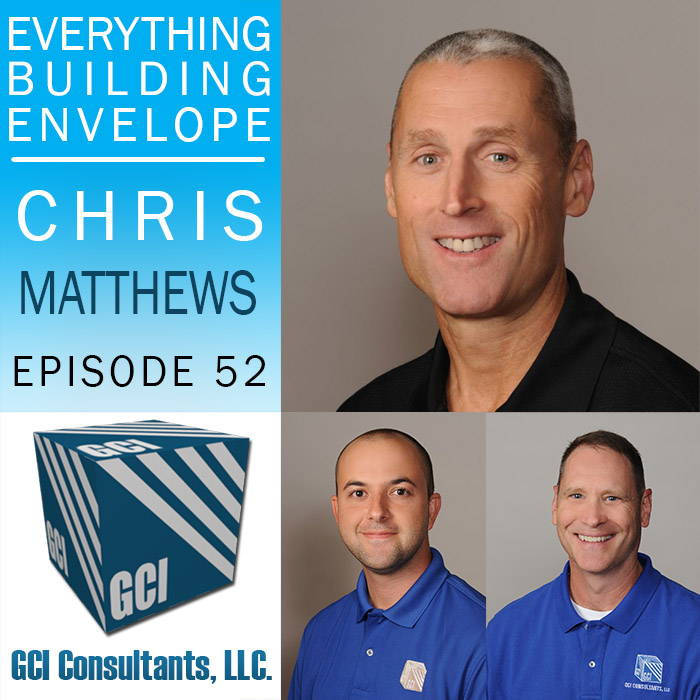
About The Everything Building Envelope Podcast: Everything Building Envelope℠ is a dedicated podcast and video forum for understanding the building envelope. Our podcast series discusses current trends and issues that contractors, developers and building owners have to deal with related to pre and post construction. Our series touches on various topics related to water infiltration, litigation and construction methods related to the building envelope.
https://www.everythingbuildingenvelope.com
*** Subscribe to the show and leave us a Review on ITunes!
Chris: Welcome everyone to our “Everything Building Envelope” podcast. I’m Chris Matthews of GCI Consultants and I will be your host today. I’m really excited today to have, as my guest, two of our forensic engineers at GCI, Bret Taylor, and Jason Bondurant. And we’ll be talking to you about a very interesting topic today, barrier versus drainage wall construction. First, I’d like to introduce my guests and have them tell you a little bit about themselves. Bret, why don’t you introduce yourself to our audience?
Bret: Hi, I’m Bret Taylor, a senior consultant too with GCI. I’ve been in the engineering and building envelope industry now for about 27 years. I graduated from NC State, North Carolina, back in the early ’90s. And I’ve kind of progressed from pure structural engineering into building envelope and forensic investigation, litigation support type work for GCI.
Chris: Thanks, Bret. And, Jason, why don’t you introduce yourself?
Jason: Hi, my name is Jason Bondurant and I’m a Senior Consultant with GCI for about six years now. I work mostly in forensics and dealing with problems with existing buildings.
Chris: All right. Thanks, guys. So, as I said, we’re going to talk today about drainage walls and barrier walls. We think it’d probably be best just to define what we mean by those types of walls first. So, Bret, can you kind of explain how we would define a drainage wall system?
Bret: Yeah. Well, in general, a drainage wall system is going to be a system in which there’s an exterior cladding behind which there will be some form of the drainage plane made up of different construction components, just depending on what’s needed for the area that you or the building happens to be in.
So, the general premise is that the exterior cladding controls the majority of the water, but based on experience and years of construction and co-development, it’s commonly known that there’s gonna be some sort of moisture that’ll make its way behind the primary cladding system and that hence little water will need to be drained back out to the exterior. So, with the drainage wall system, we typically understand that we’ll have to provide some sort of flashing to redirect that and send that water back out to the exterior.
Chris: And I think maybe like kind of the most commonly known or the most historic method of that would be a masonry veneer with through-wall flashing would kind of be the typical go-to reference for that type of construction. Jason, what are some other types of cladding systems that we see in a drainage wall application?
Jason: So, I would say one of the most common these days that we deal with are stucco and modern brick systems, which also incorporate some type of weather barrier behind the stucco and eaves and through-wall flashing to manage that incidental water penetration. And then there’s other types as well, like metal panel wall systems.
Chris: Yeah. We see metal panels sometimes some flowstone veneers, different types of siding systems. Pretty much any type of cladding system that’s going to go over a backup wall should be set up as a drainage wall system. And then comparing that or contrasting that to a barrier wall system, Jason, can you kind of explain how we would define a barrier wall?
Jason: Yeah. So, a barrier wall system, unlike a drainage wall system, a barrier wall system is really designed to stop all water at the exterior face of the wall. So, there would be no provision to manage any water that got behind that exterior plane of the wall. So, typically the wall is going to rely on exterior coating, sealers, and sealant joints to keep 100% of the water out of the building. It’s basically a zero-tolerance type of a wall.
Chris: And some of the types of barrier wall systems that we work with would be…
Jason: And I would say that for us, based in South Florida, this is the most common type of wall system that we deal with on a regular basis. And most commonly in South Florida, that would be stucco direct applied bonded over CMU and concrete walls. That’s the most common type of barrier wall system that we deal with.
Chris: Sure. And then in some of the larger buildings, commercial buildings, healthcare buildings, buildings in other areas of the country that we work on, precast panels, tilt-up walls, those types of things are also a real common type that I think of that are a barrier wall assembly. Then we had also talked about kind of one other historic type that we’re not gonna touch on as much, but that’s a mass wall system. Can you talk to us a little bit about the concept of that, Jason?
Jason: Yeah. So, the mass wall is not something that we see too often, but we do deal with it sometimes when we’re dealing with problems with much older buildings. And basically, the mass wall system, it’s essentially just relying on the sheer thickness of the wall and the ability of the wall materials to absorb and handle the moisture in order to keep the water out. So, essentially what’s happening is the wall is getting wet and then you’re just relying on the evaporation of that moisture to dry it out. And so, usually, the types of walls that we see that are managing the moisture in this way are more historic masonry-type wall systems, multi-ways, you know, brick types of walls, or other types of masonry cladding.
Chris: And I think, Bret, you had mentioned that an older type of construction that you’ve worked on, some with direct applied stucco mass wall application where they didn’t have an exterior paint on those?
Bret: Yeah. That’s correct. In South Florida area, it’s going to be direct applied stucco to CMU or maybe some other type of brick or block. But the older systems would typically, it would either be just a grey stucco or perhaps a tinted stucco. So, the tinting would address the coloration needs so that there would be no paint applied to the exterior.
Chris: And I’m telling you guys that I worked on and continue to work on a lot of projects down in the Cayman Islands and their construction method down there was similar to what Bret was saying where they would build a CMU wall, put a stucco render on the outside, and then they wouldn’t do furring and drywall like we would do here in the U.S., they would just do a plaster render on the inside of the wall with the idea being in their climate, the wall was going to get wet and they would just let it dry out. They didn’t even try to have any components there that wouldn’t be tolerant to constant wetting and drying. So, something that we don’t see very often nowadays, but another type of wall that’s out there.
Bret: So, Chris, I’ll add to that as well. That’s, or at least it was back in ’95 era. That’s how they built them in Germany. Believe it or not, over there they would use different type of block coat. So, they would have a foundational block that was a solid limestone-type cementitious material for the foundation walls. But for the upper walls or insulation, they would actually use an extruded clay block that had air entrainment in the actual clay itself.
And these things were…gosh, they must’ve been at least 12 inches wide with diamond shape, you know, extrusions on the interior and that provided the insulative piece. But then they would do a direct applied stucco on the outside and, just as you mentioned, a plaster rendering on the inside. So, they, you know, being in Germany, that’s how they got their installation with that diamond shape air void system in the block itself. So, you know, that system can be applied anywhere really with different materials.
Chris: Right. So, in those different parts of the world, it may still be a pretty common construction method, even though here we’re seeing more of the barrier and drainage type walls on the newer projects that we deal with?
Bret: Right.
Chris: So, we were going to talk some about the pros and cons of each type of system and I think just generally the performance of each type. So, Bret, could you start the conversation about the drainage wall system and some of the pros and cons and construction concerns with that type of wall system?
Bret: Sure. There are many, but to keep it relatively generic, I guess some of the pros with the drainage wall system is it does offer some redundancy, it allows you to drain any incidental water that may make its way in. And for those of you that have been following our other podcasts, you’ve heard that, you know, windows systems have a limit. They’re designed for structural capacity, but they also have some level of water resistivity, but they’re not going to resist all storm events depending on what that particular window unit is designed for.
So, if you do have a storm event that occurs that exceeds that window’s capacity, you could have some interior infiltration around or even through the window, or you could just have infiltration at other penetrations in the wall or detailing conditions in that wall. So, the redundancy that the drainage system provides and the flashing provided to kick the water back out to the exterior is definitely a pro.
An example of a con might be, at least compared to, let’s say, direct applied stucco to the block, it could be an additional cost. The detailing between the envelope components and flashing the architectural detailing and all those things could really complicate the construction and elevate the costs and perhaps even create conditions, which are, you know, really difficult to properly provide waterproofing and sealing for. So, and a lot of the newer construct is really turning out that way.
The newer construction has a lot of different architectural transitions, we’ll call them, you know, for example, bump-outs in the wall or corners in the wall, decks, patios, those types of things are going to create conditions in which you really have to pay attention to the detailing and the flashing.
Chris: And as you said, I mean, it’s a great system and I think is the logical method in that the idea being that water will get behind these cladding systems, hopefully not a lot of water, hopefully just incidental, as you said, but the plan should be that it will and that it needs to be managed. But there is a lot of workmanship, from our experience, that’s required in…workmanship and detailing required to get these things right. And as you both know, we go to a lot of jobs where it wasn’t done right and there are some pretty severe problems either by a bad plan about how these weather barriers and flashings are installed and integrated or poor execution, poor workmanship in putting those materials together.
I think a lot of people understand the purpose of the weather barrier to protect that wall behind the exterior cladding, but we also find a lot of people that don’t understand that that drainage flashing is just as important. I don’t know what you guys feel about that, but I often see buildings that are wrapped up great, but there is no through-wall flashing or it’s not properly integrated, and I try to explain to people that no matter how well you protect that wall, if you don’t drain that water out, eventually it’s going to find a way back in.
Bret: That’s right. And what I was gonna say is, the devil’s in the details. And really, I’ve seen both conditions in which the detailing wasn’t necessarily perfect, but there wasn’t, you know, any damage there. So, it was functioning. Then I’ve seen conditions where it was done properly, but maybe someone had penetrated the WRB, the weather-resistive barrier. I’ve seen conditions where bulk water was being allowed to enter and even though it was constructed properly, that bulk water just overloaded the system. So, it really boils down to the devil’s in the details and the construction has to be correct.
But, you know, the concept of a drainage wall is the drainage is only for incidental water. So, if the cladding on the exterior and the attention to detail around the sealant of paint and guttering, you know, anything that could force bulk water behind the system really has to be thought about. And then typically, that’s gonna fall on the designer of record that’s providing design and detailing for the wall construction itself.
Jason: Right. And, Bret, one thing that I was gonna add on to that, which is also I would consider a con to this type of a wall system is when we are dealing with problems with a drainage wall system, a lot of times it’s necessary to do some type of destructive testing in order to get to the bottom of where the leak is coming from because the wall system is relying on that drainage plane and that weather barrier which is concealed behind the exterior cladding. So, I would consider that another con.
Chris: Yeah. That’s a great point. Go ahead. Sorry, Bret, go ahead.
Bret: Depending on the way it was built, the water, you know, as we all know, water can travel in strange ways. So, depending on how it was built, how the water’s traveling, I mean, it could be coming from anywhere. And you’re right, you have to do DT most often in order to determine where that water’s coming in, obviously, using proper testing methods with ASTM E2128 and/or, you know, ASTM E1105 testing to trace that path of water, recreate the leakage event and then trace that path of water. I have been lucky though, a couple of times I’ve actually been able to trace the path of water without doing DT. It’s not very common, but if you have enough time and the conditions are right and you can isolate on the exterior sufficiently, it is possible to, you know, drill-down and find, you know, the only one remaining thing that it could be letting water in. But that’s very rare.
Chris: Right. Yeah. I’ve had the same experience that once in a while you can but, unfortunately, if there’s a leak problem, you can usually recreate it pretty easily, but tracking down what’s going on, as you said, Bret, you usually have to remove that wall cladding to get in there and determine what the problems are or hopefully…or how they’re going to correct them as well. I think another thing along that same line is that diagnosing them usually requires destructive testing, and then correcting them are usually very expensive problems to correct because the problems are usually hidden details behind the exterior wall cladding and that gets expensive fast to correct those.
Bret: That does. Yeah, definitely in comparison to a barrier system.
Chris: So, Jason, why don’t you talk to us about the barrier wall systems, some pros and cons that we see with that type system.
Jason: I would say one of the biggest pros, just generally, is that a barrier wall system, I would consider it to be much simpler in that you’re only relying on that exterior face of the wall to resist all the moisture penetration. So, in terms of, you know, like we were just talking about, diagnosing problems and tracing leaks, that becomes a lot simpler with this type of a wall because you can actually see that exterior plane of the wall that’s supposed to resist the water, and you can see to the condition of the coatings and sealants that are intended to resist that water. And the detailing is much simpler because you don’t have to worry about the through-wall flashing and the transitions become a little bit simpler. And so, you know, I would say those are the main pros of a barrier wall system.
As far as the cons go, and we already talked about this a little bit, but there’s a single line of defense. So, there’s no redundancy in the system, unlike the drainage wall system. So, if there’s any minor deficiency with the coating or the sealants, or if there’s an issue with the stucco, or any other type of minor deficiency in the exterior of the wall if it’s going to allow water pass that exterior plane of the wall, then it’s getting into the building and it’s a problem.
And in line with that, because it’s a single line of defense and you are relying on the coatings and the sealants, you’re relying heavily on the installation of those coatings and sealants. So, you become more reliant on the workmanship of the applicator. And, you know, when you have a large building and you’re applying thousands of feet of sealants, you know, it’s not unusual that you could have some problems here or there with the application of the sealant. So, that’s probably the major cons. And then, of course, you know, over the long-term, as those coatings and sealants tend to wear out, you know, they’ll obviously need to be maintained in order to keep the wall performing as it was intended.
Chris: Right. I guess in theory in comparing that or contrasting that to the drainage wall, in theory, those interior, if those concealed components, the weather barrier through-wall flashings, those water control details behind the cladding, if those are installed properly from the beginning, in theory, there’s minimal maintenance that could be done and that would be required to be done to those. Still would need to be, as Bret was saying earlier, you’d still need to be replacing sealants and those kinds of things, the exposed details, but the actual water control details should last I don’t want to say forever, but for a long time in that wall cavity versus, you know, constant painting of those or coatings, as you mentioned, on the barrier type walls.
Bret: So, the other con, guys, as well for the barrier wall system is, as I mentioned before, if the window system experiences a storm event that overloads it with respect to water intrusion, then you are going to have water come in. Now, I guess one good way to look at that is that if you do have that type of event, typically that’s kind of an insurance loss type situation. Perhaps you will know that the water comes in, you can address it, you know, it’ll be on the interior and hopefully, you can correct it so that it doesn’t become an issue within the wall.
Another kind of pro and/or con is that, let’s say you do get water behind the paint, which is the barrier, let’s say it’s a mass wall to stucco on block type situation with paint. Now, it’s a barrier wall system. If you get wall into the mass of the wall itself or water into the mass of the wall itself, then it’s gonna want to find its way out. So, if you have a paint on the exterior, it will come through and bubble up the paint. So, you’ll know right away if you have a problem versus if you have a drainage wall system, you may have a water intrusion issue into the wall cavity itself, it’s bypassed the drainage plan.
And if that occurs, typically it’s a wood wall construction, you could have rotten degradation that could be occurring over years and years without you knowing it. So, a lot of people want to say, “Well, I don’t want to put paint on the stucco and block wall because you know, that could have a bubbling of paint.” Well, that’s true but as long as it’s done right you shouldn’t have this scenario. And if it’s not done right, you typically know right away that you’ve got to address the problem.
Chris: Right. For sure. Yeah. Okay, guys, so we’ve talked a lot about the different types of construction and we at GCI travel all over the country looking at different types of projects. Bret, where do we kind of predominantly see these different types of systems that we’re talking about?
Bret: Well, for us in South Florida, you’re typically going to see the stucco on block or stucco on concrete frame buildings. There can be some hybrids, obviously, depending on whether or not it’s a residential versus a commercial structure, but that’s what we’ll typically see in South Florida. And then as you transition up the state, we start to see more and more wood frame construction. So, we transition from barrier wall systems to drainage wall systems.
And going further north, I’m sure it transitions even more and more to wood frame. Obviously, staying away from the coast, but throughout the country you are typically gonna have these days, I think it’s going to be mostly drainage wall systems, wood frame construction. If it’s commercial, perhaps steel frame or concrete frame buildings with metal framing infills, you could have brick veneers, you could have other siding materials throughout the country.
It just depends typically on what part of the country you’re in, what the requirements are for energy efficiency in installation, how things are done in that particular market perhaps. And again, then in South Florida where we’re heavy on the stucco, so. you know, that’s a cheaper and, I guess, faster installation for us in theory versus some parts of the country, it may be more expensive finding material to use, but I have seen it, for example, up in far north as you know, Pennsylvania.
Chris: Sure. And we do go all over on new and forensic assignments. And as you were talking, I was thinking that we’ve got a 26-storey new construction project in Atlanta right now that’s steel frame construction, steel frame infills, and that’s a modular construction of both eaves and stucco. But that’s all drainage wall.
So, certainly, a lot of drainage walls in other parts of the country where we work. And then a kind of very simple barrier type wall that we see all over the country and we haven’t talked about much about would just be precast or tilt-up walls that we see on lots of large commercial buildings all over the country. So, yeah, that’s kind of what we see in our South Florida market where our home base is. We have kind of that unique direct applied stucco that is not used as much in the other parts of the country that we travel to.
Well, I want to thank Bret and Jason for joining me today on the podcast. And I would like to thank everyone for listening to our podcast. We invite you to take a further look at our GCI Consultants services on our website at www.gciconsultants.com. You can also reach us at 877-740-9990 to discuss any of your building envelope needs. Thank you once again, and I look forward to talking with you the next time on our “Everything Building Envelope” podcast.