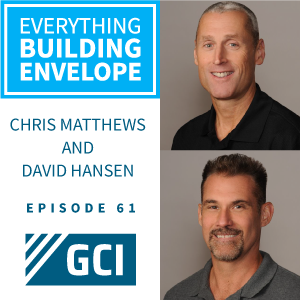
About The Everything Building Envelope Podcast: Everything Building Envelope℠ is a dedicated podcast and video forum for understanding the building envelope. Our podcast series discusses current trends and issues that contractors, developers and building owners have to deal with related to pre and post construction. Our series touches on various topics related to water infiltration, litigation and construction methods related to the building envelope.
https://www.everythingbuildingenvelope.com
*** Subscribe to the show and leave us a Review on ITunes!
Chris: Welcome everyone to our “Everything Building Envelope” podcast. I’m Chris Matthews, VP, and Principal Consultant for GCI Consultants. And I’ll be your host today. I’m excited today to have as my guest, David Hansen, one of our GCI consultants and project managers that I’ve worked with here at GCI for a number of years. And David and I have known each other a lot longer and worked with each other many years in the past.
We’ve got an interesting topic today, and David is gonna talk to you about some of the things he’s learned in his 30 years in the industry, problems, and recommendations he can offer to you. So, David, since this is your first time as a podcast guest, please tell our audience a little bit about yourself, and then we’ll jump right into our topics.
David: Hello. Once again, my name is David Hansen. And I’ve been in the glazing industry for approximately 30 years. I started in the mid-’80s, basically coming in and fabricating, cutting the aluminum stock lengths for curtain wall, window walls, actually screwing the panels together, building the framework. And that’s where I also learned about structural glazing, because most of the systems that we did were actually structurally pumped with sealant. So that’s where I started.
And from there, we did curtain walls, storefronts, window walls. So, I actually began at the ground level, fabricating, installing, building all these frames and units in the shop, and then going out and installing them in the field. From there, I also had the opportunity to work with a lot of really good mechanics, doing custom glasswork, such as mirrors, glass enclosures for very wealthy people, their showers and bathrooms, anything you could think of, custom anything. And that’s really where I got my start.
And then from there, I was promoted, and I became a project manager, actually ordering and overseeing entire projects as far as curtain wall, window wall, anything you could think of with glass and glazing. But the company I was with, they were predominantly in curtain wall and that was their forte. And from there, years later, I actually did get into designing systems along with our structural engineer, being that our structural engineer was very good with making a structurally sound system but had little experience in the field. That was where I came in, because he would come up with a design for a system and I kind of poo-pooed it because I said, no, this is gonna be too hard to install, it’s tough, I mean, you can’t do that.
So, we definitely went back and forth and designed quite a few systems. A lot of them were completely custom systems, curtain wall systems, for buildings. Some were even already standing. I remember one job in particular, the customer had a need where they wanted to redo their whole building, a 15-story building, but they wanted to leave everything they had intact. They wanted to be removed from the interior and they wanted to completely clad from the exterior, which we did. We designed a complete system that just, it’s a curtain wall system that went on the exterior of the building, and after it was all finished, we removed the windows that were 50-plus years old from the inside, and then designed applique on the interior to finish it off.
And from there, I went on to actually going into sales, and then oversight of an entire department, a wing of the company that I was with. So, I guess you could say I’ve pretty much done it all with glass and glazing from the ground up. On my first day I remember pushing a broom. I mean, so yes, I’ve pretty much done it all, anything you could really think of.
Chris: And that’s kind of, we’ve got a mix of people at GCI with different types of experience, but we’ve got some people like David that have done it all and seen it all from the ground up, like he described. And then we’ve got some engineers and architects that their background started from the formal education standpoint.
So it’s a great mix of people that we have here, but you can’t substitute for that experience of being out there, having your hands on it, knowing how it’s put together, knowing how it’s installed, that knowledge, you have to see it and experience it to be able to pass that on to our clients. And so, you talked some, David, about both of the main parts of a glazing system, the aluminum framing components and the glass itself. What’s some of the biggest problems you see with safety glazing, the glass itself, and some of the stuff you’ve worked with?
David: Well, with safety glazing, particularly, say, tempered glass, I know a lot of architects will instantly they’ll put tempered glass on the exterior of the building, and that’s something you want to hold back and not do. You only want to do tempered glass where it’s required by code, because there’s inherent flaws with tempered glass, such as the big elephant in the room always is nickel sulfide. You don’t see too much of it, but that possibility can exist. And it only exists with tempered glazing. It’s a little inclusion, a little flaw, a contaminant in the tempered glass. It’s microscopic. You can’t see it. But if it is there, that piece of tempered glass can be a ticking time bomb. It can blow down the road.
And the only way you can really detect that that really helps with that issue is heat soaking. It’s not a foolproof system, but it does help, but it is costly. So, I mean, whether you decide to do that or not, it’s really what your budget would allow. But that’s really exterior glass as far as tempering. Another problem with exterior tempering, usually, the roll distortion, the tempering roll distortion of tempered glass is usually more predominant than heat strengthened.
And you also want to make sure that your roll distortion is parallel with your horizontal dimension, meaning that when you’re driving by the building, the glass, the tempering wave distortion flows with you, it doesn’t look like you’re in a carnival if, which means your roll distortion is horizontal. If you have it going the opposite way, that roll distortion is vertical, and then when you drive by the building, it will look like a carnival, it looks bad.
But the other thing aside from exterior glazing that you want to be careful of that I have been called out quite a few times here is, say, I have had architects where they’ve designed elegant bathrooms, and they have tempered glass in their showers and bath enclosures. And I know architects, they’re going for the beauty. They want to have a beautiful installation, which means they’d like to have that glass all the way up against their perimeter substrate, whether it’s marble or drywall or whatever it may be. You’ve got to be careful and have the right, you gotta have the right gap there between.
I know a lot of people, they don’t like the look of silicone between the glass and say their marble countertop, but you’ve got to have it there, because when you have expansion and contraction in the glass or in your perimeter substrate, that can actually put too much tension on the glass, and it can actually blow a piece of glass. Another big problem with tempered glass in these same type bath enclosures that people don’t know about is they look at the piece of tempered glass, and usually it have like flat polished edges on the glass, but you’ve got to be very careful that none of these flat polished edges, you’ll see a chip at the corner or the edge of the piece of glass, and that’s a ticking time bomb, because you don’t know whether that chip happened before or after tempering.
If it happened after tempering and it didn’t blow the piece of glass into a thousand little pieces, it can, at any time, explode, and that’s something you really need to be careful of. You’ve got to inspect that piece of glass and make sure that when that’s installed in your bathroom enclosure, there is no damage to any surface, any of the corner areas especially, or along the polished edges, because your glass can blow at any time. It’s a ticking time bomb. And that’s pretty much it that I see for interior glass. You’ve just gotta be careful that you have no flaws in that piece of glass.
Chris: Well, and you covered a lot of ground there and I think that the big takeaway from that is that there are appropriate types of glass for different situations. Like you described, on the exterior of a building, tempered glass is stronger than heat strengthened or annealed glass, but there may be situations where it’s not the best option. And then, as you talked about it in the bathroom, it’s not just the having the right type of glass, but having it installed in a safe manner, so it’s not going to cause problems later on. And I know recently, like you said, we’ve had quite a few projects that you’ve been involved with where these fancy bathroom enclosures, shower enclosures, have some problems because they’ve got the right type of glass, but maybe not the expertise to get it designed and installed in a safe way, which is a way that we can help people.
David: You’re exactly right with that, Chris. You’re exactly right. And another issue that I have noticed is if you have an elegant bathroom enclosure, say a rolling door, they purchase a kit from a manufacturer, and they install it. And if you don’t have good installers, where they really know what they’re doing, they may not adjust that hardware properly, and you’ve got to be careful. I just recently came from a job where they installed it, but they didn’t have all the glass stops set properly, so this glass, this half-inch tempered glass, was actually hitting the wall. And you know as well as I do, when you bang into any kind of hard surface with the edge of a piece of tempered glass, it’s gonna blow. It’s just a matter of time. So, you’ve got to really be careful and install it properly.
Chris: Right. And the tempered glass is obviously much safer than non-heat treated glass, and that’s why the code’s required in these dangerous locations, but people can still be hurt…
David: Oh, definitely.
Chris: …and you want to not only have the right product, but have a good design overall, good functional design, where you’re not gonna have problems. And that’s kind of what we do at GCI, in general, is people usually have pretty good products selected, but we help them get it put in in the right way, so it’s gonna function, so it’s gonna do the job that they hoped it would do, but they might not have the knowledge sometimes to make that happen. So, kind of moving on over into the glazing systems themselves, when you get involved with a new project, what are some of your first steps in reviewing the system, getting familiar with it, helping our customers to get their glazing systems installed and functioning right?
David: Well, the first thing I like to do is pull up all the documents on the system, actually pull up the glazing system shop drawings to see what they drew, and then pull up the product approval for that system to see structurally what it makes, the tolerances that are built into the system, meaning, what is that caulk joint? Say, like if it’s a structural glaze system, a lot of times they’re built-in, say, where you’re able to have as much as a half-inch or five-eighths caulk joint. Anything more than that may not be approved. If it is larger than that, a lot of times you’ll need larger anchors, longer anchors, anchors, more of them. You’ve just got to really look at all of your information before you go out and look at a glazing system.
Because unlike a, so like an aluminum system or a louver, that’s one item, that’s one item that goes into that clad system. With a glazing system, I guess you could compare it to like buying a boat. Yes, you’re buying this glazing system, but there may be 50 different itemized products that go into that system, and you want to make sure that they’re installing that exactly as it’s supposed to be installed per the engineering and per the product NOA. Because I have witnessed recently where the shop drawings and the NOA say one thing, but you go out to the field and you see what they’re doing, and they will sometimes substitute materials for that glazing system. And that’s not right, because that can lead to problems down the road.
Chris: Sure. And we see that on the litigation end of what we do quite often, in that what was shown in the drawings on a project might not be, on a quick look, it looks like what’s shown in the drawings, but when you start digging in, there’s parts and pieces that have been substituted, the wrong thing used, and then you’ve got performance issues down the road because, like you said, with a boat or a car or anything else, it’s designed to operate properly with these exact parts. And when you start substituting things, maybe not even to save money, just because this was on hand and this wasn’t or whatever, people are rushed during construction, trying to get it done quickly, you know, things get overlooked or put in there that shouldn’t be, and then we end up seeing it later on that, you know, those kind of things result in a lot of problems for people.
David: Oh, sure. Yeah, you see that all the time. You see it all the time, whether it’s products, pieces, parts that get substituted, but, and also a big thing is when, say, like, a gasket is supposed to be installed a certain way and it doesn’t, it’s backwards. I mean, there’s always installer error, and you see it all the time. It’s just, you know, they’re people, people installing these systems, and you need systems that are very user-friendly, where somebody can come to work and he’s in a bad mood or in a hurry to get home. It doesn’t take a huge amount of knowledge to install a simple system the right way. But if you have a labor-intensive system, you’ve really gotta be careful. You’ve got to have top-notch installers, along with supervision for these installers, and if you don’t have it, mistakes are made. It happens all the time.
Chris: Sure, sure. So, I think I know your answer to this one, but what’s your opinion on wood bucks in glazing systems, wood bucks at the perimeters of window openings, how those get sealed properly, integrated with the system, everything related to that?
David: You know, that’s a really good question. I’m glad you thought of that. You know, I remember 30 years ago, 20 years ago, installing systems where I thought it was a great idea to install, you know, a lot of times you have a, say, a square perimeter opening with cast-in-place concrete or even block to put polyurethane, Volcom with wood bucks right up against the perimeter of the opening, and install your glazing system into that.
I’ve heard it so many times when I see details like this, where GCI does not recommend wood bucking or any organic materials at the opening, but I remember, 20, 30 years ago, this is common. It was very common in the field to just take a pressure-treated wood buck, polyurethane seal it right to the perimeter of the opening, nail it in, and then install your glazing system. And I thought that was okay, but then, when I came to GCI and I did see that it was not part of our recommendations, and we recommended a fluid-applied waterproofing at the perimeter, I thought, wow, do you really need that? I mean, I don’t know, I’ve just been, I know that it’s been done this way for so long. What do you really need?
And then I remember when I first started at GCI, doing a few water tests with our testing techs, and actually seeing a system that was installed without waterproofing at the perimeter. And yes, that glazing system, whether it’s a single square frame and a cast in place or a block opening, you think, okay, it’s sealed in, you’re good. No, but you’re not good. I mean, it was kind of a big eye-opener for me when I actually saw the concrete leaking. It was pulling water in.
The glazing system itself worked fine, but the concrete was leaking water, it was actually flooding to the inside. So, I mean, unless you have that weather barrier on the exterior, the water will come in. I mean, I was amazed when I saw that. I really was. So that was a good eye-opener for me here at GCI. So now, what we do, we recommend a fluid applied waterproofing at the exterior of the opening, the whole perimeter opening, and extending onto the vertical face, approximately an inch or two, depending upon what type of cladding system’s out there. That will keep the water out of the system. So, it’s very important, which was a big eye-opener.
Chris: Sure, yeah. And, you know, you’ve got a tested product, if we’re talking about a window that comes from the factory, fully manufactured, you’ve got a tested product that most likely is gonna perform well. But then, as you say, if you install it and seal it to something around it that’s not gonna keep the water out, it doesn’t really matter how good that window is. And, you know, I’ve had that same experience as you. Once you see that water test done, with that negative pressure on the inside, pulling that water in right around that window, through those wood bucks, you understand right away that, you know, something better has gotta be done.
And this old, you know, they call it, like, the “Florida flange,” we see it still a lot in South Florida, with the wood buck block wall, with direct-applied stucco, wood bucks around it, and then that Florida flange back-bedded up against those bucks, and if you don’t have those bucks waterproofed, you’re gonna have a problem, and it’s just one of those things that who knows how it ever even started. Like, just like you said, they’ve been doing it that way for probably longer than you and I have been doing this, 50 years, they’ve probably been doing that, or more, but nobody can remember who was the genius who thought this was a great idea in the beginning.
David: Yeah. Yeah, I know. I mean, I’ve heard it so many times, it’s actually kind of funny. It’s like, “I’ve been doing it this way 30 years,” and I’m sitting here thinking, well, you know what? Up until probably about five, six years ago, I might’ve kind of agreed with you, but now that I see what a water test, and whenever water’s pulled through that building, just to see what it does, it’s not the right way to do it. It’s definitely not. And I’ve even had guys come up to me and say, “You know what? I sealed those wood bucks to the block with Volcom and I also ran an exterior polyurethane bead, and that’s how we ran, and we ran our stucco right up to the face of those bucks. And that’s the way I’ve been doing it 30 years, and by cracky, that’s the best way to do it.” And I remember, well, you know what? Yeah, I thought that too, but it’s not. It’s definitely not.
Chris: Well, and even though some of us here at GCI are old guys, we try to keep learning, right? You don’t just say, “Okay, well, we’ve been doing it this way for 30 years and, you know, there’s nothing new out there, there’s no better way.” We try not to make our clients a guinea pig either, so it’s a little bit of a balancing act, you know. There’s new stuff, new products, new ideas all the time. We try to give them things that are proven, that we’ve got experience with and we know will work, but we also try to take advantage of advancements, right? You don’t just, you know, we’re not still living in caves either. So, you try to balance that out as far as “the way we’ve always done things” with “there might be some better ways to do it too.”
Well, and you touched some on the sealants. You were talking about the polyurethane sealants that are installed around those wood bucks, but kind of talk to us some about the different types of sealants that you see used, and what you recommend for different applications, and why people can’t just go down to the Home Depot or the hardware store and buy whatever they see in a tube there?
David: Well, I have seen people go down to the local hardware store and use that, and then two weeks later you wonder why it’s pulling away from your aluminum framing. I mean, there’s a reason why that these sealants are a little more expensive. You have manufacturer support, and you’ve got that proven track record that we were just speaking of. I mean, they’re always trying to improve their sealants. I mean, so, basically, the biggest sealant differences that I see or being used out in the field are polyurethane and silicones. And polyurethanes are good for their chosen application. Whenever the sun, if you have any application where the sun’s not gonna kill it, because polyurethane will degrade pretty quick in the sun.
Now, I know there’s a lot of installers where building owners, they don’t want to fork out the money, because it is, silicones are a little more expensive. They don’t want to fork out the money with the silicone at the exterior of their glazing system, so they’ll want to use a polyurethane. Well, I always say, yes, of course, you can use the polyurethane, but if it’s gonna be exposed to the sun, you realize that you’re only gonna get a few years use out of this sealant. I mean, it is better if you, say, paint the polyurethane, which, that’s another good application of the polyurethane. You can paint it, and the paint will stick to it, and you will get probably a few more years out of that. But most polyurethane manufacturers, at best you’re ever gonna see is a five-year warranty.
With silicone, if you actually have a good, properly formed silicone sealant joint in the field, you can get a 20-year warranty. You can get a 20-year warranty, which is great. I mean, there’s a big, huge difference between silicones and polyurethane. Like I said, 30 years ago when I was installing glazing systems using silicones, that’s mainly all that we used with the exterior, storefronts, curtain walls. I’ve gone back 30 years later, even though they gave, the manufacturer would provide a 20-year warranty, I’ve gone back 30 years after installing this building, and you look at the sealants, and you start poking at the silicone bead. It looks like it was just installed yesterday. It’s amazing. I mean, the ultraviolet does not bother the silicone. It’s amazing what I’ve seen. But, the polyurethane, on the other hand, it will degrade with the sun. But once again, if it’s the right application, where it’s not in the sun, or it’s in a wet condition, the polyurethane is better, where you’ve got to keep most all silicones out of any kind of standing water, because it will degrade it within a very short time.
So, basically the bottom line is, yes, there’s a cost difference between the polyurethane and silicone, but, I mean, as far as a maintenance problem, maintenance down the road, silicone, you can put it on, and if it’s put down properly, your substrates are tested before they’re put down so you know exactly what cleaners to use, what primers to use. And once they’re installed in their proper hourglass shape, they’ll be there forever. They’ll just last. I mean, I’ve seen them. Thirty years, and they look still brand new. Silicone is, it’s a beautiful thing. But once again, it depends upon your installation. It depends upon where you’re installing these materials.
Chris: And like the glass, we talked about in the beginning, and a appropriate product for the application that you have, we’re big believers in silicone anywhere that it’s exposed to the UV. And what we try to explain to our clients is, you know, kind of looking at it with a little longer range view, in that the polyurethanes may be a little less expensive up front, but how much are you really saving if you’re gonna own this building for any extended period of time? You know, the silicone could still be there 30 years from now, and you might have had to replace that polyurethane sealant five or six times in that 30 years, so, you know.
David: I’ve seen it, going out to the job site where polyurethanes were put down, and say, six, seven years later, where they’re starting to crack up and pull away, and actually, building maintenance people will go out there and they will, they’ll go to the local store and buy whatever they can on the shelf and just go out there and just start adding to it. You always see that, where they’re just dabbing more sealant into the opening. It’s a maintenance deal. It’s a maintenance problem, and it depends upon how long you want to have a maintenance-free building.
Chris: Exactly. Right, right. Well, you can see from our conversation today that David’s got a lot of knowledge about a lot of products and systems, especially exterior glazing systems and how they are intended to function and how to keep them functioning right, get them installed in the beginning so they function right. And we would always be willing to talk to you about any projects and concerns that you may have. And he’s a great resource, and I thank him for joining us on our podcast today. And thank you to our audience for listening. We invite you to take a further look at our GCI Consultants services on our website at www.gciconsultants.com. And you can also reach out to us at
877-740-9990, to discuss any of your building envelope needs. Thank you again, and I look forward to talking with you the next time on our “Everything Building Envelope” podcast.