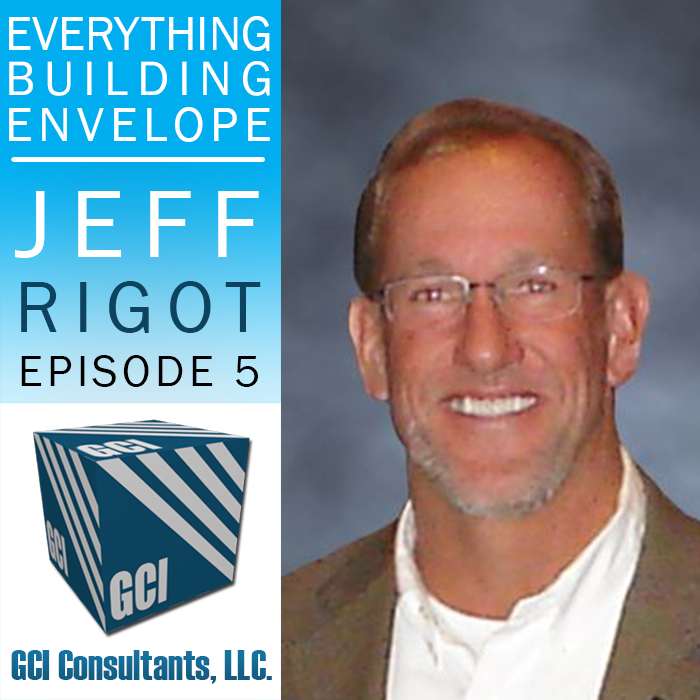
About The Everything Building Envelope Podcast: Everything Building Envelope℠ is a dedicated podcast and video forum for understanding the building envelope. Our podcast series discusses current trends and issues that contractors, developers and building owners have to deal with related to pre and post construction. Our series touches on various topics related to water infiltration, litigation and construction methods related to the building envelope.
https://www.everythingbuildingenvelope.com
*** Subscribe to the show and leave us a Review on ITunes!
Paul: Hello, everyone. Welcome to Everything Building Envelope. I’m your host Paul Beers. Everything Building Envelope podcast features topics of interest related to the XCA building envelope, including waterproofing, glazing, cladding, and roofing. We feature relevant topics in guests, and want to engage you, the listener, with thought-provoking content. Please visit our website, www.everythingbuildingenvelope.com, where you’ll find access to each episode, along with show notes and a special video selection with bonus content. Please subscribe to the Everything Building Envelope Podcast on iTunes and Stitcher. We’ve got a really interesting topic today, revolves around architectural glass and emerging trends in the industry. Really excited about our guest, somebody I’ve known for a long time, Jeff Rigget, who works with Viracon in the Florida and Caribbean territory. Hello, there, Jeff.
Jeff: Good morning.
Paul: Well, thanks very much for coming along today, and I know that this is gonna really be of interest to our listeners. Before we dive into the topic, could you maybe tell us a little bit about your background?
Jeff: You bet. But first off, Paul, I just want to say thank you for yourself and GTI for arranging the podcast today, and welcome into all the folks who are listening or will be listening. So I started my career, business, we’re dating ourselves here, but back in the 1980s with Conair company at the time, the metal framing side of the architectural window business up in Atlanta in the southeast, in field sales. And late in the 80s, I left Conair, went to work for a glazing contractor in Alabama, more or less in the sales side of the business as well, still promoting the Conair product through this glazing contractor.
And then in the early 90s, after Hurricane Andrew hit hard, there was a need for development of product, as you recall, for the upcoming hurricane codes that were…you heavily invested in time in generating. So Conair came calling, and I went back to Conair to head down to Miami in the early 1990s, around ’93 or ’94. Again, it was just after Andrew, in an effort to basically spearhead the business development and the design side of all things hurricane impact that were to forthcome with the 1994 South Florida Building Code. And so I did that, goodness, for three or four years. That carried me up from to about ’96 or ’97, and working at the test labs with Conair and developing the testing product and getting it ready for registration in South Florida to do business, I was buying glass at that time from Viracon.
We were buying laminated glass to use as install panels for the hurricane testing, and obviously I had a relationship with Viracon in years past, and always had a great deal of respect for the company and its leadership, and made the transition over to Viracon in about 1997, ’98, been there ever since, and basically in a business development role here in Florida, and as you mentioned, in the Caribbean too, in sales and marketing promoting for Viracon. So I’ve been blessed to work for two pretty good companies in my career, both Conair on the metal side and now Viracon on the glass side.
Paul: Yeah, and Viracon, you know, we work with them a lot, and they really are one of the leaders in the industry. Maybe you could tell the listeners a little bit about who they are and what they do as far as how they fit into the industry.
Jeff: Sure. So Viracon, probably the biggest misnomer that I get quite often is folks, particularly architects, think we’re a glass manufacturer. And so I’ll establish that fine line between the two. We’re actually a glass fabricator. The manufacturing of glass is done by names such as TPG and Pilkington, Cardinal here in North America, Guardian, and AGC being the fifth. So those are the folks that melt the sand, Paul, and make the large raw still sheets of glass that we then take as a fabricator, and then we transform that into value-added products specific to a building precise design. All things such as cutting glass, heat treating it, adding solar energy efficient coatings, which we’ll discuss later, laminating it for threat mitigation, whether it be impact for hurricane or for a blast or other threats, insulating glass… So all things value added to the outside of the building envelope with respect to architectural commercial glass. Viracon is headquartered in Minnesota.
We’ve been in business now for about 45 years, memory serves, and we have offices and manufacturing plants in Statesboro, Georgia, as well as Southern Utah in St. George. So we have three North American manufacturing plants, and then one in Sao Paulo, Brazil. Main Glassec. We have a joint venture with a company in Brazil servicing the Latin America, South America, again called Glassec.
Paul: So Jeff, I’ve been to a couple of the Viracon facilities, the one in Statesboro and the one, forgive me if I mispronounce this, Oatana, I think I got that right.
Jeff: Well, done.
Paul: And they are really impressive. I mean, they are very large, they’re state of the art, and I think it reflects the quality of the product that Viracon produces. I know that, you know, nobody’s perfect, but Viracon, for sure, in my book, seems to be, you know, one of the leaders in quality. So, you know, you got to give credit where credit is due. So let’s talk a little bit… Let’s get into today’s topic, you know, trends in the glazing industry. The thing that really gets… The questions that we get asked a lot now by architects and others, is about the energy code. It’s a big deal. Obviously, it’s a big focus. You know, buildings use a lot more energy than, say, automobiles do, and there’s been a lot of… I guess I would say the codes have evolved over time. In Florida, the 2014 commercial residential energy code brought some big changes to the market, and I was hoping that you could talk about that a little bit, such as, you know, when it was adopted, and what the changes were, et cetera.
Jeff: Sure. You know, it’s interesting, when you think about energy codes in Florida, you know, it is a relative new environment for us here. We’re sort of behind the 8-ball with the balance of the country that’s been dealing with higher energy efficiency on their buildings for a number of years to the ICC. Florida did adapt an energy code in the 2014, and the most current code, that it enacted, actually, in July, Paul, of 2015. So it’s a 14 building code but enacted in July of 15. So there’s a date to remember. So permits that were pulled prior to July 1st of last year actually would have been permitted under the 2010 Florida Building Code, of which there was actually an energy requirement within that code, but it was not enforced. There may have been some local enforcements, but it didn’t become mandatory until the enactment of the ’14 code again in July of 15.
And with that enactment came, as you stated, major changes in the energy requirements to… We’ll keep it, for purposes of this call, to the building envelope. So windows and doors, fixed glazing in general, now have to comply prescriptively, or alternatively with a Whole-Building Energy Modeling compliance, and the prescriptive compliance pathway has fixed glazing, performing to a SHGC, Paul, of .25, and a U factor of .50. And basically, that correlates to using insulated and laminated for hurricane impact units. So no longer, prescriptively, does Florida comply with the energy requirements using just a model of the laminated impact units. It would have to be insulated to meet those requirements. Basically, we’re asking…
Paul: I can remember, you know, like forever, the energy…glass that was for energy in Florida was like bronze tinted glass, and this is obviously a big change from that. And people in the industry, I guess even myself included to some extent, didn’t have to pay a lot of attention to the energy requirements. Before we talk about the performance path you mentioned already, can you just… You mentioned… So SHGC a U value. Can you just sort of explain each of those values for us?
Jeff: Sure. So Solar Heat Gain Coefficiency or SHGC basically correlates to the amount of radiant energy that’s transmitted through the glass from the solar spectrum, of course, the sun. So in layman’s terms, an SHGC of .25 we’re asking the glass in the window to block about 75% of the radiant heat energy that would be transferred through it, which is a pretty aggressive number. The U factor, I’ll step back and point out that the lower that SHGC value, the higher the performance of the glazing. So for example, a .20 SHGC is more energy-efficient than a .25, if that makes sense. So the lower the number, the better the performance. U value is the air to air temperature conductivity through the glazing. It’s the inverse of R-value. So a glazing U value, let’s say an insulated unit with a low-e coating has a U value of .25. That correlates to an R-value of 4. Remember, R value is the inverse of U, so you right away see that even in an insulated unit with a very high performing low-e coating, a U value of .25 is only an R of 4. So glass is highly conductive to air and to heat for that matter. So the SHGC and the U factor are the two primary values in the energy code that MBPs are looking at when they’re doing their energy modeling. There are some other things to consider.
Obviously, ultraviolet light transmittance. You want to try to minimize that. Not code required, but things that architects should have on their design radar screen. Invisible light. You know, you want to be able to balance the proper amount of visible light for the nature and the use of the building, relative to the SHGC requirements, whether it be the .25 prescriptively, or something higher than that, if it’s found through Whole-Building Energy Modeling. So you want to balance the right size of visible light transmittance for the building need as well.
Paul: Let me ask you another question. You mentioned high-performance low-e coatings. You know, that’s something we hear a lot about. And I just put new windows in my house in Florida that have the low-e coatings on them. Can you kind of talk a little bit about of what…? Well, I guess my first question would be, is low-e coating the state of the art these days? I mean, the follow-up is… Just, you know, what’s it all about?
Jeff: Yeah. So I’ll try to keep that very complex answer short, if possible. So bear with me. Coatings… I’ll just step back. All coatings relative to glass technology, there are essential metals that are embedded under the glass surface for energy efficiency. And a little bit before my time, and I think before yours as well, I remember back in the mid-70s, the flashcube reflective buildings that were being designed with these very high mirrored like coatings, which in some instances are still very much used today. The benefits of those coatings obviously being mirrored, in reflectivity they were negating the solar heat gain transmittance through the glass, but also they were negating valuable visible light transmittance. So they were very good energy performers relative to SHGC, but not very friendly to visible light transmittance. So along came in the 80s, low emissivity coatings. Again, same, same technology, more silver based metals than anything else, and these were specially selected coatings, Paul. They enabled… the glass or the coating enabled the passage of the all-important natural visible daylight transmittance, and had fairly good solar heat gain reflectivity, not as high as the mirrored reflectors prior, but it was a good balance, if you will. Natural daylight coming through the glass with relatively good SHGC performance.
Today, to your question, what would be considered state of the art today, what we see the industry, at least here in the US, we see a combination of the two, low-e and the solar reflective coatings, and more of a hybrid, if you will, where you get a unique exterior vibrancy or radiance to the coating, yet you get the natural passage of daylight. So at first glance, some of these buildings, and you’re familiar with them throughout Florida, mostly in Miami on the high rise towers, you get a very vibrant exterior appearance visually, but you can see through the window itself. There’s a view into the building from… into the public space from the exterior streets case. So they’re more of a welcoming type coating. And we can tune, or the market can tune these coatings to the amount of reflectivity that’s visually valuable for the design. So those are hybrid coatings. They’re very effective with solar heat gain performance and also very effective for natural visible light transmittance, again depending upon the nature and use of the building itself.
Paul: And you guys have a lot of flexibility with coming up with what the architect wants as far as color goes, by blending glass tints and coatings and things like that, and even air lighters. Correct?
Jeff: We do. So one of the things that makes Viracon unique in the marketplace is we’re a fabricator that we self-perform our own coatings. So we design, engineer and manufacture both reflective and low emissivity coatings and the hybrid coatings. And we have the ability of doing it in-house, therefore, we can apply it to any substrate. So any of the available raw tints that I mentioned the manufacturers produce earlier in the conversation, we can apply to any of those substrates, and for that matter, multiple surfaces. So we have more flexibility, being a self-performed coating company offering a more versatile package for designers and developers to fine-tune exactly the glass that they’re looking for, both visually and from a performance standpoint of the building.
Paul: Jeff, going down memory lane, I remember you and I were working on a project in the Caribbean, and the architect said he wanted the glass to be the same color as the bottom of a coke bottle.
Jeff: Coke bottle green, as I recall the conversation went, yeah.
Paul: But we did it.
Jeff: We did it. Yeah, we did it. So yeah, and it’s a great point. One of the things that folks know in the industry is that clear glass isn’t really clear. There’s an iron content in the raw material itself that tends to leave a light green tint. That’s the name, the Coke bottle green tint of clear glass. So years ago, the manufacturers, the raw manufacturers, developed what was called low iron glass, from a retail perspective, to try to get that ultra-visible transparency of the glass, you know, to… again, from more of a retail perspective. So you hear the term low iron glass going around in the marketplace, and that’s just that. It’s designed and intended to maximize the transmittance and to reduce that greenish hue that’s typical of clear glass.
Paul: Clear glass that’s really clear, owners don’t like paying for it, though. I can tell you from the times we’ve looked at it. …Little… not so much glass, but we’ve got a big building, doesn’t always go so well when it gets to budget time.
Jeff: Well, it’s a great point. You know, when low iron first was introduced, you know, each of these five manufacturers now, they all had their own version. Star Fire from KBG, for example, or Optic White from Covington or others. As competition entered, the pricing did come down, but it is still today a premium. And I think it’s reasonably specific. You know, you see… There’s such a demand in Florida from a development standpoint that rural entry parts of construction, I would say that the Northeast and even the Midwest, you see more use of the low iron product there, where it’s a little bit more accepted from a cost standpoint that… Yeah, hopefully, you’ll see more of it. I’m starting to see specs change where architects are always pushing the envelope and trying to maximize the light in transparency in glass. INC [SP] [inaudible 00:18:02]
Paul: Nice. So we were talking before about the energy code and the prescriptive path versus the performance path. Can you… You may have already said it, and if you did, I apologize, but it won’t hurt to say it again. Can you tell us what the values are with the prescriptive path? And then, what is the performance path?
Jeff: Sure. So the prescriptive path, again, it’s more simple in nature, where it just calls for an SHGC, a fixed glazing of 0.25 and a U factor… which is somewhat different from U value. U factor is the overall thermal conductivity to the glass and the window frame combined, Paul, and the U factor has to be .50, again, for fixed glazing. Those values do change once you get into alpable glazing or entry doors, those values go up or down somewhat. But basically, they all would correlate prescriptively in the use of insulated glass as I pointed out prior.
What I’m seeing more on monumental architectural projects in Florida is the pathway for complying using Whole-Building Energy Modeling, in other words involving an MEP to come in and do an energy study of the building. And what that does, it enables more flexibility in the facade performance numbers that may still correlate over to insulated glass or may not, depending upon the exposure of the glass per elevation and the amount of square footage, what we call window to wall ratio, the amount of vision glass, if you will, to the other cloudy materials on the building facade. So you know, again, in layman’s terms, probably just working, I can say there’s a sort of robbing from Peter to pay Paul within the building.
So you’re able to use… balance the energy-consuming entities in the building, and have maybe less performance in the facade for higher performance elsewhere, or vice versa. Again, the whole intent there, compliance with Whole-Building Energy Modeling is to design more flexibility into the design and allow a greater range of glass to select from.
Paul: Yeah, it makes sense. So what’s going on with… We were talking about the energy codes. Architecturally speaking, what are the current demonstration design trends that you’re seeing in building facades?
Jeff: I would say there’s a couple that are really going around from a national standpoint. I think that the biggest change that we’ve seen in our business, again, thinking as a diverse contract commercial supplier, is bigger glass. And I’ll come back to that trend in Florida in a minute, but just overall, in the US, there is a trend to add more glass to buildings, larger panel sizes, which really goes against the energy requirements, where you’re trying to add more glass, yet you’re saying, “Okay, we’re wanting you to do that, but at the same time we’re placing these very stringent energy performance criteria on that glass that you’re designing.”
So it’s challenging us as fabricators and coaters to design and engineer coatings that can ultimately comply with these higher energy standards, and in the amount of window to wall ratio that’s being required for facades today. So bigger glass for sure. You know, Florida, with the hurricane requirements, unfortunately, we’ve had a limit on glass size here, more so from a design performance standpoint of the overall frame, of about 40 square feet per individual light, and I would say that outside of Florida, we routinely are seeing 50,60, 70 square foot, panel sizes being designed. In other words, for sealing glass, again at points outside of Florida, but back in Florida, with the restrictions of the hurricane requirements and the impact and the cycle testing that’s required, the larger glass sizes have a more difficult time of passing particularly the cycle testing.
So I would say that that larger glass design trend, while it’s…. I see it in Florida as being something that architects want, it’s difficult to give them that because many of the framing companies are not tested greater than 40 square feet or maybe 50 square feet. So the trend is for larger glass, but more companies need to step up and retest their hurricane systems with these larger panels.
Paul: Yeah, we see that same thing in Florida projects. We have, you know, it’s a very vibrant market, particularly in Miami. They’re bringing in architects from all over the world, Europe, New York would be two places that come to mind the most, but other areas as well. And they come in, and they want… just as you’ve said, they want these really large pieces of glass, and we try to do everything we can to work with an architect and give them what they want. You know, they’re the…they’ve got the genius of figuring out, you know, how to put things together and have a really great, iconic project, but sometimes you just have to fall back, and you just can’t do it with wind loads and wind-worn debris and things like that.
Jeff: For sure. And I… You know, working here in Florida with architects over all the years, I sense the frustration at design meetings, particularly from folks that transfer into Florida, that are coming from points where big glass was the norm, or bigger glass was the norm, and now there’s such a limiter here. And it’s not just in glass size but in other configurations as well. So yeah, it’s frustrating, but I will say that the good news is that there’s hope, that there are companies that are out there, some of the big box companies, Conair and Netco, YKK and others, are testing larger sizes. And then, of course, the regional cardinal fabricators here located in Florida are also seeing the same thing. They’re always being challenged to design something bigger and better, and so we’re seeing 50 and 60 square foot sizes, which is a step in the right direction. We can certainly design the glass to meet…and build the glass to meet those sizes. It’s what will pass the cycle pass ultimately that is the limit on glass size for here in Florida. And two, keep in mind that larger glass comes with a cost, Paul. So there’s a cost premium of using larger glass, typically anything over 50 square foot in the marketplace starts to get into place premiums from the various fabricators. So designers need to keep that in mind as well.
Paul: The larger pieces of glass, what’s the risk with regards to seeing visual distortion, perceptible distortion, through the glass? Is it greater than a smaller piece, or… how does that work?
Jeff: You know distortion…really relative to glass size, I would say the aspect ratio of the glass would play more on that than anything else.
Paul: And then tell us what an aspect ratio is.
Jeff: Sure. So the length to width. In other words, if the aspect ratio… Let’s say if a light of glass was six foot by six foot, then the risk for distortion there would be greater. Particularly I’m talking about an insulated [inaudible 00:25:38], than would be a… let’s say a four by nine panel. That’s more rectangular in nature, so it’s got a longer aspect ratio, if you will, again, the width compared to the height. The issue there being, in an insulated unit, Paul, for Florida impact compliance, these are unbalanced insulated units. In other words, the inborn variety is… the hurricane membrane, the laminated membrane, is typically a pane of glass or two panes that are planed together with and bonded with an inner layer, that’s about nine-sixths, 2 inches thick overall. The outboard white is the sacrificial piece of quarter inch heat treated or tempered glass. So you have this large, unbalanced insulated unit where the center light is to the outdoors, and in an insulated unit, that air cavity, the medically sealed air cavity is constantly changing, both in pressure and in temperature. So you have an inward and outward flexing of the glass. And you can imagine the more square and larger a piece of glass is. With that center light outward, it’s actually taking the bulk of that stress in that sealed unit. So you get some concavity or convection outwards where images and reflection are probably distorted.
And we’re saying that particularly on the more reflective, I mentioned earlier, the more radiant building facades. So something to note, architecturally, if you’re designing larger glass sizes, particularly here in Florida, if you have an unbalanced insulated unit, what I would recommend doing to mitigate that risk is to use a thicker piece of outboard white, maybe a five-sixteenths or even a three-eighths. Of course, it’s cost relative, but again, depending upon the size of the unit, I would highly recommend walking through the thicker glass on the outside to balance that unit and try to minimize that pressure differential in the air cavity.
Paul: The reason I brought up distortion was because we see it out too often on projects where, you know, large pieces of glass, as you say, with aspect ratios that promote that, and you’ve got multiple pieces of glass, you’ve got a laminated glass inner layer, you got a high-performance coating, you’ve got an airspace, who know… The framing sometimes can have an effect on that, and you’re seeing it… It’s a shame, we see it a lot more than we should, and it can either be… result in a very expensive problem in replacing a lot of glass, or you can have a lot of very unhappy people. And I recommend, you know, you recommend all the things you can do. I recommend paying a lot of attention to that, because it just… It comes up at the end of the project, also. One of the last things that go in is the glass. Well, maybe not the last thing that goes in, but it goes in relatively late in the project. It’s dirty, you know, it’s not cleaned, it may have a protective film on it. They clean it up, take the film off, ready to open the building, and uh-oh, we have a problem. And it could be a very, very big problem.
Jeff: Well, yeah, honestly, we could spend this entire podcast talking about distortion. And you’re right. And maybe it’s a topic that we’ll come back and visit. I would only say in broader terms that to your point, here in Florida, distortion and glazing is basically an inherent fact of life. It’s just part of the deal. To your point, you’re using a laminated glass unit with multiple glass supplies, bonded with a plastic inner layer of any given thickness, you’ve got heat-treated glass, and you’ve got an insulated cavity that’s moving under the exposure to the sun, different temperatures throughout the day. So there’s so much going on there that if you add an aspect ratio we discussed earlier, that yeah, you really want to pay attention to not only the glass design but certainly the glass fabricator, the coatings that you’re choosing. Obviously, we’ve seen an uptick in visual mockups to demonstrate the quality of the glass prior to ordering. And certainly, in large projects, that’s become more of the norm. You get architectural and owner buy-in of the locks prior to ordering the balance of the glass. And really, it just boils down to having a conversation, as you just pointed out, with the clients. And if you see them going down a path that could be problematic in both sides, or perhaps a particular coating, you know, there’s coating and formative concerns that need to be discussed as well, consult them through that. Talk them through the dos and the don’ts and then ultimately let them vet that out. And quite frankly, some of this just comes about through trial and error and experience. You know, you hope that you don’t repeat the same thing twice. I know, speaking for as at Viracon, we stringently monitor all aspects of the fabrication process to ensure that we get as flat a glass as possible on the building, but inevitably, heat treated glass is going to have a little air to it. And then you put a reflective coating on it, you insulate it, you laminate it, and then you put another building adjacent to it, then you’re reflecting off that skin, and distortion can happen, and in fact will happen. But deal with reliable people, and hopefully, they can walk you through the concerns. You look at the mockup, get that through, and I guess in hindsight, the best I can say is the process. Just make sure you’re dealing with quality people.
Paul: Yeah, because the ASTM specifications that cover flat glass and heat treated glass and what not, one of the things they say upfront is that all glass has some degree of distortion. People probably don’t realize that, but it’s just… So it’s the degree of distortion, and whether it’s perceptible or not. You certainly don’t want to be looking out through a light of glass and have it look like you’re at the front house at the carnival. So it’s a big deal, and we’re seeing it, as I say, more than we’d like to.
One last line of questions, and I think you’re ready to… getting to the end of our time limit, we’re all far and high right now. You know, we’re… GCI consultants is very busy, I know Viracon’s very busy, I know the glass industry is very busy with longer lead times, opening factories, things like that. What do you see and what does Viracon see with the current business climate, and what’s coming down the road?
Jeff: You know, eventually, you’re right. At least here in North America, we’ve been blessed with a very active commercial building market, and look to continue that, for the several years to come. In our forecasting, we see a positive trend upward to 2020 in our core market here domestically. But you know, it’s an interesting question, because frankly, the run-up that we’re in now, if you recall, sort of caught the market here off guard, a couple of years ago, coming out of the downturn that we experienced in ’09, ’10 and ’11. We wrapped up a lot quicker in the marketplace than most folks perceived, ourselves included. And so a couple of years ago, you know, folks were dialing down capacity because the demand, obviously, was quite low at that time. And then we had to rapidly dial it back up as demand increased. And so it took about a year, a year and a half, speaking more internally of Viracon, to get capacity in line with the demand. And we’re in a good place today, with respect to again our core market. I think the industry in general capacities today are meeting the demands, again relative to the specific businesses of these fabricators. We have a longer-term perspective at Viracon because we’re dealing with bigger buildings, bigger projects that have more scheduling awareness, and so we have the ability of predicting the backlog a little bit better than someone, for instance, building a 711 down street around the corner that may need glass in a week or two. But I think balance. If you’re a developer or a builder, whether you’re dealing with a big, major fabricator like Viracon or a regional, local guy, I think there’s glass available for you in the marketplace in the timeframe that you now need it. I couldn’t say that a year and a half ago. Again, in the run-up, there was definitely a capacity constraint.
But as I said, we’re in a much better place now. I see that continuing as I mentioned earlier for the next two or three years. Here in Florida, I think we near the balance of the country, that the run-up for us has been more on the residential side, particularly in the high rise side. That has started to slow down, somewhat, and I think that will be augmented now with the commercial and retail that we’ll build in behind it. So the market itself in Florida may change relative to the sector of the construction projects, but I think overall, it will still be brisk for us going forward.
Paul: Yeah, you know, we’re seeing similar in our business in Florida, and also Southeast and in other areas, Caribbean, and even in other parts of the country, where condos, while they’re not going away, seem to be slowing down a little bit. We’re seeing a lot of multi-families still, and we’re starting to see office buildings, now, as well. We’ve got a couple of lead platinum office buildings that we’re working on now that are more recent additions to our portfolio. And we’re busy, and stuff is still coming in pretty rapidly, but as we all know, it’s cyclical, and at some point, you know… We keep looking, having been in this business for so long now, when is it going to slow down? Haven’t seen that yet, but we know it’s coming at some point.
Jeff: Yeah, I would agree. I know at some point down the road, we’ll all probably plateau out and see maybe just a flat line. I certainly don’t expect the downturn that we experienced prior, God willing, but, you know, probably the one thing that I could say from the center shop and wrap up from a contracting standpoint relative to the market demand today, particularly on the large projects, buy the glass out quickly. You know, years ago there was a trend to wait, and buy it late, and I would say that that would have gotten you in trouble. It certainly would have got you in big trouble a year and a half ago. So make sure that as a contractor, you do your due diligence to get that glass package bought out quickly, get the aluminum and the glass booked and forecasted at the respective manufacturing companies, and put it to bed, and then move on to the other trades in the company. And, you know, that’s probably another trend in SC growing is a more rapid buyout of the glass package, knowing that there could be another spike in demand, perhaps, a capacity issue down the road, but not only does it lock in your capacity for your job and allow you to meet your schedule, but it also locks in pricing. So obviously costs and schedule, you know, are all important to a contractor, you know, just try to get on that as quickly as possible and get that bought out.
Paul: Good stuff. Well, Jeff, thank you very much for coming onboard today. It was really interesting and fascinating. I know our listeners are very interested, and the energy and the explanations are good. You know, sometimes it seems like voodoo to some of us. Thank you for making it understandable, and I’m hoping that maybe we can do this again. I love the idea about talking more about distortion, and also thinking about glass damage, stretched glass, things like that, that would be something everybody really needs to focus on. So thanks so much for being with us today. We really appreciate it, and it was good stuff.
Jeff: Thanks for having me, Paul. Happy to be here, and for sure, I look forward to continuing other topics down the road.
Paul: Well, this concludes this episode of Everything Building Envelope Podcast. Hope you found it interesting and thought-provoking. Please subscribe to the Everything Building Envelope podcast at iTunes or Stitcher, or visit www.everythingbuildingenvelope.com, where you’ll find show notes, previous episodes, and bonus content videos. As an added bonus for visiting www.everythingbuildingenvelope.com, we’ve added a free white paper that’s germane what we talked about today. It’s called “What You Need to Know about Energy Codes and Recent Trends for Glazing Systems.” Energy code requirements are evolving, and it’s very important to keep up with these new developments. Thank you, everyone, for listening. Please tell your friends and colleagues about Everything Building Envelope podcast. This is Paul Beers, saying “So long, until next time.”