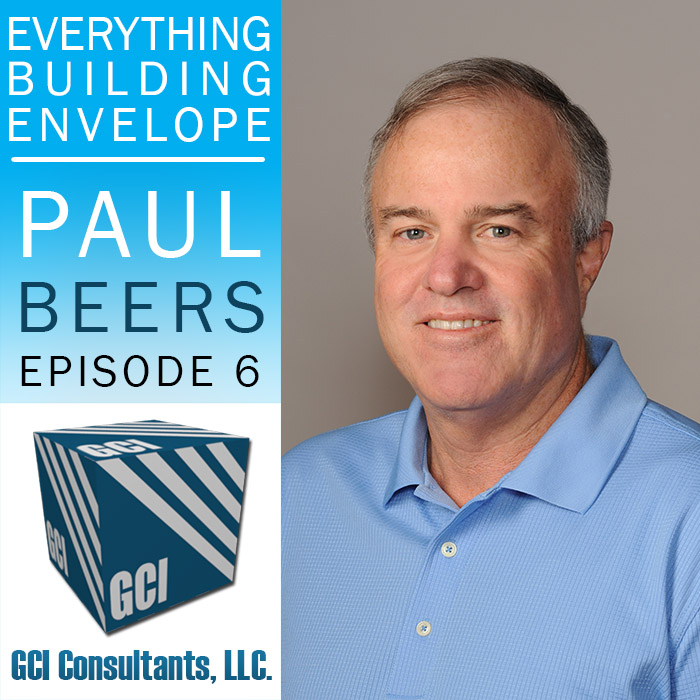
About The Everything Building Envelope Podcast: Everything Building Envelope℠ is a dedicated podcast and video forum for understanding the building envelope. Our podcast series discusses current trends and issues that contractors, developers and building owners have to deal with related to pre and post construction. Our series touches on various topics related to water infiltration, litigation and construction methods related to the building envelope.
https://www.everythingbuildingenvelope.com
*** Subscribe to the show and leave us a Review on ITunes!
Hello everyone. Welcome to Everything Building Envelope. I’m your host, Paul Beers. Everything Building Envelope podcast features topics of interest related to exterior building envelope including waterproofing, glazing, cladding and roofing. Please visit our web site www.everythingbuildingenvelope.com, where you’ll find access to each episode, along with show notes and a special video section the same as content. Please subscribe to the Everything Building Envelope podcast on iTunes and Android outlets such as Stitcher.
Today’s topic revolves around vulnerable areas within the building envelope. What I would call building envelope hotspots. In other words, what at the biggest areas of concern. We’ve been in the consulting business for quite a long time and, you know, we always think we’ve seen it all but we have not, and trends to emerge, things that really top out as being areas that need special attention, so let’s look at some of them.
Let’s start with digging holes in the ground below grade waterproofing. This has been one of the really hot spots in our consulting business, great interest here. People are very concerned about it, and the reason is, if you think about it, when you apply below grade waterproofing you dug a hole in the ground. You put the material in to keep the water out. It may be a basement. It may be below grade parking, elevator pit, things like that, and once you then pour the concrete and cover it up you can’t get back down there to fix it, so it needs to be done really well really correctly the first time. You need to select a quality system. You need to have warranties in place. You need to have oversight. You need to have involvement from the manufacturer. It’s really important if things go wrong, it’s a very difficult fix. It’s taking a shot in the dark. You’re drilling holes injecting epoxy things like that. For the below grade waterproofing is a big concern is something that really needs a lot of attention and rightly so a big part of our focus on projects when you do have anything that’s basically below the grade or underground.
The next area that we see on a lot of buildings, not just in Florida but all over, are what we call amenity deck. An amenity deck is a common area on a building. It may be a plaza. It may be a recreational area. It may even be a park, and there’s space underneath that’s either occupied by the building, parking garage something like that. A lot of hotels, condominiums, apartment buildings even office buildings have amenity decks where you might have swimming pools, tennis courts, green areas, pedestrian areas, plazas whatever, and again, not unlike below grade waterproofing, as you are building it you apply the waterproofing systems, and if there are problems it’s a very expensive fix. You’re digging up or tearing up finished area be it planted or be it tennis court, and chasing around trying to figure out what the fix is, so we really like to pay attention to amenity decks as well. Usually, it’s a waterproofing system that beneath it. We look for having proper slope to drain to get the water out. We look for using it with the proper system that will basically be able to stand the test of time. We look for, again, warranties, manufacture ****. I didn’t say this about the waterproofing, but having the whole team involved. It’s good to have a pre-construction meeting before with the subcontractor, the superintendent, the owner, the architect all involved manufacturers to go over everything, so that everybody really knows what supposed to happen, how it’s supposed to be done, what all the project requirements are, how to make and ensure quality control, when to have inspections to ensure that everything looks good and get a good outcome. Another thing that related to an amenity decks are planters. Planters are, I had a contractor tell me one time, planters are one of the lowest costs scope items in a large project but one of the biggest costs when you have to go back and fix them. So, planters, a lot of thought needs to be put into them, what proofing materials can be used. You can use a fluid applied or a sheet applied. The sheet applied can have problems sometimes with roots and things like that getting into it, so you want something that, you know, because obviously you have planters and have things growing in it, and you want to have a material that will be able to withstand any invasive roots and things like that. Again, you’ve got to have drainage. You got to use the right materials. It seems simple, but it’s more complex than it seems.
Another area that’s related to this are rooftop pedestrian areas. We’ve seen a lot of problems here on projects where it’s kind of a natural architect’s and building owners or building users should I say, really like these rooftop areas. If you think about it, it’s a great opportunity to have a sundeck swimming pool. You see a lot of swimming pools on roofs these days, and obviously what’s underneath the roof occupied space and probably not just occupied space, probably the most expensive space in the building. If it’s a apartment or condominium, it’s typically a penthouse apartment. If it’s an office building it’s typically a premier suite in the building, so you don’t want water down in there. It will be very expensive to fix. You have finishes not to mention angry people that live there who probably have lawyers, so these areas take a tremendous amount of scrutiny to make sure that everything gets done correctly. In a rooftop pedestrian area, usually it’s a waterproofing system that applied, although, the roofing manufacturers have these types of systems also. There is a crossover there, but you need to be really, really careful, again, with specifying materials, getting the manufacturers involved, getting a good installer, having the proper warranties in place. We like to test these areas before they’re completed doing a flood test, where we’ll plug the drain and then flood the area with water, leave it overnight, come back the next day and make sure all the water is still there and hasn’t leaked anywhere. If you have a leak, you want to find it during construction not afterwards. Another area that we’re seeing more on buildings these days are water features. In fact, we have a building we’re working on in Miami right now has a 75-foot waterfall in design, and it’s another waterproofing issue. I remember working on a restaurant a few years back in Miami. It was very trendy, and it had a lot of water features, and they leaked, and it was a disaster. It was causing all kinds of problems in the space with mold, and rot and odors, and it was an extremely expensive fix. Basically, shut the restaurant down, drain the water system and redo everything and do it right. It was obviously not done correctly. Anywhere, you’ve got water or the potential for water to come into the building like that, then you need to really, really pay attention to it.
Many building nowadays have balconies. People like the outdoors, even on high-rise buildings. Balconies are always an area where you have to be careful and **** seen a lot of problems with things are not done correctly, so balconies interfaces with the exterior wall of the building. Of course, it’s got some sort of sliding glass door or swinging door on it. We prefer sliding glass doors because they perform better, and they don’t have as much problems with the wind. Balconies can get in some very extreme conditions as far as window loading goes if they’re near the corner of the building, and if it’s not occupied space, but if is occupied space you should have tile or marble finishes that you put on it, and so many things need to be considered.
Let’s start with the sliding glass door or swing door. You’ve got to really think about how you detail that because a lot of buildings, particularly condominiums you’ll put the window in and then have a buyer come in 2 years later and put down marble which could be very thick, several inches in thickness, and if the marble is higher than the sliding glass door track, for example, then the water can be trapped in the sliding glass door track and that obviously is a big problem. It can’t get out. It’s going to come in, so you’ve got to detail the sliding glass door or swing door track up in the air enough to anticipate what a future owner will do. So, typically that involves put it on some sort of curve, and then the question comes, have you waterproofed that. We’ve had a lot of curved leaks that we’ve seen over the years. You basically have to have a waterproofing system that extends over the entire balcony surface up over any window or door curve or sills and also of the exterior walls. So, there’s a sequencing issue here as well, where every thing’s got to be done. If you put the window in first before you waterproof, obviously you’re not going to have the opportunity to waterproof the curve underneath the window which is very important. And, speaking of waterproofing on the balcony decks that’s another question we get sometimes. Why do we have to waterproof it? Well, waterproofing is good practice because what’s inside the slab typically is your concrete slab what’s inside the slab seal and as water gets through the concrete to the steel it can cause the rebar to rot and expand, and that causes the concrete to crack or even blow out, and that’s a very, very expensive fix, and this can happen quickly or it can happen 20 years later. You want to do everything you can to prolong the life of the balcony. Builders use galvanized rebar. They use sealers. They use waterproofing systems. You can’t really go too far here to try and do things in a way that will decrease the opportunity to have this problem happen. You’ve got railing penetrations on balconies, and the something very, very important seems like a no-brainer but it’s not is the slope. The balconies have to slope to get the water off or have drains in them if they’re really large. If they’re really large, then they have to slope into a drain, but ponding water is a big no-no, and if it occurs a lot a lot of these buildings have post-tension slabs, and they’ve got everything sloped looking good, and then they tighten the cables on the structural system inside the slab and that outer edge of the balcony curls up and then all of sudden you don’t have the property drainage. So, all that’s got to be contemplated and considered in the structural design and in the waterproofing design to have a successful balcony.
Another big hot spot are stucco systems. Many buildings, let’s say probably 75 percent of the buildings that we see are maybe even more have stucco as the exterior cladding, and it’s pretty complicated to get it right. It seems simple just slap the stuff on the wall and everything will be good, but it’s not. You have different structural frames that you have to consider. In South Florida, you have masonry, and lot of the other areas of the country we have studs and sheathing, and what’s really important with both of these systems is to get a good waterproof membrane underneath the stucco. Stucco cracks. Stucco is porous. Stucco is not waterproof.
We found that out back in the day of the heyday of EIFS exterior installation and finish systems, that were barrier systems basically, they were just adhesively applied and the whole system was supposed to keep water out of the building a hundred percent of the water, no provisions for drainage, and of course there were a lot of problems. Now, EIFS, I’m not badmouthing EIFS because EIFS has its place. It’s a high-performance finish with installation on the outside of the walls. It’s very highly regarded in some circumstances, and what I am badmouthing are barrier systems, not just EIFS but any barrier system with stucco-type systems are prone to problems. So, we want to have water drainage behind the system with either a fluid applied or sheet applied membrane. We even want to have that on masonry. Now, masonry a lot of our clients put the waterproofing around window and door openings and not on the bulk of the wall. While we’d like to see on the bulk of the wall, it’s very expensive, and we get it. There’s budgets that need to be met, so a lot of times it’s not done on the entire exterior wall, and with masonry that’s okay because if masonry gets a little bit wet there’s no harm done. It will dry out. We do recommend testing these system, field testing them, do a mock up early in the project to make sure everything is good. You’ll find out right then and there. You know, we’ve done jobs where the owner didn’t want to put waterproofing around the window and door openings. So, we said okay, let’s test it with and without, and the without leaked and the with didn’t. So, obviously it made a lot of sense to do it, and of course the owner didn’t want any water in the building, do had to pay a little extra money and do that.
The other thing with stucco systems are the areas where the stucco is adjacent to other materials, junctures, penetrations, control joints things like that. So, a juncture would be where stucco meets a window or a door or where stucco meets say a different type of cladding system. A lot of thought needs to be put into that how it’s detailed, how it’s sealed, so that it stands the test of time until water doesn’t get in. Penetrations if you think about it, you look at a building there are many. There are hose bibs, there are drying vents. People put signs on buildings, satellite dishes, electrical light fixtures. All those areas are opportunities for water to get in even around a well-designed stucco system. If you don’t contemplate and detail every one of those penetrations that’s where the water could come in. Then, the other area that we’ve seen problems with a lot in the past are controlled joints. Now, control joints are a necessary evil in stucco, and sometimes an architectural feature that can give the building a certain look maybe of different textures, of different colors or you just want to break up the monolithic surface. Very, very carefully consideration needs to be put into control joints because they’re basically kind of a penetration in the stucco, but definitely a break in the plane and an opportunity for water to get in, so you’ve got to have your waterproofing system behind it that will compensate for any water coming in, and you also need to really consider where the control joints are. You don’t want them terminating in say a window opening where they could just channel water right behind the window, and they’ve got to be properly sealed. Manufacturers control joints do have instruction on sealing them, and that needs to be done. If not, then you’re probably going to have a problem.
Glazing systems, I’m not going to go into that today, but glazing systems obviously you need to select the proper window, door, fixed glass, curtain wall. It needs to have the proper performance criteria. It needs to be properly installed and very important, when you have any building, and I would say any size building may that’s a little bit extreme, but steel water infiltration testing is very, very helpful during construction to see if the window, door, fixed glass curtain wall are performing as intended. A lot of times these systems are tested in a laboratory as vanadium systems not installed into a particular wall system, and that’s where the rubber meets the road. What you want to do, you want to test as early as possible in the project. Do an in-place mock up, test it. Many, many times we do this we’ll find a leak somewhere. If it’s early in the project we can make an adjustment to the installation or the design of the wall system and have it interfacing with the window, or maybe the window has some problem coming out of the factor. Let’s find out about it. Let’s get it fixed while everybody is still on the job before people have moved into the building, and we have a much better outcome than not doing that. You don’t want to find out later. You don’t want to find out when the building has been built, people have moved in and all of a sudden you’ve got leaks. That’s a disaster, typically.
Roofs are an obvious area of concern. We like to keep the as simple as possible. The less penetration the better, proper drainage, proper slope to drain, how they interact or intersect with parapet walls, curtain walls whatever interfaces with them. We want to use a good system with a good warranty be it built up, single fly, ETDM whatever you want to get make sure you have a good roofer, and a good manufacturer, and you want to follow all the rules or all the conditions to get the warranty, and that’s not just during insulation that’s after the roof is installed. We get involved in projects all the time that have a 20-year warranty and one of the conditions of the warranty would be an annual inspection by the manufacturer. If that’s not done, then it’s a big problem trying to get a warranty claim where you haven’t done your part of the bargain, and the roof manufacturers will almost always deny a claim because they want to inspect it every year, and if there’s a problem then they can identify and fix it, if it’s a small problem before it becomes a big problem.
Sealants, when everybody thinks of sealants they think of windows, but sealants are used in many areas throughout the project, control joints, expansion joints anywhere you have change in ****, junctures, penetrations all things we talked about before. Again, this is being simple but just putting the goop in there isn’t necessarily going to solve the problem or prevent the problem. Sealants are very complex. There’s a lot of different types. They have different elasticity, different properties as far as how they perform in UV with the sun hitting them. The sealant design is really important where you have to have a two-side adhesion you have to use bond breaker tape or backer rod, and by the way backer rod does not have anything to do with waterproofing. It has to do with the proper profile of the sealant joint so it can expand and contract, and the sealant joints typically need to be thinner than they are wide, so they can move in and out, kind of like pulling on a elastic band, and then using the proper materials silicone versus urethane. They all have their uses. We like to see silicon where it’s hits the sun. Urethane has the potential to break down over time when exposed to sunlight, but urethane may be a great sealant in a concealed condition where you want really good adhesion and strength.
Coating, you know we talked about stucco, and stucco typically needs to be painted at the end of the project. Everybody loves to want to gravitate to elastomeric coating which is kind of a waterproof coating. Not necessarily a good choice on a building that was just stucco’d recently or newly constructed building because the stucco still has moisture in it. You don’t want to trap the moisture. You would use an acrylic paint typically of that or if you did use an elastomeric paint you want to have a lot of porosity to allow moisture in and out. Now, 10 years later when this building needs to be repainted yes, elastomeric is probably a good idea. It’s dried out at this point, and there’s cracks and things like that that need to be overcome, so the thought needs to be put into what’s going to be used, and there’s different products for different scenarios and also different life cycles of the building.
Last, I have on my list here is pretty interesting because we see this all the time, and I’ve got it. I’m calling it glass quality, so there’s two things that I think of with glass quality, and this can be big money. You can be so, so careful with it. One, is having the glass get damaged while it’s being installed in the building. Scratches would be the primary thing. You get stucco on it, drywall, mud, people bang into it with tools whatever. When glass gets scratched, they buff it out. Typically, when glass gets scratched it needs to be replaced especially if it’s got a lot of scratches on it, very, very expensive. The unit owners come into their million dollar condominium they’re not going to put up with having a big scratch going through the painted glass, and there are industry standards to evaluate scratches which can be helpful, but ultimately if the unit owner is sitting at their breakfast table, and they’re looking out at the ocean, and there’s a scratch say at the bottom corner of the window right in their field of vision, they’re not going to put up with that, and it’s a big fight, and it’s a fight you don’t want to have, so protecting the glass during construction with film, with good practices, good housekeeping everything you can do to keep that from happening is really, really important.
The other thing that we’re seeing more and more of these days is the distortion. In fact, I recently replaced the windows in my house in Florida, and the glass came out distorted. It was laminated glass. It’s no good. It looked like you’re looking at the fun house when you looked through the glass. Industry standards really do not address the distortion in a way that meshes with the consumer expectations. All glass has some degree of distortion in it, so it’s basically what you can see when you’re looking through it, but very, very important I highly recommend inspecting all the glass. Well, first of all set the expectations upfront with the supplier. Get some samples, do some mock ups then have something as a baseline to compare all the rest of the glass on the project to, and inspect it when it comes out. Don’t put it in the building if it’s distorted. Have it replaced immediately. Fixed fight waiting to happen if you’re not really careful with this.
So, those are my hot spot, and what do we do about it. I have talked about this along the way. Obviously, paying a lot of attention to the design and making sure everything is well detailed. We come in a lot of times working on projects where we assist the line team, or the owner or do a peer review to see if everything has been addressed and has been addressed up to the industry standard of care. A great idea to get manufacturers themselves involved during the design. Get their input. They work with this stuff every day, and they know how things need to be. Also, manufacturers also have a lot of requirements that need to be met, and they can advise on what should and shouldn’t be done. Warranty requirements, again, if you don’t get it right up front and you don’t follow all the rules, so to speak, of what needs to be done of the warranty and that includes proper us of materials, proper detailing, installation, probably some inspections and documentation that things were done right during the installation, and as I said before post-installation requirements **** roofs if you don’t have the manufacturers inspection annually you’re probably going to lose your warranty. As you go through the construction process there’s submittals. Always require full submittals like windows and doors are a great example, shop drawings. All major projects you do shop drawings for windows and doors. When you get into some of the smaller stuff, you know, wood frames, multi-family, hotels things like that and submittals aren’t done that’s just looking for trouble. If you want to make it work on paper first, then you want everybody in the field to understand how it works and give you a much better chance of success. Pre-installation meetings, we love to do those. We do them typically for waterproofing, glazing, cladding and roofing. Get everybody together, go over the plans and specifications, review the submittals, have the installers out there, go out in the field, look at the field conditions, discuss any issues, answer any questions, get everybody on the same page gives you a much better chance of success.
Quality control inspections during the work, a great idea to go check and make sure things are getting done right. If you catch a problem during construction it can be fixed. If it’s missed then afterwards problems develop, you’re tearing out finishes. You have angry occupants of the building. It’s typically a lot of drama a lot of problems so why not catch it during construction.
I talked about field testing. We like to do it on windows, doors and the surrounding wall areas. We like to do flood tests with waterproofing. There is steel and adhesion tests that can be done. There’s a whole mired of tests that can be done to make sure that everything so copasetic and that if there are problems, again let’s find it during construction. So, I think the big thing is as construction is going on and you’re doing your inspections and you’re doing tests, if you do have issues make sure they get followed through on and make sure they get fixed. Sometimes where we work on projects we do inspection we send our reports, and we wonder if anybody is even reading them, and it’s great to do all that, but if the problem ultimately doesn’t get fixed then what good is it.
So, I hope you enjoyed this episode of Everything Building Envelope and found it interesting and thought provoking. I really appreciate, by the way, the comments people have been sending me after these episodes and encourage you to please if you have any ideas, thoughts, comments whatever bring it on. I’d love to hear it. Please subscribe to the Everything Building Envelope podcast at iTunes or any Android outlet such as Fixture or visit everythingbuildingenvelop.com. You’ll find show notes, previous episodes and voluminous content videos. An added bonus for visiting everythingbuildingenvelop.com web site, we’ve added a free Whitepaper for Building Envelope hot spots, so I’m going to put this into a little essay and kind of a checklist, but if you would like a copy of that please visit www.everythingbuildingenvelope.com. Thank you for listening. Please tell your friends and colleagues about Everything Building Envelope podcast. This is Paul Beers saying so long until next time.