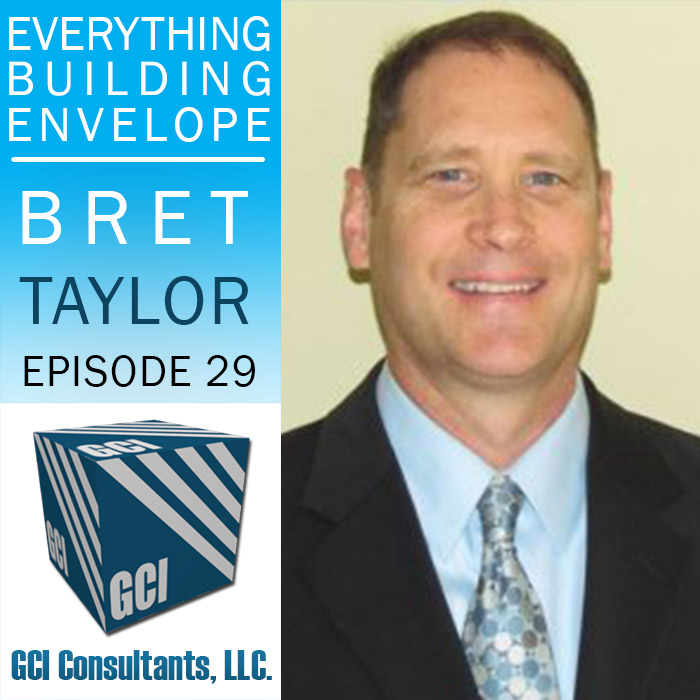
About The Everything Building Envelope Podcast: Everything Building Envelope℠ is a dedicated podcast and video forum for understanding the building envelope. Our podcast series discusses current trends and issues that contractors, developers and building owners have to deal with related to pre and post construction. Our series touches on various topics related to water infiltration, litigation and construction methods related to the building envelope.
https://www.everythingbuildingenvelope.com
*** Subscribe to the show and leave us a Review on ITunes!
Paul: Hello, everyone. Welcome to the “Everything Building Envelope” podcast. This is your host, Paul Beers. And our guest today is Bret Taylor. Welcome, Bret.
Bret: Good morning, Paul. Glad to be here.
Paul: So Bret is a fellow team member of mine at GCI Consultants. And Bret, before we get into the subject, maybe you could tell everybody a little bit about your background.
Bret: Absolutely. Well, like a lot of engineers, started working for firms just out of college to gain experience as I came up through the ranks. Focused in on structural engineering as my career focus. And did some building design, like most junior engineers do, so small commercial, residential type structural engineering work, construction repair type work.
And then eventually broke off on my own, started my own firm. I did that for 15 years in North Carolina. Enjoyed that thoroughly, learned a lot. And as I was, I guess, getting exposure as the leader of my own firm, I started to run into different scenarios that were different from just regular design work. Because I’d get calls from clients that would say, “Hey, you know, we have this structural issue. Can you come out and take a look at it?” And I did, and I guess my segue into the forensic world. And it just advanced from there.
And then I started doing work for insurance companies, investigating various types of cause and origins, issues there, water penetration, hail damage, lightning strikes, that kinda thing. And so my forensic career evolved even more. Then a couple years ago I decided to make a change. I wanted to get involved in, I guess, the larger forensic world and made the move to Florida.
Paul: We’re really happy that you did. So you’re a licensed engineer in Florida, and a bunch of other states, that’s right?
Bret: That’s correct. I’ve gained licensure in a total of 12 states. I was just gonna say, essentially all up and down the east coast of the States, and then over as far as Louisiana.
Paul: Great. One thing that I know that you didn’t tell anybody about I think is really interesting, when you were early in your career you worked overseas, didn’t you?
Bret: I have, yeah. Very early on I found an opportunity to work in Germany after the wall came down. Essentially when the wall came down, East Berlin opened up to West Berlin. And the infrastructure was in horrendous disrepair from all those years of socialist occupation from the USSR. And so lots of construction work going on, and they just needed more professionals than they could source. And so there was an architect professor who was German at NC State, from which I graduated, that was getting his architectural students work. I met with them and they helped me plug in. So yeah, I got about a year and a half exposure in Germany.
Paul: Yeah, that sounds like funny actually. Yeah, it’s a great opportunity. I wish I would have done stuff like that in my younger days actually. We got a really great topic today, stucco around wood frame window openings. So Bret, you recently were the primary author on a publication of that same name that was produced by the Florida Lath and Plaster Bureau, is that right?
Bret: That’s correct. Part of a windows committee that broke out around the topic of wood frame window openings with all the stucco litigation going around currently. We decided to break out a committee. I joined that committee. And we have many more technical bulletins planned, but as we were getting into discussing what we wanted to accomplish in the committee it became apparent pretty quickly that this is a huge topic. Because once you create an opening, that’s an opening you have to seal. On top of that, with a window installation you have a lot of integration between the different parties that are performing different component of the wall construction.
Paul: Yeah. You know, so wood frame construction really is a big part of the construction methodology that’s out there. We see it anywhere from single-family homes to, you know, pretty good sized, mid-rise type structures, multi-family residential, hotels, office buildings, commercial, you know, retail, all sorts of different things. And they’re all different obviously, and one size doesn’t fit all. But as you say, there’s been a lot of, over the years, litigation. And on our expert witness side of things we’ve done many, many, many hundreds, maybe thousands of buildings over the years with wood frame and stucco.
And, you know, where there’s been allegations of things maybe not going correctly or having issues. So this is a great topic, and really excited to see the piece that you guys put out. And maybe we can just sort of run through it a little bit more. I know it focuses with codes, and standards, and whatnot. So can you maybe run us through some of the highlights of it?
Bret: Sure, absolutely. I guess to start off I’d just say, you know, it’s for general educational purposes to help folks in the industry get their head around the codes, and guidelines, and standards that are involved. So it should be helpful to folks in the industry. It’s not a document that covers every single aspect, and certainly doesn’t get into details. We plan on working on some details in the future. But the takeaway is that there’s a lot here that folks need to know about. The designers need to be fully aware of these codes, standards, and guidelines, as well as the contractors. Because we’re all having to work together to make this building envelope penetration functional likes it’s supposed to.
So, you know, just having said that, just keep that in mind. And we developed this as a roadmap really to help people focus in on what’s important. And as we started to discuss what we wanted to create with this technical bulletin, it started to get big really quick in terms of information. So we had to step back a little bit, and we decided to break this into different technical bulletins going forward. And the first one we thought, it’d be best to create one that painted this thing as a global perspective so that people had the understanding that it was complex and there was more to come.
Paul: So can you kinda run us through, first, as you already mentioned, you guys talked about introduced codes, references standards, and industry guidelines? And kinda had a discussion that, you know, I think, just to summarize, as everybody’s familiar with the code, the Florida Building Code in this case, or the Florida Residential Code. And I wanna point out, too, by the way, while this was obviously put out by the Lathe and Plaster Bureau, this discussion can certainly go far beyond Florida. In fact, it has a national perspective on it. Now there’s obviously the Florida Building Code is not in other parts of the country, but the theory is pretty much the same everywhere. Would you agree with that?
Bret: Correct. The addition there would be that obviously Florida has many more opportunities for wind-driven rain. And so we seem to see the problems resulting from water leaks a lot faster, and maybe to a larger degree than others may see them. Although, you know, recently we’ve had a couple of jobs, one in Pennsylvania where they had pretty significant sheathing and wood frame damage to a single-family home. So, you know, it’s not isolated to Florida, for sure.
Paul: Oh, you know, and the sequencing of construction, the reference standards, the detail, and what, really doesn’t change from Florida, to Pennsylvania, to Colorado, or wherever. I mean, there’s some nuances with different climates and whatnot, but the concepts basically are the same, or very similar. Would you agree with that?
Bret: That’s correct. In general, the flashing, the concept of flashing is gonna remain the same throughout.
Paul: So let’s go through this a little bit, the document, which, as I said, was put out by Florida Lathe and Plaster Bureau. We’re gonna, just for everybody, in fact, if you wanna pause and get a copy of it in front of you, we’re gonna have it on our website. It’ll be in the show notes at www.everythingbuildingenvelope.com website. It’ll also be on our website at gciconsultants.com. There will be a link to download it. Or you can go straight to the Florida Lathe and Plaster Bureau’s site, www.flapb.com So any one of those places you can get it, it’s free. And if you wanna read along while we talk about it, that’s where you would go.
Bret: Yeah, there’s a special page, Paul, that addresses all the technical bulletins they put out. They have several that are very helpful. One of the other recent ones that was published is a lathe checklist. So inspectors in whatever capacity they function can utilize this to just have a checklist as they go through and make sure the lathe was installed correctly.
Paul: Yeah, you know, that’s great. Really great that they’re taking this one, because there’s certainly an information void at times, it seems like. So very helpful to try and pull things together from kind of a global or big-picture perspective. So the document references some codes, standards, and industry guidelines throughout the construction sequence. You know, without reading it verbatim, could you just kinda summarize what the sequence is and what kinda documents are referenced?
Bret: Yeah, so I put this together in the order of construction, or at least, you know, tried to. So obviously you start with your rough framing. There’s a little bit of waterproofing that can be done at the rough framing stage. Then you have your fenestration installation. Then you have your supplemental waterproofing around that fenestration, your stucco application afterwards, and then caulking and painting, hopefully following your stucco installation. So that’s the general format. We just tried to make it, I guess, visually and conceptually consistent with the way it was produced in the field.
Paul: And what are some of the standards and industry guidelines that are used along the way through this process? Or should I say, what are some of the other organizations that have guidelines that are useful and necessary to really do a thorough job of designing and then ultimately installing things correctly?
Bret: Right. Well, obviously Florida Building Code, Florida Residential Code are key. They’re gonna drive you towards referenced standards in those documents. They have different chapters that point towards reference standards, so that’s the key. So when you’re looking at the Florida Building Code, Florida Residential Code, you know, you’re gonna go towards the chapter six Wall Construction. That’s gonna contain quite a bit of information. They referenced ASTM E 2266, that’s gonna be your standard guide for design and construction or low-rise frame building wall systems. Chapter seven is gonna cover wall covering, finish direction area. Chapter six of the FRC is gonna cover exterior windows and doors.
AAMA is gonna have several standards that are helpful and they focus in specifically on different types of window installation. And they have one specifically, 300, which is the standard practice for installation of exterior doors and wood frame construction for extreme wind and water exposure. So that’s gonna be key down here in Florida. And they’ll have other ones that are just standard installation around wood frame openings that don’t have extreme conditions that would apply elsewhere.
ASTM E 2112 installation of exterior windows, and doors, and skylights is key. ASTM, of course, with regard to stucco, C 926, C 1063, those all address stucco applications specifically, stucco and lathe application. So yeah, there’s plenty of standards there for which to get some guidance. A lot of those standards are consistent in their message. So, you know, once you kinda go through one you get exposure to the other ones.
But my approach there was to just kind of include everything so that the detailer and the installer could be working off consistent documentation. And I think it’s important for everybody to know what’s involved so that they can recognize if someone in the chain of the process perhaps didn’t do what they were supposed to do. And we can segue into that later in terms of responsibility. But essentially everyone has to know what their part is and what codes and standards apply to them.
Paul: So the design professional needs to be aware of all this, and reference, utilize it in developing plans of specifications. Because ultimately that’s what’s used to build the building, correct?
Bret: Correct. And as you know, that’s not always the case. Some plans and specifications for projects just aren’t what they need to be. The details should fall on the designer of record, whomever that may be. And for whatever reason, those sometimes aren’t fleshed out adequately to make sure that the building is gonna perform per the Florida Building Code, or whatever code you’re utilizing. I think they all gotta be relatively consistent in that respect. If they say that the building envelope should be detailed and constructed in a way to prevent water intrusion.
Paul: That’s right. You know, you talk about details and I just think back to the one. My favorite is, you know, you see it on residential and also on multi-family where they’ll draw a typical wall section, and that’s it. There’s a typical wall section, and it’ll say “stucco” with an arrow pointing at it. So at that point, basically you’re leaving it up to the builder/installer/sub-contractor/workmen to put it up the way they think it should be done. And it’s just a process that’s inviting error.
Bret: Absolutely. And here’s where I get a little frustrated with those professionals, and we all kind of…we do it in our designs in certain areas and it’s acceptable. So for example, if we wanna kinda point back towards a structural example. You know, for the structural engineer, we’re designing the building to resist all the loading on that building so it doesn’t collapse, and to protect the public, and protect the occupants, and protect the investment. Well, okay. So I designed the structure but I don’t necessarily design the wood trusses, let’s say, that this property, whether it’s residential or commercial, has a wood truss roof on it.
I don’t actually design the roof trusses. That’s something that’s developed over the years where the manufacturer of the truss typically provides that design. They may have employed an engineer that does that design, or they may farm that out to another engineer. But essentially what I’ll say is, in my plans, you know, “Truss design per applicable loading.” And then it’s up to the building to find a truss manufacturer to provide that truss package and that truss design. And then I review that truss design to make sure it’s consistent with my plans and details.
So that’s a case where it’s okay to point towards someone else to provide a component of the design. But ultimately, as a structural engineer of record, I’m still responsible for that truss package to make sure it is applicable to my design scheme. And similar, this is typically in an architectural realm, similarly the plans and details focused around the building envelope fall under the architect, unless, of course, they wanna farm that out to someone else, which is okay as well.
But you can’t just point towards a standard wall section and say, “Stucco.” That’s not acceptable nor helpful. That really opens people up to RFIs at a minimum, but certainly potential litigation going down the road, which is part of the reason we’re having this podcast today.
Paul: Yeah, I mean, I think the key takeaway from that is somebody’s gotta design all the parts and pieces that go into the building. And ultimately design professionals has a responsibility to make sure that happens, whether he designs it or somebody else does. At a minimum, he or she should be reviewing everything and making sure it’s complete. And what’s interesting is you get into the wood frame…this is Paul’s observation, the wood frame construction market is lacking sophistication and depth. And what I mean by that is, you know, a lot of times it’s a low-bid scenario. So they’re trying to build a house, an apartment building, whatever, for the lowest possible cost and meet the code, which, you know, it’s supposed to be a minimum standard, but actually becomes the baseline standard. You know, “What do we have to do to say we met the code?”
So in an effort to save money, maybe you’re not paying the design professional to be able to do the job that they need to. And you’re ultimately leaving it up to contractors, installers, and whatnot to put everything together correctly. Nobody’s really looking over their shoulder and making sure that’s being done right. And guess what? You end up with problems. It’s just sort of inevitable. So one of the things, and Bret, you’ve talked about this so far, is that somebody’s gotta pay attention to the details.
Bret: Right, the devil is in the details, for sure.
Paul: Yeah.
Bret: And I’ll tell you, with the changes in the code standards and guidelines, along with the products that are changing rapidly…and then the lines are blurring, too, between who’s involved in what. I mean, you have window installers now that apparently they get asked to provide the flashing as part of their scope, versus having someone who may have more experience in that provide the flashing. Sometimes the framers even get called in to provide at least a certain level of building envelops protection and flashing.
Paul: So let’s talk a little bit about the scenario you just described where different people are providing things that are maybe outside of their scope, and, you know, may not have a good set of plans and whatnot. So let’s talk a little bit about what can be done to try to overcome some of these limitations, I guess we’ll call it. And so when GCI Consultants gets involved with wood frame projects, which we do frequently, you know, we basically go through a process where we try to work with an owner and architect that’s our client. We try to work with them to come up with a decent set of plans and specifications that show everything. But really then we get into submittals, shop drawings, product literature, things like that.
And often, you know, with the plans, and specs, and submittals, we don’t always end up with a clear picture of what’s gonna happen. So we really like to see two things happen at that point. One is to have a pre-installation meeting where everybody that’s involved, so that’s owner, architect, possibly structural engineer, framer, stucco contractor, window manufacturer, window installer, caulker, painter, everybody that’s involved comes to that meeting. And now we get the plans out, we get the submittals out if there are any. And we go through everything and basically try to review, “Here’s how we’re gonna do this.”
The other thing that we really like to do is a mock-up at the very beginning of the project. Now this could be an in-place mock-up, like the first area where we’re starting the work. Let’s install everything, let’s frame it, let’s sheath it, let’s waterproof it, let’s put the window in, let’s caulk it, let’s paint it. And let’s, you know, all agree that we’re doing it the right way. And just that alone brings you many, many, many levels above just having the guys go out and put it in. What are your thoughts with that, Bret?
Bret: Well, I agree. And I think mock-ups are becoming more and more popular and important. Because again, with all these new products coming online, and the labor not necessarily being able to keep up with proper installation and use of those products, I think it’s kinda key that you do that mock-up. I think in the grand scheme of things it’s a pretty cheap insurance policy to get everybody on the same page.
Oh, and then that’s kind of a segue to another important code point here, which is, like you said earlier, the code is minimum. But people think it’s baseline, or that that’s really all you should focus on is just meeting code. Sometimes you need to go well beyond code, and sometimes code that’s minimum actually doesn’t even apply to your situation. So an example of that would be stucco attachment to the building. The prescriptive stucco attachment that’s provided by the code doesn’t always work for every location, for sure, especially the higher glossy ones.
Paul: So if it doesn’t work, then what needs to be done?
Bret: Well, therein lies the need for the detailing. The designer of record needs to think about the application that they have in hand. And they need to think through each of the details, make sure that it’s gonna meet the actual code requirements, which in general is gonna mean meeting the wind load resistance. And then if you go through a mock-up, you can often discover, “Okay, well, this may meet the code, but we have an issue here with installation sequence.” Or, “We have a compatibility issue with product.”
So, you know, just running through that process of doing your mock-up, I think will flesh out a lot of the problems, put everybody on the same page. And then on top of that, it gives an opportunity for, you know, a company like us, for example, to go out there and provide third-party water testing in that window assembly and assure that that system is gonna function in the way that the owner intended to.
Paul: Yeah, because, you know, people always say, the question I’ve been asked many times is, “Well, the window’s already been tested, hasn’t it? Why do I need to test it again?” And great, the window has been tested in a laboratory, who knows where and when? So there’s so many things to confirm when you get it into the field. First of all, was the window manufactured the same way as the one that passed the test? And then even more important, you’ve got all these surrounding surfaces, you know, stucco, maybe a balcony floor, a ceiling, you know, whatever. None of that’s included in a product approval test for a window. So the system is never tested unless basically you do a field test during construction.
Bret: That’s correct. Yeah, the window is just a component of the system. And, you know, AAMA has done a lot to drive forward the window industry and window, AAMA, and windows and door manufacturers, and others have done a lot. But essentially the water infiltration testing, the wind load testing, and others, those tests are just testing the window unit. And a lot of times they’ll actually exclude portions of the window that people may not…well, not portions, but a portion of the window that people may not think about. And with respect to wood frame construction, that’s gonna be the window fin. So in other words, the fin, it’s part of the window. But in terms of the water infiltration testing, it’s actually not included.
Paul: No, that’s right. And as well as how it interfaces with all the surrounding materials.
Bret: Yeah. So yeah, your mock-up is key.
Paul: Yes. I see in the publication that you also put a little blurb in towards the end about maintenance. Do you wanna talk about that a little bit?
Bret: Absolutely. I don’t have to tell you that it’s a large part of what we run into when we’re doing our investigations. Florida has some amazing sun and fun. That sun and fun comes with a cost. The sun is very intense here, so it tends to degrade paint and caulking quicker than maybe some other locations around the state. And so owners are having to do maintenance more often, maybe, than other parts of the country.
So yeah, it’s key to do that maintenance. And actually Florida Lathe and Plaster Bureau has developed a separate technical bulletin. If people wanna pull that up, that’s TBST-04-12, and that is Stucco and Building Exterior Maintenance. And it goes through the requirements for maintenance there. But essentially, if I had to pick one spot that I would really focus in on that would be the interface of the stucco, and the window frame, and the detailing of the accessories, and the sealant around that interface. That tends to be a location where details aren’t always correct.
And even if they are correct, or even if they’re not correct, let’s say. Even if you do a good stucco or sealant around a not-so-good stucco detail, that’ll go a long way for sure. But if it’s done correctly, but the sealant and the paint aren’t maintained, eventually you’re probably gonna have at least the potential for water intrusion there.
Paul: Yeah, and stucco, I mean, I’ve said this many times, I’ll say it again. Stucco cracks, I mean, it happens. It’s not necessarily catastrophic where it’s cracking and falling off the building, but, you know, it gets hairline cracks and whatnot. And over time, sealants degrade and paint, you know, may chalk, or wear off.
So all these parts and pieces have finite performance cycles, or life cycles. But a well-designed exterior wall system accounts for all this. You’ve got a moisture vapor barrier within the wall system, where if any water gets in it collects it and drains it to the outside. And obviously the maintenance is very important because the less water that gets in the better. But as you mentioned, there’s a lot of parts and pieces. And really everything needs to be done well to have an overall globally well performing and healthy building.
Bret: That’s correct. That’s actually probably even a separate topic because we can go far and deep on that. But in general, I’ll point back to the fact that the code is minimum. And, you know, stucco, as you said, cracks. Stucco, if it’s not painted, is actually going to absorb water and then will release that water whenever the conditions around it dry out. So it’s, you know, it can absorb and expire water cyclically. As long as the system is designed to accommodate that, then you shouldn’t have any issues. But again, the fact that the code is minimum doesn’t necessarily remove the potential for having water penetration issues. So for example, if you’re on the north side of the building, or if you have an area where there’s sprinkles that continually impact that stucco, a good system over time can still have issues and/or degrade more quickly.
Paul: Yeah. So you mentioned that the publication, “Stucco Around Wood Frame Openings” with the Florida Lathe and Plaster Bureau as kind of a starting point. What’s next?
Bret: Well, we are in the process of determining what it is we wanna discuss going forward. We have some bullet points in the bulletin. We’re currently talking about details, trying to figure out if we wanna provide some details to assist people with that. There’s a lot of work there that still needs to be done. But I think, you know, stucco to window frame interface details, like I mentioned a minute ago, is the key one that we need to focus in on. That’s challenging, though, because there’s so many different window manufacturers, and a couple…at least three or four common window profiles that need to be addressed. And of course, then you get into different types of flashing, and different configurations of windows, even different installation schemes of the window.
So for example, you have a flush window, or you can have an inset window. So there’s a lot to consider there. We’re still in the process of trying to figure out what it is we wanna cover and how we wanna cover it. But in general, I think we’re going to try to touch on each component that may affect the window installation, on down to, you know, the sheathing, the framing. So for example, there with the sheathing, if you have sheathing that doesn’t have adequate gapping, over time that can create some issues that may impact your stucco and/or window installation.
Paul: Yeah, it’s a big undertaking, no question about it, as you correctly point out. A lot of variability, a lot of different scenarios. So I wanna commend you and the Florida Lathe and Plaster Bureau for, you know, having this conversation, having this discussion, putting out this document. And I think it’s really great. And I really appreciate you coming on the podcast today. I thought it was a really good discussion. So thanks very much for that.
Bret: Absolutely. And Paul, let me just give a little bit of a plug for stucco in general. I mean, you know, obviously the Florida Lathe and Plaster Bureau is focused around that type of construction. There are a lot of cases going around currently that are revolved around stucco and its construction. Stucco is just like any other building siding material, you know? It’s not perfect, but if you build it properly, it will perform its function. I think a lot of the issues that we’re running into now with stucco aren’t necessarily, you know, just the material. It’s the fact that it’s a wall system is a complex system. A lot of different pieces and parts have to come together properly in order for it to function properly.
But, you know, the first thing people see is stucco. And, you know, they, “Well, this is stucco.” Or even a window, they say, you know, “There’s a leak and it must be the window.” So people tend to simplify things, I think, too much. And there are other causes for building envelope issues other than what you can readily see on the exterior. So I’d say, you know, we’re trying to promote stucco in general at the Florida Lathe and Plaster Bureau. It’s been a great building material for a long time. And, you know, we’re just trying to help people understand that the material itself is not necessarily a problem, and you can accomplish a very sturdy, sound, and aesthetically pleasing building exterior with stucco.
Paul: Yeah, I’ll give a “me too” on that one as well. If you look at it from a nationwide perspective, and I don’t think this is an exaggeration, there’s millions of structures that have high-performing, well-performing, durable stucco installation. We do tend to focus on the problems, which, you know, they’re out there. And we don’t focus so much on the fact that it is a really good option for exterior growth buildings, and it’s been used successfully, repeatedly throughout the…actually throughout the world. So yeah, let’s recognize it for what it is.
So with that, again, thank you, Bret. And I’d like to thank everybody for listening to the “Everything Building Envelope” podcast. Please visit www.everythingbuildingenvelope.com. We’ll have show notes, and we will have a link to the Florida Lathe and Plaster Bureau, along with a link to the particular document that we’ve discussed today. And also, gciconsultants.com, if you’d rather go there we’ll have the same links there as well. So thank you, everyone. And until next time, this is Paul Beers saying so long.