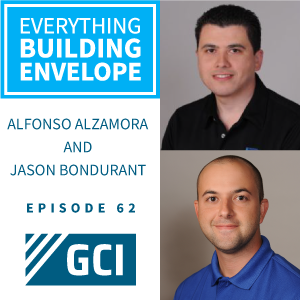
About The Everything Building Envelope Podcast: Everything Building Envelope℠ is a dedicated podcast and video forum for understanding the building envelope. Our podcast series discusses current trends and issues that contractors, developers and building owners have to deal with related to pre and post construction. Our series touches on various topics related to water infiltration, litigation and construction methods related to the building envelope.
https://www.everythingbuildingenvelope.com
*** Subscribe to the show and leave us a Review on ITunes!
Alfonso: Welcome everyone to our Everything Building Envelope podcast. I am Alfonso Alzamora, Vice President and Principal with GCI Consultants and I will be your host today. I am really excited today to have as our guest, one of our engineers that I work with here at GCI Consultants and the guest, Jason Bondurant. We have got a really interesting topic to share with you today, which is all about pool decks and plaza decks waterproofing. So Jason, since you are a repeat guest, let’s just jump right into talking about plaza decks and pool decks waterproofing. So why don’t you tell us a little bit about the typical components that we find in these types of systems?
Jason: So when we talk about plaza deck waterproofing system, typically what we’re referring to is a waterproofing membrane that’s installed on the structural deck, typically a concrete deck, and typically these types of systems are installed over occupied space where it’s essentially functioning as a roof or occasionally we’ll see them installed over parking garages or other types of spaces.
And usually, these types of membranes will be covered by some type of overburden. So, it’ll be concealed in the finished assembly. You won’t actually see the waterproofing membrane. These areas are somewhat different than roofing systems in that they’re also intended for vehicular or pedestrian traffic or used as greenscape or planter areas. And because of that, these types of systems are exposed to some of the harshest conditions. And one of the things that really makes these systems challenging is that they do require a high level of coordination between the waterproofing and the adjacent envelope systems.
So the typical components kind of from top to bottom would be at the top you’d have some type of wearing surface which could be bricks, it could be pavers, precast flab or exposed aggregate. And then beneath that, you’ll have some type of fill where it may be a topping slab, it may be sand, or it may be a mortar setting bed. And then beneath that, you would have some type of drainage layer. Typically, these days we would see a prefabricated drainage mat, but it could also be a layer of gravel or some kind of drainage medium that’ll allow the water to flow easily. And then beneath that, we would have the waterproofing membrane and the protection, of course, which is on the structural deck.
Alfonso: Right. And I’m sure you agree that, you know, as with any waterproofing system that drainage is a critical part of the assembly. So why don’t you tell us a little bit more about the drainage layer?
Jason: Yeah. So the drainage, like you said, with any waterproofing or roofing system, it’s the most critical aspect. And for these types of protective membrane waterproofing systems, there are some unique aspects to the drainage that we don’t have to be concerned about with a typical roofing system. So, with these protected membrane systems, they need to be designed so that you have the expectation that water is going to get all the way down to the waterproof membrane level, which is beneath the overburden. So, the deck needs to have a bi-level drainage system that’ll allow water to enter the drain from the waterproof level which is beneath all the overburden and also from the wearing surface level.
And it requires special detailing and typically what ends up happening is they’ll wrap the drain with some type of filter fabric and they’ll install gravel around the drain to avoid blocking the drain bowl at the membrane level and ensuring that water can get into the drain there.
It’s worth noting that water that does collect on the membrane and pond on the membrane can cause problems over the long-term, including de-bonding of the waterproofing membrane, cracking of topping slab, deterioration of insulation, leaks to the interior. So, drainage is something that should not be overlooked and it’s critical that the drainage is provided at both the wearing surface and the waterproofing membrane level.
Florida building code does require that the deck has a quarter inch per foot slope. Sometimes with these types of decks, we see that they’re not quite getting that and we’ve dealt with some manufacturers that will warranty the waterproofing system even on a flat deck with the understanding that there will be some ponding water there but the building code does require that the deck does slope to drain.
Alfonso: So how does that slope requirement converts, you know, to a typical roofing system requirement?
Jason: Well, the quarter inch per foot would be the same for roofing. So I guess the main difference is that a plaza deck waterproofing system like this is typically designed to withstand some amount of hydrostatic pressure, unlike a roof. So, with these types of systems, even if the drainage is not ideal, let’s say, they can oftentimes still perform. But, you know, and that’s why I think some of the manufacturers will allow less than the minimum code required slope, but it is required in the building code. So, we do have to make sure of that.
Alfonso: Right. And I guess Jason also, like you were saying since, you know, typically this type of application would be, you know, like an amenity deck or a pool deck or in a garage, sometimes, you know, particularly with amenity like some pool decks, you want to have that kind of level or flat surface versus a roof area where you have other means of obtaining the required slope. Typically, we see them use, you know, tapered insulation or you have, you know, lightweight insulated concrete that will help you have that required slope at that roofing membrane. But with this type of assembly, you were saying that, you know, we don’t see that that often. Right?
Jason: Yeah. That’s right. And it’s possible to have insulation either on top of or beneath the membrane, but typically in South Florida here, it’s not very common.
Alfonso: Right. And you mentioned particularly in South Florida, if they’re using insulation as far as their assembly that is gonna need to be incorporated into their [inaudible 00:07:34] approval documents, NOAs, and all their certification testing. So Jason, how do we go about specifying, you know, a particular waterproofing system for these types of application, and what would be the common types of waterproofing systems that you see for these types of applications?
Jason: Well, there’s a lot of different considerations that we need to keep in mind, and every project is going to be unique. I would say that the most common type of system that we see and the one that we most often recommend is a hot rubberized asphalt reinforced waterproofing membrane. And typically, it’ll have a modified bitumen cap sheet or a protection layer on top of it. So that’s the most common.
Another one that we’ll see often is a torch-applied modified bitumen membrane two or three-ply system. This type of a system, just to give you an example of the different considerations that go into mind, we might want to use a torch-applied system on a project because maybe getting a melter to melt the hot asphalt onto the roof of, you know, a 50 story building is not realistic with this particular project. So we may want to use like a torch applied type of a system.
The reason why the torch applied is modified bitumen system, is sometimes used as the next best option, is because it does still have some redundancy being that it’s multiple different layers. Another common one that we’re seeing more of recently is a cold liquid-applied reinforced membrane like a PMMA waterproofing membrane. These have some advantages in that being that they’re cold-applied they’re safer. There’s no open flame or hot asphalt that you’re dealing with. Typically they’ll cure very quickly. And then another one that we do see occasionally is a single-ply waterproofing membrane, like a TPO or a PVC membrane.
Alfonso: Okay. So that’s very interesting what you just said because… So, in addition to the considerations as far as the actual performance of the different type of systems and, you know, different types of waterproofing membranes, the other thing that comes into play with all of this is the actual job site conditions and site logistics. As far as, you know, like you were saying, maybe it is not possible to carry the melter to, you know, whatever this pool deck is, so many, feet high on the building. So that’s obviously something important to consider as well, putting that theory along with how you can actually achieve this in a productive way. So that’s interesting, Jason.
And then you mentioned also, you know, these cold liquid-applied systems. Sounds like it’s, you know, more of an easier installation as far as, you know, the labor goes. So, is that your experience as well? Is that typically that type of installation would be completed maybe faster and, you know, with less labor than you would see when you have like a torch apply mud bit system?
Jason: Yeah, I think so. I think probably it can be applied faster and it cures faster.
Alfonso: Okay. So, are there any special considerations with the planter areas?
Jason: Yeah. So, like we were talking about with just the system in general, with the planter, a drainage is the most important aspect. So typically, the drains in a planter what we want to do is we want to design the drain so that water can get into the drain the full height of the planter.
So typically, what we like to see is we have our drain bowl that’s set in the structural deck at the bottom of the planter. And then, attached to the grate over the dream bowl, we would have some type of perforated pipe. Usually, it would be a PVC pipe that has holes drilled into it and that pipe would extend up to the top finished surface of the planter basically at grade in the planter. And then there would be another drain inlet at the top of that PVC pipe.
And then this whole assembly would get wrapped in a filter fabric and surrounded by gravel so that the planter has good drainage from the top at grade level all the way down to the waterproofing membrane level. And then obviously, like we mentioned before, it would need to have a drainage mat which gets installed above the waterproofing membrane, which would carry any water that gets down to the waterproof level to the drain and prevent any water from standing on top of the waterproofing.
And then, one thing that is unique to the planter areas is they would typically require some type of root barrier. And, you know, we’ve seen many projects where we’ve dug up planters that are leaking and we find that the roots inside the planter have just born holes all through the waterproof membrane. So the root barrier is something that’s really critical inside the planter as well.
Alfonso: Exactly. And so Jason, so after you have all these components installed and, you know, the assembly before you put all the overburden materials, I mean, is there any way to check or verify the integrity of the membrane before moving forward to basically cover [inaudible 00:13:46]?
Jason: Yes. And actually, it’s required to check it before it gets covered by anything. The building code requires that you do some type of integrity testing to check that there are no leaks in the finished waterproofing.
Most commonly what we’ll see is just the standard flood test. There’s an ASTM standard for flood testing horizontal waterproofing installations. And basically, what they do is they’ll plug the drain bowl and they’ll fill up the deck with about two inches of water or so on the waterproofing. This is before any overburden gets installed. And then they’ll leave that water on the waterproofing for 24 to 48 hours. And then after the test, they’ll check the underside to see if it’s leaking anywhere. And if it’s leaking, then, you know, obviously repairs will need to be made and then it will need to be tested again to confirm that it’s not leaking.
One of the other newer ways that we’re seeing people testing waterproofing installations is the electronic leak detection which is basically they will install wires around the perimeter of the deck and mist the deck with water and then they’ll walk every square foot of the deck with the testing company. And essentially, they have these probes that they’ll stick into the water onto the membrane and if there’s any breach in the membrane, they’ll be able to tell. And it’s actually quite impressive to see them do. They can really pinpoint the exact locations of breaches using this kind of a method.
There are some limitations in that they typically don’t test the drain bowl flashing because the metal of the drain will interfere with the test. So actually on some jobs, we see them do both the flood testing and the electronic vector mapping just because you can never do too much testing with these types of systems because the fact is that once the deck is done and it’s signed off and the waterproofing is okay, then they’re gonna cover this with sometimes a topping slab, sometimes pavers, planting soil. And in the event of a problem in the future, all these things would have to come off the deck in order to fix the problem. And so, you know, that’s why this type of testing is required and that’s why we definitely don’t want to ever cut any corners when it comes to testing these.
Alfonso: Right. Right. So that’s very interesting because construction, you know, we don’t really associate a lot of technology in that way with construction job sites. So, you know, the first test you were describing the standard flood test, you know, it’s a very simple, basic test, something that you would definitely think about when you’re thinking about a construction job and very effective from what you were describing. But it’s very interesting to see that there’s other technologies that incorporate different elements that can also allow us to verify, you know, the integrity of these types of membranes in a different way. And like you were saying, this is critical since this thing is pretty much gonna get buried with all these different overburdened materials and components that you have been talking about.
So, up to now, I guess we have been describing how you should go about designing or installing waterproofing system in a plaza deck or amenity deck application starting with a new construction approach and trying to make sure that everything is done in a right way and then properly [inaudible 00:17:52] as you were describing just now. But what about those existing buildings that you get called on where they have actually problems with these plaza deck installations or pool deck installations and like you were saying everything is already covered up by all the overburden materials. So, what are some of the typical problems you see there on those existing buildings and how do you go about investigating the source of the problem?
Jason: Well, when it comes to investigating any type of a leak whether that be with these types of waterproofing systems or glazing systems or roofing systems, we typically want to do some type of water testing. And I think that that’s a good starting point with these types of decks because the fact is that when they’re complete, we can’t actually see the waterproofing. We’re typically looking at pavers or we’re looking at a planter.
And so, what I typically like to do is start with some amount of water testing in the general area above where the leak is reported. And then ideally you would test a certain area at a time. So, you try to isolate one thing at a time with your test, keeping in mind that it might take hours for water to actually make its way all the way to the interior of the building. And so, you just kind of have to have a methodical approach with your testing.
And usually, once I’m able to recreate the leak and we have a general idea of where the leak is coming from, at least looking at a plan of the deck, then it’s almost always you’ll require some amount of intrusive or destructive testing to investigate the leak. So that might mean chipping up a topping slab. It might mean digging up a planter, but because the waterproofing is concealed under these overburdens, it usually is required to do some amount of destructive or intrusive testing.
And then usually what we do is once we’re able to pinpoint the exact source and we’re able to see the membrane and find out what’s going on, we’ll have the contractor do whatever repair is necessary. And then we’ll test it again before we cover everything back up just to ensure that we found the source of the problem.
So, some of the typical issues that we see when we’re investigating these types of systems, I would say probably the most common one is failure to tie the waterproofing system on the deck into the other envelope system. So usually that means tying into the flashing at the base of the wall tying into the weather barrier on the exterior wall or in, you know, most commonly in South Florida where we don’t have a weather barrier tying into the stucco.
So, one of the most common issues that I see, as an example is, it may be a renovation. Maybe it’s an older building and they’ve replaced the waterproofing system on a pool deck and the contractor doesn’t bring the waterproofing up high enough on the wall, the flashing to where now you’re left with a void between the top of the waterproof flashing and the stucco on the exterior wall. Typically, we like to have some kind of overlap there to make sure that the envelope is continuous.
And we see similar problems at door thresholds, the window openings where the waterproofing might stop just in front of a door or window opening and it’s not fully integrated with the perimeter sealant on the window or door. That’s another really common one.
I would say another common problem is with any of these systems that are coatings and with any coating in general, the most critical aspect of that coating is ensuring that it’s the proper thickness. So, we’ve been involved in some projects where we’ve seen that the coating was far too thin. And then we’ve also been involved in projects where the coating has actually been too thick. I think a lot of people wouldn’t expect that the coating could be too thick, but actually coating becomes too thick it can cause problems with the exterior part of the coating may skin over and cure faster than the interior part of it. And what we’ve seen happen before is that exterior side of the coating will skin over and that interior side will continue to cure and let-off gases and that can cause blistering in the coating if it’s installed too thick.
Another really common one just to mention one more thing, if I have to pick a third one, is penetrations in the waterproofing. And a really common problem that we see is after these waterproofing systems are installed and they’re tested, we have other trades coming in, electricians, one of the most guilty parties in this, and they’ll put holes through the deck or through the waterproofing and won’t seal them properly. And so that’s a common place that we find leaks.
And then also another common problem with penetrations is the penetrations being clustered too closely together, which prevents the waterproofing contractor from properly detailing the waterproofing around each individual penetration. So, I would say those are some of the more common things that I’ve seen.
Alfonso: Right. And I think those are all great examples of the kind of problems we see when some of these buildings that we’re called upon to investigate because they have issues. And like you were saying earlier coordination here among the different trades is critical because like you mentioned penetrations and also the interface between, you know, different conditions which are typically being worked by different trades. And we see a lot of problems there just like you described, you know, if there is no proper coordination and the electrician is just walking through the waterproofing and putting holes on it, that’s obviously gonna result in a problem.
And in the same way, in all of these transitions, one that I can think of that we see often is the connection or the transition between your pool deck waterproofing where it ties in into the actual pool structure or, you know, typically you have a gutter at the perimeter of the pool and maybe your waterproofing contractors that are doing the deck is different from the guy that is actually doing the waterproofing at the pool structure. So, there’s right there a point which, you know, they may not be talking to each other and then you have a gap on your waterproofing. Have you seen anything like that as well, Jason?
Jason: Well, yeah. Absolutely. And something else that you just reminded me of too, which we didn’t get the chance to talk about, but expansion joints are, you know…I’m sure anybody that has dealt with any of these types of systems before knows that these are one of the most common areas that are gonna leak. And each manufacturer will have a slightly different way of treating expansion joints. I think you could probably do a whole podcast in itself on expansion joints.
One of the things that I’ll just say about that is this, and I guess this is more to the architects out there, but use common sense when it comes to expansion joints. You know, try not to put a fountain over top of an expansion joint. If you can, get the expansion joint off the deck a little bit so that it can shed water and you don’t have any chance of any ponding water on top of it.
So, I think, you know, just some of these basic kinds of principles could go a long way when dealing with expansion joints. But like I said, we could do a whole other podcast just on that alone.
Alfonso: Exactly. I think we’re actually running out of time here. So, I guess we have to come to a stopping point. I would like to thank all our listeners for growing our podcast and tuning in. Thank you again for listening today. We also invite you to take a further look at our GCI Consultants services on our website at www.gciconsultants.com or you can reach us at 877-740-9990 to discuss any of your building envelope needs. Thank you once again, and I look forward to talking with you the next time on our Everything Building Envelope podcast.