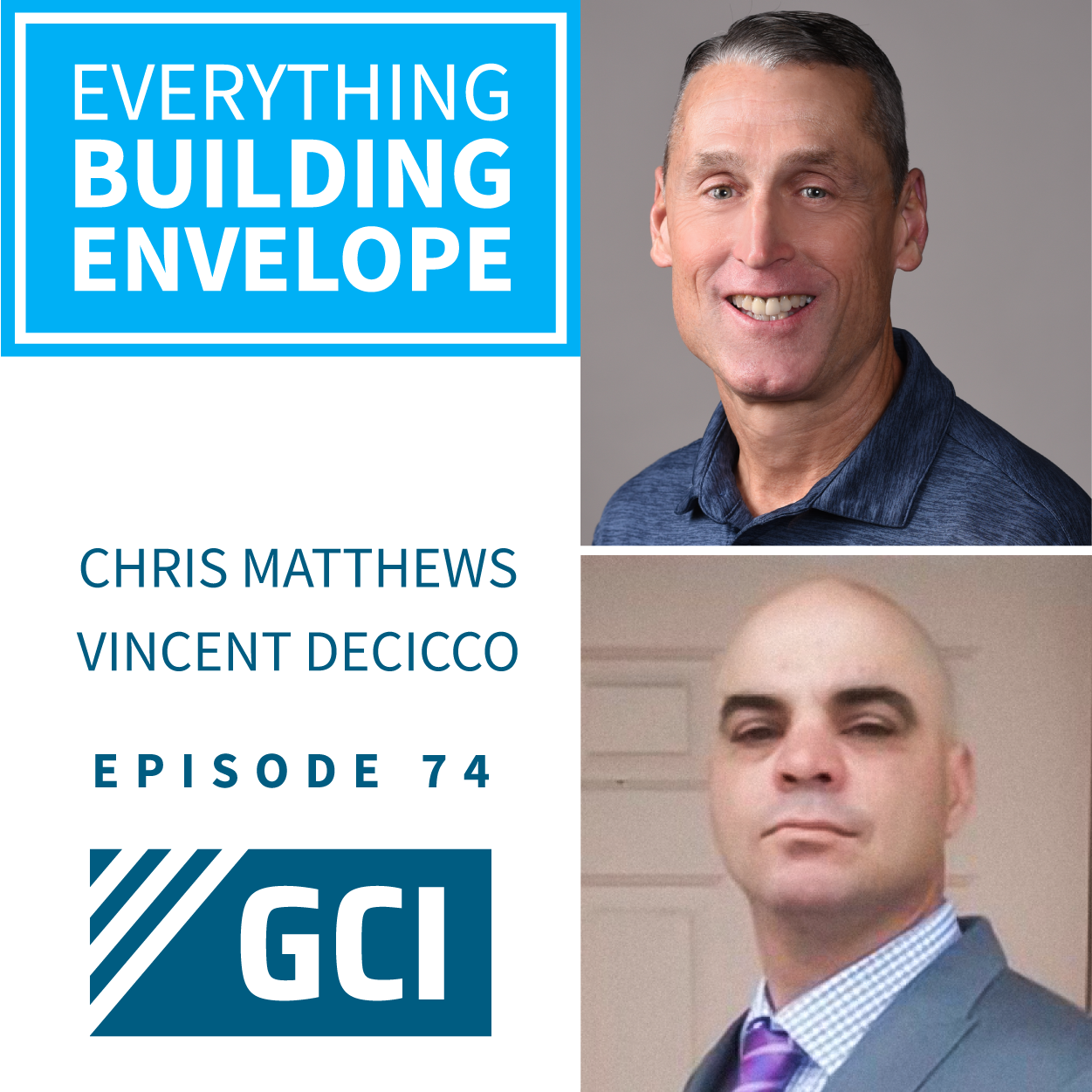
In this episode, Chris Matthews, President and Principal for GCI Consultants, speaks with Vincent Decicco, owner of Full Frame Virtual Reality. They discuss hurricane preparedness, documentation of structure conditions prior to an event, and what people can do as policyholders to protect themselves and document their structures and their possessions.
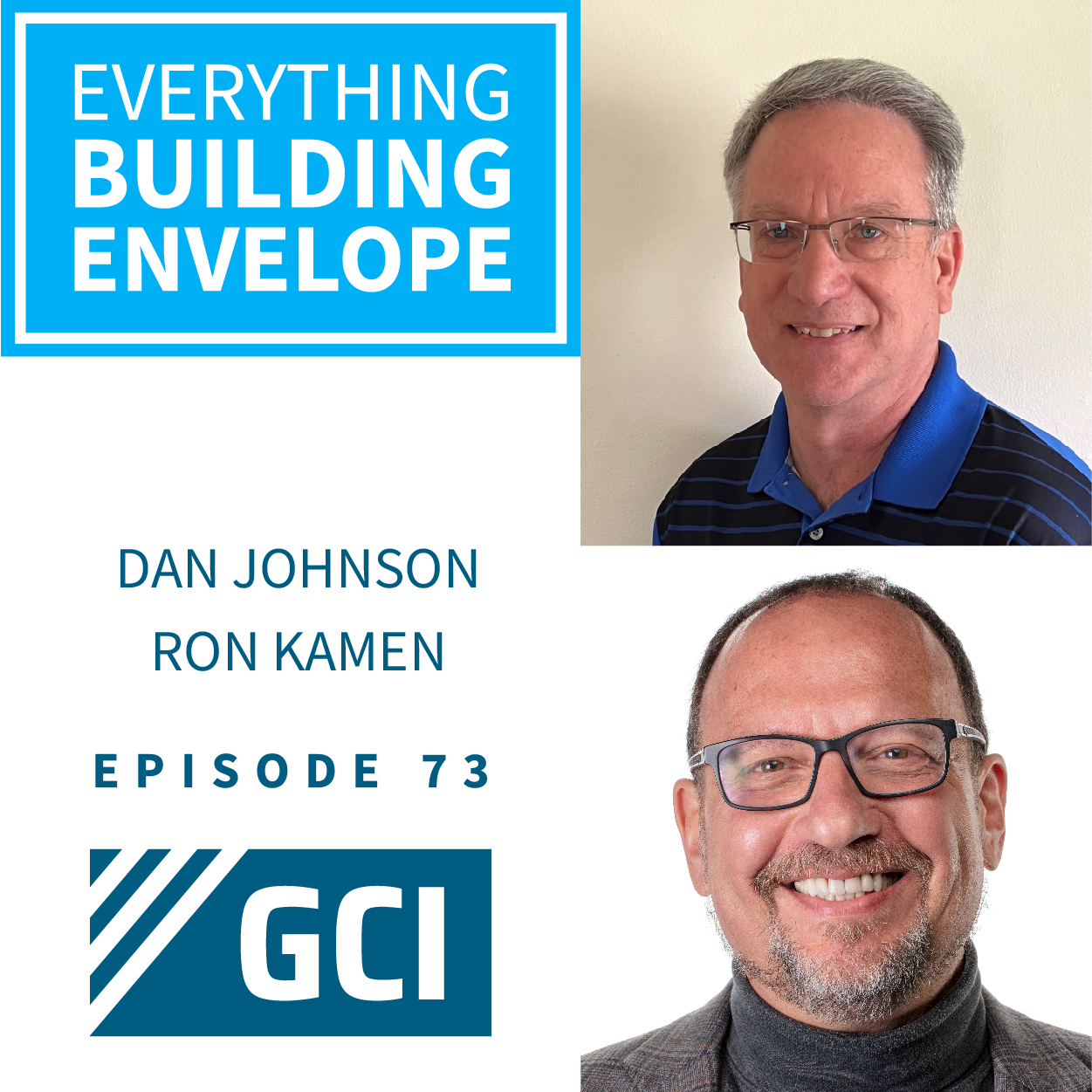
Clean Energy and Affordable Clean Energy Systems
(Released on July 21)In this episode, Clean Energy and Affordable Clean Energy Systems, Dan Johnson, senior consultant for GCI Consultants talks with Ron Kamen, with EarthKind Energy Consulting. They discuss, “Clean Energy and Affordable Clean Energy Systems.”
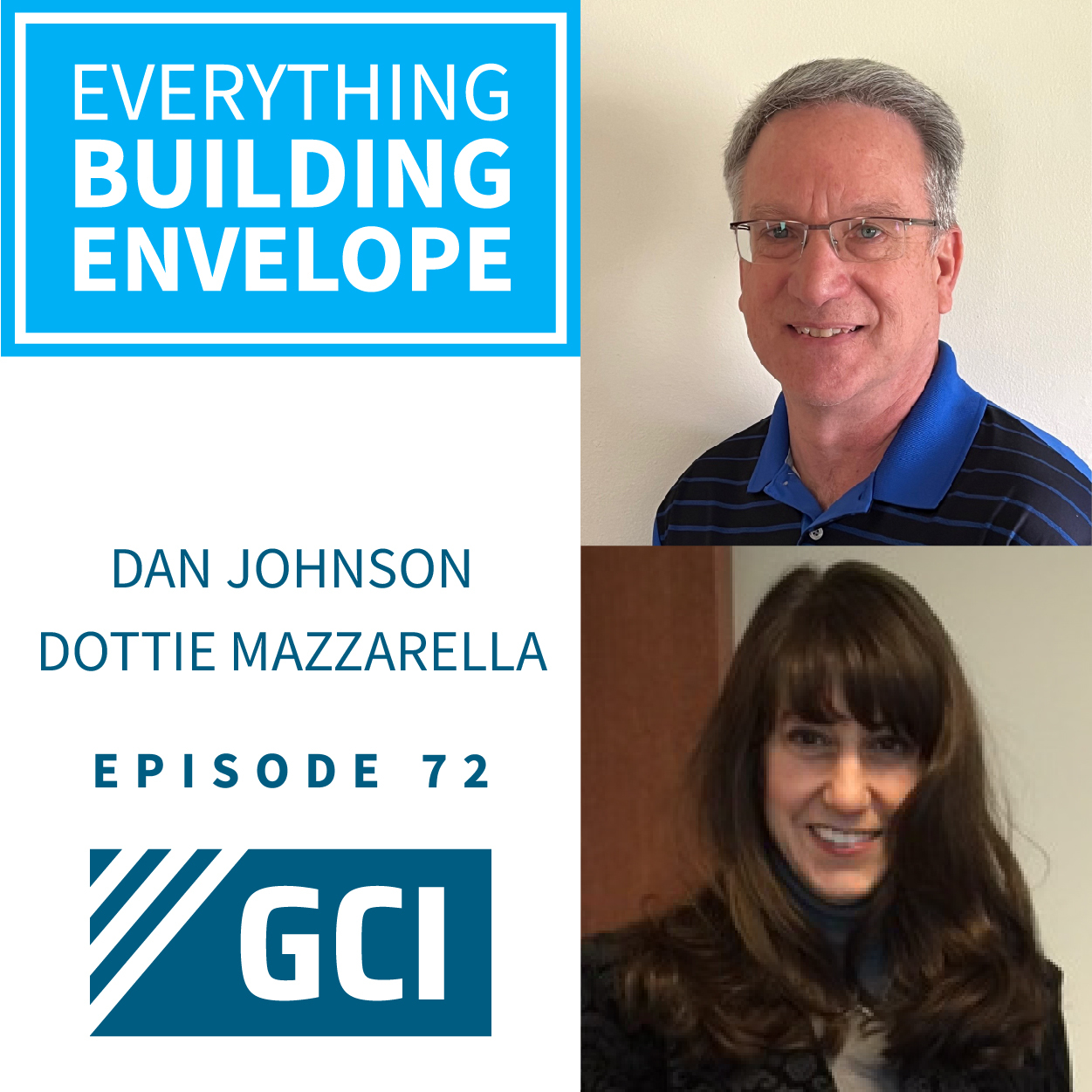
International Property Maintenance Codes
(Released on July 9)Listen as, Dan Johnson, Senior Consultant for GCI Consultants speaks with Dottie Mazzarella, Vice President of Government Relations for the International Code Council. They discuss the international building code development and the International Property Maintenance Codes.
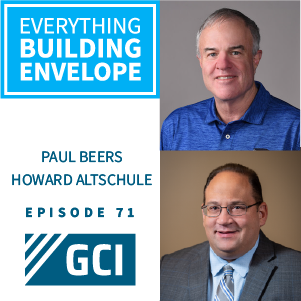
Weather and Scientific Evidence Around Various Disasters
(Released on November 29)Listen as, Paul Beers, CEO and Managing Member for GCI Consultants speaks Howard Altschule, CEO, Certified Consulting Meteorologist at Forensic Weather Consultants, CE Instructor. They will discuss various weather disasters and their scientific evidence.
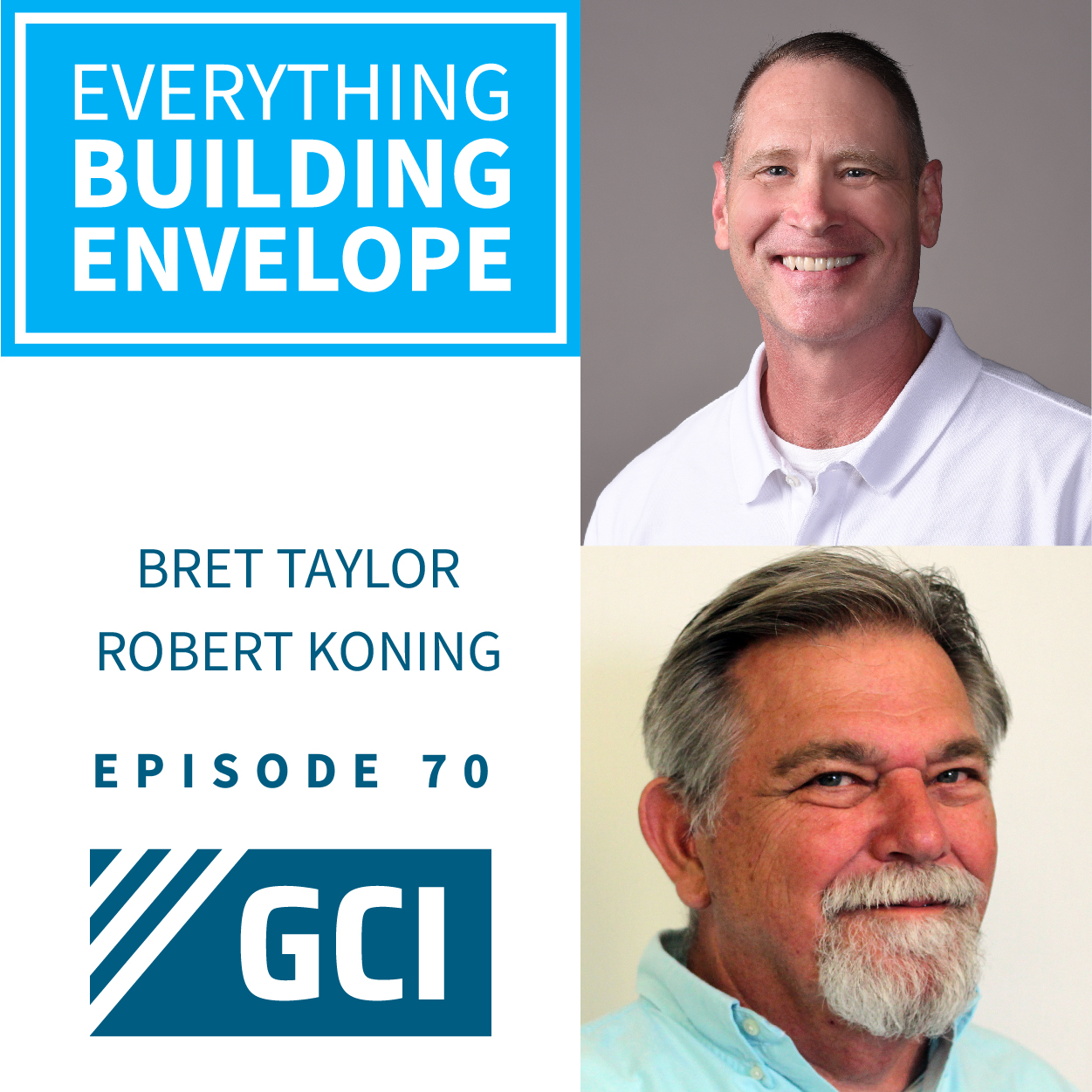
The State of Stucco
(Released on September 16)In this episode, Bret Taylor, Professional Engineer, and Sr. Consultant for GCI Consultants talks Robert Koning Director of Contractors Institute, Stucco Institute, Building Officials Institute, and he’s also the developer of the Sealed Cladding System. They’ll discuss the state of stucco, the history of the Stucco industry, and the future that lies ahead for stucco.
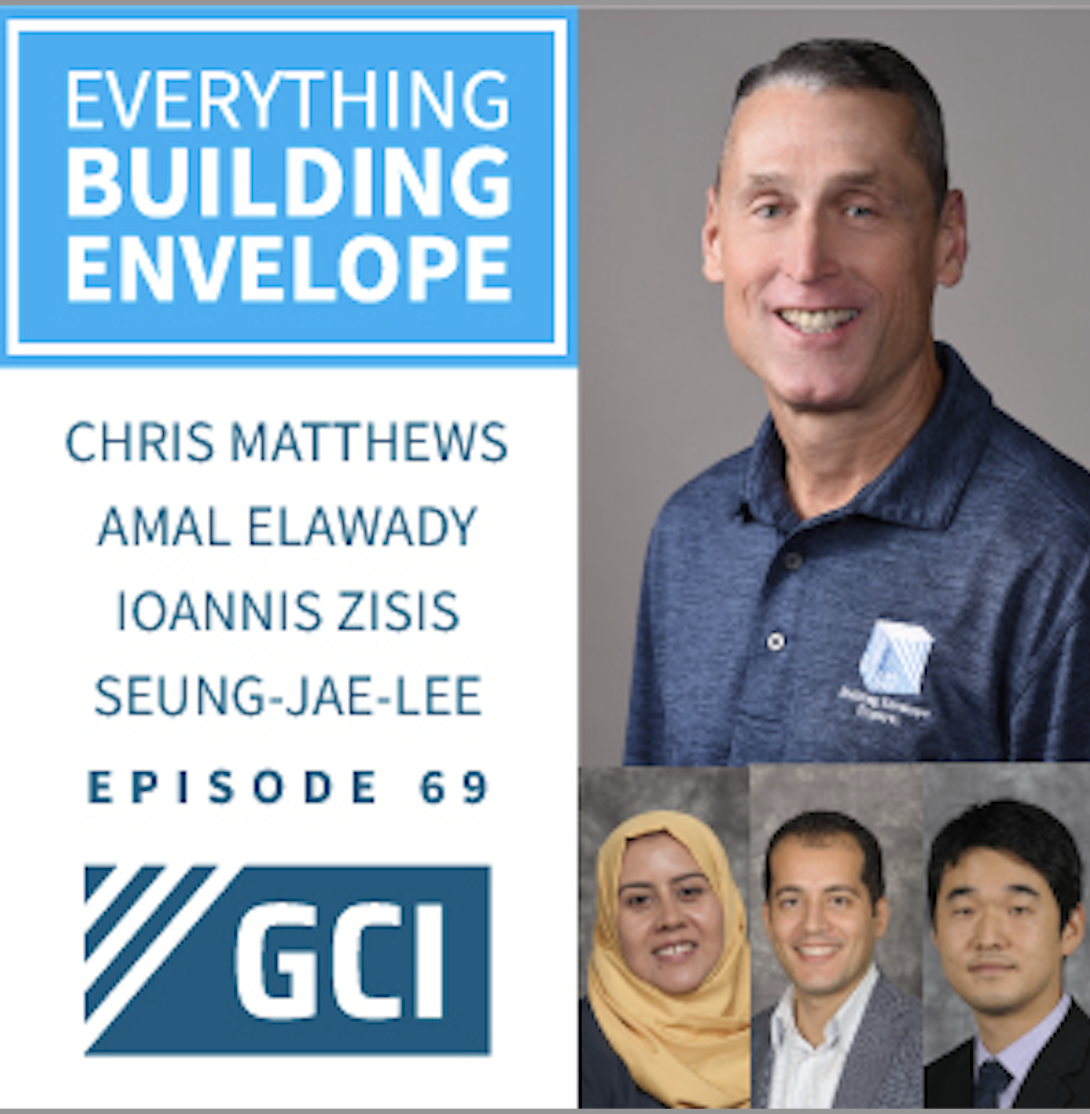
FIU Wall of Wind Research Facility: Environmental Effects on Buildings
(Released on August 19)In this episode, Chris Matthews, President and Principal for GCI Consultants talks with staff members from FIU , starting with, Ioannis Zisis from FIU who is an Associate Professor, Dept. of Civil & Environ. Engineering. They’ll discuss the Wall of Wind and research on curtain walls, and simulation of damage from water-ingress.
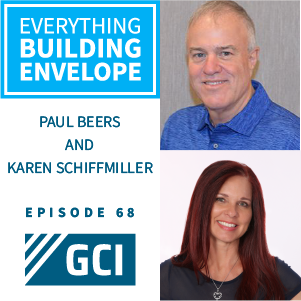
Navigating Hurricane Season Property Damage
(Released on June 15)In this episode, Paul Beers, CEO and Managing Member for GCI Consultants talks with Karen Schiffmiller, President of FAPIA, the Florida Association of Public Insurance Adjusters, the largest public adjusting association in the country. They’ll break down the claims review process for hurricane property damage and how FAPIA helps their policyholders.
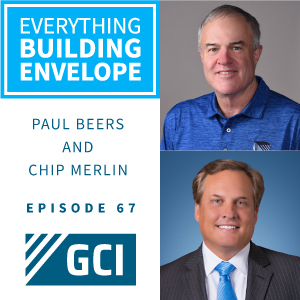
Dealing With Your Insurance Company After a Loss
(Released on May 26)n this episode, Paul Beers, CEO and Managing Member for GCI Consultants, talks with Chip Merlin, Founder and President of Merlin Law Group, about teh representation and advocacy of insurance policyholders who are in disputes with their insurance carriers. They’ll break down teh claims review process and help you understand when you need to hire an attorney.
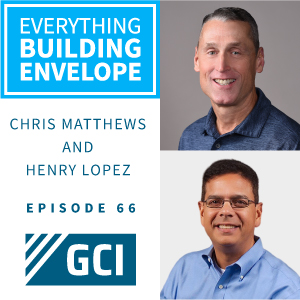
Building an Entrepreneurial Company Culture Through Technology
(Released on April 23)In this episode, Chris Matthews, President and Principal for GCI Consultants, talks with Henry Lopez, managing partner at Levante Business Group, about how GCI has built a company culture through the values of entrepreneurship. Listen in as the two experts discuss how technology has played a part in building a sustainable company culture in the current climate of the building envelope industry.
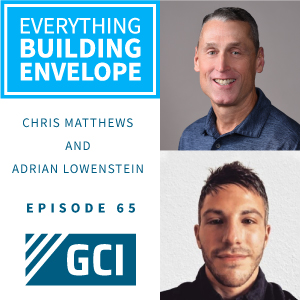
Comparing Building Envelope Industry Perspectives and Trends – Skyline Windows
(Released on March 30)Listen to Chris Matthews, President and Principal for GCI Consultants, talk with Adrian Lowenstein, National Business Development Manager for Skyline Windows, about the Building Envelope industry’s hot topics. Listen in as the two experts discuss energy code requirements, sustainability trends, and technology trends that they see in the Northeast where Skyline Windows is based versus the Southeast where GCI Consultants does a lot of work.
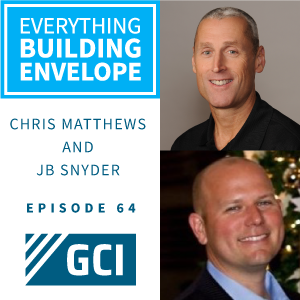
Tremco Products and Applications for Building Envelopes
(Released on November 7)Listen to Chris Matthews, GCI Consultants CEO & Founder talk with JD Snyder, Senior Technical Representative of Tremco Sealants, about the COVID-19, common waterproofing building envelope issues, and technology in the field. Listen in as the two experts discuss the in and outs of the current state of the Building Envelope landscape
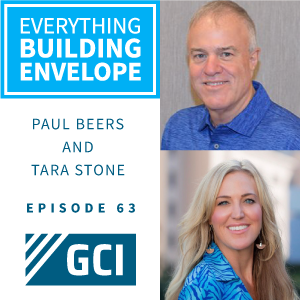
Catastrophe Insurance Claims
(Released on September 3)Listen to Paul Beers, GCI Consultants CEO & Founder talk with Tara Stone, president of Stone Claims Group, about catastrophe insurance claims, wind storms, and hurricanes amidst this year’s current hurricane season. The two experts discuss the in and outs of the insurance claim process and how building envelope experts work together with insurance adjusters to identify damage.
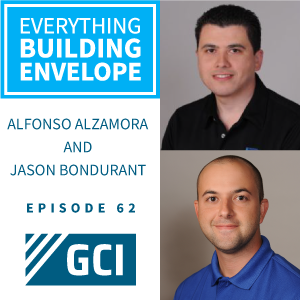
Deck Waterproofing
(Released on August 21)Listen to GCI Consultant team members and industry experts, Alfonso Alzamora and Jason Bondurant discuss plaza deck and pool deck waterproofing. Learn about the typical components that we find in these types of systems and how they are installed.
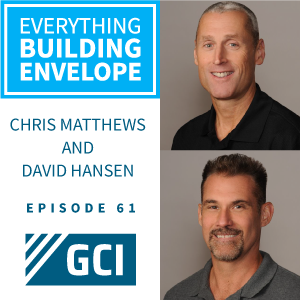
Wall Systems
(Released on July 10)Today’s podcast will focus our conversation with David Hansen on his extensive knowledge of products and wall systems, especially exterior glazing systems and how they are intended to function, how to get them installed correctly, and how to keep them functioning right. David is gonna talk to you about some of the things he’s learned in his 30 years in the industry, problems, and recommendations he can offer to you.
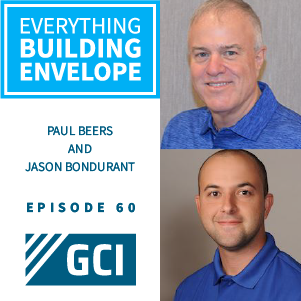
Due Diligence of the Exterior Building Envelope
(Released on June 25)Jason Bondurant deals with forensic investigations, problems with existing buildings. The main purpose of Due Diligence of the Building Envelope is to assess the condition of the building envelope at a property, to identify any deficiencies which might require repair or replacement. The building envelope refers to the exterior skin of the building, the exterior wall systems which might be brick or stucco glazing systems like storefronts, curtain walls, sliding glass doors, waterproofing systems on balconies or plaza decks, and the roofing systems on the roof of the building.
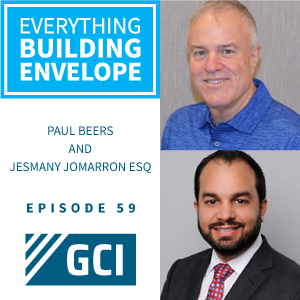
Is Your Building Prepared For Hurricane Season
(Released on June 1)As hurricane season unfolds, we’re preparing for the possibility of tornadoes and thunderstorms that can cause storm damage to commercial properties and homes. Learn more about preparing your building for hurricane season from two industry experts; Jesmany Jomarron, the founding Partner at FPJL Trial Attorneys; and Paul Beers, a leading expert witness on hurricane damage and protection.
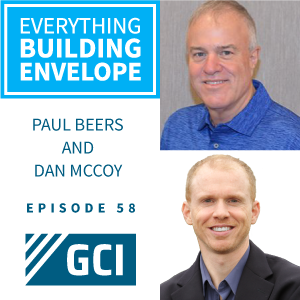
Systems Processes and Working Remotely
(Released on May 19)One of the best things any company can do is set up technology systems and processes that help prepare them to work under any circumstances. GCI was prepared for the current crisis and hasn’t had to make many (if any at all) adjustments to work remotely. We continue to deliver a rapid response to our clients now, and in the future beyond the current crisis. Here’s a look at some of the technologies and strategies we’ve been using with great success for the past decade.
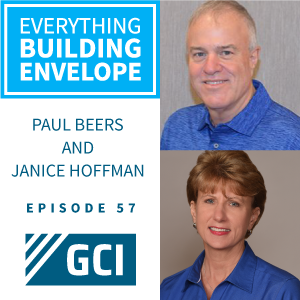
COVID-19 Protocols for Building Envelope Inspections
(Released on May 12)The new normal for the construction industry is being defined right now. Keeping people safe is the name of the game. What has changed is that we’re implementing new COVID-19 safety protocols and training for all GCI personnel – this includes our inspectors who come onsite at your property. What hasn’t changed is our dedication to providing our expert opinions and experience to assess and interpret the damage to your property.
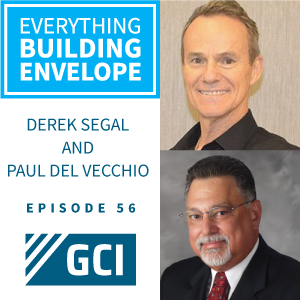
What Every Building Owner Needs To Know About Doors & Windows
(Released on April 30)Understanding the current condition of your doors and windows and their possible vulnerabilities can protect your building from future damage, protect people from harm, and protect your investment for the long haul.
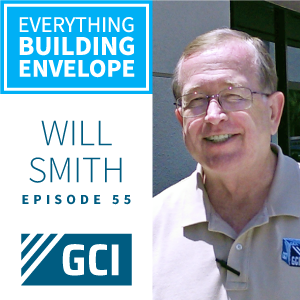
Is Your Expert Really An Expert?
(Released on March 20)- Is your construction litigation expert really an expert?
- Education vs. Experience
- Proven Methodology
- Investigation Standards
- Strategies For Testifying
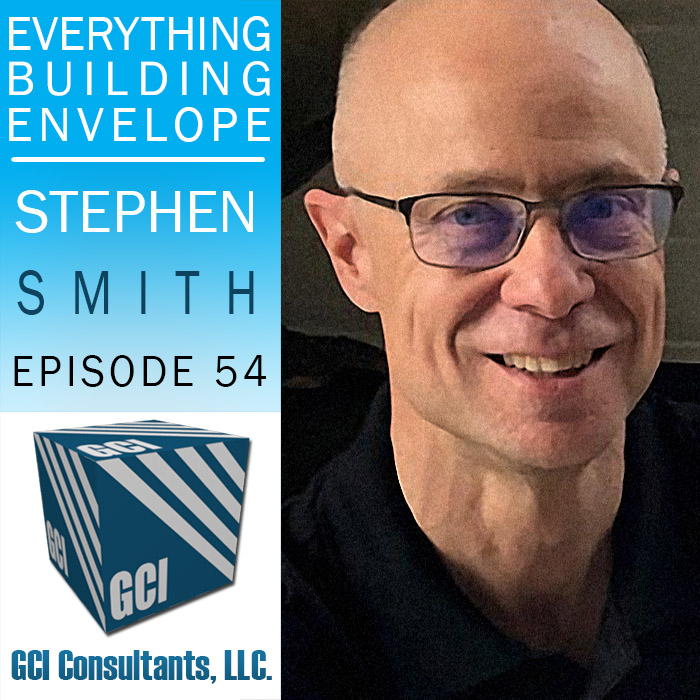
Field Chat – Text Messaging for Construction Projects
(Released on February 4)- About Stephen Smith
- What is Field Chat
- Job Site Communication
- FieldChat Platform
- Text Messaging
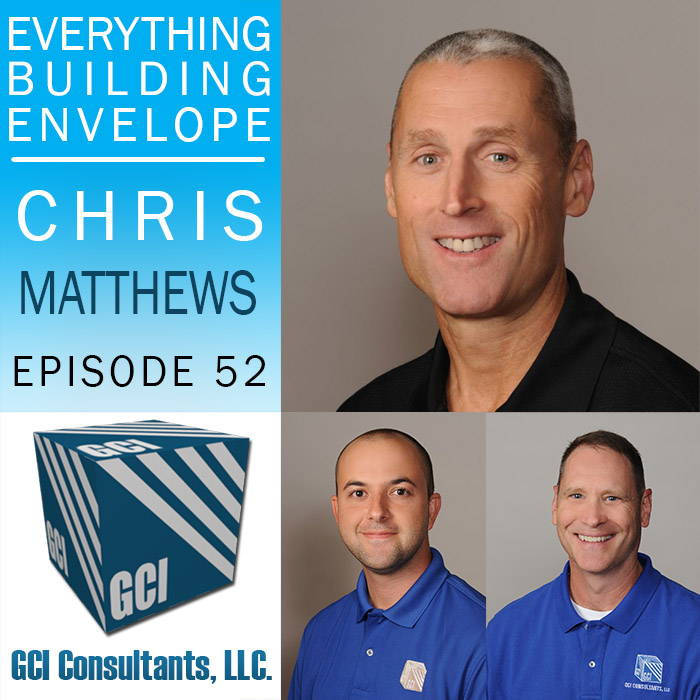
Drainage vs. Barrier Wall Systems
(Released on January 1)- About Bret Taylor & Jason Bondurant
- Barrier vs Drainage Wall Construction
- Drainage Wall Systems
- Cladding Systems
- Barrier Wall Systems
- Mass Wall Systems
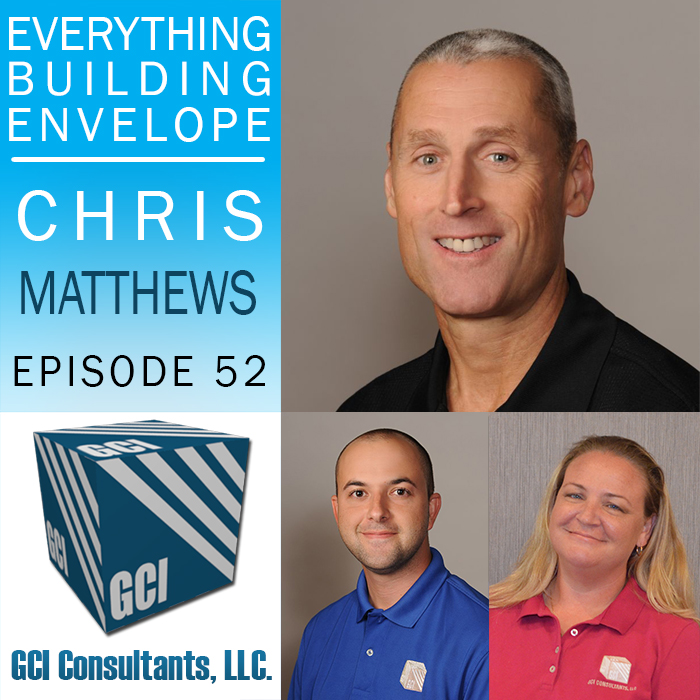
Facade Investigations
(Released on December 6)- About Shuana Serafini & Jason Bondurant
- What is a Facade?
- Facades & Waterproofing
- Facade Performance
- Facade Investigations
- Identifying Problems
- Due Diligence Work
- Condition Assessments
- Forensic Inspections & Reporting
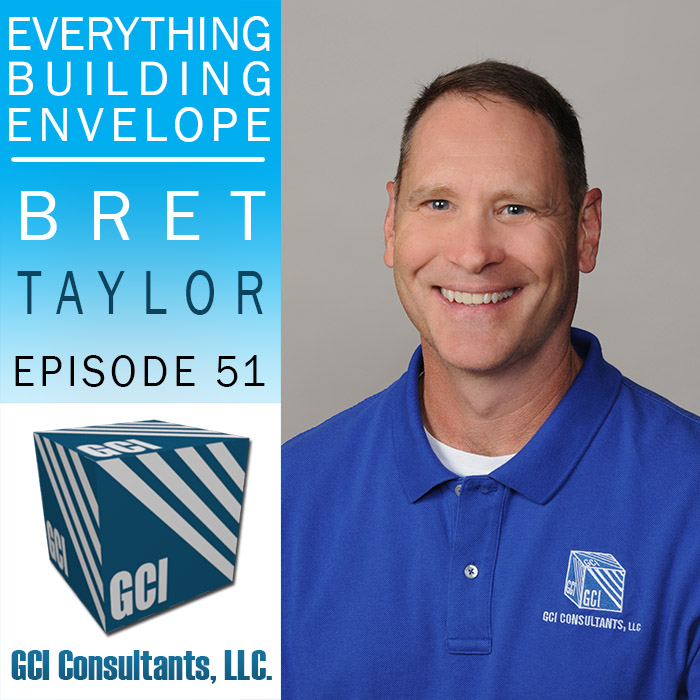
Litigation Consulting and Expert Witness Services
(Released on November 11)- Litigation Support and Consulting Services
- Water Infiltration Testing
- Forensic Testing of Buildings
- Construction Defect Cases
- Water Leakage Causation
- Plaintiff and Burden of Proof
- Expert Witness Testimony
- Forensic Inspections & Reporting
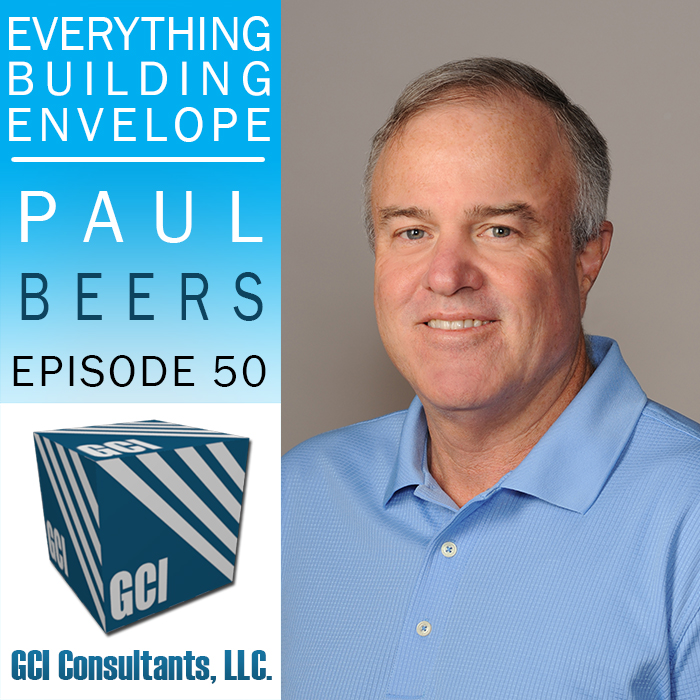
Hurricane Information and Recovery Procedures
(Released on October 16)- Hurricanes in 2016, 2017, 2018, 2019
- GCI’s Prior Involvement with Claims
- Maria Rivera & Paul Build a Team
- Recent Hurricanes & Damages
- Water Leakage & Remediation
- Pre-Inspections of Buildings
- Glazing Inspections & Reporting
- Water Leakage Investigations
- Litigation Consulting
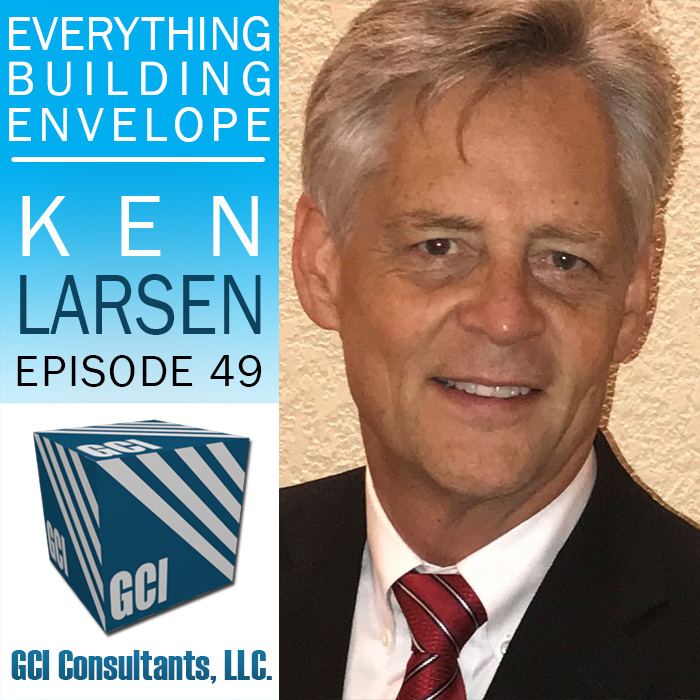
Building Inspections, Cleaning and Restoration
(Released on October 1)- About Ken Larsen
- International Dry Standard Organization
- The Restoration Industry
- Building Restoration Contractors
- Hurricane Michael Examples
- Competent Standards of Care
- F500 Standard of Care
- Moisture Management, etc
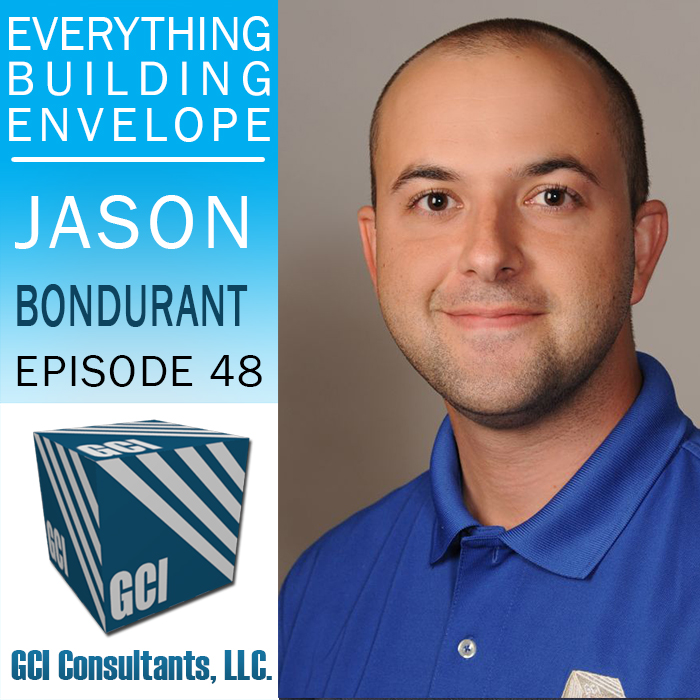
Water Leakage Investigations
(Released on August 16)- Forensic Investigations on Existing Buildings
- Water Leakage, Water Intrusion & Water Damage
- Insurance claims due to water infiltration
- Structural ratings versus water intrusion
- Laboratory tests versus tropical storms or hurricanes
- etc
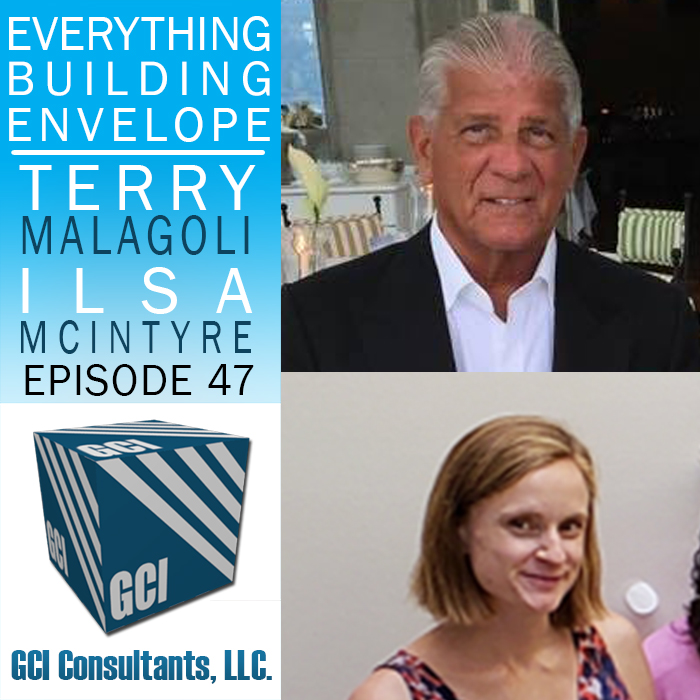
Infrared Testing in the Construction Industry and Beyond
(Released on April 1)- What is the role of infrared envelope inspections in building commissioning for verifying new construction and reducing liability?
- How can infrared envelope testing add value to green initiatives and energy saving programs?
- How does IR imaging detect failing window seals and faulty or missing insulation invisible to the naked eye?
- How much can energy loss disrupt building heating and cooling distribution, and how much can it affect utility costs?
- How can IR testing be used to evaluate current masonry conditions and control costs on repairs?
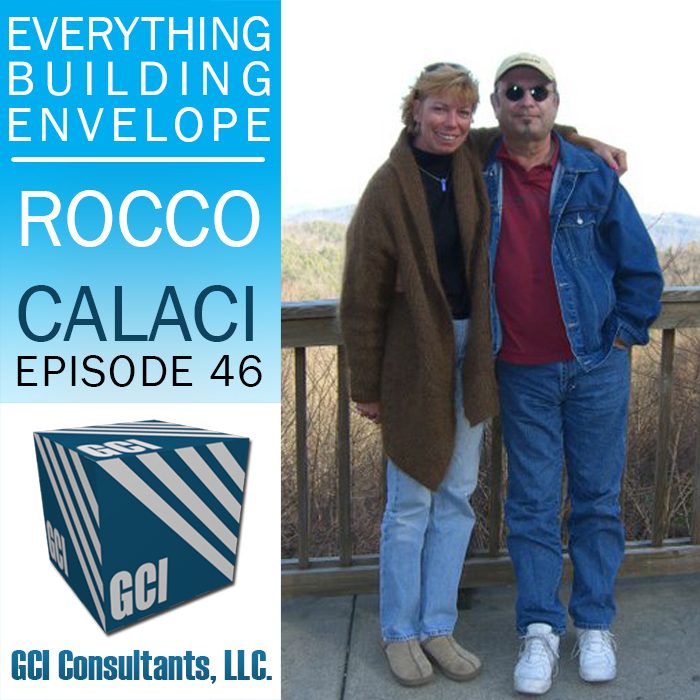
Meteorological Data, Storms, Wind, Rain, Intensity, Accuracy & Computer Models
(Released on March 1)- About Rocco & LRC Services
- Meteorological Data
- Federal Weather Databases
- Repository of US Weather Radar
- Weather Event Historical Data
- Microscale to Synaptic Scale Data
- Mesocyclones, Microbursts & Tornadoes
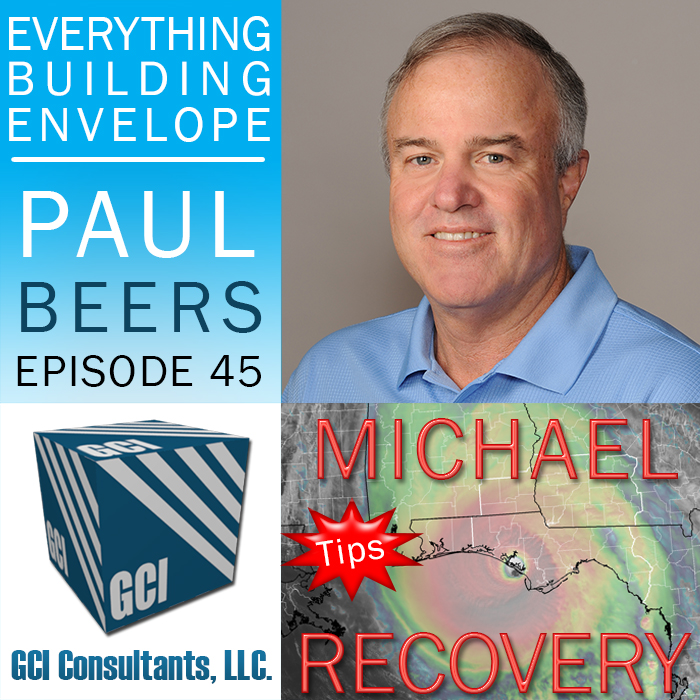
Wind Damage to Windows, Investigation & Claims
(Released on February 20)- Paul Interviewed on Newstalk 101 in Panama City
- Intro to Tara Munoz & Paul Beers
- Wind Damage to Windows, Visual & Discrete
- Building Code Changes by Paul Beers After Andrew
- Expert Testimony and Forensic Testing vs Insurance Claims
- Wind Damage Characteristics
- Insurance Company Obligations & Claim Denials
- and much more…
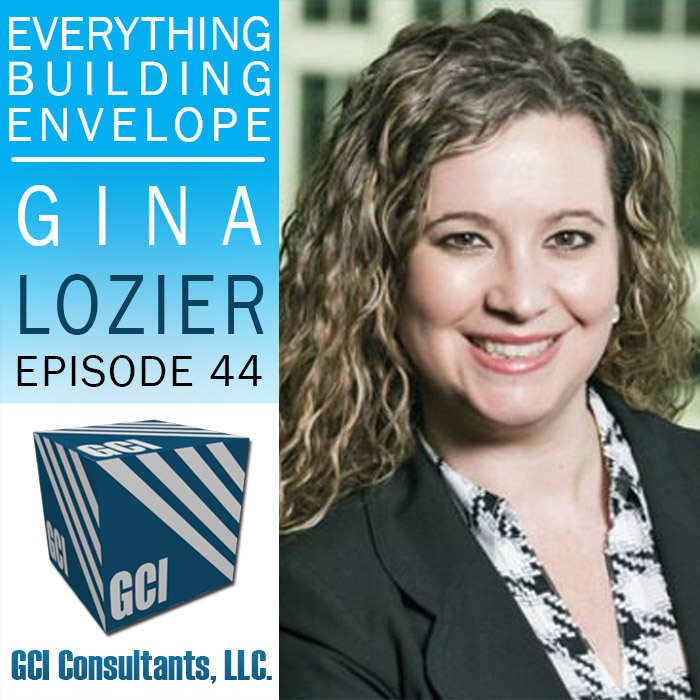
Windstorm Insurance Claims, Coverage, Experts & Litigation
(Released on February 1)- About Gina Lozier
- 2017 Hurricane Season Damages & Costs
- Insurance Company Claim Mitigation Tactics
- Why policy owners should have an expert on their side
- When claims go to trial, etc.
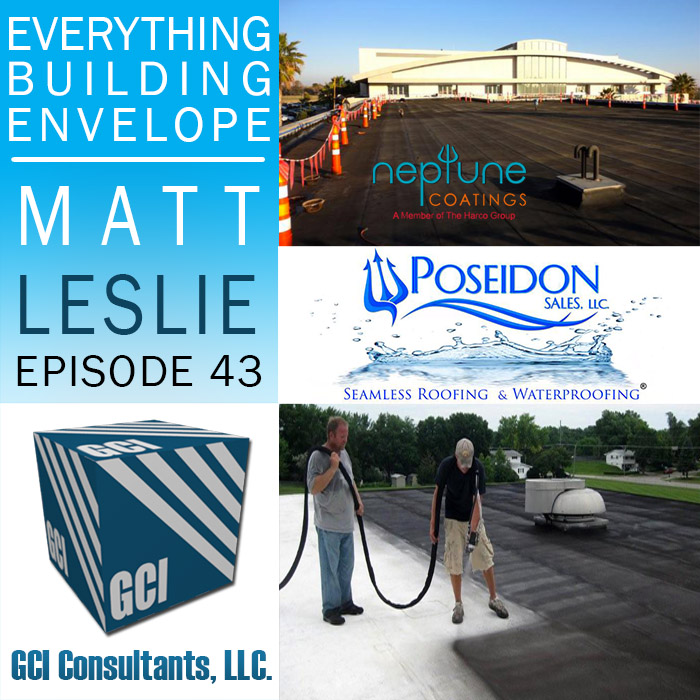
Roofing and the Wet Suit Waterproofing Membrane System
(Released on December 26)- About Matt Leslie & the Roofing Industry
- Wet Suit Membrane & its many uses
- About Neptune Coatings
- Wet Suit Durability
- Building Envelope Applications
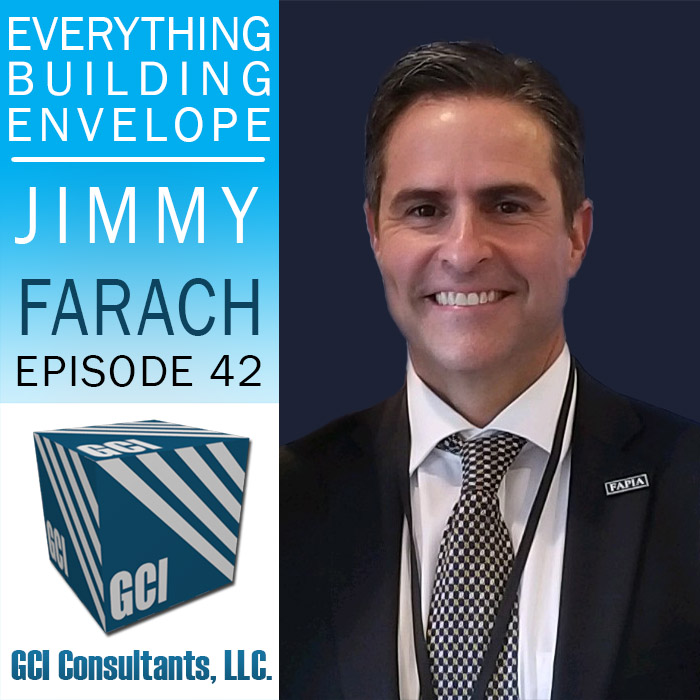
FAPIA, Hurricanes & Insurance Claims
(Released on September 4)- About Jimmy Farach of FAPIA
- What are some of the differences you see between the 0/4 0/5 hurricanes and Irma related to the way the claims process is going?
- What types of damages are you seeing from Irma vs the storms of the 04 and 05 seasons?
- Do you feel the involvement of a claim advocate such as yourself makes a difference in the way a claim is handled and the result?
- How have you changed the way you approach claims, assess damages and investigate the loss for Irma?
- If there were 3 or 4 critical points you could stress to a property owner now after Irma or for any future storm such as Irma, what would those be?
- Do you see any differences in changes in weather patterns and storms over the past 10 years or so?
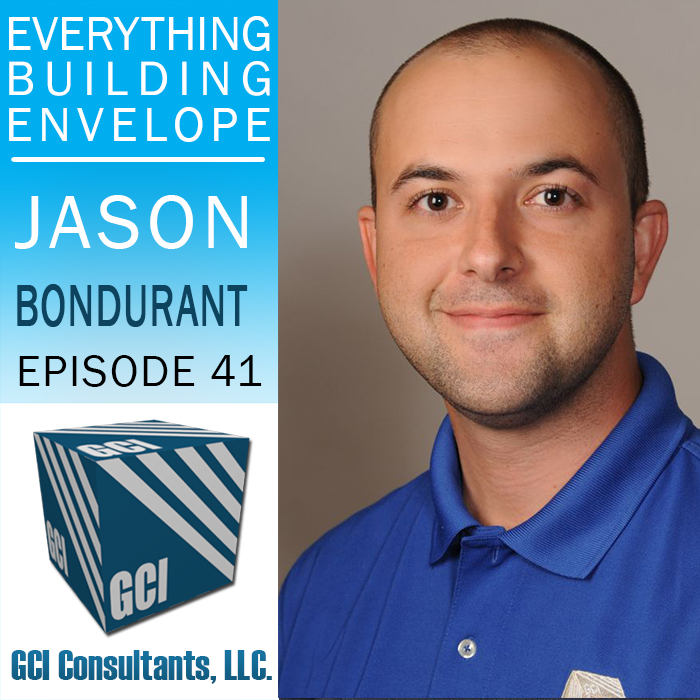
Strategic Projects Division and Testing Methods
(Released on May 3)- Strategic Projects
- Water Testing Methods
- Hurricane Recovery
- Water Penetration in Buildings
- Results & Solutions
- Consultants versus Contractors
- Elimination of Problems
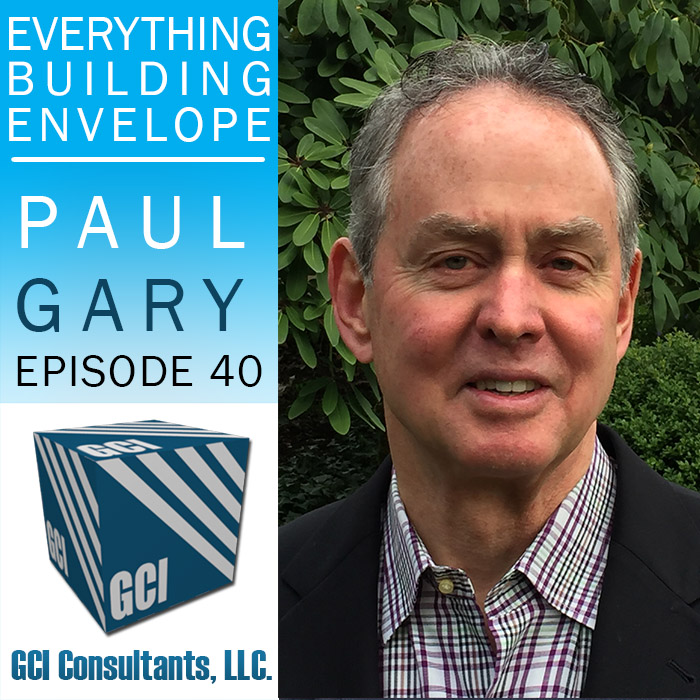
Construction Industry Legal Services
(Released on April 3)- About The Firm
- Notice of Defect & What to do
- Florida 558 Notices
- Opportunity to Cure – Right of Repair
- Documentation needed to avoid insurance issues
- Product Warranties & Importance
- Water Leakage Defects & Contractor Inspections
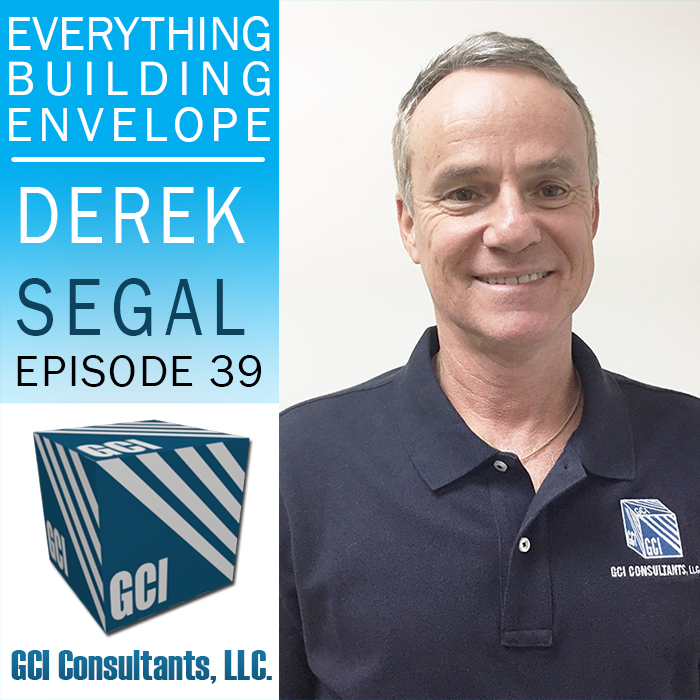
Roof Systems, Hurricane Preparation & Recovery
(Released on March 2)- Roof Consulting
- Hurricane Preparation
- Vendor Relationships
- Investigations
- Maintenance
- Warranty & Insurance
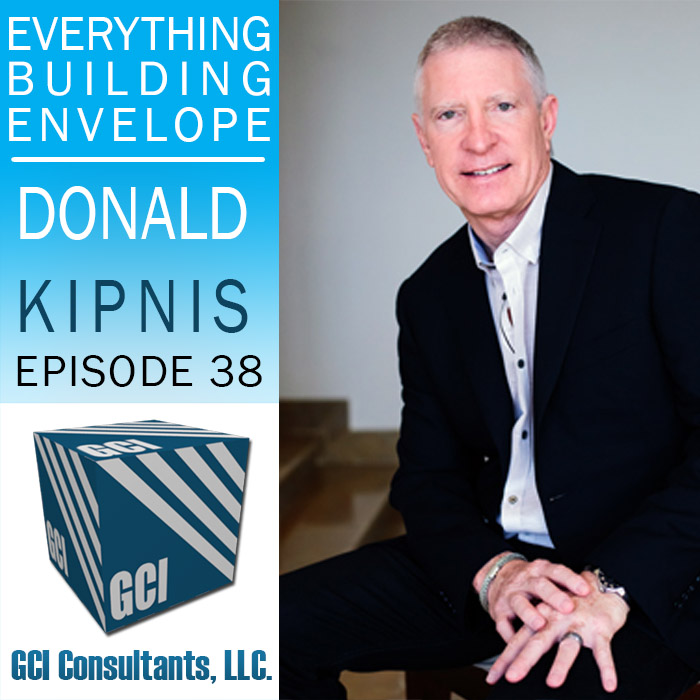
Construction Project Management
(Released on January 2)- Broken by design
- Benefits to professional owner/Association representation and project management
- Replacing a contractor
- Bidding versus Best Value – is low bid the lowest cost???
- Contractor Insurance & bonding
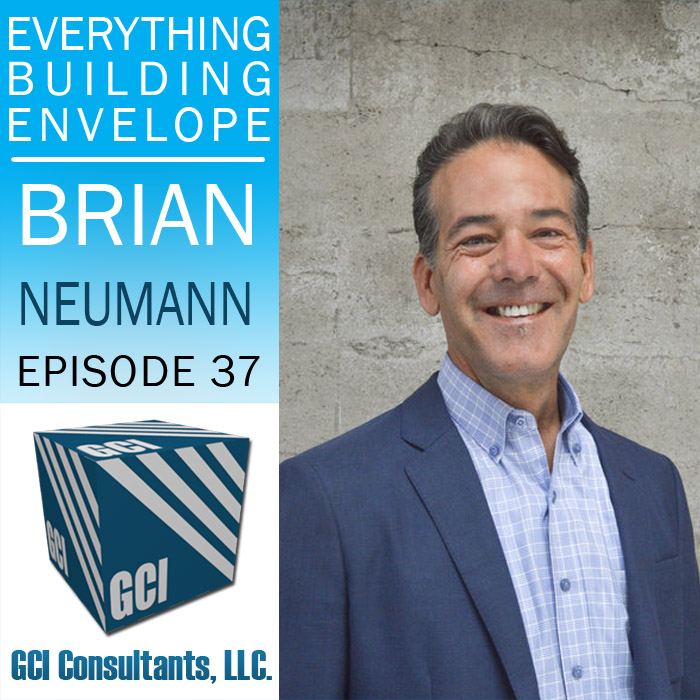
Building Envelope Architects
(Released on December 19)- About Brian
- Building Envelope Architecture
- Materials Used
- New Technologies
- Building Systems
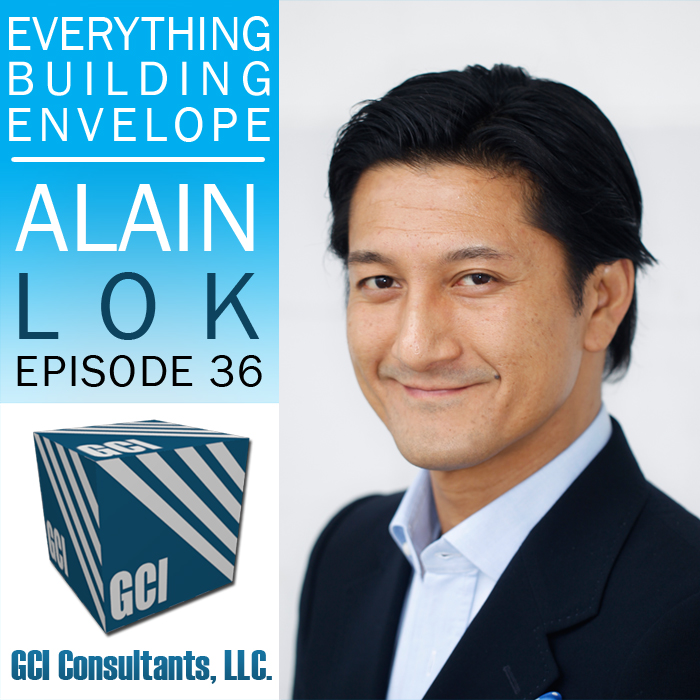
Kryton Smart Concrete Technology
(Released on December 1)- About Kryton International
- Krystol Technology
- Krystol Internal Membrane
- Crystalline Admixture
- Waterproofing Concrete
- Membrane Systems
- Warranties
- Product Explanations
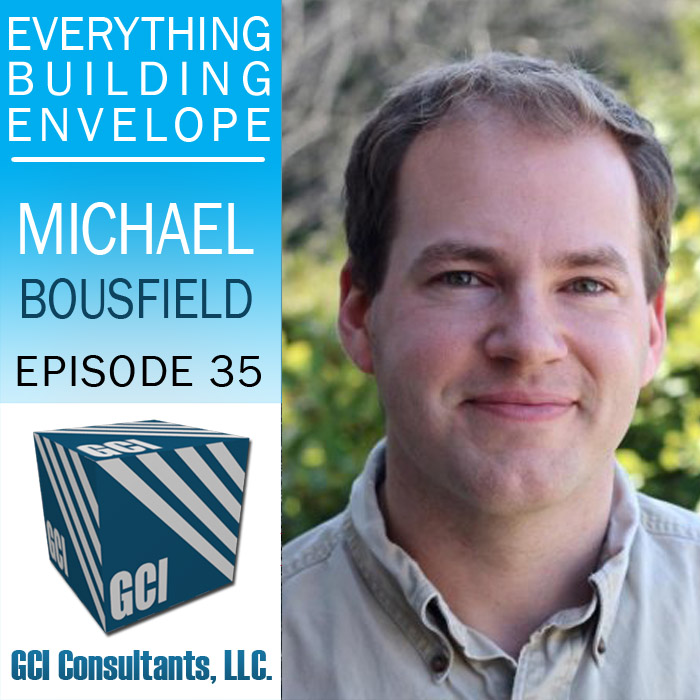
Energy Efficient Fiberglass Windows & Doors
(Released on November 17)- About Cascadia Windows and Doors
- Cascadia’s Experience in the Building Envelope
- Making Buildings more Energy Conserving
- Heat Gain & Loss in the Window Assembly
- Product Strength & Longevity
- 3 Categories of Products
- Read our Article Here