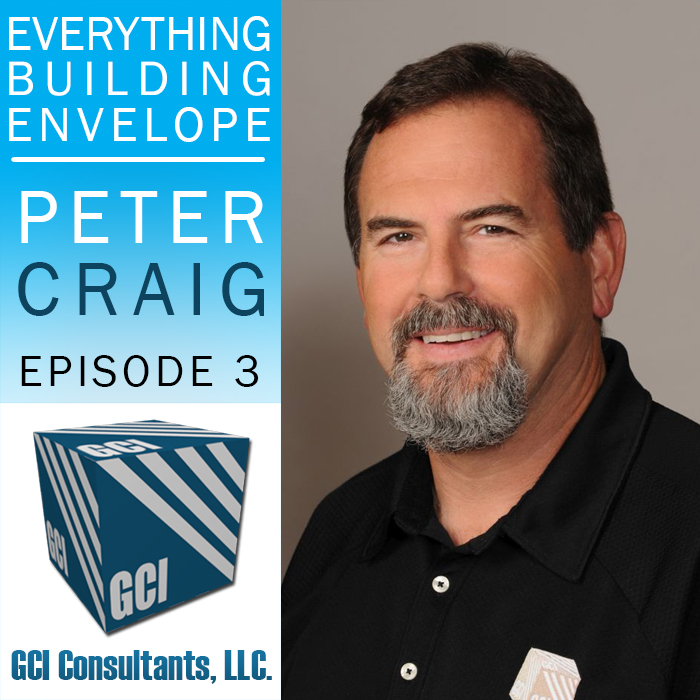
About The Everything Building Envelope Podcast: Everything Building Envelope℠ is a dedicated podcast and video forum for understanding the building envelope. Our podcast series discusses current trends and issues that contractors, developers and building owners have to deal with related to pre and post construction. Our series touches on various topics related to water infiltration, litigation and construction methods related to the building envelope.
Paul: So, welcome back everybody to the Everything Building Envelope. Paul Beers here and we have a really interesting topic today, we’re gonna talk about trends in waterproofing. Waterproofing has probably been one of our bigger hot buttons at GCI. There’s a lot of demand for services because, you know, there’s a lot of exposure. If things start leaking obviously that causes problems.
I’m very excited to have my coworker and colleague, Peter Craig, here as our guest today. Peter and I have worked together for a really long time. Peter, I was thinking, we first met it was in the 1990s I think at a ASTM symposium in Detroit.
Peter: Dearborn, Michigan.
Paul: Yeah. So, we first met there and Peter came to work with us… How long have we been working together now?
Peter: Eighteen years and one month.
Paul: Yeah. So when we first met we didn’t have gray hair, right?
Peter: No, we did not.
Paul: So Peter’s expertise is waterproofing and I think probably many of the listeners know Peter and have worked with him over the years. But for those who don’t, Peter why don’t you just give us a little overview of what it is that your expertise is and your background and whatnot.
Peter: My background is I spent 30 years working in waterproofing. I spent the time prior to the 18 years I’ve been with GCI working for contractors, I did the work as a regional sales managers for them so I was very exposed to the aftermath of what happened if waterproofing wasn’t done correctly, and then for the last 18 years with GCI I’ve been responsible for the waterproofing of building envelope exteriors to try and alleviate any leaks and problems from the outset.
Paul: So Peter, you know, we’ve worked on a lot of significant projects and seen some challenging ones. You know, we do things like have projects, coastal areas that have basements in them below the water tables and of course we work in extreme environments and, you know, U.S. and Caribbean. It seems like architects are doing more and more, you know, getting more daring I guess in trying to maximize the projects and get more uses out of them.
Peter: Yes, you’re all finding that. You know, the basement area becomes an important part of helping maintain a high-rise structure because that’s where a lot of your load bearing and your structural support goes and rather than simply having a dead space, yes, they’re utilizing them for parking garages, basement storage, that type of stuff that’s below grade.
Paul: So, you know, the below grade is I’d say I just remember back and I’d like to hear what you think about it but, you know, it didn’t seem like there was that much emphasis on it when we first started working together. And now, that’s kind of the driver and a lot of times in why we get involved with projects.
Peter: Yeah, it’s… What’s happening below the building becomes critical because obviously, one can’t lift the building up afterwards to get to those areas. You’re also, as you mentioned earlier, in a lot of coastal environments so high water table environments that need to go down into the ground to support the building leads to the fact that you’re now within the water table and add sort of different situations to the construction, both dewatering the hole that you’re trying to put your building into and then also managing the water once the building is constructed.
Paul: How are folks doing this?
Peter: The traditional ones have always been the waterproofing systems that can be pre-applied into the foams because they limit the size of the hole that needs to be created because one only needs to be able to slide a foam down. And so typically your bentonite waterproofing products and then Grace’s sheet products tend to be the most popular and the most widely used. The trend though that we’re seeing a little bit is to try and reduce the amount of material that needs to be used below grade and that is to do with the giant foundation mat and the elevated pits.
Paul: Is that something that’s becoming more common or… And generally why are they doing that? Is it easier? Is it better? Is it cheaper? All of the above?
Peter: It’s kind of all of the above. Obviously, the hot button is for everybody associated with building a building. Architect remains sort of inert because he’s in a design situation, he’s looking for waterproofing. But both the general contractor and the developer or owner are usually looking for savings both in terms of time and money and the idea is to reduce the amount of waterproofing that’s down below grade.
The easiest way of describing it is that the foundation mat usually is a large box that has to be pushed into the ground and that’s constructed out of concrete, usually it has some imprints in it which are the elevated pits. But that whole box then needs to be waterproofed very often because it’s sitting within the water table. The theory now is to try and separate the bottom of the building which should be the slab on grade from that foundation mat by putting a layer of dirt between the top of the mat and the underside of the slab and what it effectively does is it separates the foundation mat away from the rest of the building and therefore your waterproofing no longer has to encompass the foundation mat, it can run over the top of it beneath the slab. And that reduces a significant amount of material in the sense that you don’t have to waterproof the mat and those vertical surfaces. It reduces the time because you’re not involved with trying to waterproof those, dewatering to allow them to waterproof, or even the size of the hole that needs to be built.
Paul: So that helps the schedule too?
Peter: It does help the schedule and it recognizes pretty significant savings. We’ve seen savings anywhere from $60,000 to $100,000 depending on the size of the building and the size of that mat by readjusting the structural engineering side of it to allow for the mat to be a little further down.
Paul: So before the foundation and the slab are all interconnected or the slab is right on top of the foundation?
Peter: Essentially that was it. They were connected to each other, the steel link the two and the slab sat directly on top of the foundation mat. There was some trend and there has been done…some work done on some smaller projects where they’ve used a different waterproofing component to go over the top of those pile caps and basically act as a bond breaker between the foundation mat at the pile cap on the bottom of the slab but usually that has to be pre-approved with a structural engineer. Some of them like concrete to touch concrete, others can live with the fact that the steel will hold the two pieces of concrete together.
Paul: Good. You know, below grade obviously is a starting point when we provide services on a project that’s typically our…not typically, always the first thing that we do, they dig a hole in the ground and that’s when we get started. So once we start coming out of the ground, what do we get into at that point that have, you know, the waterproofing priorities?
Peter: Well I think the biggest issue you’re seeing that follows on that as far as design changes is that horizontal surfaces and terrace decks are not simply being used as decks. Obviously, there’s an emphasis on greening, chasing lead points but also at the same time it’s sort of in an urban environment trying to create greenscapes so one tends to find that terrace decks, and plaza decks have swimming pools, planters, spas, shuffleboard courts, any number of aspects to make them a large amenities deck but at the same time there’s still a roof system below and as a result we need to be very focused on our waterproofing in that area. Again, because the accessibility afterward is very difficult to get to simply because of the overburden and the types of materials and plants that are put on the deck.
Paul: And, you know, so a lot of times with these amenity decks we have occupied spaces below them such as…well, it could be dwelling units, it could be common areas. I know we did a job a few years back that had a…in a hotel that had the ballroom underneath the swimming pool. How did everybody feel about that?
Peter: It’s always an uncomfortable one, yeah. But like I said, architects tend to think creatively and then leave it up to everyone else to figure out how to be able to create that dream. And certainly, you can. The choice of materials that you use in those areas play a big part in it. Obviously one can go with conventional roofing systems but they do have their limitations, the placement of the insulation. Whether it’s on the inside in the ceiling area or on the outside on the roof area plays a part with it. Traditionally it had been for the last 10 years it was called fluid applied waterproofing that was used on the decks. In the field of waterproofing, it typically is good, better and best when one looks at options that are available for you. Obviously there are economic costs with it, they may also be time-saving costs with different products. There’s also warranty coverage that impacts things. But for the last 10 years, hot fluid applied waterproofing had not been part of the equation, they had…
Paul: Let me just interrupt for half a second. Why is that? Because that, you know, that was always pretty traditional. Why did they go away from that?
Peter: The reason that they moved away from it was basically fire code requirements. You’re using a product that is 400 degrees Fahrenheit, so there’s a safety factor with that but there was also then an open flame associated with the kettles that we used to melt the hot rubberized asphalt that was used with it. There was always a concern with the materials and moving the kettle higher up in the building, that there was a fire risk, and so simply up until the second floor above grade was only areas that they were allowed to be used. That has since subsequently changed.
Paul: So they went away from that and then to the cold applied and how did that work out?
Peter: Cold applied has been a learning curve for everybody. When it was first introduced in the market it was considered sort of the latest greatest product. It was innovative in the sense that it didn’t use as much material, it was green concrete orientated so it could be put on off to 7 days instead of 21. It was also… So there were economics and time savings which everybody really appreciated and jumped all over as part of the features that they look for. What we’ve discovered though in the last five years is that these products, typically the poly extruded urethanes and the cold fluid applied systems do not handle standing water very well, they do not handle high alkalinity within the water, and they do not handle water that heats up to extreme temperatures. All three things do occur very regularly on a terrace deck where water can be trapped below the surface that people are unaware of. And what we’ve learned from cold fluid applied is that the benefits and features that they gave us at the outset did not present themselves over the long term. Decks that have been down for 5 to 10 years have been discovered to have re-emulsified which means basically the water sitting on them has been reabsorbed by the material itself and then rearranged its chemical composition as those H20 molecules rejoined the product.
Paul: So basically the product has broken down or has failed at that point?
Peter: That’s correct. And needs to be replaced and obviously, at that point, it requires taking everything off the top of the terrace deck and then re-waterproofing it which can have a significant impact both in terms of cost and convenience to those that are in the hotel or the high-rise condominium or dwelling.
Paul: You know, it’s funny you say that because I remember one of our customers years ago who we did a lot of work with as a general contractor. And he would hire us to do quality control work and take it out of his pocket, basically spending his, you know, money that he had in the project. And he always said that, you know, he’d rather spend the warranty dollars up front than at the end of the project. And the other thing that he said that was really interesting was he was talking about decks and planners and he says, “Very small impact on the cost of the project scope going in.” So it’s a very low-cost item when you compare it to everything else. But the repair costs are enormous when you’re having to remove, dig dirt up, remove materials, all those sorts of things.
Peter: He’s actually…he’s spot on. And the other thing that you discovered now obviously as we hinted earlier, the cold fluid applied systems are very sensitive to the substrate requirements. So they need to have a pitch of a minimum of an eighth of an inch going to the drains. In order to be effective, they need to be able to drain water and not have water stand on them for long periods of time. And that’s seen a change within the industry itself.
The hot fluid applied that we referred to earlier that had been outlawed because it had an open flame has come back into the equation, they recalibrated and redesigned the system so that they use melters now, there is no open flame that are gas-powered, or they’re gas, in terms of air gas and in terms of petroleum are used to run both of those pieces of equipment so they can move up to the top and they’re now being reintroduced because they are more forgiving as a waterproofing system. They allow for standing water, they can handle ponding water, they can handle water with alkalinity in it, they can handle the extreme temperatures. One gets a 20-year warranty and often can get the fact that there is no slope written into the warranty unrecognized or that there is a standing water being recognized and also incorporated into the warranty.
Paul: So, you know, we were talking about standing water, ponding water. You know, when you have an amenity deck it could be, you know, acres in size. We’ve seen them with tennis courts and landscaping and swimming pools. I mean, they can be very large, for instance, over a parking garage. And why is it so important to be able to, you know, not have the slope to drain requirement?
Peter: Well, the key aspect that you have obviously is most structural decks oppose tension which means that the deck itself is usually being poured in a monolithic manner. If you’re required to slope an eighth of an inch per linear foot you would have to pull the deck in multiple sections in order to be able to get the pitches that you need from the high points down to the low points where the drains are located and what you’ll typically find at that particular stage is that the concrete contractor will tell you that it will drive his costs through the roof to change the pouring cycle or alternatively to change his slumps so that they can then rework the concrete to get these slopes and pitches at the structural level. It’s much easier for them to reintroduce those at the lightweight concrete stage which is done later.
One of the aspects that you talked about though, too, that we’re seeing is a change with that because of the size of the decks and what’s on them, traditionally a manufacturer requires a flood test. So once the waterproofing is put down, two inches of water is placed over the top of it left for 24 or 48 hours, come back, have a look at the bottom and determine if anything’s leaking, if it’s not, deck is considered waterproof and everyone moves on with the overburden installation. The issue obviously is you had, like you said earlier, you’ve got a much larger deck with lots of different things on top of it. What happens if it leaks down the road? That often then becomes hunting the needle in a haystack as you look to try and find where the specific location is that the water is coming in and in some cases, it may migrate some distance before it reveals itself down below.
One of those solutions that we’ve seen is a system called electronic vector mapping testing which is becoming more widespread in terms of its use. The system is designed where there are thin electric wires running around the perimeter of the deck. They’re attached to an electrical current which is then run through them. The deck itself only needs a small film of water across the top of it in order to be able to handle the electrical current, that basically if there is no break in the waterproofing membrane, the electrical current is able to pass across and over the top of the water making a complete circuit. And this is then monitored on a device. If there is a pinhole anywhere within it, the electrical current or the vectors are drawn directly to the to the hole and as a result somebody who’s doing the survey can actually walk up to the location where the membrane is compromised and pinpoint within a number of inches as to exactly where the hole is located. The advantage you have obviously for that long-term for a hotel or somebody like that with a large amenities deck is if there is a leak, the ability to go back and then pinpoint exactly where that leak is occurring can severely shorten the amount of time needed to make that repair, because repair could actually be undertaken in a couple of days as opposed to a week or two weeks if you were looking for the leak beforehand. And that’s one of the advantages of the vector mapping, that once those wires are installed with the small attachments left, the attachments can be left exposed through the hardscape system and the wires left in place and that way at any point during the service life of the deck one can come back and run that testing again if there are any leaks or it’s compromised. So again, it may not be for every building that’s built there but certainly depending on how often your deck’s gonna be used and what the inconvenience might be like to be out of service, it’s something that should be considered.
Paul: So that’s pretty interesting and I actually didn’t know that. So what you’re saying is that you can pre-wire a deck during construction or maybe even after construction for this vector mapping analysis whenever it’s needed?
Peter: Yes, correct. It’s put down… Basically, the wires are thin, they’re probably like a string for a guitar. It’s not a very large thing so it doesn’t impact in terms of the space it takes up and it needs to be around the perimeters and then it’s just simply a case of leaving an inch or two that may stick up above the pavers in an, you know, unobtrusive location where somebody can come in and then hook up to be able to put the electrical charge through it. So it does allow you to leave it in there permanently and it does give you quick and rapid access for leak detection down the road.
Paul: It’s that. You know, and to be able to go find, pinpoint the leak, it’s huge, I know, you know, on these decks where the water is coming out doesn’t mean that’s where…you know, right above it is where it’s coming in and to be able to avoid having the demolition, large areas of deck and then hope you found it. I mean, I’m sure that you would be able to tell us your experiences where people have done big demo and repair jobs and found out they missed the spot.
Peter: Yeah. Oh no. Or they open certain locations and then once you’ve opened it up, you’re then now looking for that location. Somebody gave the analogy the other day in a conversation about the fact that they had a waterproofing system down that had happened to have caught a small thumbnail in it. And the thumbnail had compromised the waterproofing system but it was trapped inside the membrane itself. And so they said they knew the deck was leaking under the old conventional system but they weren’t able to find it and it took them a number of days of actually sort of walking slowly and surveying the entire deck before they actually found this nail that was embedded in the membrane that had created the problem. With something like vector mapping, they would have found that thing within minutes of turning the electrical current on.
Paul: Good stuff. So another trend that we were gonna talk about was, what’s going on on the roofs of buildings these days and then how does that involve you as opposed to a roofer?
Peter: We’re seeing a little bit more in the sense that roofs are not being left as idle space. Obviously in condominiums, that’s where you’re selling your top of the line units with penthouses and condominiums so one is seeing that the roof is being converted into utilized space, whether that’s a small penthouse deck with a dipping or plunge pool that’s available for that particular unit owner or you’re seeing them use it for everybody in terms of becoming common area space with again as an amenities deck, one is either sort of seeing them on the top level of the parking garage or you’re seeing them being used again on the roof. We’re also seeing them for example in the service industry or hospitality where a rooftop area can be utilized for weddings and as a functional area of space and so we’re seeing a little bit more of that being used. And it leads to a combination of things. We’re seeing some roofing systems that get used under amenities decks and at the same time we are also seeing hot fluid applied systems being used up in those roofing areas because they’re doing other things on the deck to utilize it as an amenities deck.
Paul: And then what about green roofs? Sorry, give us a little… Tell us what… Well, I think hopefully most listeners know what a green roof is, but maybe a little brush up there.
Peter: Well, the green roof is basically taking the horizontal surfaces. Basically, if you’re in a large city they refer to the urban heat index which is all the areas that can reflect light. And so the idea behind it is to try and reduce the amount of asphalt and concrete that’s being exposed to direct sunlight. And so rather than simply putting an all paver system on it or put this conventional roofing system on, these areas are being turned into garden roofs where they’re introducing landscaping to add greenery to there to break down the amount of heat build-up and also they utilize the space as a opportunity for the residents to be able to use and utilize that area without being scorched to death in terms of high heat and reflectivity.
Paul: Yeah, you know, roof, I mean, I know I’ve been to some rooftop bars and whatnot and they’re pretty cool. The whole issue there is that there’s a lot of stuff underneath it. So, you know, if you have even an amenity deck, you know, if it’s leaking in the parking garage you certainly don’t want that to happen and you may have some damage, damage a car or something like that. You’re on top of a 20 story building and it leaks, it can affect a lot of interior spaces and really have a big damage claim. Do you see more redundancy on these rooftop systems than you do in other areas or what’s being done to try and lessen the potential for liability?
Peter: I think you are seeing that redundancy being built in, I think what you’re looking at there and you’re seeing it in some of these, we talked earlier about below grade waterproofing. You know, the emphasis on using the best products that are available or the best systems that are available. As we talked about earlier there’s good, better and best and in some cases best is worth the investment simply in these cases because they’re sort of user friendly or system friendly in terms of the substrate and we can sort of all go to bed with a lot more peace of mind knowing that although we can’t see what’s happening on the waterproofing system, we know that it can defend against most of the types of situations that we may find.
The other thing that’s very helpful and that we push for a lot and would encourage everyone to do and that is to have a pre-installation meeting before the work starts on these. What you’ll find as we’ve discussed here in this podcast is that your concrete subcontractor is involved, your mason is involved, there’s building planter walls. You may have other trades as well, electrical or plumbing that are involved because they put penetrations through the decks and stuff like that that the waterproofing is impacting other trades and other trades also have responsibilities towards ensuring that we have the right kind of substrates for waterproofing and as a result to put everybody in a room so they understand what their roles are, or that their role in this particular project has changed in terms of responsibility is very important in terms of being able to get out and get those things done correctly.
Paul: What other quality control measures are, you know, you or we are typically providing or recommending to our clients that can help them from, you know, the third party perspective? Talk just briefly about why a third party…why use a third party instead of having the contractor do his own quality control?
Peter: Well, I mean, the situation that you’re looking at, one is experience and expertise. A contractor could do his own quality control that would have to do with him being familiar with regards to the system, the processes of installing it and what type of testing or other material qualifications that are needed.
Paul: Is there any concern about the fox guarding the henhouse, so to speak?
Peter: Well, it will always be there. I was just about to get to that. Everyone else has got a vested interest from a financial perspective. Obviously the general contractor is somewhat biased because his project and his contract is based on time. So he’ll always be looking at that from the back of his mind. The manufacturer obviously is in the business of selling materials and so again if you don’t know whether you’re being upsold or whether there are areas where you may be able to make some compromises or look at some revisions in terms of saving money or time, it may not be offered to you at that particular point. We represent somebody who has no vested interest financially other than being reimbursed for our time but what we do is provide an unbiased opinion which someone can make an informed decision that’s in their best interests.
Paul: And then what… And this, we’ll run through real quickly, what a typical scope of services would be for waterproofing on, say, a 20-story high-rise building?
Peter: That… Twenty-story high, it would depend on a lot of what they’re doing. I mean, waterproofing services would include below grade which may simply be the elevator pit depending on the construction or it may have more to do with the foundation. And the basement, as we move out of the building, that will have to do with cantilever balcony decks which is typically a membrane system designed to protect the concrete. We have the amenities and terrace decks that we’ve talked about or roof areas that would be a part of it. We have walls and other things that we have that are a part of it. What we typically provide as our services is that we do review at the outset, which is to look at all the construction documents to make sure that all the areas that are to be waterproofed have been recognized and have been mocked up correctly with the system that’s been used. We look at the specifications to determine that the types of qualifications that the installer brings to the table are important, very often they’re required to be certified but they don’t look for experience. Somebody who got certified yesterday and arrives today meets the certification qualifications but it doesn’t mean they know how to use the system. And then obviously while the work is being done, we can either provide full-time inspections if it’s a very sensitive installation or alternatively spot checks during the course of it to make sure that the work is being done correctly. Participation in the pre-installation meeting is to make sure that all the issues that need to be resolved have been before the work starts.
Paul: So, you know, another big concern I know with waterproofing systems are warranties. And that, you know, there’s a lot of different…obviously different types of warranties and whatnot. You know, there’s material warranties and then there’s I guess what I would call system warranties or warranties that include everything including fixing it.
But as a material warranty, it may just say, you know, if this material fails we’ll give you some more. Lots of luck digging a hole in the ground to put it in there. What’s kind of…if you can just talk a little bit about warranties, maybe start with below grade and then just kinda go up the building?
Peter: Well, typically below grade waterproofings, again a lot of people say waterproofing is not worth the paper that it’s written on. I mean, and to a certain extent it might be correct. The issue you’ve gotta realize is that the warranty was drawn up by the manufacturer so therefore it’s obviously designed to protect him and his interest from being exploited. So as a result, as you said, warranty is typically divided into the least bang for your buck is a material warranty which just simply states that if the warranty…if you have a failure they’ll provide you with new material which is essentially shipping a bucket to your project site and then from there on, you’re own your own.
Labor and material is the next one that comes up which says that if you have a problem with the material, they’ll ship you the new material and then they’ll pay somebody to go ahead and install that material for you.
The next one that needs to go up above that which is the key one that needs to be brought in in a lot of contracts is an installer’s warranty. Very often the manufacturer doesn’t pick up the installation aspect of it unless it’s specifically asked for or a part of their warranty which means that if something wasn’t installed correctly or the preparation wasn’t done correctly and the material fails as a result of that, it’s not the material manufacturer’s responsibility at that point to repair it, we go to the installer and it’s important to have them tied into it, and at least for about two years because one to two years, if they’ve done something incorrectly, the outside will typically fail within that period of time. If it’s material related to do with the weathering and aging of the material, you’ll want the longer term warranties.
Generally speaking below grade runs 5 year warranties, 10 years with a slightly more stringent inspection program supervised by the manufacturer. And when you move up the building, your deck membrane systems and balcony decks are usually 5 years, and when you get to the hot fluid and cold fluid applied systems and terrace and amenities decks, you’re running anywhere from 10 to 15 years for the cold fluid applied, and then for the hot rubberized asphalt it runs 15 to 20 years typically for the warranty coverage.
Paul: More in line with what you see of some roofs.
Peter: Correct.
Paul: Are there any all-encompassing warranties available where, you know, they basically say, “If this fails we’ll fix it.”
Peter: There are some. Again you’re probably going to pay a little bit more for it when you…at the outset and there may be a situation where to get more bang for your buck you’re basically paying a few more bucks to upgrade your warranty. One manufacturer that I’m aware of which is Neogard, used to run a system where they actually provided what was called a joint and several warranty. They work with a certified applicator program, they didn’t sell to just anybody but based on that it meant that they would cover the labor and material and the installation and they would do it together and separately. So that if for example the installer went out of business three years into a five-year warranty, Neogard would continue to pick up the installation side of. It was based on, you know, looking at the finances of the subcontractors that we’re using as well. It was a calculated risk but it was an all inclusive package. Basically, if anything went wrong with the material installed, somebody was liable and somebody incurred the cost to repair it, not the owners.
I know for example some of the hot rubberized asphalt as we mentioned earlier have specific warranties that we’ve talked about, being a flat roof or being aware of standing water in some of those and it will become more comprehensive in terms of what their coverage is. You get some of the more inclusive ones too. For example, CETCO have a HydroShield warranty which is a specialized one. You pay more for it, it requires more inspections but as a result, they’ll give you more coverage based on the fact that they’ve had more QC upfront in terms of how the product’s installed and used.
Paul: Interesting. And I know that we’re a certified CETCO inspector and when we get involved with these CETCO projects, there’s specific requirements that are required of a third-party inspector and we’re out there a lot and that’s how they basically have assurances that what their warranting was done correctly underground basically.
Peter: Yes, correct. They sold lots of material for a while and everybody used it, it was the most popular material but essentially they had no real check on what was happening sort of once the rolls of material left the vendor to go out to be installed and as a result they were getting all sorts of phone calls saying, “Hey, our product’s…your product’s leaking, come out and fix it.” and we went out and when, “We didn’t know you used the product here and you don’t use the product like this.” And as a result, they realize they’re exposing themselves to a great deal of liability so they’ll continue to sell the material like that but if you want a strong warranty they wanna be involved in the quality control up front in order to be able to make sure that their risk and their liability is minimized. And so yes, they have benchmark inspections that we have to do at particular points throughout the process but essentially every piece of bentonite material that’s put in under that warranty has had eyes on it before concrete is poured on top of it to make sure that it’s done correctly.
Paul: Yeah, good stuff. So, Peter, I’d really like to thank you a lot for being the guest today on the Everything Building Envelope podcast.
Peter: You’re welcome.
Paul: It’s really interesting and I’m hoping that we’ll have some future episodes where maybe we can dig deeper on some of this stuff. I’d like to thank everybody for listening. If you have any questions, Peter can be contacted through GCI, through the GCI website and he’d be happy to, I’m sure, you know, chat with you about things.
Peter: Sure. And if, again, if it’s a question that has more a broad-based appeal we can introduce it into another podcast and answer it for everyone.
Paul: Yeah, that’s right. We’d love to have any suggestions for topics. So with that, this is Paul Beers.