all these years, that really doesn’t mean anything to me. We’ve had seasons that, the year Hurricane Andrew came, 1992, was supposed to be a diminished season. And, of course, it only takes one and then other seasons which were supposed to be really bad, not much happened. So it’s a guessing game, who knows? One could come next week. One could come not at all. And, you know, I guess if you live in a hurricane-prone area, the real thing to consider is that it’s not if, it’s when the storm is gonna come. I lived in South Florida since 1968. And honestly, it was until 1992 before we really had anything semi-serious.
It was Hurricane Andrew and that was not that bad where I was. And it was actually 2004 with Hurricanes Frances and Jeanne before we really got hit. And then guess what? The next year, 2005, we got hit again. So there’s no predicting, natural disasters, when they’re gonna occur. In this episode, we’re gonna talk about the history of hurricane glazing, how it came about, how it developed into a cottage industry in Florida and beyond. We’re also gonna talk about how there are many uses for hurricane glazing beyond hurricanes. I bet you didn’t know that. But these systems are really good, you know. They’re good for security, they’re good for natural disasters, and they can be used for other applications such as bomb blast protection, tornadoes, seismic events, earthquakes, security, civil unrest. They’re good for energy and the glass that’s typically used, laminated glass, is always, even before the hurricane market came into existence, was used for acoustics.
So let’s talk about where it all began. The hurricanes, as we all know, have been around for forever as far as we’re concerned. First, let’s talk about where it all began. Hurricanes have been around for a very, very long time. However, the characteristics of where they strike have changed a lot. As time’s gone by, population density in coastal areas has increased significantly. So storms that came through say, 100 years ago, maybe the worst hurricane ever hardly hit any population, particularly when you think of areas like coastal Atlantic and Gulf areas. So now, when they come through, there’s many, many people in harm’s way. The first real evidence of storm damage in damaged urban areas, was actually in 1982, I believe. Hurricane Alicia in downtown Houston caused a tremendous amount of glass breakage in the downtown area. And researchers went in, investigators went in after the fact and took a look at what happened and tried to figure out why this occurred.
What they found was that, you know, hurricanes have always been known for high wind. But what they didn’t really account for was the fact that this wind also picks up debris and flings it around. So in downtown Houston, many of the buildings had roof gravel on the roofs. And the gravel basically was there to protect the roof and to weigh it down, whatever. What was not really contemplated was the fact that in a severe windstorm, such as a hurricane, this gravel could be lifted and hurled at the building next door and that’s exactly what happened. They would look at a building, say it was a 60-story building and up on the 50th, the 60th floor, very little damage, but from 50 and below, all kinds of glass breakage. And that really didn’t jive with conventional wisdom that the higher you went in the air, the worse it got.
So looking into it further, they saw the building next door was a 50-story building and it had roof gravel or used to have roof gravel and it made a lot of sense that things were blowing off of other adjacent buildings and causing the damage to their neighbors. So that was well documented. Nothing was really done in the codes and standards arena. There were some research papers that were developed, I think there was even some code changes proposed, and basically wasn’t adopted. I think it was the, “Well, that happened to them, it’s not gonna happen to me,” attitude prevail at the time. The next big event which really was a game changer for the hurricane protection business and the glazing industry was Hurricane Andrew in South Florida in 1992. Hurricane Andrew, at the time, was called a Category 5 hurricane. It may have been revised, it’s obviously debatable, to a strong Category 4.
But the eye of Hurricane Andrew came into Miami-Dade County, the southern part of Miami-Dade County in 1992 and caused tremendous damage. There were housing developments that were completely flattened, there were commercial buildings that had a lot of glass loss, roofs were blown off. I think at the time, try and remember, I believe that the damage figure was 20-some-odd billion dollars. And it was just a magnitude way greater than anything that had ever been seen before in the U.S. It was staggering losses, it turned the insurance market upside down, it caused all the building codes to really be looked at. In Miami-Dade County, they always thought that…well, they were proud of their code, it was the hurricane code and they worked hard on it, they designed it for hurricane winds, the strongest hurricane winds. And it was the most advanced code in the nation, probably in the world for wind storms by far. And the shock and dismay when this hurricane came through and damaged everything was really incomprehensible.
So they put together a commission, The Metro Dade Building Code Evaluation Task Force, and the job…and it was comprised of very high-level building officials, wind experts, university researchers, it was a who’s who of the hurricane business. One of the members, I remember, was Herb Saffir who invented the Saffir-Simpson Hurricane Scale, for example. So they were tasked with examining the damage, looking at the code and figuring out what went wrong and how to fix it. They held a lot of hearings over probably a year, a year and a half’s time. They looked at all the damage mechanisms which was basically roofs blew off, garage doors caved in, windows and doors were lost. And when you lose the integrity of the building envelope, windows, doors, things like that, that causes something called Internal Pressurization.
So if you have the windows and doors intact, the hurricane basically stays outside. When you start losing windows and doors, then the storm basically comes inside. So the pressure when the envelope is intact on the roof, there’s a very, very strong uplift pressure trying to pull it off and that’s what they designed for, and the design was correct for that. When you add in loss of the building envelope such as broken windows, garage door failures, things like that, and the storm comes inside, not only do you have the uplift on the roof trying to pull it off, but you’ve got the wind inside trying to push it off. So you’ve doubled the pressure. And the buildings were not designed for that kind of pressure. And the result was really tragic that many, many homes would have…countless people after the storm said, “Yes, I was in there, the windows blew and as fast as that happened, the roof came off.”
And obviously it was terrifying and it was not anticipated and it was not something that anybody wanted to happen. If you live in a hurricane-prone area, obviously, you should design for it and you don’t want roofs coming off. So long story…I was gonna say “long story short,” but it’s a long story. So the end result was after further research and investigation, it was really determined that one of the keys to having a viable protection of buildings and to strengthening the code was to eliminate the problem of windows coming off. So the obvious solution at the time was, let’s board everything up. Let’s cover the windows so they can’t get broken, also storm shutters. And by the way, the storm shutters from back in that era, many of them could not stop…they were wind-resistant, but also could not stop wind-borne debris.
They were made out of materials such as PVC and very lightweight metals and if you had a significant debris item blowing in the wind, it would go right through them and the window behind and then all the trouble began. So after the codes had determined, the Task Force had determined that they needed to strengthen the code and they wanted to board everything up, there was also an effort…and I was involved in this, to promote, rather than saying a prescriptive standard, let’s board everything up, let’s have a performance requirement, which is, let’s develop a test that you can put building products in front of, and if they pass the test, then it’s worthy and if it doesn’t, it’s not. And this would allow for a lot of other options that maybe weren’t even contemplated in 1993, let’s say, when this debate was going on. And the Building Code Evaluation Task Force liked that idea.
There was…and what we proposed back then was, we proposed a task where we shot, fired 2 by 4s out of an air can, and, you know, calibrated to a certain weight, certain speed, and we fired them at these test specimens and they were supposed to bounce off basically, not penetrate them. And, you know, the obvious thing that you would think of as a hurricane shutter, but also we were in the process of developing hurricane glazing systems that would also bounce the missile. Now bouncing the missile is wonderful, but if you think about it, in a hurricane, after the missile, product gets hit with debris, what happens? Well, the wind doesn’t just stop, then the product has to survive the winds that follow. And they can be very, very severe, obviously, you know, over 100 miles an hour and they’re cyclic which means they cause vibration and they can go on for hours or even days afterwards.
So the second part of what we proposed was a cyclic wind loading test. And we proposed 18,000 wind cycles, which there was some scientific research that indicated that, in a storm, the cyclical nature of the winds could cause a tremendous amount of cycles. And I’m trying to remember, I think it was 40,000, 50,000 or more cycles in a windstorm, such as a hurricane. So we reduced that to 18,000 and there was research behind it. In fact, the writer from Australia of the research paper was the one who designed the 18,000 cycles for us. And we proposed that along…so first, you impact the test specimen, then you do the wind cycles, and if it survives all that, then it’s worthy. And the idea was that, not only would it be hurricane shutters, but it would be impact glazing, as well. There was great debate over a couple of years, a lot of opposition to it in the beginning, which was really surprising to me. Basically, everybody was opposed to it initially, I guess, you know, change is not good.
The glazing industry, the hurricane shutter industry, the home builders, many special interests trying to defeat the code, and the big argument was that we were gonna make buildings unaffordable because this was gonna be so expensive. Well, the general public really wanted to be protected. “The Miami Herald” was coming out with articles all the time, I say “all the time,” on a regular basis that we’re basically advocating doing the right thing, and ultimately the Dade County Commission passed this. So now we had the new codes in place and the next big challenge was developing systems that would comply and it wasn’t easy. I mean, there was a lot of trial and error, a lot of experimentation. We found out quickly that the impact bouncing the missile off of the glass or the shutter was the easy part. And actually keeping it in place during the cyclic loading was really the hard part.
So these systems are basically fairly complex. When I say “systems,” you know, hurricane impact glass alone is not gonna really do anything for you, neither is the strongest hurricane framing that you can find, what you need is everything to work together. So the systems that were developed initially, and basically are still in use, was you would have a wind resistant frame, typically aluminum. Although there certainly are other materials that could work, you had impact glass that could bounce the missile. And then the real key to it all was keeping the glass in the frame. And we did this with structural silicone glazing. So these three parts together were what it took to be able to pass the test. Again, very complex. It sounds, maybe it sounds simple, but very complex because there were a lot of variables. For instance, the strongest glass wasn’t necessarily the best glass for these systems. If it was really stiff and rigid, the missile would go sailing right through it, whereas if maybe it had a little bit of flexibility to it, when it hit, then the missile would bounce off of it.
So as time went on, more systems got developed. And then the codes basically started to consider it…after it got adopted in Miami-Dade County, we took it to the Southern Building Code Congress, which was the code at that time in Florida and most of the hurricane-prone areas in the Atlantic and Gulf Coast, and it was rejected. And this happened two or three years in a row. They basically said that it wasn’t a consensus standard, and that was what they needed or what they wanted, and otherwise, they weren’t gonna approve it. The same folks who were fighting this in Dade County were doing their thing at the Southern Building Code Congress, as well. We took it to ASTM, we developed a couple of standards, ASTM 1887, 1886, and 1996. One was a specification for hurricane testing and the other was the test method itself.
And over a matter of a few years and, you know, ASTM is a consensus standards organization, so everyone has to agree. And they have a process to actually have that happen. It’s really a great system. And it wasn’t easy, but eventually, these two standards were published. When that happened, the International Building Code had come into effect or been put forth at that point. And with the ASTM standards, it was put into the International Building Code. The International building code was also the basis for a new effort in Florida, the Florida Building Code, and the same codes basically came into, or the ASTM standards that were in the International Building Code and the requirement for impact protection became part of the Florida Building Code.
So, here we are in 2016 and after this tumultuous beginning, the codes, the hurricane glazing codes are now well accepted. They didn’t ruin construction. In fact, if you go to South Florida these days, particularly Miami, it’s shocking how many projects are under construction. And these are big buildings. My company is working on one right now that’s 80 stories in Miami. So the codes, yes, it added expense, but no, it didn’t cause construction to stop or put the industry out of business, make buildings or housing unaffordable. They’re more expensive in South Florida because of this, yes. But as I said before, if you live in an area where there’s hurricanes, then, of course, you want to be able to resist it. And I can tell you having lived through three hurricanes in ’04 and ’05, in both cases, I lived in a townhouse that had impact-resistant hurricane shutters, storm panels. That’s scary enough having the shutters up, but it’s really scary you know, I can’t imagine not having had them and the fear that I would have felt had I been in an unprotected building.
Of course, I know probably more than the average person does, but it just makes sense. So where are we today with these systems? Well, it’s a mainstream item. You’ll find all of the companies in hurricane-prone areas offer these systems. In fact, now that they offer them, they aggressively market them and this is from, you know, mom-and-pop window companies, right on up to the biggest curtain wall and glazing system manufacturers. The way things work these days is that you have to have a tested and approved system. Miami-Dade County has a product approval system, so does the Florida Building Code. And these codes have protocols and they require testing and design and testing of the systems. And then they require what we call a Notice of Acceptance document that’s ultimately reviewed and produced by the building code authorities.
So let’s look at where we are with these systems today. What’s required to get approval in the hurricane areas, where are the codes, who approves them? Well, here we are in 2016 and these systems are now mainstream in the glazing industry. They’re very well accepted, actually, not just in the glazing industry, by the building industry, the general public, the insurance industry, there’s a lot of folks that are very big fans and very engaged with this. And the process now as it’s, kind of, been since the beginning is you have to take a system, design it, bring it into a laboratory, and test it to all the various performance requirements for impact testing, cyclic loading. You also have to test it for structural loading, you have to test it for water infiltration, for air infiltration, there’s many tests that need to be done. When that’s all done, then a set of engineer drawings and documents need to be put together and submitted to a product approval agency.
The two primary product approval agencies for these systems are…the one that’s been doing it all along is Miami-Dade County Product Control, and also the Florida Building Code has a product approval system. So these are submitted and reviewed by these organizations or these approval agencies and ultimately, they’re issued a Notice Of Acceptance or an NOA document. And that’s really where the rubber meets the road for evaluating these, using these systems on projects, what their loads are, and being able to basically prove performance. It’s one thing to say this is hurricane-proof for hurricane-resistant. You know, there were a lot of claims in that regard as these systems were being developed with window film and other things that really didn’t work. And, you know, what sorted that all out was the product approval system and having the ability to see, you know, what has been through the testing and the approval process.
So, these systems have really performed well. So, you know, they were developed in the ’90s or began to be developed in the ’90s and what was a little scary was, until 2004, there wasn’t really a significant windstorm event in any of the areas where these systems were being used to see if they really worked. Well, in 2004, that ended in a big way, there were two…there were actually more than two. There were multiple storms in Florida. There was Charlie, Frances, Jeanne. But the big test that I found was actually Hurricane Ivan in the Cayman Islands. We’d been involved down there working on several bank buildings. Cayman National Bank was one, Swiss Bank, which is now UBS, was another, and then a few other buildings. And we had helped them, you know, develop and install the hurricane impact glazing systems.
These were commercial buildings so they were curtain wall framing with laminated glass and silicone. Anyway, in 2004, Grand Cayman gets hit with Hurricane Ivan, a Category 4/5 storm that was a direct hit. It caused massive damage. Most of the entire island was covered with storm surge, the winds were tremendous, the damage was extensive. Surprisingly, there was very little loss, if any loss of life. But this was kind of the, “Oh, no, here, we’re gonna find out how these things really work,” moment. So I went down there about three weeks after the storm to help with the recovery and, lo and behold, found out that there was a lot of damage throughout the island. In fact, I remember driving down the street after being picked up at the airport and having to have special permission, by the way, to fly in there. And driving down the street and basically seeing that we’re riding along and it’s cli-clink [SP], cli-clink, cli-clink, we’re riding over power lines that are down in the road. There was no power on the island, no water, everywhere you looked, there was severely damaged buildings.
But guess what? Cayman Bank, Cayman National Bank, Swiss Bank, the buildings that we worked on, they did fine. They were, you know, they had some superficial damage, but they were basically in good shape and it was really heartening to see how well these systems worked. And that’s been demonstrated time and time again. The last big storm in Florida that caused a lot of damage was Hurricane Wilma. And there was a lot of damage to windows and doors, but all the damage to windows and doors were buildings that were built before the code changes. So those were ’80s, ’70s, you know, and earlier. And my company investigated hundreds and hundreds, maybe even thousands of buildings that had storm damage and to the windows and doors and it was extensive and it was millions upon millions upon millions of dollars of damage.
But we didn’t look at any new buildings. We didn’t look at any buildings that had hurricane impact glass. You know why? Because they all performed well. They did well and they, you know, the worst thing that happens with those systems as they get hit with debris and the glass cracks or breaks, but it stays in the frame, the building’s protected. So it can be replaced over time, not under duress and it’s a really important point to consider with these kinds of systems. So what are the materials that are being used to make up these systems these days? You know, again, we’re into this more than 25 years now, since Hurricane Andrew, and the systems have evolved and in the beginning, we were, kind of, trying to adapt existing systems into and make them work. And now, obviously, you’ve got a lot of smart people in the glazing industry and these systems have been custom-designed to meet the need.
And there’s been materials that have been developed particularly in the glass side of things that were made…I shouldn’t say “just for,” but that were made with the hurricane market in mind. So laminate glass, we’ve seen a lot of iterations of it over the years, some of it good, some of it not so good. They used to have a lot of these resin base liquid pour inner layers. There may still be some out there that are fine, but there were a lot of them that really didn’t perform well. They would pass the test, but then you get them out in the field and two years later, the glass was clouding up and the edges were…you couldn’t even see through them, delaminating. So durability was a big concern and the PVB inner layers, which are still used today and it’s a good solid product, the PVB inner layers, you know, from a performance standpoint had struggled with the large missile tests.
You know, with some systems, you could get it to pass, but not all. The small missile tests which I didn’t talk about…so there’s a small missile test above 30 feet of building elevation where rather than shooting a 2 by 4 at the glass, you shoot steel balls or ball bearings to simulate roof gravel and PVB is used a lot for that market. However, new products have come along, the one that comes to mind is an ionoplast interlayer which is a different material than PVB, polyvinyl butyral. And one of the trade names for that is SentryGlas Plus, that’s a very commonly used system these days. It’s proven very well for performance, also for durability. PVB can be susceptible to moisture around the edges and SentryGlas Plus is not. So even in glass handrails with exposed edges, things like that, it works well, you know. So also what’s going on now is the energy codes have been increased quite a bit in this decade, I guess I would say.
And the requirements now are…even in Florida, you know, you have to have a high-performance coating, like a low-E coding, and you have to use insulated glass. So people listening in the rest of the country are thinking, “Hello, we’ve been doing this for so long.” But in Florida, the market was always monolithic glass. So for hurricanes, you would have probably a tinted, you know, gray or bronze tinted glass with a laminated glass inner layer, and that was it. Now we’re seeing systems, and it’s just coming into play now with the recent code changes, where we have insulated, laminated glass units.
These are very heavy, very stout units, you would have, just as an example, you would have a regular light of glass, say heat-strengthened glass.
Then you would have a half-inch airspace and then you would have a laminated unit that could be just for example, 9/16-inch thick, two pieces of 1/4 inch glass with the interlayer and it ends up being…trying to do my math here, like an inch and a half or so thick. And maybe a little bit less than that. And, you know, so this doesn’t fit in the average glazing frame. So the new framing members have to be designed to accommodate this. You still need to keep it in the frame after a break so there’s got to be room for the silicone. And these systems exist and not only exists with the Florida manufacturers, the national manufacturers, anybody that sells into…there’s even manufacturers from Canada that sell into the hurricane glazing market. And in fact, the Canadian manufacturers are big in the Caribbean, as well. And the Caribbean has…although I don’t know if they have code requirements in all these islands.
If you build a significant building in the Caribbean, hospital, resort hotel, government building, typically you’ll see a Miami-Dade specification because they’re in harm’s way even more so than coastal areas of the U.S. So these systems are very mainstream now. They’re out there, they’re easy to find. And basically, they’re common, I guess they’re common would be the thing I would say. So, you know, the title of this podcast, we talked about hurricane glazing systems and, you know, how can you use them? Or can they be used beyond the hurricane market? And the answer is a resounding yes. So the system, if you think about it, is a really durable, hard to crack into type of system. You’ve got a very strong frame, you’ve got state of the art laminated glass that you can’t shoot 2 by 4s through.
So hurricane glazing systems be used beyond the hurricane market. If you think about it, they’re really strong framing systems, really strong glass, it can survive impacts from flying 2 by 4s, it can survive tremendous amounts of wind pressure and wind cycle. So surely, there’s other places that this will work and the answer is a resounding yes. Yes, you can use them in other places. So some of the markets that these types of systems can be tested and adapted to are bomb blasts, tornadoes, security, breaking and entering, civil unrest, things like that, seismic earthquakes and acoustic. If you think about it, these systems, as strong as they are, are a perfect fit for this. And in fact, these tests have been done. So if you have a hurricane-resistant, you know, state of the art hurricane-resistant system, say, in Texas, you may not even know it.
But this system is good for, not only for the hurricane, but it’s also…if there was a seismic event, in seismic events, the big danger is glass breaking and falling out of the frame. And it’s gonna stay in the frame because, you know, short of a structural failure of the building, it’s gonna stay in the frame because the glass is attached with structural silicone. Bomb blasts, a much higher load, it’s an impulse load, like a millisecond as opposed to a hurricane, which goes on for quite a long time. But the fact is that, you know, again, you’ve got a glass product that’s gonna resist the impulse. You’ve got a very strong framing system and it’s attached to the frame. Certainly, you would wanna test it if you’re gonna use it for a bomb blast application, but the same type of design works for that, as well. And then the big area of opportunity that I don’t think it’s being used much, but maybe it should be, is in tornado-prone areas.
A tornado is basically a severe windstorm. It’s obviously a lot smaller in size and it can be different intensities. Although most hurricanes, most tornadoes don’t have winds higher or any higher than a hurricane. And you look at critical facilities in tornado-prone areas, such as public buildings, hospitals, shelters, schools, things like that, I don’t think that they…in fact, I know most of them, if not all of them, well, I shouldn’t say “if not all of them,” but a vast majority don’t have any special considerations for these types of events, these tornadoes. You know, you go hide under a desk or you go into the hallway, things like that. And I’d suggest to you that it’s appropriate to consider like in a hospital that has critical patient care, where you can evacuate the patients, it’s appropriate to consider hardening the building.
So in the event that this does occur, they do have a tornado, you’re not gonna have property and life at near the risk you would without these types of windows. And from a security standpoint, we’ve already seen this where hurricane systems of have been put into say, for example, storefronts and the bad guys come along and try and throw bricks or garbage cans or whatever through the window to rob the store, and they bounce off. And they can sit there and throw that brick 100 times at it and it’s not gonna go through. They’re gonna get tired and go somewhere else before they ever get in. So from a security standpoint, it’s really good. Same thing would apply to start civil unrest, you know, if there’s rioting or looting, say, after a storm, again, the buildings with the hurricane-resistant systems, they’re not getting in without significant effort.
And typically, there’ll be other places to go and have a lot easier time with it. Before the hurricane market, laminated glass was used a lot for acoustics and sound attenuation. It was mainly used actually in airports. And this is still a perk that you get when you put these systems in. People all the time…I have friends who put impact windows in their house and they say, “Oh, wow, I never realized how much quieter it would be inside now that I’ve got this new glass.” Upgrading or putting in new impact windows also leaves an opportunity for glazing to be upgraded to meet the state of the art energy codes. You can put low-E coatings into it, you can make it into laminated glass units. So the opportunities for the hurricane type systems go far beyond the hurricane market. And they are being used in instances for this today, you know.
So the market’s well accepted, the hurricane market’s well accepted, there are other applications for it to grow. And it’s really interesting to see, you know, how things have evolved. So that’s the story of “The Hurricane Glazing System,” where it came from and where it is today. This concludes this episode of, “Everything Building Envelope Podcast.” I hope you found it interesting and thought-provoking. Please subscribe to the “Everything Building Envelope Podcast” at iTunes and Android, outlets such as Stitcher, or by visiting www.everythingbuildingenvelope.com where you’ll find the show notes, previous episodes, and bonus content, videos and things of that sort.
As an added bonus for visiting the www.everythingbuildingenvelope.com, we’ve added a free report you can download entitled “Seven Common Pitfalls To Avoid With Hurricane Glazing Systems.” These types of systems are expensive and critical for protecting people and property and you want to avoid these problems that could result in an outcome that’s less than what you were hoping for.
So, thank you for listening. Please tell your friends and colleagues about the “Everything Building Envelope Podcast.” This is Paul Beers saying so long, until next time.